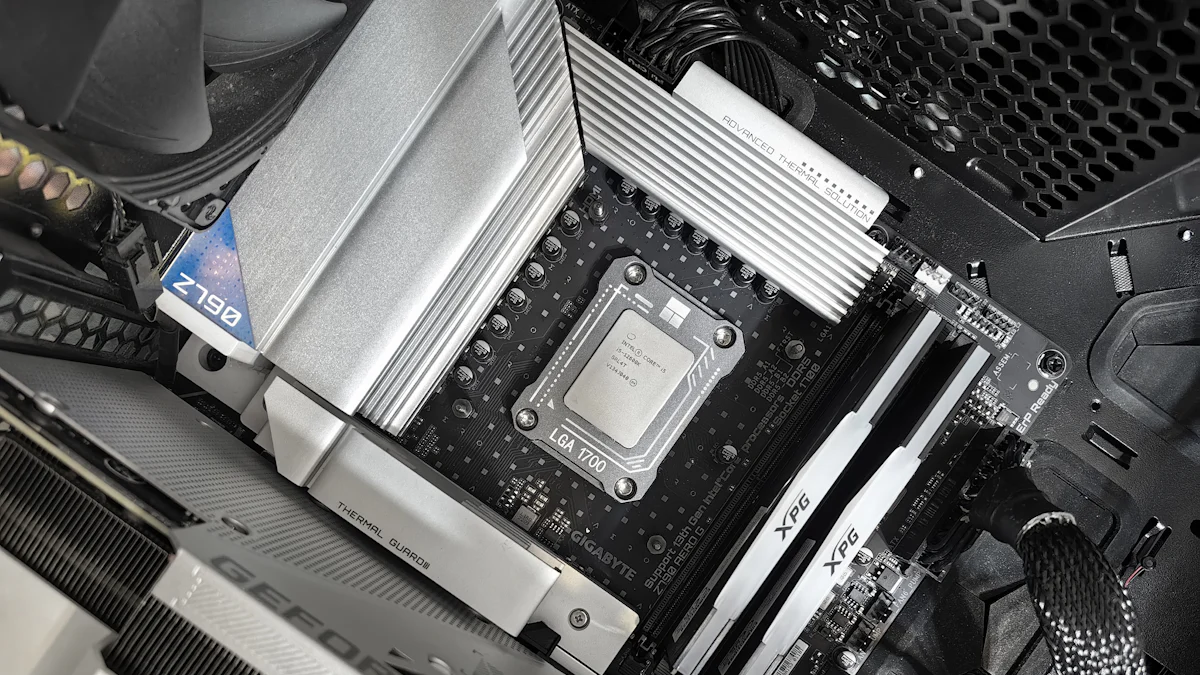
Silicon carbide coating for MOCVD プロセスは、パフォーマンスを向上させる上で重要な役割を果たします。 優れた熱安定性は、高温条件下で信頼性の高い動作を保証しますが、化学抵抗は腐食性環境から重要なコンポーネントを保護します。 これらの特性は、基質の完全性を維持し、一貫した薄膜の成長を可能にし、欠陥の危険性を減らすために不可欠です.
SiC coated susceptors、特に、提供することによってプロセス効率を高めて下さい 耐久、保護表面 摩耗および汚染に抵抗する。 この耐久性は、メンテナンスの必要性を最小限に抑え、コンポーネントの寿命を延ばし、運用コストを削減します。 歩留まりを改善し、エピタキシャル成長の均等性を保障します、, SiC coating for MOCVD 半導体製造、その他先端用途に欠かせない製品です.
要点
- 炭化ケイ素のコーティングは熱および抵抗の化学薬品で強いとどまることによってMOCVDの仕事をよりよく助けます.
- これらのコーティングは重要な部品を損傷および錆から安全保ちます、熱い場所でよく働かせます.
- SiCコーティングされた部品はプロセスをより速く、より低い間違いを作り、材料の質を改善し、作ります助けます より良い半導体.
- 炭化ケイ素のコーティングは堅い条件にもかかわらずグラファイトおよび水晶より強いです.
- 彼らの強さは企業のためのお金を節約するより少ない固定が必要であることを意味します.
- これらのコーティングはのためのキーです グリーンエネルギーのような新しい技術、電気自動車およびよりよいコミュニケーション用具.
- コーティング技術の新しいアイデアは、シリコンカーバイドを今日のニーズにさらに優れています.
- より多くの人々はハイテクなプロダクトをより正確および信頼できるように助けるので炭化ケイ素のコーティングを望みます.
MOCVDとコーティングの役割を理解する
What is MOCVD?
メタホロジー化学蒸気蒸着(MOCVD)は、基質に薄膜を作成するために使用されるプロセスです。 これらのフィルムは、半導体、LED、およびその他の高度な電子機器の製造に不可欠です。 工程中、金属化合物や反応ガスを加熱チャンバーに導入。 高温は、これらの化合物を分解し、材料の薄い層を基質に堆積させます.
フィルムの厚さと組成を正確に制御できます。 高性能な電子部品を製造するために重要なのは、均一性を保証します。 MOCVDは、光学系や再生可能エネルギーなどの産業に広く使われています。これにより、高品質の材料を効率的に生産することができます.
なぜ保護コーティングがMOCVDでCrucialであるのか
保護コーティングは、MOCVDプロセスの効率性と信頼性を確保するために重要な役割を果たしています。 高温および腐食性のガスのようなMOCVD部屋の中の極度な条件は保護されていない部品を損なうことができます。 炭化ケイ素のようなコーティングは摩耗および汚染からこれらの部品を保護する強い障壁を提供します.
SiC上塗を施してあるグラファイトの感受性 mOCVDプロセスでは、半導体および光電子工学の薄膜およびコーティングの準備の重要性を強調しています。 SiCコーティングは、MOCVDプロセスの要求条件に理想的な、優れた耐薬品性と熱安定性を提供します。 この安定性により、スセプターは、半導体製造に共通する高温および腐食性環境下でも構造的完全性を維持します。 CVD SiCコーティングされた感受性器の使用はMOCVDプロセスの全面的な効率を高めます。 欠陥を減らし、基質の質を改善することによって、これらの感受性はより高い収穫およびよりよい形成の半導体装置に貢献します.
コーティング材料の選択はMOCVD装置の性能に直接影響を与えます。 MOCVDのための炭化ケイ素のコーティングは優秀な熱安定性および化学抵抗が原因で好まれます。 これらの特性は、感受性者が維持することを確実にします 一貫した熱配分精密なフィルムの厚さおよび構成を達成するために必要である、.
複数 mOCVDプロセスの課題 更に保護コーティングの必要性を強調して下さい:
チャレンジ | 説明 |
---|---|
アクセサリー | 熱膨張係数の相違による低いコーティングの付着力は割れることおよび間隔につながります. |
フィードバック | 高温での性能に影響を与える不純物を防ぐため、超高純度が必要です. |
安定性 | 高温および腐食性の大気への抵抗は故障につながる欠陥を避けるために重要です. |
酸化抵抗 | 塗料は高温で酸化し始め、劣化や脱塩につながります. |
均一性と粗さ | 強烈なコーティングは熱応力を引き起こし、割れの危険性を高めることができます. |
穀物のサイズ | 均一粒径は安定性を高めます;より小さい穀物は酸化および腐食により多くの傾向があります. |
これらの課題に対処することで、炭化ケイ素コーティングはMOCVDシステムの耐久性と効率を保証します。 重要なコンポーネントを保護し、メンテナンスニーズを減らし、プロセス全体の信頼性を向上させます.
MOCVD用シリコンカーバイドコーティングの主な利点
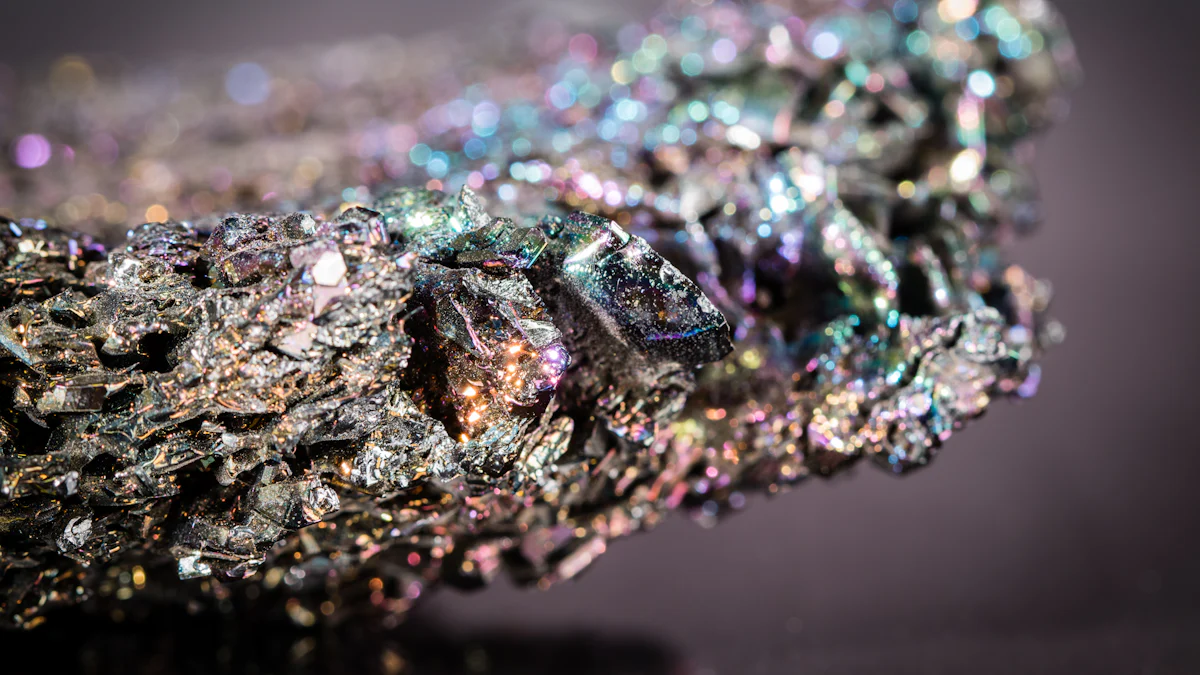
熱安定性および高温性能
炭化ケイ素のコーティングは高温環境で、それらにのための理想をさせます MOCVDアプリケーション. . これらのコーティングは、極端な熱の下で構造的完全性を維持し、信頼性の高い性能を保証します.
- SiC3立方炭化ケイ素の陶磁器のコーティングは温度にまで耐えます 1600°C 大気圧で.
- 酸素、水素、窒素などの反応環境で効果的に機能します.
- コーティングは、高温でガスの酸化や反応からコンポーネントを保護します.
この優れた熱安定性により、ウェーハ全体の一貫した熱分布が保証されます。 熱応力を最小化し、薄膜蒸着時の欠陥のリスクを低減します。 均一性を維持することにより、炭化ケイ素コーティングは最終製品の品質を向上させます.
化学抵抗および長寿
炭化ケイ素のコーティングはMOCVDプロセスのために重要な顕著な化学抵抗を提供します。 これらのコーティングは、腐食性ガスや劣化のない過酷な化学物質への暴露に耐える.
研究は、その α-SiCがうまく機能 穏やかな酸性および非酸化の環境で。 対照的に、β-SiCは強いアルカリおよび酸化条件への優秀な抵抗を示します。 この汎用性は、 炭化ケイ素 さまざまな化学環境に耐えるコーティング.
MOCVDの塗布では、感受性器の炭化ケイ素のコーティングは堅い、保護表面を提供します。 高温でも腐食や劣化に抵抗します。 スセプターの構造的完全性を維持することにより、これらのコーティングは長期的信頼性を保証します。 耐久性は、メンテナンス要件を減らし、運用コストを削減します.
プロセス効率および収穫の強化
炭化ケイ素のコーティングはMOCVDプロセスの効率そして収穫をかなり改善します。 熱安定性および化学抵抗はよりよい基質の質および少数の欠陥に貢献します.
Aspect | Benefit |
---|---|
熱安定性 | 付加的な熱安定性および酸化の保護を提供します. |
欠陥の減少 | 欠陥を減らし、基質の質を改善して下さい. |
収穫の改善 | 半導体製造における高い歩留まりに貢献します. |
耐食性 | 高温での腐食や劣化に抵抗します. |
熱配分 | ウェーハ全体の効率的な熱分布を促進します. |
これらの利点は、より高い生産性と高性能半導体デバイスに変換します。 プロセス効率を高めることによって、炭化ケイ素のコーティングは製造業者が高度の電子部品のための成長した要求を満たします.
MOCVD用シリコンカーバイドコーティングは、これらの結果を達成する際に重要な役割を果たしています。 そのユニークな特性は、精度と信頼性に依存する業界に不可欠です.
MOCVD Outperformsの代替品のための炭化ケイ素のコーティング
グラファイトコーティングとの比較
グラナイトコーティングは、それらによるMOCVDプロセスで頻繁に使用されます 優秀な熱伝導性. . 薄膜蒸着に欠かせない均一な熱分布を保証します。 しかし、グラファイトコーティングは高温環境の重要な制限に直面しています。 それらの化学的安定性は、特に反応性雰囲気の中で極端な熱の下で減少します。 この不安定性は、望ましくない反応につながり、エピタキシャルレイヤーの純度と一貫性を損なうことができます.
シリコンカーバイドコーティングは、一方、熱伝導性と化学的安定性の両方で優れています。 高温でも構造の整合性を維持し、信頼性の高い性能を保証します。 グラファイトとは異なり、炭化ケイ素は化学抵抗を高めるために追加のコーティングを必要としません。 これにより、MOCVD アプリケーションのより効率的で耐久性のある選択が可能になります。 不要な反応を防ぐことで、シリコンカーバイドコーティングは、高品質のフィルム蒸着とプロセスの信頼性の向上に貢献します.
水晶コーティングとの比較
水晶コーティングは化学純度および光学特性のために評価されます。 これらの特性は水晶を特定の適用のために適したようにします。 しかし、石英は、要求の厳しいMOCVDプロセスに必要な機械的強度と熱伝導性が欠けています。 高温下での耐久性は、先進半導体製造における有効性を制限します.
対照的に、炭化ケイ素のコーティングは例外的な熱安定性および伝導性を提供します。 構造の整合性を損なうことなく強烈な熱に耐え、高温用途に最適です。 また、シリコンカーバイドの機械的強度により、長持ちする性能が確保され、頻繁なメンテナンスの必要性が軽減されます。 これらの利点は炭化ケイ素のコーティングを精密および信頼性を要求する企業のための優秀な選択にします.
炭化ケイ素の独特な利点
シリコンカーバイドコーティングは、代替材料とは別にそれらを置くユニークな特性を持っています。 これらの利点は、MOCVDプロセスに不可欠です
- 優れた熱伝導性 沈殿物の間に精密な温度制御を保障します.
- 高い化学的安定性は、不要な反応を防ぎ、堆積フィルムの純度を維持します.
- 強い機械強さは粗い環境で摩耗し、引き裂きます抵抗します.
- 極端な条件下で確実な性能はプロセス効率を高めます.
- 比類のない耐久性および耐食性は重要な部品の寿命を拡張します.
炭化ケイ素のコーティングはまた欠陥の危険を減らす熱拡張の不一致を最小にします。 これにより、均一な熱分布が確保され、エピタキシャル層の品質が向上します。 これらの特性を組み合わせることで、炭化ケイ素のコーティングはMOCVDの適用の優秀な性能を提供します。 歩留まりを高め、維持費を削減する能力は、それらが現代の産業のための好まれる選択をします.
MOCVD用シリコンカーバイドコーティング用途
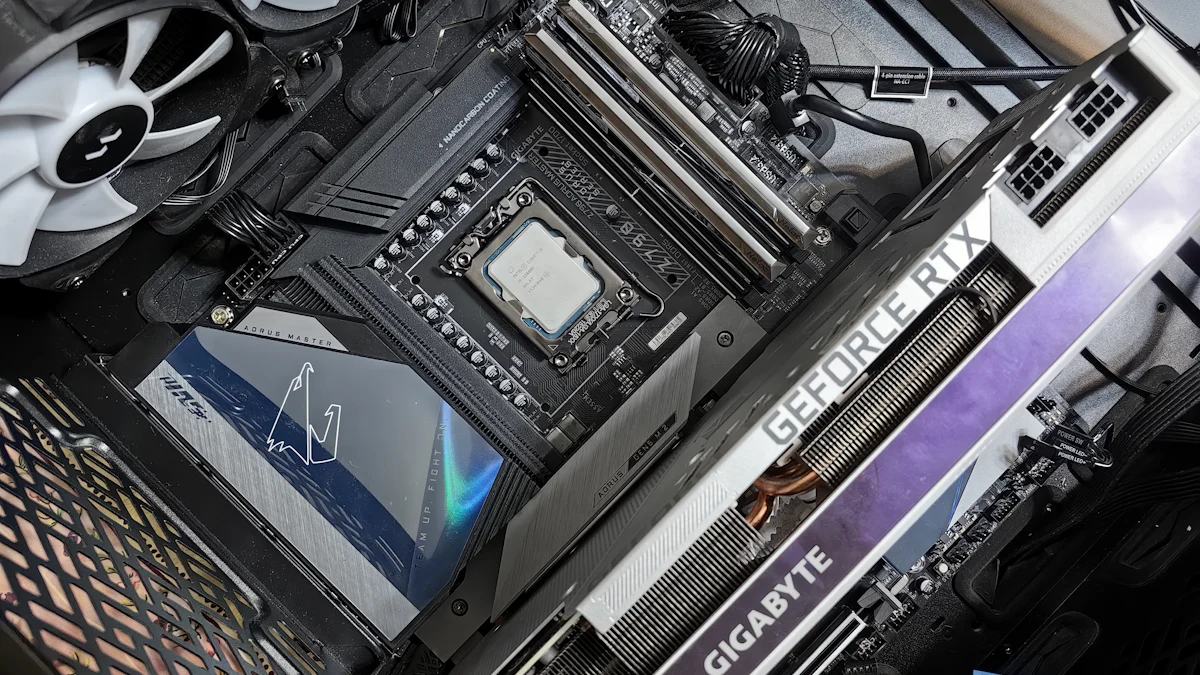
半導体製造
炭化ケイ素のコーティングは演劇をします 半導体製造における重要な役割. . これらのコーティングはあります mOCVDプロセスに不可欠、それらは沈殿物の部屋の中の粗い条件からのグラファイトの感受性を保護するところ。 これらの環境の極端な温度と反応性ガスは、非コーティングされたコンポーネントを劣化させることができます。 炭化ケイ素のコーティングは一貫した薄膜の成長を保障するために必要な熱安定性および化学抵抗を提供します.
- SiC上塗を施してあるグラファイトの感受性は熱安定性および酸化の保護を高めます。 薄膜蒸着時の均一性を維持するには、この安定性が不可欠です.
- コーティングは汚染および欠陥の危険を減らす化学腐食に抵抗します.
- 基質品質の向上により、シリコンカーバイドコーティングは半導体製造における高い歩留まりに貢献します.
これらの利点は、高性能半導体の製造に欠かせない炭化ケイ素コーティングを作ります。 厳しい条件に耐える能力は、信頼性と効率的な製造プロセスを保証します.
再生可能エネルギー技術
再生可能エネルギー部門は、効率と耐久性を向上させるために、先進材料に依存しています。 シリコンカーバイドコーティングは、使用されるコンポーネントの性能を高めることで、この目標をサポート MOCVDプロセス. . これらは、太陽電池や再生可能エネルギー技術で使用される薄膜を作成するために不可欠です.
炭化ケイ素のコーティングは沈殿物の間に精密な温度制御を保障する優秀な熱伝導性を提供します。 この精度は、より効率的な太陽電池につながる薄膜の品質を向上させます。 さらに、コーティングは摩耗および腐食に抵抗し、重要なコンポーネントの寿命を延ばします。 メンテナンスニーズを削減することにより、炭化ケイ素コーティングは再生可能エネルギーメーカーの運用コストを削減します.
再生エネルギーの需要は成長し続け、炭化ケイ素コーティングのような信頼できる材料の必要性を運転します。 独自の特性により、よりクリーンなエネルギー源への移行に価値のある資産が生まれます.
高技術の応用
MOCVDプロセスにおけるシリコンカーバイドコーティングの新たな機会を創出しています。 業種 等 電気自動車 (EV)、5Gワイヤレス通信と高度な光電子工学は、高品質の薄膜に依存しています。 シリコンカーバイドコーティングは、これらの用途に必要とされる精度と信頼性を保証します.
- パワーエレクトロニクスの生産における炭化ケイ素コーティングによる電気自動車のメリット これらのコーティングは、EV技術の開発を支えるコンポーネントの効率性と耐久性を向上させます.
- 5Gワイヤレス通信は、精密な薄膜で高度な半導体を必要とする。 炭化ケイ素のコーティングはこれらのフィルムの質を高めます、より速く、より信頼できるネットワークを可能にします.
- LEDやレーザーダイオードなどの光電子デバイスは、薄膜堆積のためのMOCVDプロセスに依存します。 炭化ケイ素のコーティングは一貫した性能を保障し、欠陥を減らし、収穫を改善します.
シリコンカーバイドコーティングの汎用性は、ハイテク産業の重要な材料となります。 新興アプリケーションのニーズを満たす能力は、近代的な製造の重要性を強調しています.
MOCVD用シリコンカーバイドコーティングの未来
コーティング技術の革新
コーティング技術の最近の進歩は、MOCVDの炭化ケイ素コーティングの性能を変えています。 これらの革新は熱安定性、化学抵抗および全面的な効率を改善することに焦点を合わせます。 研究者は、炭化ケイ素コーティングの特性を高めるために新しい方法を検討しています, 彼らは現代の産業の成長要求を満たしていることを確認します.
Innovation Type | 説明 |
---|---|
熱安定性および酸化の抵抗 | SiCコーティングは、薄膜成長の一貫性のために重要な高温環境で追加の熱安定性と酸化保護を提供します. |
物質的なインターフェイスおよび表面の特性制御 | SiCコーティング特性の調整により、フィルムと基板間の相互作用が向上し、成長モードとインターフェイスの品質を向上させることができます. |
不純物汚染を減らす | SiCコーティングの高純度は、基板からの不純物の汚染を最小限に抑え、エピタキシャルフィルムの高純度を保証します. |
生産プロセス改善 | 研究は、コーティングの純度と均一性を高め、コストを削減しながら品質と寿命を増加させることに焦点を当てています. |
新しいコーティング技術 | グラファイトの感受性のTACのコーティングの調査は熱伝導性および耐食性を改善します. |
これらの進歩は、炭化ケイ素コーティングが極端な条件下で信頼性を維持していることを保証します。 たとえば、表面特性の改善は、コーティングと基質の間の相互作用を高め、より良いフィルム成長につながる。 また、不純物の汚染を抑えることで、半導体製造に重要なエピタキシャルフィルムの純度が確保されます。 これらの分野に焦点を合わせることによって、研究者はより有効で、耐久のコーティングのための方法を舗装しています.
先進産業における需要の拡大
The demand for 炭化ケイ素コーティング mOCVDプロセスでは、さまざまな業界に急速に増加しています。 この成長は、新技術の高性能材料の必要性によって運転されます。 自動車、航空宇宙、通信、再生可能エネルギーなどの産業は、この需要をリードしています.
- 電気自動車は、先進的な半導体デバイスを必要とする、改善された効率および耐久性のための炭化ケイ素のコーティングに頼る.
- 再生可能エネルギーシステムは、これらのコーティングを使用して電力処理能力を高め、太陽電池製造に不可欠です.
- 5Gワイヤレス通信のロールアウトは、信頼性の高い半導体デバイスに依存し、炭化ケイ素コーティングの市場をさらに高めます.
- 航空宇宙用途は、シリコンカーバイドコーティングの熱安定性を利用して、高性能な環境を実現します.
- 消費者エレクトロニクスは、炭化ケイ素コーティングの精度と信頼性の恩恵を受けるエネルギー効率の高い装置を要求します.
について 自動車分野、特に炭化ケイ素系技術の使用拡大 電気自動車の上昇による。 同様に、, テレコミュニケーションとコンシューマーエレクトロニクスは、高度な半導体技術の必要性を駆動しています. . これらの業界は、現代の製造における炭化ケイ素コーティングの汎用性と重要性を強調しています.
業界は革新を続け、MOCVDの炭化ケイ素コーティングの役割はさらに重要になります。 そのユニークな特性は、精度、信頼性、耐久性を必要とする用途に不可欠です.
炭化ケイ素のコーティングは一致させた熱安定性および化学抵抗を渡すことによってMOCVDプロセスの成功を保障します。 耐久性は維持の必要性を減らし、部品寿命を拡張し、 重要なコスト節約. . インダストリーズは、効率と歩留まりを高める能力から恩恵を受け、代替品よりも好ましい選択をしています.
グローバルトレンドは、 炭化ケイ素コーティングの重要性の高まり mOCVD用 欧州は持続可能性に焦点を当てながら、アジア太平洋地域における急速な拡大と北米のドライブ需要の進歩。 企業の革新として、炭化ケイ素のコーティングは精密および信頼性を達成するために必要ままです.
よくあるご質問
シリコンカーバイドコーティングは、MOCVDプロセスに最適ですか?
炭化ケイ素のコーティング 熱安定性、耐薬品性、耐久性に優れています。 これらの特性は高温、腐食性の環境の信頼できる性能を保障します。 コンポーネントを保護し、メンテナンスを削減し、プロセスの効率性を改善し、MOCVDアプリケーションに不可欠です.
シリコンカーバイドコーティングが半導体製造を改善する方法は?
炭化ケイ素のコーティングは熱安定性を高め、化学腐食に抵抗します。 これは一貫した薄膜の沈着を保障し、欠陥を減らし、基質の質を改善します。 これらの利点は、より高い収量とより良い成形半導体デバイスにつながり、高度な製造に不可欠です.
炭化ケイ素のコーティングは費用効果が大きいですか?
はい、炭化ケイ素のコーティングは維持の必要性を減らし、部品寿命を拡張します。 耐久性は、ダウンタイムと交換コストを最小限に抑えます。 プロセスの効率および収穫を改善することによって、それらはMOCVDプロセスに頼る企業のための長期費用節約を提供します.
シリコンカーバイドコーティングは極端な温度に耐えることができますか?
炭化ケイ素のコーティングは極度な熱の下で例外的によく行います。 1600°Cまでの温度で構造的な完全性を維持します。 高温MOCVDプロセス中に一貫した熱分布と信頼性の高い性能を保証します.
炭化ケイ素のコーティングからの企業の利点は何ですか?
シリコンカーバイドコーティングから半導体製造、再生可能エネルギー、先進エレクトロニクスなどの産業が活用できます。 電気自動車、5G通信、光電子などの新興技術も、その精度と信頼性で重要である.
炭化ケイ素のコーティングはグラファイトのコーティングと比較しますか?
シリコンカーバイドコーティングは、優れた化学的安定性と熱伝導性を発揮することにより、グラファイトをアウトパーフォームします。 それらは反応環境の劣化に抵抗し、信頼できる性能を保障します。 グラファイトとは異なり、炭化ケイ素は追加のコーティングを必要としません。耐久性と効率的な選択を実現します.
なぜシリコンカーバイドコーティングが再生可能エネルギーにとって重要なの?
シリコンカーバイドコーティングは、太陽電池などの再生技術で使用されるコンポーネントの効率性と耐久性を向上させます。 蒸着中に精密な温度制御を確保し、薄膜品質を高め、メンテナンスニーズを減らし、クリーンなエネルギー供給への移行をサポートします.
What advancements are being made in silicon carbide coatings?
革新は熱安定性、化学抵抗およびコーティングの純度を改善することに焦点を合わせます。 研究者は表面特性を高め、不純物の汚染を減らします。 これらの進歩は炭化ケイ素のコーティングが現代企業の成長する要求に応じることを確認します.