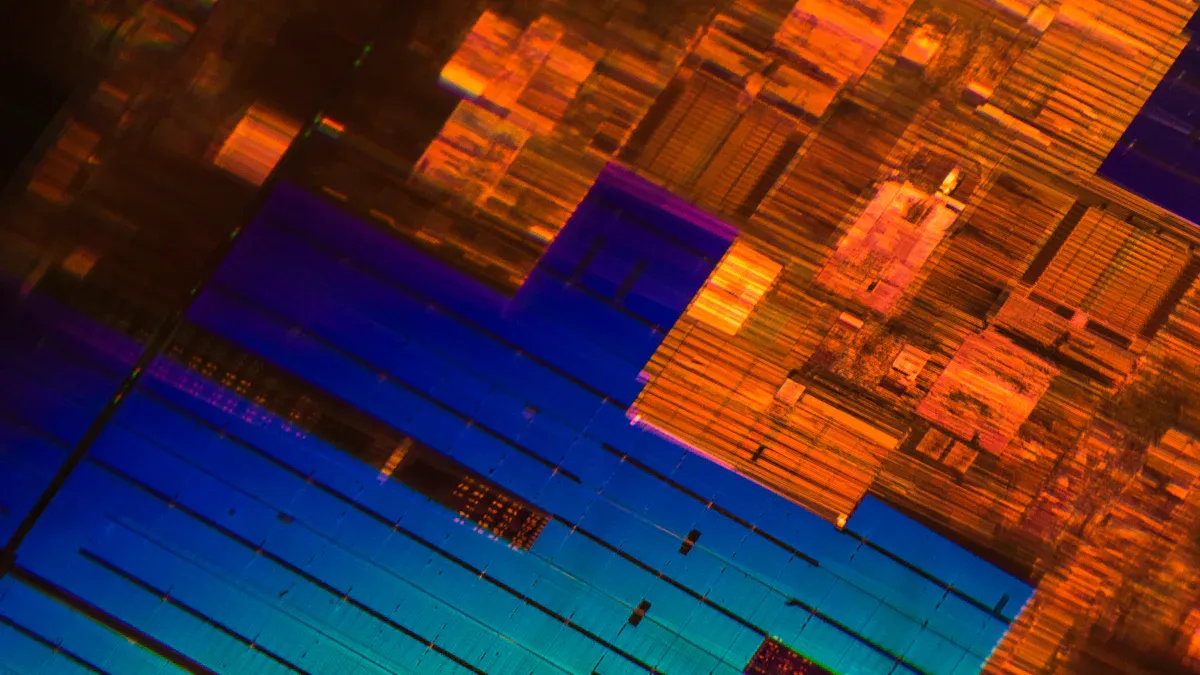
Silicon carbide coating enhances the performance of graphite susceptors in demanding industrial processes. This advanced coating provides exceptional resistance to oxidation and chemical corrosion, ensuring stability in high-temperature environments. The global demand for such solutions reflects their growing importance. For instance:
- The silicon carbide susceptor market, valued at USD 175.3 million in 2023, is expected to reach USD 595.5 million by 2033, growing at a 15.5% CAGR.
- The SiC Coated Graphite Susceptor Market is projected to grow from USD 291.43 million in 2021 to USD 412.23 million by 2030.
Products like the Graphite Susceptor with Silicon Carbide e Silicon Carbide Coated Graphite Carriers play a vital role in improving thermal stability and reducing contamination risks. These benefits are further enhanced by innovations such as CVD silicon carbide coating, offering unparalleled durability and efficiency. Additionally, solutions like the Silicon Carbide Coating 6 pieces enable manufacturers to achieve higher productivity and cost savings.
Asporto chiave
- Silicon carbide coating stops graphite susceptors from rusting or breaking down. This makes them last longer in very hot conditions.
- These coated susceptors spread heat evenly, which helps keep processes steady in industries like making computer chips.
- Using silicon carbide-coated susceptors lowers the chance of contamination. This improves product quality and increases production.
- The strong silicon carbide coating means less fixing is needed. It also makes graphite susceptors last longer, saving companies money.
- Industries like solar panel making and advanced material work gain a lot from the reliability and efficiency of these coated susceptors.
Understanding the Role of Graphite Susceptors
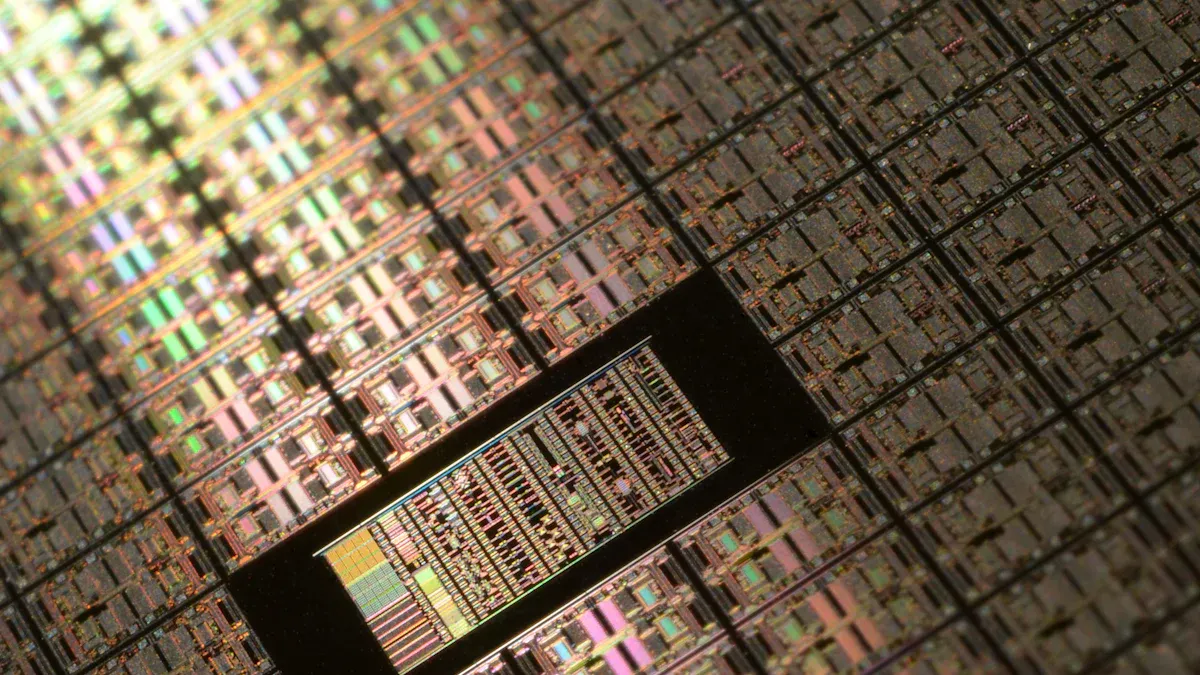
What Is a Graphite Susceptor with Silicon Carbide?
A graphite susceptor with silicon carbide is a specialized component used in high-temperature industrial processes. It consists of a graphite substrate coated with silicon carbide (SiC), a material known for its exceptional thermal and chemical properties. This coating enhances the susceptor’s resistance to oxidation and corrosion, making it suitable for demanding environments. The design ensures compatibility with processes like chemical vapor deposition (CVD), where high temperatures and reactive gases are common.
A study highlights the use of pyrolytic carbon materials in CVD reactors, emphasizing their resistance to highly corrosive gases like hydrogen chloride and chlorine trifluoride. This resistance is crucial for maintaining the integrity of susceptors in such environments.
The silicon carbide coating also prevents the graphite substrate from reacting with process gases, reducing contamination risks. This makes the graphite susceptor with silicon carbide an essential tool in industries like produzione semiconduttore and solar cell production.
Applications in High-Temperature Industrial Processes
Graphite susceptors with silicon carbide coating play a vital role in various high-temperature applications. These include semiconductor manufacturing, where they support the growth of 4H-SiC epilayers via CVD. The coating addresses challenges like etching at elevated temperatures, ensuring high-quality film growth and longer operational lifetimes.
Caratteristica | Designazione |
---|---|
High-temperature resistance | Capable of withstanding temperatures up to 1600°C+, enhancing durability in high-temperature processes. |
Resistenza alla corrosione | The silicon carbide coating prevents chemical corrosion, protecting the graphite substrate. |
Low particle shedding rate | Reduces contamination risk in sensitive applications like semiconductor manufacturing. |
Thermal expansion compatibility | Ensures structural stability at high temperatures, minimizing deformation and extending service life. |
These features make the graphite susceptor with silicon carbide indispensable in industries requiring precision and reliability.
Importance in Heat Distribution and Process Stability
Graphite susceptors with silicon carbide coating ensure uniform heat distribution, which is critical for process stability. They maintain consistent temperatures during heating and cooling cycles, preventing thermal stress and deformation. This uniformity is particularly important in semiconductor and LED manufacturing, where even minor temperature fluctuations can compromise product quality.
- SiC-coated graphite susceptors are essential in semiconductor manufacturing, LED production, and solar cell fabrication.
- They ensure uniform heating and cooling during deposition processes, preserving the integrity of semiconductor wafers.
- The growing demand for semiconductor devices highlights the need for high-performance materials like SiC-coated graphite susceptors.
By improving heat distribution and process stability, these susceptors enhance efficiency and reduce operational costs in high-temperature industrial processes.
Challenges of Using Pure Graphite Susceptors
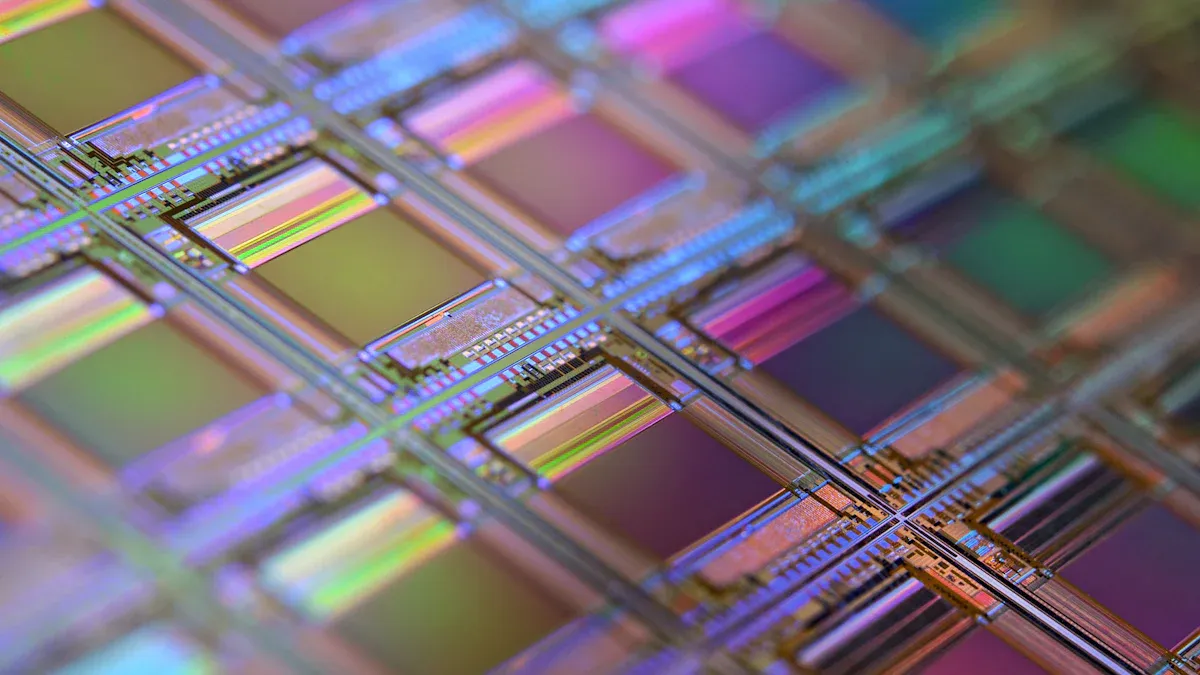
Corrosion and Oxidation in Harsh Environments
Pure graphite susceptors face significant challenges in harsh industrial environments. High temperatures and reactive gases accelerate oxidation, weakening the material over time. Corrosion from chemical exposure further compromises the structural integrity of graphite. This degradation reduces the efficiency of manufacturing processes, especially in industries like semiconductor and solar cell production. Without protective coatings, pure graphite cannot withstand prolonged exposure to these conditions, leading to frequent replacements and increased operational costs.
Risk of Contamination in Sensitive Applications
In sensitive applications, such as produzione semiconduttore, contamination poses a critical risk. Pure graphite susceptors often react with process gases, releasing particles or impurities. These contaminants can settle on wafers, affecting their quality and yield. For instance, during chemical vapor deposition (CVD), uncoated graphite may interact with silicon vapor, introducing defects into the final product. This issue highlights the need for advanced solutions that prevent contamination and ensure consistent performance.
Maintenance and Longevity Issues
Pure graphite susceptors require frequent maintenance due to their limited durability. High-temperature processes cause thermal stress, leading to deformation and cracking. Additionally, exposure to corrosive environments accelerates wear and tear. Coating technologies, such as silicon carbide (SiC) and tantalum carbide (TaC), address these issues effectively. SiC coatings, for example, withstand temperatures up to 1,650°C and extend the service life of graphite susceptors by three to five times. TaC coatings prevent molten silicon infiltration, reducing wafer warpage during rapid thermal processing. These advancements minimize maintenance needs and enhance the longevity of susceptors, making them more reliable for industrial applications.
Suggerimento: Upgrading to a Graphite Susceptor with Silicon Carbide coating can significantly reduce contamination risks and improve durability, ensuring better performance in high-precision processes.
Advantages of Silicon Carbide Coating
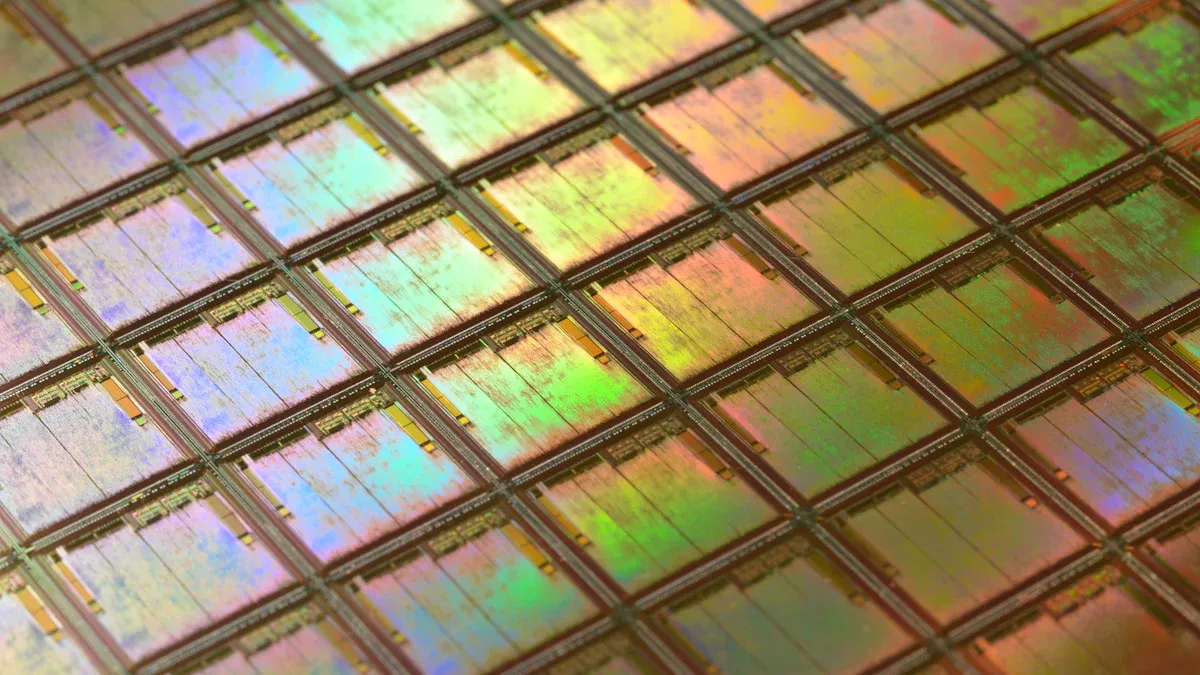
Enhanced Corrosion and Oxidation Resistance
Silicon carbide coating provides exceptional protection against corrosion and oxidation in harsh industrial environments. This coating acts as a barrier, shielding the graphite substrate from reactive gases and chemical residues. For example, it resists corrosive gases like hydrogen chloride and chlorine trifluoride, which can degrade pure graphite. This resistance ensures the structural integrity of the susceptor, even in extreme conditions.
Coating Type | Performance in BWR Conditions | Observations |
---|---|---|
Cr | Low mass change | Promising candidate |
CrN | Low mass change | Promising candidate |
TiN | Rapid oxidation | Not suitable |
ZrN | Complete dissolution | Not suitable |
The table above highlights the superior performance of coatings like silicon carbide in corrosive environments. By preventing oxidation and chemical reactions, silicon carbide-coated susceptors maintain their durability and reduce the risk of contamination.
Superior Thermal Conductivity and Heat Management
Silicon carbide-coated graphite susceptors excel in thermal conductivity, ensuring efficient heat management during high-temperature processes. The coating enhances heat transfer, enabling uniform temperature distribution across the susceptor’s surface. This uniformity is critical for processes like chip growth, where consistent heating ensures high-quality results.
Thermal conductivity (W/mK) |
---|
300 |
The table demonstrates the impressive thermal conductivity of silicon carbide-coated materials. This property minimizes thermal stress, reducing the likelihood of deformation or cracking. As a result, these susceptors improve process stability and enhance the quality of semiconductor wafers.
Increased Durability and Reduced Maintenance Costs
Silicon carbide coating significantly extends the lifespan of graphite susceptors. The coating’s wear resistance reduces material degradation, minimizing the need for frequent replacements. For instance, in abrasive environments, silicon carbide materials have shown three times the wear resistance compared to traditional materials. This durability translates to lower maintenance costs and fewer unscheduled downtimes.
- A refinery using silicon carbide materials reduced maintenance costs by 40% within three years.
- Continuous operation in abrasive slurry pipelines saved over $100,000 in five years.
- Extended equipment lifespan ensures long-term economic benefits for industrial applications.
By enhancing durability and reducing maintenance needs, silicon carbide-coated susceptors offer a cost-effective solution for high-temperature processes. Industries benefit from improved reliability and reduced operational expenses.
Compatibility with High-Temperature and High-Precision Processes
Graphite susceptors with silicon carbide coating demonstrate exceptional compatibility with high-temperature and high-precision processes. Their ability to withstand extreme conditions makes them indispensable in industries like semiconductor manufacturing, photovoltaic production, and advanced material processing.
The silicon carbide coating enhances the thermal stability of the susceptor. It prevents deformation and cracking during rapid temperature changes, ensuring consistent performance. This feature is critical in processes like chemical vapor deposition (CVD) and epitaxial growth, where precise temperature control directly impacts product quality. The coating also minimizes thermal stress, allowing the susceptor to maintain its structural integrity even at temperatures exceeding 1600°C.
High-precision processes demand materials that can deliver uniform heat distribution. The silicon carbide-coated surface ensures even temperature across the susceptor, reducing the risk of localized overheating. This uniformity is vital for applications like wafer fabrication, where minor temperature variations can lead to defects. By maintaining consistent thermal conditions, these susceptors improve yield rates and reduce material waste.
The coating also provides excellent chemical resistance, protecting the graphite substrate from reactive gases and corrosive environments. This resistance ensures that the susceptor remains stable and contamination-free, even in processes involving aggressive chemicals. Industries benefit from reduced downtime and maintenance costs, as the coated susceptors require less frequent replacement.
The Graphite Susceptor with Silicon Carbide offers a reliable solution for high-temperature and high-precision applications. Its advanced design supports demanding industrial processes, ensuring efficiency and long-term performance.
Nota: The superior compatibility of silicon carbide-coated susceptors with high-temperature and high-precision processes makes them a preferred choice for industries seeking enhanced productivity and reliability.
Real-World Applications of Graphite Susceptor with Silicon Carbide
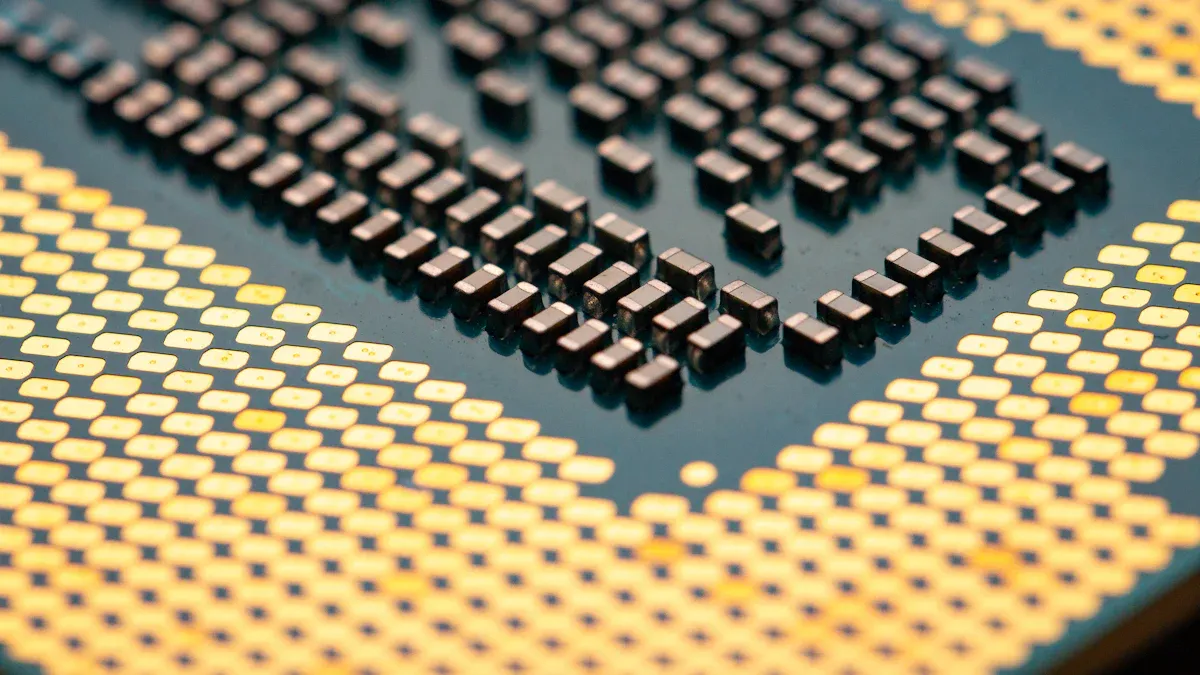
Semiconductor Manufacturing (e.g., CVD, MOCVD, Epitaxial Growth)
Graphite susceptors with silicon carbide coating play a pivotal role in semiconductor manufacturing processes such as Chemical Vapor Deposition (CVD), Metal-Organic Chemical Vapor Deposition (MOCVD), and epitaxial growth. These processes demand materials that can withstand extreme temperatures and maintain structural integrity. The silicon carbide coating enhances the thermal shock resistance of graphite susceptors by 22%, ensuring consistent performance during rapid temperature changes.
Metrico | Valore |
---|---|
Process yield improvement | 88.5% to 93.2% |
Sustained operation temperature | 1,600°C |
Mass loss over 1,000 cycles | < 0.5% |
Planarity requirement | ≤3µm across 600mm² |
The coating also minimizes contamination risks by preventing chemical reactions between the graphite substrate and process gases. This feature is critical for achieving high-quality yields in semiconductor wafer production, including 3DIC applications, where yield improvements of up to 8.3% have been reported.
Photovoltaic and Solar Cell Production
In the photovoltaic industry, silicon carbide-coated graphite susceptors are essential for producing high-efficiency solar cells. These susceptors reduce graphite consumption by 18% over three years, contributing to cost savings and sustainability. The global solar PV manufacturing capacity increased by 35% in 2023, reflecting the growing demand for advanced materials like silicon carbide-coated graphite.
- Orders for SiC-coated graphite parts grew by 22% in the same period.
- The coating’s versatility allows it to enhance thermal management in solar cell production, ensuring uniform heat distribution and reducing material waste.
This technology supports the production of high-purity monocrystalline silicon wafers, a critical component in solar energy systems.
New Energy Materials and High-Temperature Sintering
Graphite susceptors with silicon carbide coating are indispensable in the development of new energy materials. They are widely used in high-temperature sintering processes for lithium-ion battery components and electric vehicle power electronics. In chemical vapor deposition reactors, these susceptors enable the production of silicon carbide wafers, which are vital for electric vehicle applications.
- TaC-coated graphite bipolar plates, often used alongside SiC-coated susceptors, enhance corrosion resistance in proton exchange membrane electrolyzers.
- This innovation supports green hydrogen production, a key element in renewable energy strategies.
The ability of silicon carbide-coated graphite to withstand aggressive environments and high temperatures makes it a cornerstone in advancing clean energy technologies.
Case Studies Demonstrating Process Stability and Cost Savings
Real-world applications of the Graphite Susceptor with Silicon Carbide demonstrate its ability to enhance process stability and reduce operational costs. Below are two case studies showcasing its impact in industrial settings.
Case Study 1: Semiconductor Manufacturing Efficiency
A leading semiconductor manufacturer faced challenges with wafer contamination and frequent susceptor replacements. The company integrated silicon carbide-coated graphite susceptors into its chemical vapor deposition (CVD) process. The results were remarkable. The new susceptors reduced particle contamination by 35%, leading to a significant improvement in wafer yield. Additionally, the enhanced durability of the coated susceptors extended their service life by three times compared to uncoated graphite. This change minimized downtime and maintenance costs, saving the company over $200,000 annually.
Case Study 2: Solar Cell Production Optimization
A photovoltaic company sought to improve the efficiency of its solar cell production line. The introduction of silicon carbide-coated graphite susceptors addressed issues related to heat distribution and material degradation. The uniform thermal conductivity of the susceptors ensured consistent heating, reducing defects in solar wafers by 22%. Over a two-year period, the company reported a 15% increase in production capacity and a 20% reduction in material waste. These improvements translated into cost savings of approximately $150,000 per year.
Insight: These case studies highlight how silicon carbide-coated graphite susceptors enhance process reliability and reduce operational expenses. Industries can achieve higher productivity and long-term cost efficiency by adopting this advanced technology.
Silicon carbide coating elevates the performance of graphite susceptors, making them indispensable for industrial applications. This advanced coating addresses critical challenges like corrosion, contamination, and limited durability. By enhancing process stability, the Graphite Susceptor with Silicon Carbide ensures consistent results in high-temperature environments. Industries benefit from improved efficiency, reduced operational costs, and long-term reliability. These coated susceptors represent a significant step forward in meeting the demands of modern manufacturing processes.
FAQ
What is the purpose of silicon carbide coating on graphite susceptors?
Silicon carbide coating protects graphite susceptors from oxidation and corrosion. It enhances their durability and ensures stable performance in high-temperature environments. This coating also minimizes contamination risks, making it essential for precision-driven industries like semiconductor manufacturing and solar cell production.
How does silicon carbide improve heat distribution?
Silicon carbide offers superior thermal conductivity, ensuring even heat distribution across the susceptor’s surface. This uniformity prevents thermal stress and deformation, which are critical for maintaining process stability in applications like chemical vapor deposition (CVD) and epitaxial growth.
Can silicon carbide-coated susceptors reduce maintenance costs?
Yes, silicon carbide-coated susceptors last longer due to their resistance to wear and chemical damage. Their extended lifespan reduces the need for frequent replacements, lowering maintenance costs and minimizing downtime in industrial processes.
What industries benefit most from silicon carbide-coated graphite susceptors?
Industries like semiconductor manufacturing, photovoltaic production, and advanced material processing benefit significantly. These susceptors support high-temperature and high-precision processes, ensuring efficiency, reliability, and cost savings in demanding applications.
Are silicon carbide-coated susceptors customizable?
Yes, manufacturers like Semicera offer customization options. Adjustments in size, coating thickness, and other parameters ensure compatibility with specific industrial processes, enhancing performance and meeting unique production requirements.
Suggerimento: Customization ensures that susceptors align perfectly with process needs, maximizing efficiency and reliability.