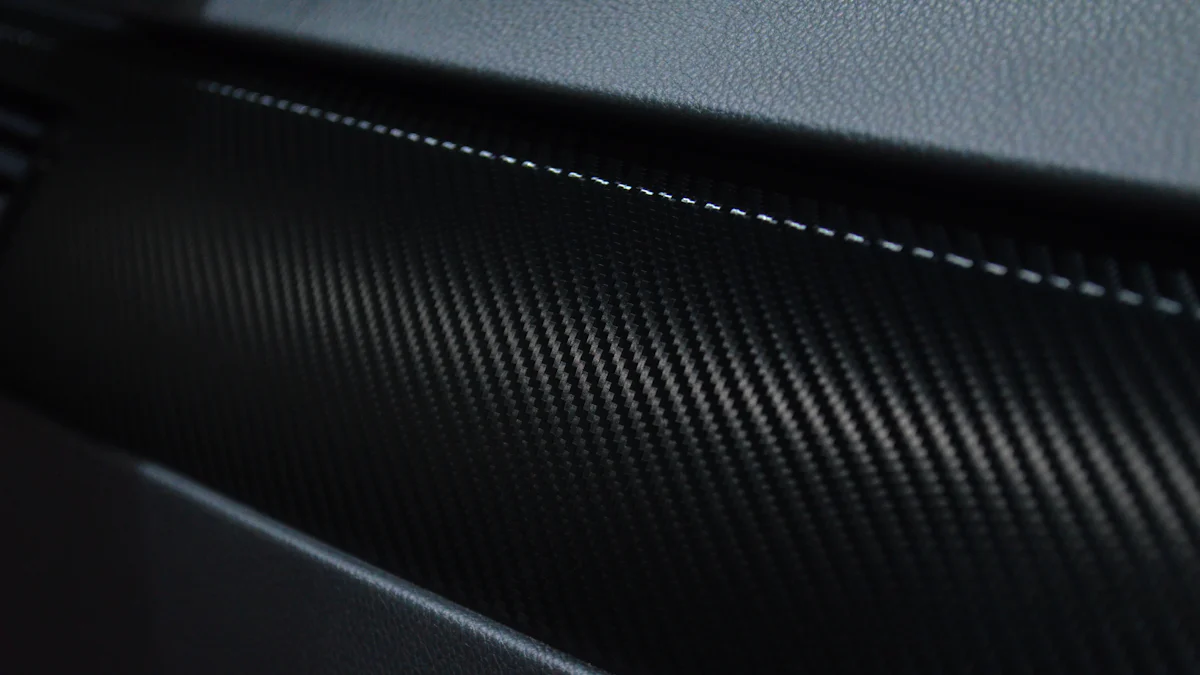
Carbon-carbon composites are cutting-edge materials made from carbon fibers integrated into a carbon matrix. If you’re wondering what is carbon composites, they are known for their remarkable strength, lightweight nature, and exceptional thermal resistance, making them essential in various industries. Carbon carbon composites applications span across aerospace, automotive, and industrial sectors, where their unique properties are highly valued.
The global demand for carbon-carbon composites is on the rise. In 2022, the market was valued at USD 20.5 billion and is expected to grow significantly, reaching USD 38.32 billion by 2032. The manufacturing process involves multiple steps, including precursor preparation, carbonization, and molding, resulting in durable and versatile structures.
Key Takeaways
- Carbon-carbon composites are lightweight yet incredibly strong, with tensile strength surpassing steel by 7-9 times, making them ideal for high-performance applications in aerospace and automotive industries.
- The manufacturing process involves critical steps such as precursor preparation, carbonization, and densification, which are essential for achieving the desired mechanical and thermal properties of the composites.
- Emerging applications for carbon-carbon composites include advanced aerospace components, high-performance sports equipment, and innovative medical devices, showcasing their versatility and growing importance in various sectors.
What Are Carbon Carbon Composites?
Definition and Properties
Carbon carbon composites are advanced materials composed of carbon fibers embedded within a carbon matrix. These composites stand out due to their unique combination of mechanical and thermal properties. They exhibit high strength, excellent thermal conductivity, and remarkable stability under extreme temperatures. Their tensile strength surpasses steel by 7-9 times, while their low density makes them significantly lighter than metals.
These materials also resist acids and alkalis, ensuring durability in harsh environments. Their low thermal expansion and superior thermal shock resistance make them ideal for applications requiring precision and reliability. Additionally, carbon carbon composites offer excellent wear resistance and design flexibility, enabling their use in diverse industries. These characteristics make them indispensable in scenarios where performance under extreme conditions is critical.
Industrial Applications
Carbon carbon composites play a vital role in various industries due to their exceptional properties. In aerospace, they are used in aircraft components such as clips, brackets, and fuselage panels, where lightweight and high strength are essential. The automotive industry benefits from these composites in lightweight parts that enhance fuel efficiency.
In sports and leisure, carbon carbon composites are found in high-performance equipment like bicycles and tennis rackets. Medical devices also utilize these materials for components requiring a combination of strength and low weight. Their versatility and reliability make them a preferred choice across multiple sectors, driving innovation and efficiency.
Materials and Tools for Carbon Carbon Composites
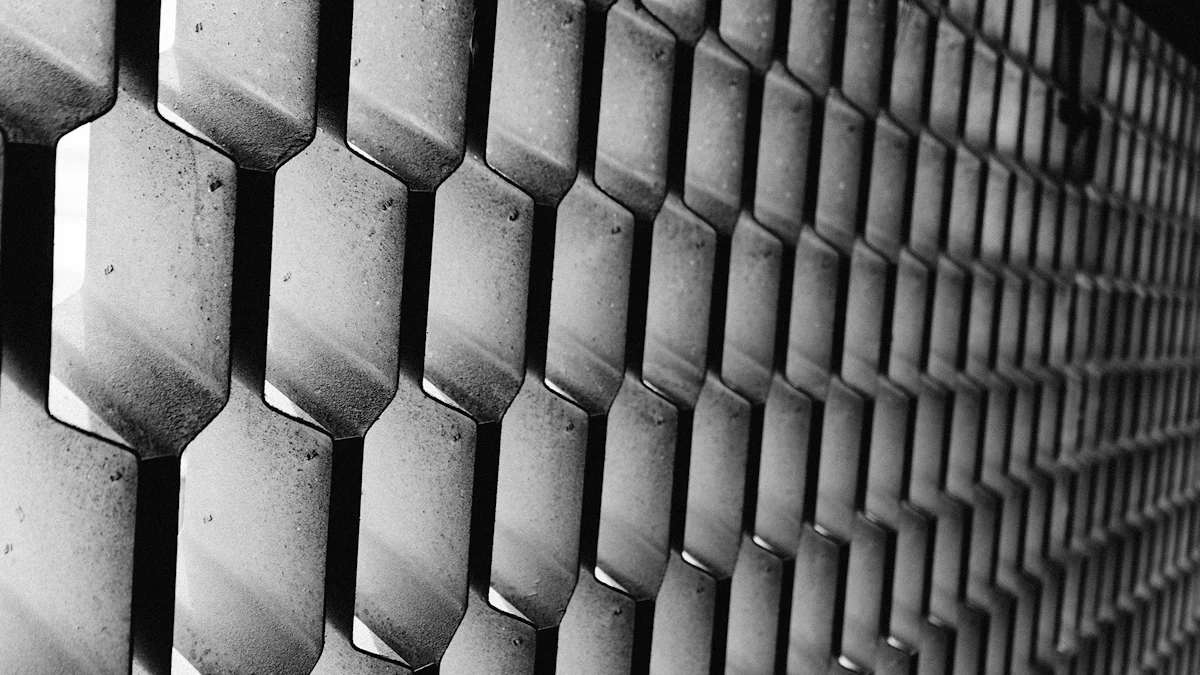
Carbon Fiber Precursors
Carbon fiber precursors form the foundation of carbon carbon composites. Approximately 90% of carbon fibers are derived from polyacrylonitrile (PAN), while the remaining 10% come from rayon or petroleum pitch. PAN serves as the primary precursor due to its ability to produce fibers with superior strength, stiffness, and heat resistance. The quality of the PAN precursor directly impacts the performance of the final composite material. Rayon and pitch, although less common, offer unique properties that make them suitable for specific applications. These materials undergo a series of chemical and thermal processes to transform into high-performance carbon fibers.
Resins and Matrix Precursors
The matrix in carbon carbon composites binds the carbon fibers together, enhancing their structural integrity. Thermosetting resins, such as epoxy, are widely used due to their ease of application and ability to form glassy carbon upon pyrolysis. Pitch materials, derived from petroleum or coal tar, provide higher density and superior mechanical properties, making them ideal for structural applications.
Type of Resin/Matrix | Characteristics | Effectiveness |
---|---|---|
Thermosetting Resins | Easy to use for fiber impregnation, forms glassy carbon | Effective for complex geometries and high temperatures |
Pitch Materials | High-density carbon, superior mechanical properties | Suitable for structural applications with enhanced porosity |
The carbonization process further improves the material’s properties, ensuring its suitability for high-temperature environments.
Essential Equipment
Manufacturing carbon carbon composites requires specialized tools and materials. Key equipment includes:
- Carbon fiber fabric (woven or unidirectional)
- Resin systems (epoxy, polyester, or vinyl ester)
- Molds (custom or pre-made)
- Vacuum bagging equipment and heat sources like ovens or autoclaves
- Brushes, rollers, and squeegees for resin application
Safety gear, including gloves, goggles, and respirators, ensures worker protection during the manufacturing process. These tools and materials enable precise fabrication, ensuring the composites meet industry standards.
Step-by-Step Process for Making Carbon Carbon Composites
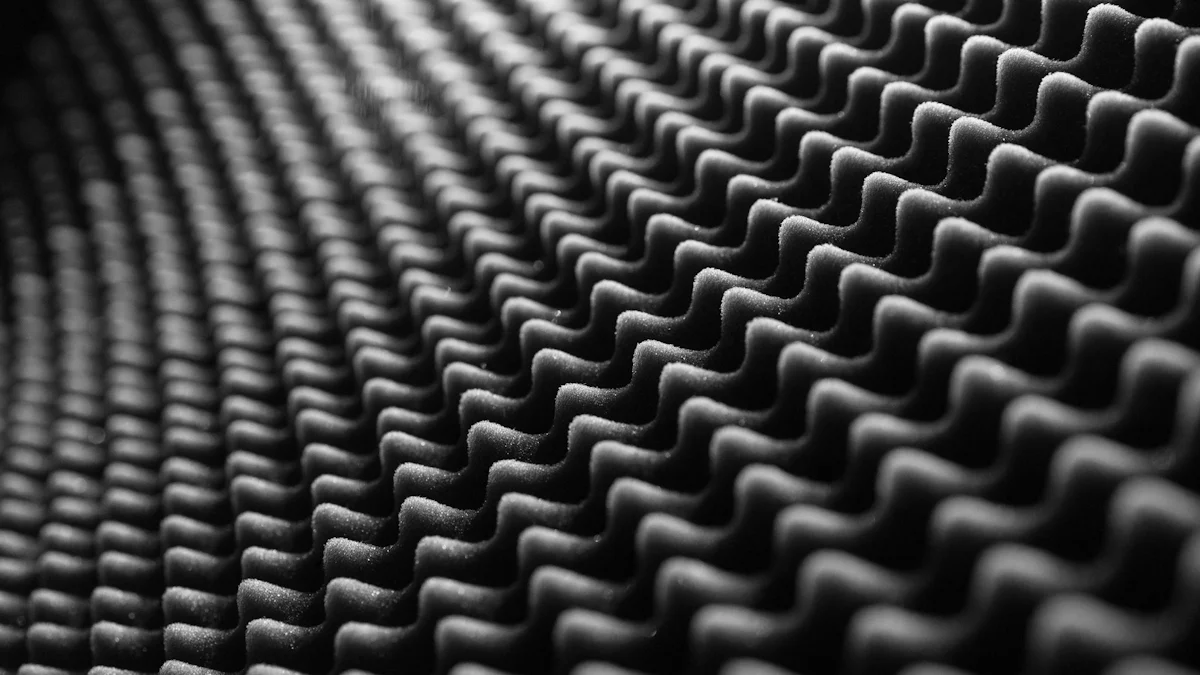
Precursor Preparation
The preparation of precursors lays the foundation for manufacturing carbon carbon composites. This process begins with selecting a suitable precursor, typically polyacrylonitrile (PAN), due to its superior strength and thermal properties. The precursor undergoes carbonization, where it is heated in an inert atmosphere at high temperatures to convert it into graphite. This step enhances the material’s structural integrity and thermal resistance.
Once carbonized, the fibers are processed into various formats, such as woven cloth, braided tubes, or prepreg sheets. These formats allow for flexibility in designing composite structures. The final step involves molding the prepared carbon fibers into desired shapes using epoxy resins and curing them under controlled conditions. This meticulous preparation ensures the fibers are ready for integration into the composite matrix.
Carbonization and Densification
Carbonization transforms the carbon fiber preform into a solid carbon structure. This process occurs at approximately 1000°C in an oxygen-free environment, removing volatile elements and leaving behind a porous carbon matrix. The resulting material, while strong, often requires densification to achieve the desired mechanical properties.
Densification involves infiltrating the porous structure with additional matrix precursors, such as pitch or resin. Techniques like chemical vapor deposition (CVD) or chemical vapor infiltration (CVI) are commonly used. For thin-walled composites, CVD is particularly effective due to its ability to uniformly coat the material. Thick-walled composites, however, may require multiple cycles of densification to ensure uniformity and strength. Surface machining is often necessary to remove excess material and prepare the composite for final assembly.
Surface Treatment and Final Assembly
Surface treatment enhances the bonding strength between the carbon fibers and the matrix. This step involves creating additional bonding sites on the fiber surface through chemical or mechanical processes. Sizing, a protective coating applied to the fibers, improves their processability and acts as a coupling agent, ensuring compatibility with the resin.
Once treated, the components are assembled into the final structure. This stage may involve additional machining to achieve precise dimensions and ensure a smooth surface finish. The completed carbon carbon composite undergoes rigorous quality checks to confirm its performance under extreme conditions. These steps result in a durable and reliable material suitable for demanding applications.
Techniques for Manufacturing Carbon Carbon Composites
Chemical Vapor Deposition (CVD)
Chemical Vapor Deposition (CVD) is a widely used technique for manufacturing carbon carbon composites. This process involves depositing a thin layer of carbon onto a substrate by introducing a carbon-containing gas into a high-temperature chamber. The gas decomposes under heat, leaving behind a uniform carbon coating.
CVD offers several advantages, including precise control over the thickness and composition of the deposited layer. This precision ensures the composite achieves the desired mechanical and thermal properties. The method is particularly effective for creating thin-walled structures, as it allows for even distribution of carbon across complex geometries. Industries rely on CVD for its ability to produce high-quality composites with excellent performance under extreme conditions.
Resin Transfer Molding
Resin Transfer Molding (RTM) plays a crucial role in producing robust carbon carbon composites. This technique involves infusing resin into dry fiber reinforcements within a closed mold. The process ensures the fibers are thoroughly impregnated, resulting in a strong and durable composite material.
Key steps in RTM include:
- Placing dry fiber reinforcements into a two-part mold.
- Clamping the mold shut to create a sealed cavity.
- Forcing resin into the cavity at high pressure to ensure complete impregnation.
RTM is highly efficient and allows for the production of complex shapes with minimal waste. Its ability to create high-quality composites makes it a preferred choice in industries requiring precision and reliability.
Hot Pressing and Sintering
Hot pressing and sintering enhance the mechanical properties of carbon carbon composites. This technique involves applying heat and pressure simultaneously to compact the material and eliminate porosity. The process improves the composite’s strength, durability, and surface finish.
Manufacturers benefit from hot pressing and sintering due to its cost-effectiveness and efficient material usage. The enhanced surface finish achieved through this method is critical for applications demanding high precision. These advantages make hot pressing and sintering a valuable technique in the production of advanced composites.
Challenges and Future Trends
Cost and Manufacturing Challenges
Producing carbon carbon composites involves complex processes and specialized equipment, which significantly increases costs. The raw materials, such as polyacrylonitrile (PAN) and high-quality resins, are expensive. Additionally, the carbonization and densification stages require high temperatures and prolonged processing times, leading to elevated energy consumption. These factors make the production of these composites resource-intensive.
Scaling up manufacturing to meet growing demand presents another challenge. Maintaining consistent quality across large-scale production requires precise control over every step of the process. Industries must also address environmental concerns, as the manufacturing process generates emissions and waste. Overcoming these challenges is essential to make carbon carbon composites more accessible and sustainable.
Innovations in Techniques
Advancements in manufacturing techniques are transforming the production of carbon carbon composites. Researchers are exploring automated processes, such as robotic fiber placement, to enhance efficiency and reduce labor costs. Additive manufacturing, or 3D printing, is emerging as a promising method for creating complex composite structures with minimal waste.
Innovations in chemical vapor deposition (CVD) and resin transfer molding (RTM) are improving material properties while optimizing production times. These advancements enable manufacturers to produce composites with higher precision and performance. Continued research and development in this field will likely lead to more cost-effective and environmentally friendly solutions.
Emerging Applications
Carbon carbon composites are finding new applications across various industries due to their exceptional properties. In aerospace, they are used in airplane braking systems, rocket nozzles, and re-entry vehicle heat shields. The automotive sector benefits from lightweight and high-performance materials that enhance vehicle efficiency.
In sports, these composites improve equipment performance, such as in bicycles and tennis rackets. Medical devices utilize them for their strength and stability, making them ideal for surgical tools and implants. Renewable energy solutions also employ these materials for their thermal properties, contributing to advancements in energy storage and generation. These emerging applications highlight the versatility and growing importance of carbon carbon composites in modern industries.
The process of creating carbon carbon composites involves several critical steps:
- Selecting a precursor like PAN fibers.
- Carbonizing fibers at high temperatures to form graphite.
- Weaving or molding fibers into desired formats.
These composites offer high strength, thermal stability, and lightweight properties, making them indispensable in aerospace, automotive, and medical industries. Future advancements, including nanotechnology and sustainable materials, promise to expand their applications further.
Carbon carbon composites represent the pinnacle of material innovation, driving progress across diverse sectors. Exploring their potential can unlock new possibilities for high-performance solutions.
FAQ
What makes carbon-carbon composites unique?
Carbon-carbon composites combine high strength, lightweight properties, and thermal resistance. These characteristics make them ideal for demanding applications in aerospace, automotive, and industrial sectors.
How long does it take to manufacture carbon-carbon composites?
The manufacturing process can take several weeks. Carbonization, densification, and surface treatments require precise control and multiple cycles to achieve the desired properties.
Are carbon-carbon composites environmentally friendly?
Carbon-carbon composites offer durability and long lifespans, reducing waste. However, their production involves energy-intensive processes. Researchers are exploring sustainable methods to minimize environmental impact.