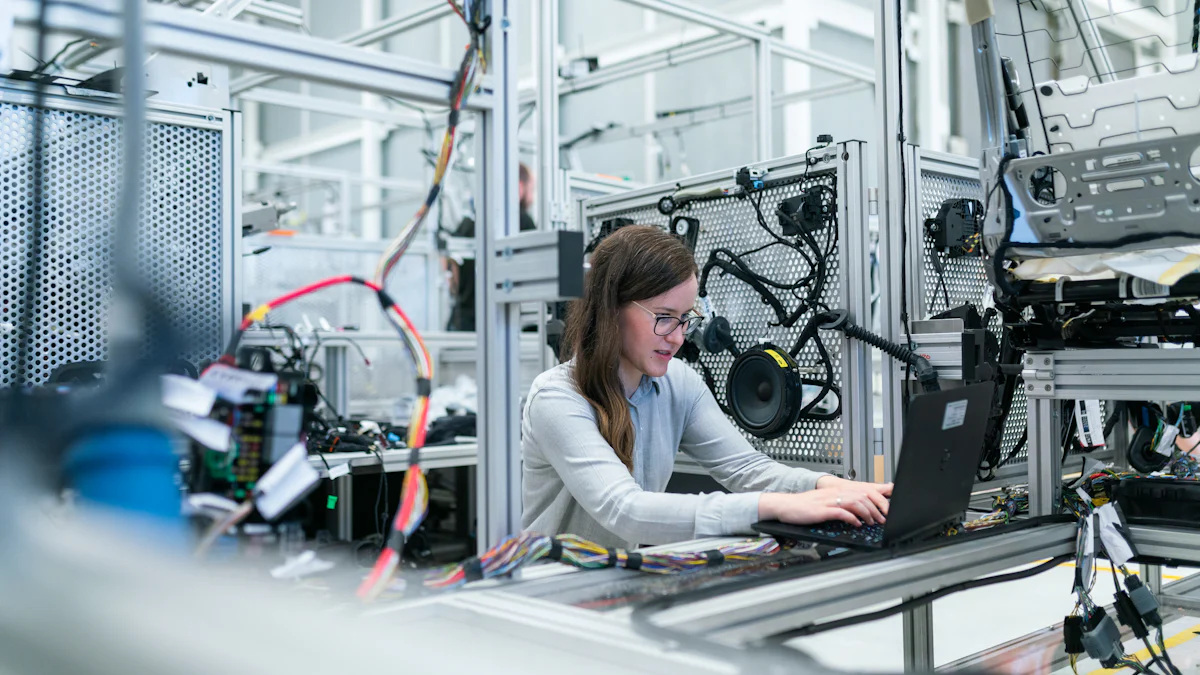
エピバレルのスセプターは半導体製造の重要なコンポーネントです。 エピタキシャルの沈着プロセスの間にウエハへの重大なサポートを提供し、安定性および精密を保障します。 これらの受容器は、多くの場合、炭化ケイ素やグラファイトなどの高純度材料から作られ、極端な温度に耐え、化学腐食に抵抗します。 自社設計は均一な温度分布を促進し、高品質のウエハを生産するために不可欠です。 汚染を防止し、熱プロファイルを維持することにより、エピバレルの受容器は、ウェーハの生産の効率性と一貫性を達成するために、ピボタル役割を果たします。 現代の半導体製造に欠かせない信頼性.
要点
- エピバレルのスセプターは、エピタキシャルの堆積プロセスの間に安定性と均一な温度を維持し、高品質のウェーハの生産を保証します.
- 炭化ケイ素のような高純度材料から作られて、これらの感受性は極端な温度と化学腐食に抵抗し、耐久性と性能を強化します.
- 円筒設計により、複数のウェーハの同時処理を可能にし、妥協のない製造効率を最適化します.
- 汚染を防止し、熱プロファイルさえ確保することにより、エピバレルの受容体は、半導体デバイスの歩留まりと信頼性を大幅に向上させます.
- 高度なスセプター技術への投資により、メンテナンスコストを削減し、半導体製造における全体的な効率性を向上させることができます.
- エピバレルスセプターの一貫した性能は、欠陥のない薄膜を達成するために不可欠であり、最終的な半導体製品の機能性に直接影響を与えます.
エピ・バレル・スセプターとは?
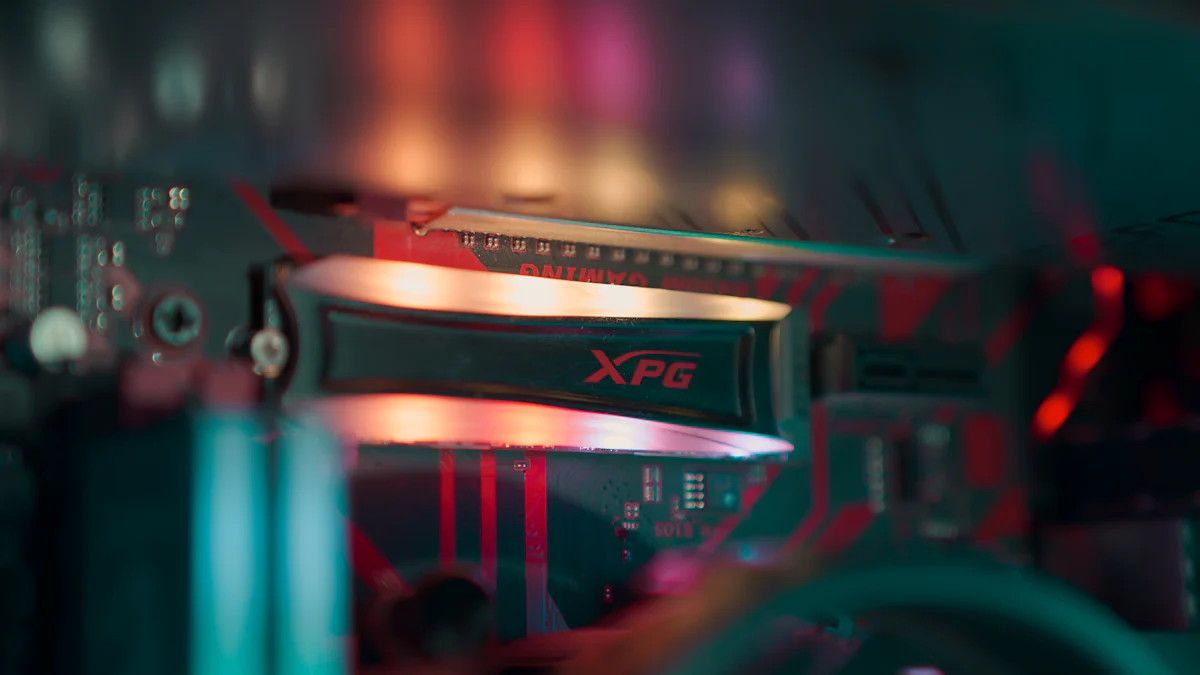
Epi Barrel Susceptorsの意味と目的
エピバレルスセプターは、半導体製造における重要なコンポーネントとして機能します。 これらの円筒形のプラットフォームは、高品質の半導体デバイスを作成するために不可欠であるエピタキシャルの堆積の間にウェーハをサポートしています。 複数のウエファーを同時に保持し、熱することによって、基質を渡る均一温度の配分を保障します。 この均一性は、最終半導体製品の性能と信頼性に直接影響を与える一貫した薄膜堆積を達成するために不可欠です。 設計は、ウェーハ処理のクリーンな環境を確保し、汚染を最小限に抑えます.
エピバレルの感受性の第一次目的はウエファーの生産の効率そして精密を高めることです。 メーカーは、高温プロセス中に安定性を維持するために、これらのコンポーネントに依存しています。 それらがなければ、エピタキシャル成長の必須レベルの精度を達成することはほぼ不可能です。 彼らの役割は、単なるサポートを超えて拡張します。彼らは積極的に半導体製造の全体的な品質と歩留まりに貢献します.
エピバレルスセプターの構造と材料
エピバレルの感受性器は通常炭化ケイ素(SiC)またはグラファイトのような高純度材料からなされます。 これらの材料は極端な温度に耐える能力のために選ばれ、化学腐食に抵抗します。 特にSiCコーティンググラファイトは、優れた熱性能と耐久性に非常に評価されています。 このコーティングは酸化に対する感受性の抵抗を高め、より長い操作寿命を保障します.
スセプターの円筒構造により、複数のウェーハを一度に保持し、製造工程のスループットを最適化することができます。 その設計は均一エピタキシャルの沈殿物のために重要である熱プロフィールを、促進します。 また、スセプターの周りのラミナガスフローパターンは不純物や汚染の危険性を減らします。 先進的な素材と思いやりのあるデザインの組み合わせにより、現代の半導体製造に欠かせないエピバレルの受容体が生まれます.
エピ・バレル・スセプターの役割
エピタキシャル蒸着プロセスでは、エピバレルのスセプターはピボタル役割を果たします。 ウェーハ用の安定したプラットフォームを提供し、正確なアライメントと一貫性のある加熱を保証します。 この安定性は、ウェーハ表面に希望する薄膜成長を達成するために不可欠です。 熱プロファイルを維持するためのスセプターの能力は、堆積プロセスがすべてのウェーハ全体で均一に行われることを保証します.
また、これらの受容体に使用される高純度材料は、堆積過程における汚染を防ぎます。 薄型フィルムの品質を損なうことができ、最終半導体デバイスにおける欠陥につながる。 このようなリスクを最小限に抑えることで、エピバレルの受容体はより高い収量とより良い製品の信頼性に貢献します。 エピタキシャルの沈着の彼らの役割は半導体の企業の重要をアンダースコアします.
エピ・バレル・スセプターはどのように機能しますか?
エピタキシャル蒸着プロセスにおける機能性
エピバレルスセプターの機能性は、その設計の心にあることを観察しました。 これらのコンポーネントは、温度が1000°C〜1200°Cの範囲であるエピタキシャル原子炉内で動作します。 スセプターの第一次役割は表軸の沈殿物プロセスの間にウエハのための安定した、均一プラットホームを提供することです。 この安定性により、薄膜がウェーハ表面全体に一貫して成長し、高品質な半導体デバイスを生産することが重要となります.
スセプターの円筒構造により、複数のウェーハを同時に保持できます。 熱プロファイルを維持しながらスループットを最適化します。 シリコンカーバイド(SiC)やSiCコートグラファイトなどの高純度材料は、熱伝導性を高め、酸化に抵抗します。 これらのプロパティは、受容体が極端な条件下で確実に実行されることを保証します。 不純物および汚染を防ぐことによって、感受性は最終的なプロダクトの収穫そして質に直接影響を及ぼすウエファーの完全性を保護します.
「バレルスセプター」 エピシステムは、業界の専門家が強調した優れた熱性能、熱プロファイル、および優れたコーティング接着を提供します。 この高度なエンジニアリングにより、スセプターが現代の半導体製造の厳しい要求を満たしていることを確認します.
ウェーハ処理における安定性と効率性の向上
安定性と効率性は、エピバレルスセプターの運用上の成功を定義します。 これらのコンポーネントは、ウェーハ処理中に精密なアライメントと一貫した加熱を維持することに優れています。 スセプターの堅牢な構造により、振動や機械的障害を最小限に抑え、蒸着プロセスを妥協する可能性があります。 この安定性は、目的の薄膜特性を達成するために不可欠です.
効率は高温および抵抗の化学腐食を扱うsusceptorの能力からの茎。 化学蒸気蒸着(CVD)プロセスを通したSiCコーティングは、感受性の耐久性および熱性能を高めます。 このコーティングはまた維持の条件を減らします、susceptorに半導体のfabsのための費用効果が大きい解決をします。 また、スセプターの周りのラミナガスの流れは、汚染のリスクを最小限に抑え、ウェーハ処理の効率性をさらに向上させます.
先端材料、精密工学および革新的な設計の組合せはエピバレルのsusceptorを半導体の製造の必要な用具にします。 厳しい条件下で一貫した結果を提供する能力は、業界でその価値を強調します.
半導体製造におけるEpi Barrel Susceptorsの使用
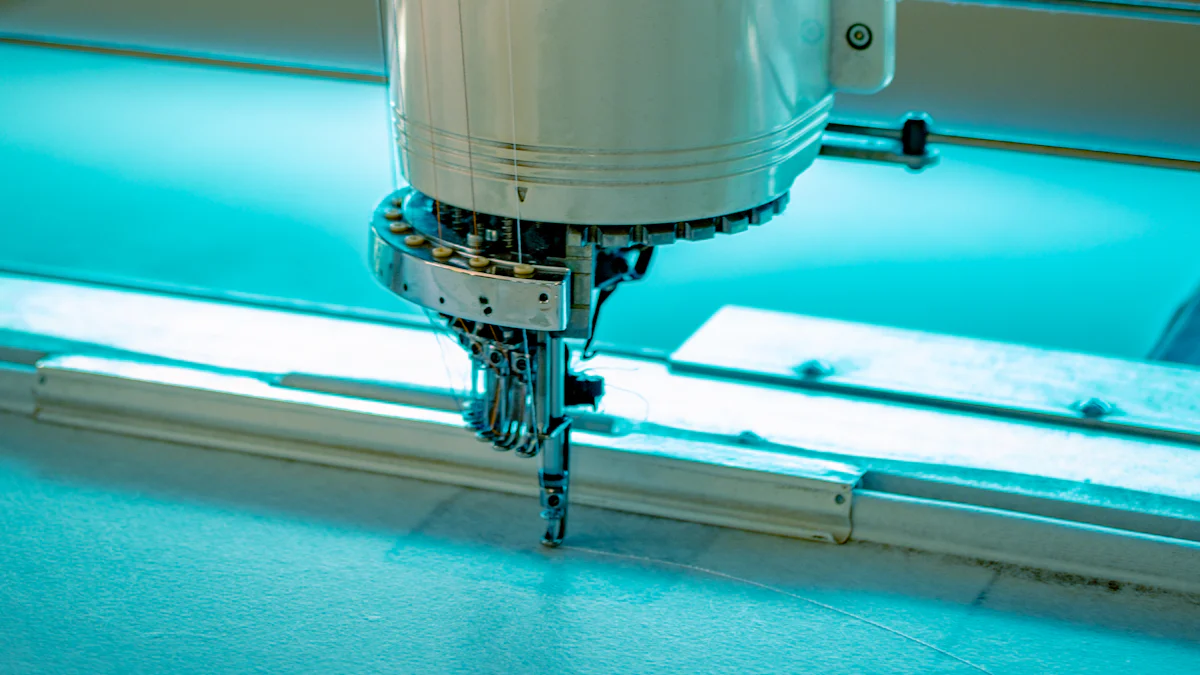
高品質のウェーハ製造用途
高品質のウエハを生産する際には、エピバレルのスセプターが重要な役割を果たしていると私は観察しました。 これらのコンポーネントは、欠陥のない半導体ウェーハを作成するために重要なエピタキシャル堆積プロセス中に均一性を保証します。 熱的プロファイルを維持することで、あらゆるウェーハ間で一貫した薄膜成長を実現します。 この一貫性は、半導体デバイスのパフォーマンスと信頼性に直接影響します.
メーカーは、ウエハ処理中に汚染を防ぐため、エピバレルの受容体に依存しています。 シリコンカーバイド(SiC)やSiCコートグラファイト、レジスト酸化、化学腐食などの高純度材料。 この抵抗はウエハの生産のためのきれいな環境を保障しま、不純物の危険を減らします。 この特徴は、最終製品の品質を大幅に高めることを発見しました.
「バレルスセプターEpiシステムは、業界の専門家が指摘したように、優れた熱性能を提供し、汚染や不純物を防止します。 高品質なウェーハ生産を実現するための不可欠なツールです.
複数のウェーハを同時に処理する能力は、製造効率を最適化します。 スセプターの円筒設計により、品質を損なうことなく最大スループットを実現できます。 精密と生産性のこの組み合わせは、半導体製造におけるエピバレルの感受性の重要性を強調しています.
製造における精密・歩留まりの向上
精密・歩留まりは、半導体製造の成功と、両分野におけるエピバレルの受容体を定義します。 これらのコンポーネントは、エピタキシャル蒸着プロセス中に精密なアライメントと安定した加熱を保証します。 安定性は機械的障害を最小限にし、そうでなければ薄膜の欠陥につながる可能性があります。 この精度は、より高い収量とより良いデバイス性能に直接貢献する方法を見てきました.
エピバレルの感受性器で使用される高度材料は耐久性および熱伝導性を高めます。 化学薬品の蒸気の沈殿(CVD)によって加えられるSiCのコーティングは、摩耗および酸化への抵抗を改善します。 この耐久性は、メンテナンスの要件を減らし、サスペンサーをメーカーの費用対効果の高いソリューションにします。 極端な条件下で一貫した性能を維持することにより、これらのコンポーネントは信頼性の高いウェーハ処理を保証します.
また、スセプター周辺のラミネアガスフロー設計により、汚染リスクを最小限に抑えます。 ウェーハを保護するだけでなく、製造プロセスの全体的な効率を高めます。 精密工学と革新的な設計のこの組み合わせは、半導体製造における高い基準の歩留まりを改善し維持するために、エピバレルの受容体を不可欠としていると考えています.
なぜエピ・バレルのスセプター マット
一貫したウェーハ品質の重要性
半導体製造の成功を一貫したウェーハ品質で定義する方法を見てきました。 エピバレルのスセプターはエピタキシャルの沈殿物の間に均一温度の配分を維持することによってこの一貫性を保障します。 半導体デバイスの性能に直接影響する薄膜の欠陥を防止します。 これらのコンポーネントがなければ、高品質のウェーハに必要な精度がほぼ不可能になります.
シリコンカーバイド(SiC)やSiCコートグラファイト、レジスト酸化、化学腐食などのエピバレル式スセプターに使用される材料。 汚染リスクを軽減し、クリーンな加工環境を確保します。 ザ・オブ・ザ・ バレルのスセプター エピシステム 優れたコーティング密着性と不純物を防止する能力でこれを実行します。 これらの特徴は、欠陥のないウエファーを生産することを目指している製造業者のための信頼できる選択をします.
私は、感受性器の円筒形設計も重要な役割を果たしていると観察しました。 複数のウェーハを越えた熱プロファイルでも、品質を損なうことなくスループットを最適化できます。 先端材料と思考工学のこの組み合わせにより、エピバレルスセプターは一貫して高品質の結果を届けることを保証します.
「バレルスセプター」 エピシステムは、優れた熱性能を提供し、汚染や不純物を防止します。 この機能は、ウェーハの品質を維持する上で、これらのコンポーネントの重要性を強調します.
半導体への影響 装置の性能および信頼性
半導体デバイスの性能と信頼性は、使用されるウェーハの品質に大きく依存します。 エピバレルサスペンサは、ウェーハ処理中に精密なアライメントと安定した加熱を保証します。 私はこの安定性が機械的障害を最小限に抑えることを発見しました。そうしないと薄膜の欠陥につながる可能性があります。 これらの欠陥は、最終的なデバイスの機能性を侵害することが多い.
について インフォメーション SiCの上塗を施してあるバレルのスセプター veTekセミコンダクターは、先進材料が製品品質と歩留まりを向上させる方法を示しています。 その優秀な熱伝導性および高温抵抗は表軸成長の間に粗い環境のためにそれを理想的にします。 これらの特性は、ウェーハが汚染から解放され、デバイス信頼性を直接改善することを確認します.
メーカーは、現代の半導体製造の厳しい要求を満たすために、エピバレルの受容器に依存しています。 極端な条件下で一貫したパフォーマンスを維持する能力は、最終的なデバイスが意図どおりに実行されることを保証します。 高品質な生産と長期デバイスの信頼性を両立させるために欠かせないものと考えております.
エピバレルのスセプターは半導体製造の必須コンポーネントとして立ちます。 これらは、高品質のウェーハを生成するために重要であるエピタキシャル蒸着中に正確なウェーハのサポートと均一な温度分布を保証します。 SiCコーティンググラファイト、レジスト酸化、コンタミネーションなどの高度な材料は、効率と信頼性の両方を強化します.
業界の専門家として「半導体製造などの高温プロセスにおいて重要な役割を果たしているバレルスセプター」.
スループットを最適化し、一貫した結果を維持することにより、これらのスセプターは、現代の半導体デバイスのパフォーマンスと信頼性に直接貢献します。 精密・効率性を実現する役割は、半導体技術の高度化における価値を捉えています.