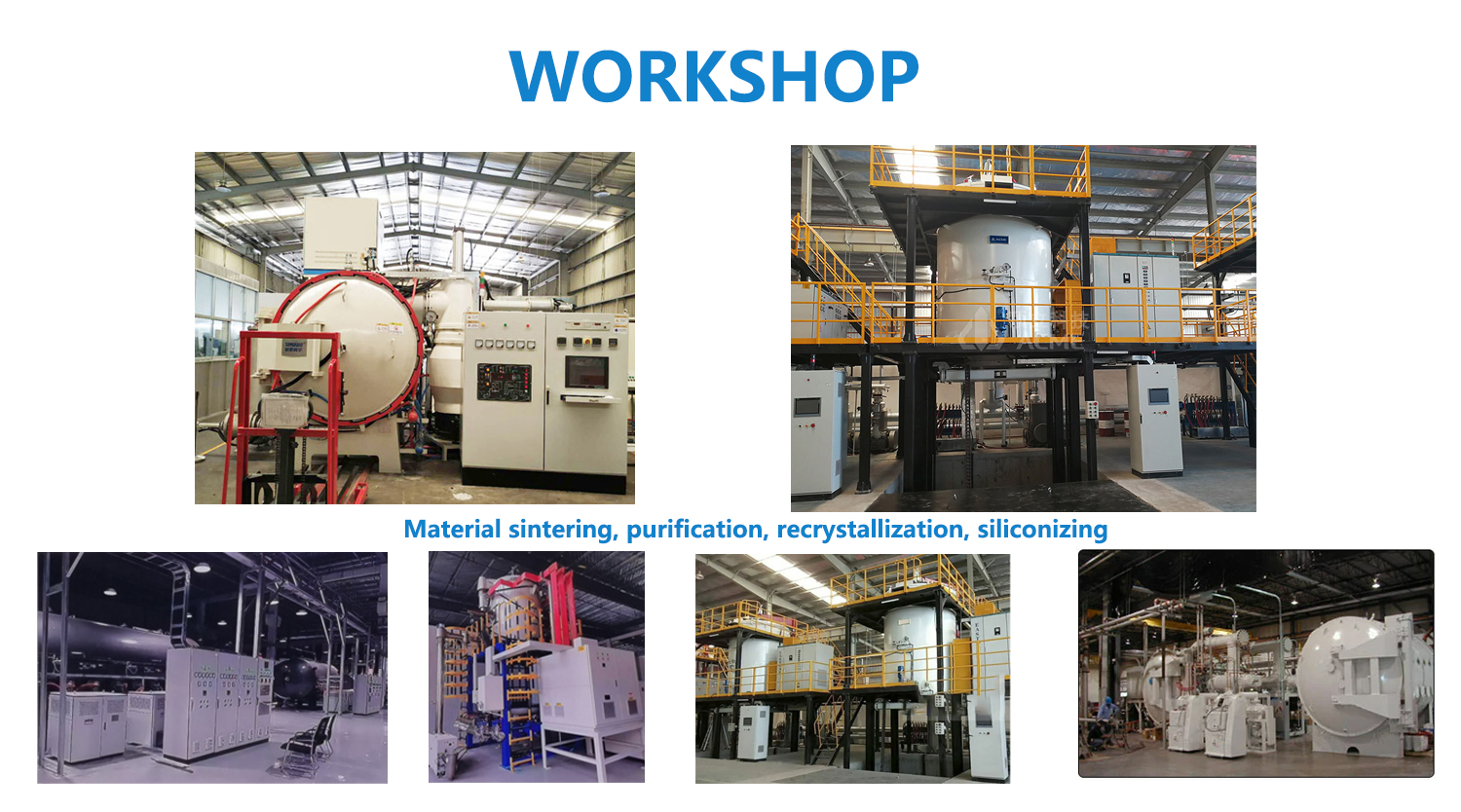
The semiconductor industry in 2025 demands unprecedented advancements in efficiency, precision, and durability. With the rise of artificial intelligence and high-performance computing, manufacturers must innovate to meet these challenges. Materials like 炭化ケイ素セラミックコーティング have become indispensable. This SIC Coating enhances wear resistance, thermal stability, and chemical corrosion resistance, making it ideal for high-temperature and abrasive environments. Its ability to withstand temperatures up to 1600°C and resist chemical erosion ensures reliable performance in corrosive conditions. By leveraging silicon carbide particles, SIC coatings deliver unmatched durability and efficiency for semiconductor manufacturing.
要点
- 炭化ケイ素 Ceramic Coating makes tools stronger and last longer.
- It handles very high heat, up to 1600°C, without breaking.
- The coating stops harmful chemicals from damaging tools, adding 40% more life.
- It helps control heat, stopping tools from getting too hot.
- Using this coating lowers repair costs and boosts production speed.
- It saves energy and reduces waste, helping the environment.
- Special methods like CVD make the coating even and long-lasting.
- This coating is key for new tech like AI, IoT, and 5G.
What is Silicon Carbide Ceramic Coating?
Overview of Silicon Carbide
Silicon carbide, often referred to as SiC, is a compound of silicon and carbon. It is renowned for its extraordinary hardness, thermal stability, and chemical resistance. These properties make it a preferred material in industries requiring high-performance solutions. In semiconductor manufacturing, silicon carbide plays a pivotal role due to its ability to withstand extreme conditions while maintaining structural integrity. Its unique characteristics, such as high sublimation temperature (approximately 2,700°C) and chemical inertness, make it an ideal choice for protective coatings.
Key Properties of Silicon Carbide Ceramic Coating
Exceptional Thermal Resistance
I find that one of the most impressive features of silicon carbide ceramic coating is its ability to endure extreme temperatures. It remains stable in environments reaching up to 1600°C, which is critical for semiconductor processes involving high heat. This thermal resistance ensures that equipment coated with silicon carbide operates reliably, even under the most demanding conditions.
Superior Chemical Stability
Silicon carbide ceramic coating exhibits remarkable chemical stability. It resists acids, alkalis, and other corrosive substances, thanks to the formation of a thin passivated SiO2 layer. This property allows the coating to protect semiconductor equipment from chemical erosion, ensuring longevity and consistent performance.
High Mechanical Durability
The coating’s mechanical durability is another standout feature. With a hardness approaching that of diamond, silicon carbide ceramic coating offers exceptional wear resistance. This makes it ideal for protecting components exposed to abrasive environments, reducing the need for frequent replacements or repairs.
Characteristic | 説明 |
---|---|
高い硬度 | Approaching that of diamond, providing excellent wear resistance. |
High-Temperature Stability | Maintains stability in environments up to 1600°C. |
化学安定性 | Significant resistance to various chemical media. |
Excellent Thermal Conductivity | Widely applicable in heat dissipation and thermal management fields. |
How Silicon Carbide Ceramic Coating is Manufactured
化学気相成長法(CVD)
化学気相成長法(CVD) is a widely used method for applying silicon carbide ceramic coating. In this process, silicon carbide precursors are introduced into a reactor. These precursors react with a carbon-containing gas at high temperatures, forming a thin, uniform SiC layer on the substrate. This technique ensures high purity and a robust bond between the coating and the underlying material.
物理蒸着(PVD)
Physical Vapor Deposition (PVD) is another effective method for manufacturing silicon carbide ceramic coatings. This process involves vaporizing the coating material in a vacuum and depositing it onto the substrate. PVD produces a dense, durable coating that enhances the performance of semiconductor equipment. It is particularly useful for applications requiring precise control over coating thickness and composition.
By leveraging these advanced manufacturing techniques, silicon carbide ceramic coatings achieve the durability, thermal resistance, and chemical stability needed for semiconductor manufacturing. These coatings not only protect equipment but also optimize performance, making them indispensable in the industry.
Applications of Silicon Carbide Ceramic Coating in Semiconductor Manufacturing
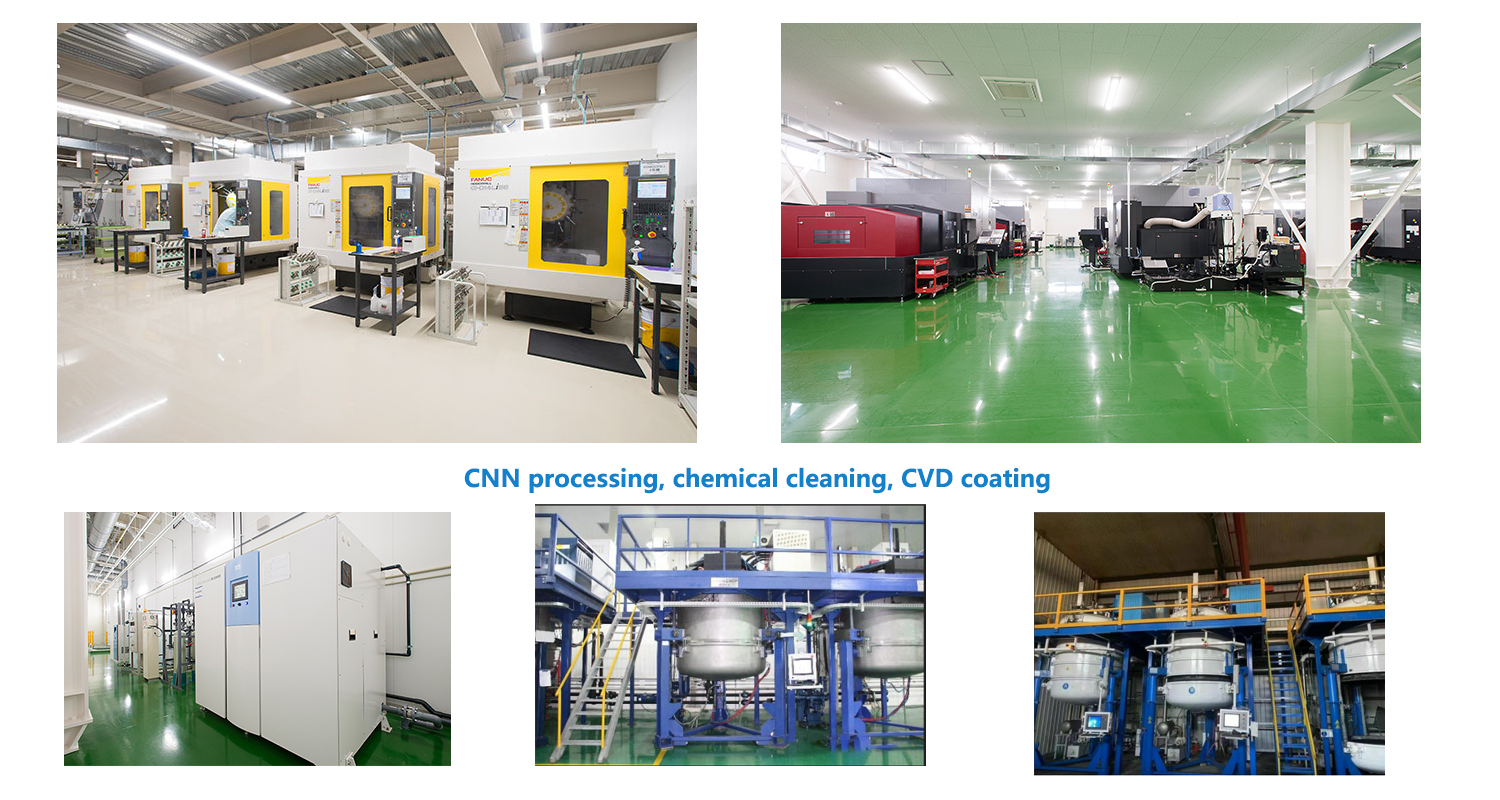
Enhancing Wafer Processing Equipment
Protection Against Corrosive Chemicals
I’ve seen how wafer processing equipment faces constant exposure to corrosive chemicals during semiconductor manufacturing. Silicon carbide ceramic coating acts as a robust shield, protecting critical components from chemical erosion. Its ability to resist acids, alkalis, and oxidation ensures that equipment maintains its integrity even in the harshest environments. The coating’s high-temperature stability, up to 1600°C, further enhances its protective capabilities. This makes it an essential solution for processes like Chemical Vapor Deposition (CVD) and Plasma-Enhanced Chemical Vapor Deposition (PECVD), where high heat and reactive gases are common. By applying this coating through advanced CVD techniques, manufacturers achieve a high-purity, durable layer that significantly extends equipment life.
Improved Thermal Management
Thermal management is crucial in wafer processing, and I’ve found that silicon carbide ceramic coating excels in this area. Its high thermal conductivity ensures efficient heat dissipation, which prevents localized overheating. This property allows for precise temperature control, a critical factor in achieving consistent results during semiconductor fabrication. The coating evenly distributes heat across the equipment, optimizing performance and reducing the risk of thermal damage. Its application in heat dissipation and thermal management fields has proven invaluable, particularly in environments requiring stringent temperature regulation.
Role in Plasma Etching and Deposition Processes
Plasma etching and deposition processes demand materials that can withstand extreme conditions. Silicon carbide ceramic coating provides a high-performance protective layer that excels in these applications. I’ve observed how its exceptional thermal resistance and chemical stability make it ideal for environments involving high temperatures and corrosive plasma. The coating prevents damage to equipment caused by reactive ions and gases, ensuring durability and efficiency. Its superior thermal conductivity also aids in maintaining precise temperature control, which is essential for achieving high-quality results in these processes. By enhancing the reliability of manufacturing tools, this coating supports the production of advanced semiconductor devices.
Extending the Lifespan of Manufacturing Tools
Manufacturing tools coated with silicon carbide ceramic experience a significant increase in lifespan. I’ve seen cases where tools upgraded with ceramic coatings achieved up to 40% longer life when used in demanding applications. This improvement reduces downtime and maintenance costs, offering substantial savings for manufacturers. The coating minimizes friction, reduces soldering in casting, and prevents micro-cracks, all of which contribute to enhanced tool performance. Machines with coated components require fewer service intervals, leading to more consistent production and improved operational efficiency. By investing in silicon carbide ceramic coating, manufacturers can ensure their tools remain reliable and productive over extended periods.
Supporting Advanced Technologies (e.g., AI, IoT, and 5G)
I’ve observed that advanced technologies like AI, IoT, and 5G demand semiconductor manufacturing processes that are more precise and reliable than ever before. These technologies rely on high-performance chips capable of handling immense data loads, operating at high speeds, and maintaining efficiency under extreme conditions. Silicon carbide ceramic coating plays a pivotal role in meeting these requirements.
One of the key benefits of this coating is its ability to withstand high temperatures, up to 1600°C. This feature is critical for processes like MOCVD and epitaxial growth, which are essential for producing high-quality semiconductor wafers. The coating’s thermal conductivity ensures even heat distribution, preventing localized overheating and maintaining the integrity of the chips. This level of precision is indispensable for AI processors, which require consistent performance to handle complex algorithms.
The chemical stability of silicon carbide ceramic coating also makes it ideal for environments involving reactive gases like hydrogen, ammonia, and methane. These gases are commonly used in processes such as CVD, PECVD, and PVD thin film deposition. I’ve seen how the coating’s resistance to chemical erosion ensures that manufacturing tools remain reliable, even in corrosive conditions. This reliability is crucial for IoT devices, which often operate in harsh environments and require durable components to maintain connectivity and functionality.
For 5G technology, the demand for high-frequency, low-latency communication has pushed the boundaries of semiconductor design. Silicon carbide ceramic coating enhances the performance of RF and DC plasma processes, which are vital for producing the advanced materials used in 5G chips. Its wear resistance and hardness protect critical components from damage, reducing downtime and ensuring uninterrupted production. This durability translates to faster deployment of 5G networks and more reliable devices for end users.
In my experience, the integration of silicon carbide ceramic coating into semiconductor manufacturing not only supports the growth of AI, IoT, and 5G but also drives innovation across the industry. Its unique combination of thermal, chemical, and mechanical properties makes it an indispensable solution for advancing these transformative technologies.
Benefits of Silicon Carbide Ceramic Coating
Increased Efficiency in Manufacturing Processes
I’ve seen firsthand how manufacturing efficiency improves when using silicon carbide ceramic coating. This coating optimizes thermal management, which is critical in semiconductor production. Its high thermal conductivity ensures even heat distribution, preventing hotspots that could disrupt processes. By maintaining consistent temperatures, the coating reduces the risk of defects during wafer fabrication. This leads to smoother operations and fewer interruptions.
Another way it boosts efficiency is by minimizing downtime. Equipment coated with silicon carbide operates longer without requiring maintenance. The coating’s resistance to wear and corrosion ensures that tools remain in peak condition, even in harsh environments. This reliability allows manufacturers to maintain high production rates without frequent pauses for repairs or replacements. In my experience, this translates to faster turnaround times and higher throughput.
Enhanced Durability and Reduced Maintenance Costs
Durability is one of the standout features of silicon carbide ceramic coating. I’ve observed how its exceptional hardness protects equipment from wear and tear. Components exposed to abrasive materials or high-friction environments benefit greatly from this coating. It prevents surface degradation, extending the lifespan of critical tools.
Reduced maintenance costs are another significant advantage. The coating’s chemical stability shields equipment from corrosive substances, such as acids and alkalis, commonly used in semiconductor processes. This protection eliminates the need for frequent part replacements. I’ve seen manufacturers save substantial amounts by investing in this coating. The reduced need for repairs not only cuts costs but also minimizes production delays, ensuring operations run smoothly.
Improved Yield and Product Quality
In my experience, silicon carbide ceramic coating plays a vital role in improving product quality. Its ability to maintain precise temperature control ensures uniformity during wafer processing. This consistency reduces the likelihood of defects, resulting in higher-quality semiconductor chips. Manufacturers can achieve better yields, as fewer products are discarded due to imperfections.
The coating also enhances the performance of tools used in plasma etching and deposition processes. Its resistance to reactive ions and gases prevents contamination, which is crucial for maintaining the purity of semiconductor materials. I’ve noticed that this leads to more reliable and efficient production, meeting the stringent standards of advanced technologies like AI and 5G.
By integrating silicon carbide ceramic coating into manufacturing processes, I’ve seen companies achieve a competitive edge. The combination of efficiency, durability, and quality makes this coating an indispensable solution for the semiconductor industry.
Cost-Effectiveness Over Time
I’ve observed that investing in silicon carbide ceramic coating delivers significant cost savings over time. While the initial application may seem like a substantial expense, the long-term benefits far outweigh the upfront costs. This coating enhances the durability of semiconductor manufacturing equipment, reducing the frequency of repairs and replacements. By extending the lifespan of critical components, manufacturers can allocate resources more efficiently.
One of the key advantages I’ve noticed is the reduction in downtime. Equipment coated with silicon carbide operates reliably for extended periods, minimizing interruptions in production. This consistency leads to higher throughput and fewer delays, which directly impacts profitability. Additionally, the coating’s resistance to wear and chemical corrosion ensures that tools maintain their performance, even in harsh environments. This reliability eliminates the need for frequent maintenance, saving both time and labor costs.
Another factor contributing to cost-effectiveness is the improved yield in semiconductor manufacturing. The coating’s ability to maintain precise temperature control and resist contamination results in fewer defects during production. Higher-quality output means fewer discarded products, which translates to better resource utilization. Over time, these efficiencies add up, making silicon carbide ceramic coating a smart investment for manufacturers aiming to optimize their operations.
Sustainability and Energy Efficiency
Sustainability has become a critical focus in semiconductor manufacturing, and I’ve seen how silicon carbide ceramic coating aligns perfectly with these goals. Its exceptional durability reduces the need for frequent replacements, which minimizes waste and conserves resources. By extending the lifespan of manufacturing tools, this coating supports a more sustainable production process.
I’ve also noticed how the coating contributes to energy efficiency. Its high thermal conductivity ensures effective heat dissipation, reducing energy consumption during semiconductor fabrication. This efficiency not only lowers operational costs but also decreases the environmental impact of manufacturing processes. In applications like electric vehicles and LED lighting, silicon carbide semiconductors enhance energy efficiency, leading to significant reductions in emissions.
The recyclability of silicon carbide-coated components further supports sustainability. At the end of their lifecycle, these materials can be effectively recycled, minimizing their environmental footprint. This aligns with the industry’s push toward greener practices and demonstrates the coating’s role in promoting a circular economy.
In my experience, silicon carbide ceramic coating represents a perfect blend of performance and environmental responsibility. It helps manufacturers meet their sustainability targets while maintaining the efficiency and reliability required for advanced semiconductor production.
Why Silicon Carbide Ceramic Coating is Essential in 2025
Meeting the Demands of Advanced Semiconductor Nodes
I’ve seen how advanced semiconductor nodes push manufacturing processes to their limits. These nodes require materials that can endure extreme conditions while maintaining precision. Silicon carbide ceramic coating meets these demands with its exceptional high-temperature stability. It withstands temperatures up to 1600°C, ensuring reliable performance in heat-intensive environments. This stability is critical for processes like epitaxial growth and plasma etching, where even slight temperature fluctuations can compromise results.
The coating’s chemical corrosion resistance also plays a vital role. It protects equipment from acids, alkalis, and other aggressive agents commonly used in semiconductor manufacturing. This protection ensures that tools remain functional and precise, even in harsh conditions. Additionally, its high thermal conductivity prevents localized overheating by evenly distributing heat. This feature supports the precise temperature control required for advanced semiconductor nodes, reducing defects and improving yield. In my experience, this combination of properties makes silicon carbide ceramic coating indispensable for meeting the challenges of modern semiconductor production.
Addressing Sustainability and Energy Efficiency Goals
Sustainability has become a top priority for the semiconductor industry. I’ve noticed how silicon carbide ceramic coating aligns perfectly with these goals. Its durability reduces the need for frequent replacements, minimizing waste and conserving resources. By extending the lifespan of manufacturing tools, it supports a more sustainable production process.
Energy efficiency is another area where this coating excels. Its high thermal conductivity ensures effective heat dissipation, reducing energy consumption during manufacturing. This efficiency not only lowers operational costs but also decreases the environmental impact of production. For example, in applications like electric vehicles and renewable energy, silicon carbide-coated components enhance energy efficiency, contributing to significant reductions in emissions. I’ve seen how this coating helps manufacturers meet their sustainability targets while maintaining high performance.
Supporting the Growth of Emerging Technologies
Emerging technologies like electric vehicles, renewable energy, and advanced computing rely heavily on efficient and durable semiconductor components. Silicon carbide ceramic coating plays a crucial role in supporting these advancements.
- It enhances the efficiency and longevity of semiconductor tools, which is essential for sectors like electric vehicles and renewable energy.
- North America leads the market for silicon carbide coatings, with a projected growth rate of over 10% from 2023 to 2030, driven by the increasing demand for electric vehicles.
- The Asia Pacific region is experiencing rapid growth, with a 12% CAGR fueled by semiconductor applications and renewable energy investments.
- Europe emphasizes sustainability, with a growth rate of approximately 9%, focusing on innovations in automotive and renewable energy technologies.
I’ve observed how this coating’s unique properties, such as wear resistance and thermal stability, make it ideal for producing high-performance chips. These chips power the technologies shaping our future, from AI to 5G networks. By integrating silicon carbide ceramic coating into manufacturing processes, we can drive innovation and meet the demands of a rapidly evolving technological landscape.
Ensuring Reliability in High-Temperature Environments
I’ve seen firsthand how high-temperature environments challenge semiconductor manufacturing. Processes like epitaxial growth, plasma etching, and 化学蒸着 (CVD) demand materials that can endure extreme heat without compromising performance. Silicon carbide ceramic coating excels in these conditions, offering unmatched reliability and protection for critical equipment.
One of the standout features of this coating is its high-temperature stability. It remains effective at temperatures up to 1600°C, ensuring consistent performance even in the most demanding applications. This stability is vital for maintaining precision during semiconductor fabrication, where even minor temperature fluctuations can lead to defects. The coating’s ability to withstand such heat makes it indispensable for advanced manufacturing processes.
The application method also plays a crucial role in ensuring reliability. I’ve observed how the use of high-purity CVD reactors during the coating process creates a uniform and durable layer. This method ensures a strong bond between the coating and the substrate, enhancing its resistance to thermal stress. The table below highlights the key aspects of this application method:
Application Method | 説明 |
---|---|
Chemical Vapor Deposition | High purity CVD reactor for coating application |
In addition to thermal stability, the coating offers excellent chemical resistance. It protects equipment from corrosive substances like acids and alkalis, which are commonly used in semiconductor processes. This dual protection against heat and chemicals ensures that tools remain reliable over extended periods, reducing the risk of downtime and costly repairs. The following table summarizes the coating’s critical properties:
プロパティ | バリュー |
---|---|
High-Temperature Stability | Up to 1600°C |
Chemical Resistance | Excellent |
Another factor contributing to reliability is the coating’s ability to manage heat effectively. Its high thermal conductivity ensures even heat distribution, preventing localized overheating. This feature not only protects equipment but also enhances the precision of temperature-sensitive processes. I’ve seen how this capability improves the overall efficiency of semiconductor manufacturing, leading to higher yields and better product quality.
In my experience, silicon carbide ceramic coating represents the gold standard for reliability in high-temperature environments. Its combination of thermal stability, chemical resistance, and effective heat management makes it an essential solution for the semiconductor industry. By investing in this advanced coating, manufacturers can ensure their equipment performs consistently, even under the most extreme conditions.
Future Trends in Silicon Carbide Ceramic Coatings
Innovations in Coating Application Techniques
I’ve noticed that advancements in coating application techniques are transforming the semiconductor industry. One of the most cutting-edge methods involves using high-temperature, high-purity Chemical Vapor Deposition (CVD) reactors. This technique ensures a uniform and durable silicon carbide layer, enhancing the performance of components in semiconductor manufacturing. Processes like CVD and PECVD rely heavily on these advanced application methods to achieve precision and reliability.
Several innovative sintering techniques are also gaining traction. These include:
- Reaction sintering
- Pressureless sintering
- Recrystallization sintering
- Hot pressing
- Hot isostatic pressing
- Spark plasma sintering
- Flash sintering
- Oscillatory pressure sintering
Each method offers unique benefits, such as improved bonding strength, reduced porosity, and enhanced thermal stability. These innovations allow manufacturers to tailor coatings to meet specific operational demands, ensuring optimal performance in high-stress environments.
Development of Hybrid Coating Materials
The development of hybrid coating materials is another exciting trend I’ve observed. Traditional silicon carbide materials often contain free silicon, which can limit their effectiveness in certain applications. To address this, the industry is shifting toward CVD-coated silicon carbide. This advancement eliminates free silicon, resulting in coatings with superior chemical resistance and thermal stability.
Hybrid materials are expanding the use of silicon carbide coatings across various industries. For example, combining silicon carbide with other advanced materials enhances its mechanical properties, making it suitable for even more demanding applications. These hybrid coatings are particularly valuable in semiconductor manufacturing, where precision and durability are paramount.
Integration with Smart Manufacturing Technologies
Smart manufacturing technologies are reshaping the way silicon carbide ceramic coatings are applied and utilized. I’ve seen how the integration of sensors and data analytics into coating processes enables real-time monitoring and quality control. This ensures consistent application and reduces the likelihood of defects.
Emerging trends like tailored coatings and smart coating technologies are also gaining momentum. Tailored coatings are designed to meet the specific needs of different semiconductor materials, while smart coatings can adapt to environmental changes, such as temperature fluctuations or chemical exposure. These advancements not only improve the efficiency of manufacturing processes but also enhance the performance and longevity of coated components.
The semiconductor industry is also adopting eco-friendly solutions and advanced nanotechnology in coating development. These innovations contribute to energy savings, reduced greenhouse gas emissions, and improved system performance. As the market for semiconductor ceramic coatings grows at a 7% CAGR, these trends will play a crucial role in shaping the future of the industry.
Anticipated Industry Standards and Regulations
I’ve noticed that the semiconductor industry is rapidly evolving, and with it comes a growing emphasis on stringent standards and regulations. These guidelines aim to ensure product quality, environmental responsibility, and operational safety. Silicon carbide ceramic coatings, such as the one offered by Semicera, are uniquely positioned to meet and exceed these expectations.
1. Compliance with Environmental Regulations 🌍
Governments and industry bodies worldwide are prioritizing sustainability. I’ve observed that manufacturers now face stricter rules to reduce waste, emissions, and energy consumption. Silicon carbide ceramic coatings align perfectly with these goals. Their durability minimizes the need for frequent replacements, which reduces material waste. Additionally, the high thermal conductivity of these coatings enhances energy efficiency during semiconductor fabrication. This contributes to lower carbon footprints and supports compliance with global environmental initiatives like the Paris Agreement.
ヒント By choosing silicon carbide ceramic coatings, manufacturers can stay ahead of environmental regulations while improving operational efficiency.
2. Meeting Quality and Performance Benchmarks ✅
The semiconductor industry demands precision and reliability. I’ve seen how silicon carbide ceramic coatings help manufacturers meet these high standards. For example, the coating’s ability to withstand temperatures up to 1600°C ensures consistent performance in heat-intensive processes. Its chemical stability protects equipment from corrosive substances, maintaining the integrity of manufacturing tools. These properties align with ISO 9001 and other quality management standards, which emphasize durability and performance.
Key Standard | How Silicon Carbide Coating Complies |
---|---|
ISO 9001 | Ensures consistent quality and reliability in manufacturing. |
RoHS (Restriction of Hazardous Substances) | Free from harmful materials, supporting safer production. |
3. Adapting to Industry-Specific Guidelines 🏭
Each semiconductor application has unique requirements. I’ve noticed that silicon carbide ceramic coatings are versatile enough to meet these needs. For instance, in plasma etching, the coating’s wear resistance ensures tools last longer, reducing downtime. In wafer processing, its thermal conductivity supports precise temperature control, which is critical for advanced nodes. These capabilities align with industry-specific standards, such as SEMI S2 for equipment safety and SEMI F47 for voltage sag immunity.
4. Preparing for Future Regulations 🚀
I believe the future will bring even stricter standards as technologies like AI, IoT, and 5G continue to grow. Silicon carbide ceramic coatings are already ahead of the curve. Their sustainability, efficiency, and reliability make them a future-proof solution. By investing in these coatings, manufacturers can ensure compliance with upcoming regulations while maintaining a competitive edge.
注: Staying proactive about standards and regulations not only ensures compliance but also builds trust with customers and stakeholders.
In my experience, silicon carbide ceramic coatings represent more than just a protective layer. They are a strategic investment that helps manufacturers navigate the complex landscape of industry standards and regulations. By adopting these coatings, companies can achieve operational excellence while contributing to a more sustainable future.
課題と考察
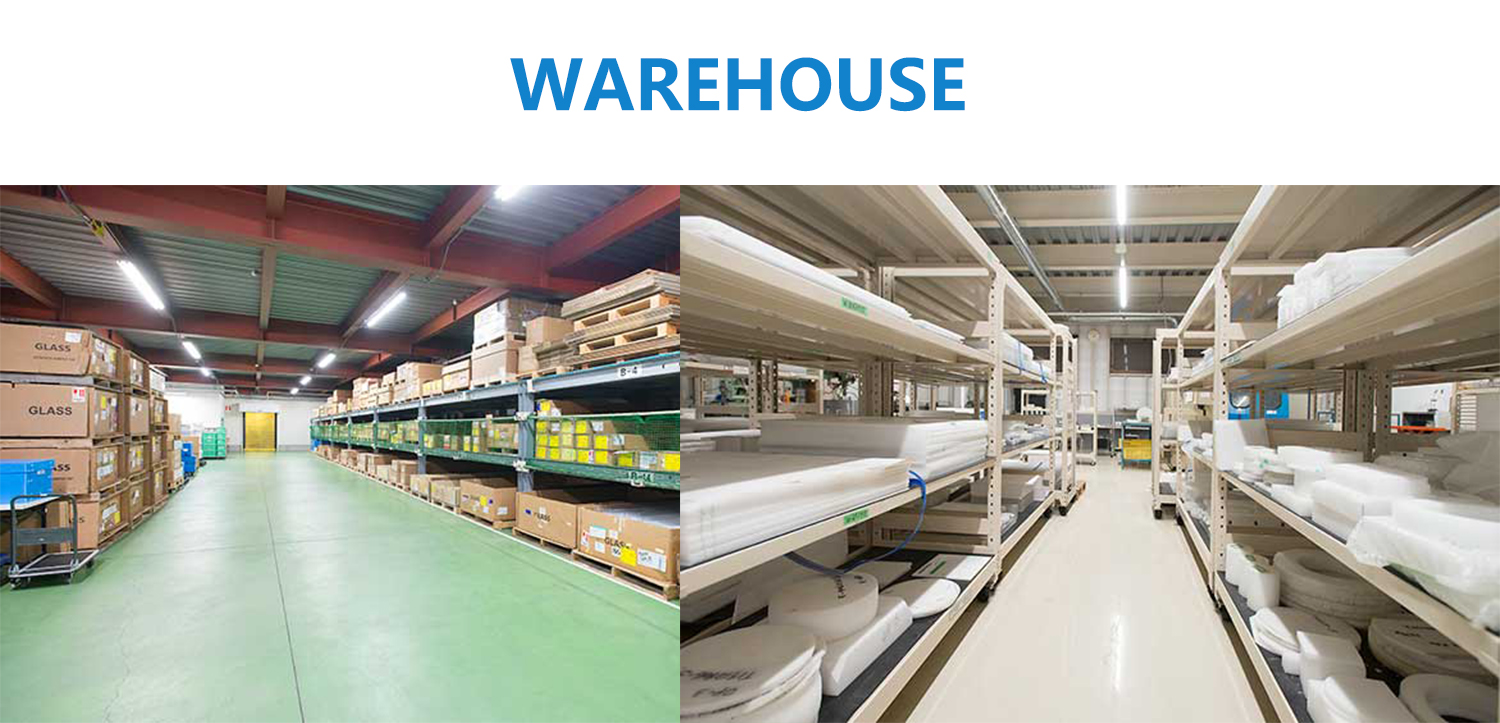
Cost of Implementation
I’ve observed that implementing silicon carbide ceramic coating requires careful financial planning. The costs associated with this technology can be divided into direct and indirect categories. Direct costs include material feedstock, operator labor, and fees for external coating services. Indirect costs often involve additional quality assurance checks, staff training, and storage for coated components. These factors can add up quickly, especially for manufacturers scaling up their operations.
To evaluate the financial viability of adopting this coating, I recommend using methods like payback period, net present value (NPV), internal rate of return (IRR), and total cost of ownership (TCO). These tools provide a clear picture of the long-term benefits versus the initial investment. The table below summarizes the primary cost considerations:
Cost Type | 説明 |
---|---|
Direct Costs | Material feedstock, operator labor, or fees from external coaters. |
Indirect Costs | Additional quality assurance checks, increased inventory levels, training for staff, and storage for coated parts. |
ROI Methods | Payback period, NPV, IRR, and TCO are crucial for evaluating financial viability. |
While the upfront costs may seem significant, I’ve seen how the long-term savings in maintenance and increased equipment lifespan often justify the investment.
Compatibility with Existing Manufacturing Processes
In my experience, silicon carbide ceramic coating integrates seamlessly with most semiconductor manufacturing processes. Its high-temperature stability, chemical corrosion resistance, and thermal conductivity make it an ideal choice for demanding applications. For instance, it performs exceptionally well in processes like Chemical Vapor Deposition (CVD) and Plasma-Enhanced Chemical Vapor Deposition (PECVD). These processes often involve extreme heat and reactive gases, which can degrade uncoated equipment. Silicon carbide ceramic coating protects against these challenges, ensuring reliable performance.
I’ve also noticed that this coating’s ability to withstand temperatures up to 1600°C makes it highly versatile. It enhances the durability of tools and equipment without requiring significant modifications to existing setups. This compatibility reduces the need for costly overhauls, allowing manufacturers to adopt the technology with minimal disruption.
Overcoming Technical Barriers in Adoption
Adopting silicon carbide ceramic coating on a large scale presents some technical challenges. I’ve identified two primary barriers that manufacturers must address:
- High production costs: The advanced techniques required to produce silicon carbide coatings, such as CVD and PVD, can be expensive. These methods demand specialized equipment and skilled operators, which increases the overall cost.
- Complexity in manufacturing SiC structures: Creating intricate silicon carbide-coated components requires precision and expertise. This complexity can slow down production and limit scalability.
Despite these challenges, I’ve seen how ongoing innovations in coating application techniques are helping to overcome these barriers. For example, advancements in sintering methods and hybrid materials are making the production process more efficient. By investing in research and development, manufacturers can reduce costs and improve the accessibility of this transformative technology.
注: Addressing these challenges requires a strategic approach. By focusing on cost optimization and technical innovation, manufacturers can unlock the full potential of silicon carbide ceramic coating.
Ensuring Quality Control and Consistency
I’ve always believed that quality control is the backbone of semiconductor manufacturing. In my experience, silicon carbide ceramic coating plays a pivotal role in ensuring consistent performance and reliability across production lines. Its unique properties make it an ideal solution for maintaining the high standards required in this industry.
Precision in Coating Application
The application process for silicon carbide ceramic coating demands precision. I’ve seen how advanced techniques like Chemical Vapor Deposition (CVD) ensure a uniform layer with minimal defects. This precision eliminates inconsistencies that could compromise the performance of semiconductor tools. For example, the high-purity CVD reactors used in the process create a flawless bond between the coating and the substrate. This ensures that every coated component meets the same rigorous standards.
ヒント Regular calibration of coating equipment ensures consistent application and minimizes variability.
Real-Time Monitoring and Inspection
I’ve noticed that integrating real-time monitoring systems into the coating process significantly enhances quality control. Sensors and automated inspection tools detect irregularities during application, allowing immediate adjustments. This proactive approach prevents defects from reaching the production floor. For instance, thermal imaging cameras can monitor temperature distribution during the coating process, ensuring uniform heat treatment.
Quality Control Tool | Function |
---|---|
Thermal Imaging Cameras | Monitor temperature distribution. |
Automated Optical Inspection (AOI) | Detect surface defects in real time. |
Meeting Industry Standards
Silicon carbide ceramic coating consistently meets stringent industry standards. I’ve observed how its chemical purity of 99.99995% ensures compliance with ISO 9001 and SEMI S2 guidelines. This level of purity minimizes contamination risks, which is critical for producing high-quality semiconductor wafers. The coating’s ability to withstand extreme temperatures and corrosive environments further guarantees reliability.
注: Adhering to industry standards not only ensures product quality but also builds trust with clients and stakeholders.
Consistency Across Batches
Batch-to-batch consistency is another area where silicon carbide ceramic coating excels. I’ve seen how manufacturers use statistical process control (SPC) to monitor production variables. This approach ensures that every batch of coated components performs identically, reducing variability in semiconductor manufacturing.
- Key Benefits of SPC in Coating Processes:
- Identifies trends and prevents defects.
- Maintains uniformity across production runs.
- Enhances overall process reliability.
Final Testing and Validation
Before coated components reach the production floor, they undergo rigorous testing. I’ve observed how manufacturers use stress tests to evaluate the coating’s performance under extreme conditions. These tests simulate high temperatures, corrosive environments, and mechanical stress to ensure the coating meets all operational requirements.
コールアウト Final validation ensures that only the highest-quality components are used in semiconductor manufacturing.
In my experience, silicon carbide ceramic coating sets the gold standard for quality control and consistency. Its precise application, real-time monitoring, and adherence to industry standards make it indispensable for semiconductor manufacturers aiming to achieve flawless production.
炭化ケイ素セラミックコーティング has become a cornerstone for semiconductor manufacturing in 2025. Its unmatched thermal resistance, chemical stability, and mechanical durability address the industry’s most pressing challenges. I’ve seen how its applications enhance efficiency, extend equipment lifespan, and improve product quality. These benefits make it indispensable for advanced manufacturing processes. As the industry evolves, I believe innovations in this coating will continue to drive sustainability, performance, and operational excellence. Its role in shaping the future of semiconductor technology cannot be overstated.
よくあるご質問
What makes silicon carbide ceramic coating ideal for semiconductor manufacturing?
Silicon carbide ceramic coating offers unmatched thermal resistance, chemical stability, and mechanical durability. It withstands temperatures up to 1600°C, resists corrosive chemicals, and protects equipment from wear. These properties make it indispensable for high-precision semiconductor processes.
How does silicon carbide ceramic coating improve equipment lifespan?
I’ve seen how this coating reduces wear and corrosion, extending the lifespan of manufacturing tools by up to 40%. Its hardness and chemical resistance minimize damage, ensuring tools remain reliable even in harsh environments.
Can silicon carbide ceramic coating enhance manufacturing efficiency?
Yes, it optimizes thermal management and reduces downtime. Its high thermal conductivity ensures even heat distribution, preventing overheating. This consistency improves production rates and reduces defects, leading to smoother operations.
Is silicon carbide ceramic coating environmentally friendly?
Absolutely. Its durability reduces waste by minimizing the need for replacements. High thermal conductivity lowers energy consumption during manufacturing, supporting sustainability goals. Recyclable components further contribute to eco-friendly practices.
What industries benefit most from silicon carbide ceramic coating?
I’ve observed its impact across semiconductor manufacturing, electric vehicles, renewable energy, and advanced computing. Its properties support high-performance chips for AI, IoT, and 5G, making it essential for emerging technologies.
How does the coating ensure product quality in semiconductor manufacturing?
The coating maintains precise temperature control and resists contamination. These features reduce defects during wafer processing, ensuring high-quality semiconductor chips. This consistency improves yield and meets the stringent standards of advanced technologies.
What application methods are used for silicon carbide ceramic coating?
Chemical Vapor Deposition (CVD) and Physical Vapor Deposition (PVD) are the primary methods. These techniques create a uniform, durable layer that enhances the performance and longevity of semiconductor equipment.
Why should manufacturers invest in silicon carbide ceramic coating?
I’ve seen how this coating delivers long-term cost savings by reducing maintenance and extending equipment lifespan. It improves efficiency, enhances product quality, and supports sustainability, making it a smart investment for any manufacturer.
ヒント Reach out to Semicera for tailored solutions that meet your specific manufacturing needs.