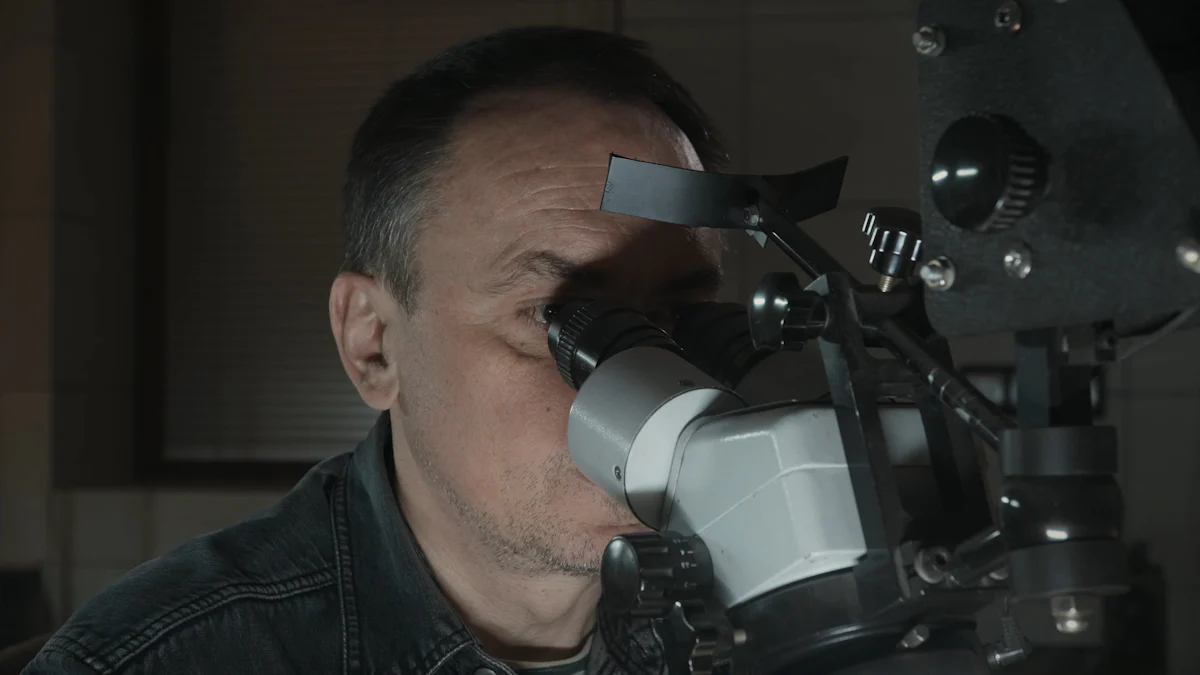
Recent breakthroughs in lpe susceptor technology have revolutionized semiconductor manufacturing. Innovations like silicon carbide (SiC)-coated susceptors and inductively heatable designs have set new benchmarks in performance. SiC-coated susceptors, known for their high thermal conductivity and resistance to thermal shock, ensure faster and more uniform heating. This advancement reduces production time while enhancing efficiency. Additionally, inductively heatable designs optimize energy usage by precisely targeting heat distribution. These developments not only improve the quality of epitaxial layers but also extend equipment lifespan, making them indispensable in modern semiconductor processes.
Key Takeaways
Recent advancements in SiC coatings and inductively heatable designs significantly enhance semiconductor manufacturing efficiency.
- SiC-coated susceptors provide high thermal conductivity and resistance to thermal shock, ensuring faster and more uniform heating during the epitaxial growth process.
- Inductively heatable designs optimize energy usage by delivering precise heat distribution, reducing production time and operational costs.
The integration of AI and IoT technologies in susceptor systems allows for real-time monitoring and predictive maintenance, improving overall production quality.
- Custom-built susceptors are becoming increasingly important, allowing manufacturers to tailor designs for specific applications like LED production and power electronics.
- Continuous innovation in susceptor technology is essential for meeting the evolving demands of the semiconductor industry and supporting the development of next-generation devices.
Overview of LPE Susceptor Technology
What is LPE Susceptor Technology?
Definition and primary applications of LPE susceptor technology, including its role in epitaxial growth.
LPE susceptor technology plays a pivotal role in the Liquid Phase Epitaxy (LPE) process, a method widely used in semiconductor manufacturing. A susceptor, typically made from materials like graphite or silicon carbide (SiC), serves as a substrate holder within an epitaxial reactor. It ensures precise temperature control during the deposition of thin crystalline layers on a substrate. These layers, known as epitaxial layers, are critical for producing high-performance semiconductor devices.
The primary applications of LPE susceptor technology include the fabrication of silicon wafers, compound semiconductors, and optoelectronic devices. By providing a stable and controlled environment, susceptors enable the uniform growth of epitaxial layers, which directly impacts the quality and performance of the final product. Recent advancements, such as SiC-coated pancake and barrel susceptors, have further enhanced the efficiency and reliability of this technology.
"The design and material composition of susceptors significantly affect the quality and purity of the epitaxial layers produced during LPE processes." This insight underscores the importance of continuous innovation in susceptor technology to meet the evolving demands of the semiconductor industry.
Importance in Semiconductor Manufacturing
Critical role of LPE susceptors in achieving high-quality epitaxial layers and supporting advanced manufacturing processes.
In semiconductor manufacturing, the quality of epitaxial layers determines the performance and reliability of electronic devices. LPE susceptors ensure consistent heat distribution and precise temperature control, both of which are essential for achieving defect-free epitaxial growth. Traditional susceptors often struggled with uneven heating, leading to variations in layer thickness and quality. However, modern designs, such as SiC-coated pancake susceptors, have addressed these challenges by enabling fast and uniform heating. This innovation reduces production time and enhances overall efficiency.
SiC-coated barrel susceptors, specifically designed for applications like LPE PE2061S 4” wafers, offer additional benefits. Their durable silicon carbide coating withstands high temperatures and thermal shocks, ensuring long-term reliability. These advancements not only improve the manufacturing process but also reduce operational costs by extending the lifespan of the equipment.
The integration of advanced LPE susceptor technology supports the production of cutting-edge semiconductor devices, including microprocessors, memory chips, and power electronics. By enabling the precise deposition of epitaxial layers, susceptors contribute to the development of smaller, faster, and more energy-efficient devices. This makes them indispensable in the pursuit of technological progress in the semiconductor industry.
Recent Patents in LPE Susceptor Technology
Breakthrough Patents in the Last 5 Years
Key patents, such as those for SiC-coated susceptors and inductively heatable designs, and their unique features.
The past five years have witnessed significant advancements in lpe susceptor technology, driven by groundbreaking patents that address critical challenges in epitaxial growth processes. Among these, patents focusing on SiC-coated susceptors and inductively heatable designs stand out for their innovative features and transformative impact.
One notable patent, filed by LPE S.p.A., introduces inductively heatable susceptors designed for epitaxial reactors. This design leverages electromagnetic induction to achieve precise and efficient heating. Unlike traditional methods, this approach minimizes energy loss and ensures uniform temperature distribution across the susceptor surface. Such precision directly enhances the quality of epitaxial layers, making it a game-changer for semiconductor manufacturing.
Another key development involves SiC-coated pancake and barrel susceptors. These designs, protected under recent patents, utilize silicon carbide coatings to improve thermal conductivity and resistance to thermal shock. The enhanced durability of these coatings allows susceptors to withstand extreme conditions during the epitaxial growth process. This innovation not only extends the lifespan of the equipment but also ensures consistent performance over time.
Patents from Applied Materials, Inc. further highlight advancements in chamber architecture and gas flow systems for epitaxial deposition. For instance, the "Method for epitaxially depositing a material on a substrate by flowing a process gas across the substrate" introduces a dual-flow system. This system optimizes the interaction between process gases and the substrate, resulting in more uniform deposition. Similarly, the "Gas injector for epitaxy and CVD chamber" patent refines gas delivery mechanisms, enhancing the efficiency of chemical vapor deposition (CVD) and epitaxial processes.
These patents collectively represent a leap forward in lpe susceptor technology, offering solutions that address both performance and efficiency challenges in semiconductor manufacturing.
How These Patents Address Industry Challenges
Solutions provided by these patents, including enhanced durability, efficiency, and adaptability to industry needs.
The patented innovations in lpe susceptor technology tackle some of the most pressing challenges faced by the semiconductor industry. These include the need for improved durability, energy efficiency, and adaptability to evolving manufacturing requirements.
SiC-coated susceptors, for example, address the issue of thermal degradation. Traditional susceptors often suffered from wear and tear due to repeated exposure to high temperatures. The silicon carbide coating, however, provides exceptional resistance to thermal shock and oxidation. This improvement significantly reduces maintenance costs and downtime, ensuring uninterrupted production cycles.
Inductively heatable designs solve the problem of uneven heating, a common issue in conventional susceptor systems. By using electromagnetic induction, these designs deliver targeted and uniform heat distribution. This precision eliminates temperature gradients that could compromise the quality of epitaxial layers. As a result, manufacturers achieve higher yields and better product consistency.
Patents like the "Chamber architecture for epitaxial deposition and advanced epitaxial film applications" introduce modular and scalable designs. These innovations allow manufacturers to adapt their equipment to different production scales and material requirements. The flexibility offered by such designs ensures that the technology remains relevant as industry demands evolve.
In addition, advancements in gas flow systems, as outlined in Applied Materials’ patents, enhance the efficiency of material deposition. By optimizing the interaction between gases and the substrate, these systems reduce waste and improve layer uniformity. This not only lowers operational costs but also aligns with the industry’s push toward sustainable manufacturing practices.
Through these innovations, recent patents in lpe susceptor technology provide robust solutions that meet the industry’s need for reliability, efficiency, and adaptability. They pave the way for the production of next-generation semiconductor devices, ensuring that manufacturers remain competitive in a rapidly advancing market.
Innovations Driving Change in LPE Susceptor Technology
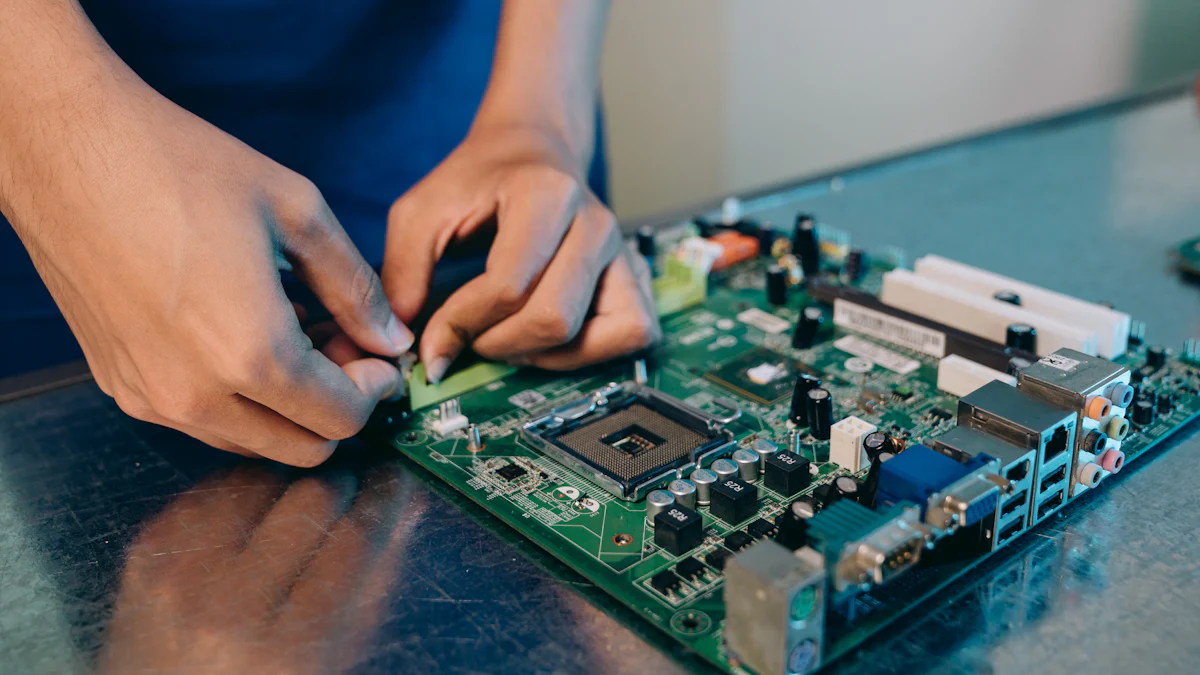
Material Advancements
Use of SiC coatings and graphite in susceptor design to improve performance and durability.
Material innovations have significantly transformed the capabilities of lpe susceptor technology. Silicon carbide (SiC) coatings, in particular, have emerged as a cornerstone in enhancing susceptor performance. SiC offers exceptional thermal conductivity, oxidation resistance, and durability, making it ideal for high-temperature applications. These properties ensure that susceptors maintain structural integrity under extreme conditions, reducing wear and extending operational lifespan.
Graphite, often used as a base material, complements SiC coatings by providing a lightweight yet robust foundation. When combined, SiC-coated graphite susceptors deliver superior heat absorption and distribution. This combination ensures uniform heating during epitaxial growth, which is critical for producing high-quality semiconductor wafers. For example, SiC-coated barrel susceptors exhibit remarkable surface smoothness and heat distribution, ensuring consistent performance even in demanding environments.
"The SiC-coated barrel susceptor for single crystal growth exhibits a very high surface smoothness," highlighting its reliability in achieving precise epitaxial layers.
These advancements not only improve production efficiency but also align with the industry’s push for sustainable and cost-effective manufacturing solutions.
Design and Manufacturing Innovations
Advances in susceptor geometry, coatings, and manufacturing techniques for better heat distribution and efficiency.
Recent innovations in susceptor design and manufacturing have addressed long-standing challenges in heat distribution and energy efficiency. Engineers have refined susceptor geometries to optimize heat flow within epitaxial reactors. Pancake susceptors, for instance, feature flat designs that enable fast and uniform heating. This reduces heating time and enhances production throughput.
Manufacturing techniques have also evolved to incorporate advanced coating processes. Chemical vapor deposition (CVD) methods ensure that SiC coatings adhere uniformly to the susceptor surface. This uniformity minimizes defects and enhances the durability of the coating. Additionally, modular manufacturing approaches allow for the customization of susceptors to meet specific application requirements, such as those in LED production or power electronics.
"SiC-coated pancake susceptors enable fast and uniform heating, reducing heating time and enhancing production efficiency," demonstrating the impact of these design improvements.
These innovations collectively enhance the reliability and adaptability of lpe susceptor technology, ensuring it meets the diverse needs of modern semiconductor manufacturing.
Integration with Emerging Technologies
Adaptation of LPE susceptors to trends like AI and IoT for smarter and more efficient manufacturing processes.
The integration of emerging technologies, such as artificial intelligence (AI) and the Internet of Things (IoT), has further elevated the potential of lpe susceptor technology. AI-driven systems analyze real-time data from epitaxial reactors, enabling precise control over temperature and gas flow. This level of automation minimizes human error and ensures consistent production quality.
IoT connectivity allows susceptors to communicate with other components in the manufacturing ecosystem. Sensors embedded in susceptors monitor critical parameters, such as temperature and pressure, and relay this data to centralized systems. This interconnected approach facilitates predictive maintenance, reducing downtime and operational costs.
"By optimizing the interaction between gases and the substrate, these systems reduce waste and improve layer uniformity," aligning with the industry’s focus on efficiency and sustainability.
The adoption of these technologies not only enhances the functionality of susceptors but also positions manufacturers to stay competitive in an increasingly digitalized industry.
Industry Impact and Future Outlook
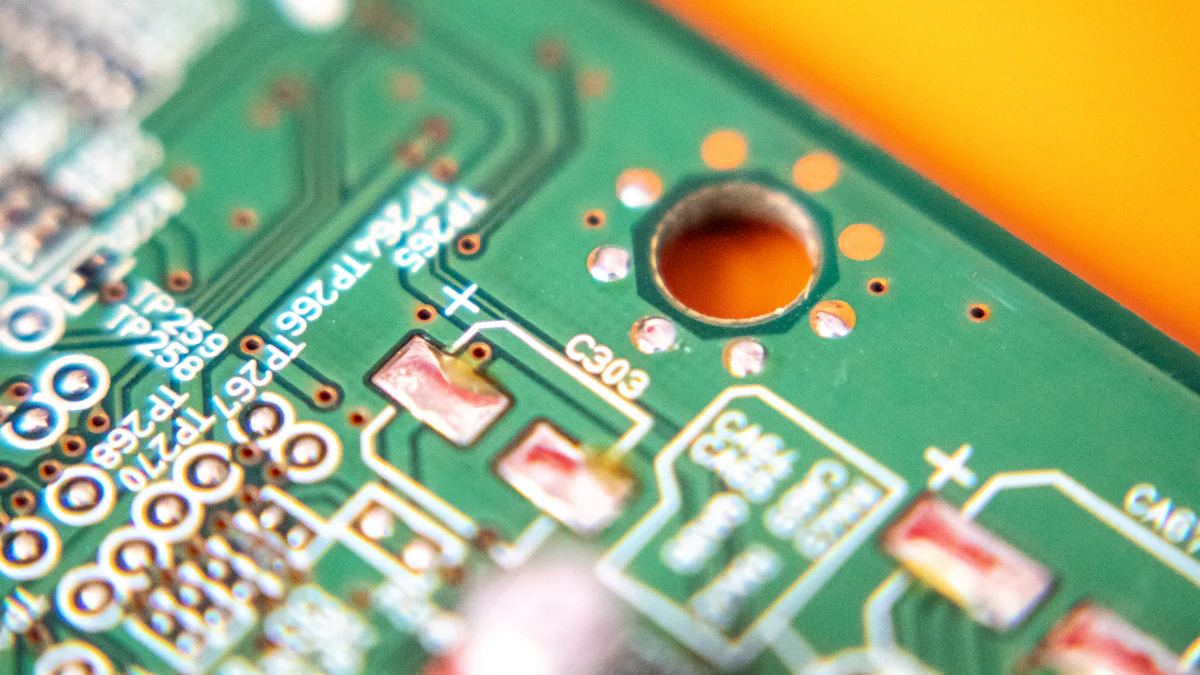
Impact on Semiconductor Manufacturing
Improvements in production efficiency, product quality, and cost-effectiveness due to recent advancements in LPE susceptor technology.
Recent advancements in lpe susceptor technology have significantly transformed semiconductor manufacturing. These innovations have improved production efficiency by enabling faster and more uniform heating during epitaxial growth. SiC-coated susceptors, for instance, ensure consistent thermal performance, reducing the time required for each production cycle. This efficiency directly translates to higher throughput, allowing manufacturers to meet growing market demands.
The quality of semiconductor devices has also seen remarkable improvements. Modern susceptors provide precise temperature control, which is critical for achieving defect-free epitaxial layers. High-quality layers enhance the performance and reliability of electronic components, including microprocessors and memory chips. By minimizing defects, manufacturers can produce devices that meet stringent industry standards.
Cost-effectiveness has emerged as another key benefit. Durable materials like silicon carbide reduce maintenance needs and extend equipment lifespan. Inductively heatable designs optimize energy usage, lowering operational costs. These advancements not only reduce expenses but also align with the industry’s push for sustainable manufacturing practices.
"Advancements in semiconductor technologies are driving the demand for high-precision epitaxy susceptors." This statement highlights the pivotal role of these innovations in shaping the future of semiconductor manufacturing.
Future Trends in LPE Susceptor Technology
Predictions for upcoming developments, such as custom-built solutions and further integration with advanced technologies.
The future of lpe susceptor technology promises exciting developments that will further enhance its capabilities. Custom-built solutions are expected to gain prominence as manufacturers seek tailored designs to meet specific application requirements. These bespoke susceptors will address unique challenges in areas like LED production and power electronics, ensuring optimal performance for specialized processes.
Integration with advanced technologies will continue to drive innovation. Artificial intelligence (AI) and the Internet of Things (IoT) are likely to play a more significant role in susceptor design and operation. AI algorithms could analyze real-time data to optimize temperature control and gas flow, ensuring consistent quality. IoT-enabled susceptors may communicate with other manufacturing equipment, creating a fully connected production ecosystem. This connectivity will facilitate predictive maintenance, reducing downtime and enhancing overall efficiency.
Emerging manufacturing techniques, such as Atomic Layer Deposition (ALD), will also influence susceptor technology. ALD’s precise control at the atomic level complements the high-precision requirements of modern susceptors. This synergy will enable the production of next-generation semiconductor devices with unparalleled performance and reliability.
"Atomic Layer Deposition (ALD) has become an indispensable part of semiconductor manufacturing due to its precise control at the atomic level." This insight underscores the importance of integrating cutting-edge methods into susceptor technology.
As the semiconductor industry evolves, the demand for innovative susceptor solutions will continue to grow. These advancements will not only meet current challenges but also pave the way for groundbreaking applications in emerging fields like quantum computing and advanced AI systems.
The advancements in lpe susceptor technology, such as SiC-coated and inductively heatable designs, have redefined the standards of semiconductor manufacturing. SiC coatings enhance durability and thermal performance, while inductive heating ensures precise energy efficiency. These innovations address critical industry challenges, including production consistency and cost-effectiveness. Staying informed about these developments is essential for manufacturers aiming to maintain a competitive edge. As the semiconductor industry evolves, continuous innovation in susceptor technology will remain pivotal in driving progress and meeting future demands.
FAQ
How do susceptor films work?
Susceptor films play a crucial role in industries like food packaging and semiconductor manufacturing. In the food industry, these films efficiently heat packaged foods in microwaves by converting microwave energy into heat. This ensures even cooking and enhances food quality. In semiconductor applications, susceptor films contribute to precise temperature control during processes like epitaxial growth, ensuring consistent results.
What are the features of SiC-coated barrel susceptors for LPE PE2061S?
The SiC-coated barrel susceptors for LPE PE2061S offer exceptional durability and performance.
What is the purpose of CVD SiC coating protectors in LPE SiC epitaxy?
CVD SiC coating protectors serve as a critical component in LPE SiC epitaxy.
Why is silicon carbide (SiC) a preferred material for susceptors?
Silicon carbide (SiC) stands out due to its exceptional thermal conductivity, oxidation resistance, and durability. These properties make it ideal for high-temperature applications like epitaxial growth. SiC-coated susceptors ensure uniform heat distribution, reduce wear, and extend equipment lifespan, which are critical factors in achieving efficient and reliable semiconductor production.
How do inductively heatable susceptors improve manufacturing efficiency?
Inductively heatable susceptors utilize electromagnetic induction to deliver precise and uniform heating. This method minimizes energy loss and eliminates temperature gradients, ensuring consistent epitaxial layer quality. By optimizing energy usage and reducing production time, these susceptors significantly enhance manufacturing efficiency.
What are the advantages of using graphite in susceptor design?
Graphite, often used as a base material for susceptors, offers lightweight yet robust properties. When combined with SiC coatings, graphite enhances heat absorption and distribution. This combination ensures uniform heating during epitaxial growth, improving the quality of semiconductor wafers and extending the operational lifespan of the equipment.
How does advanced susceptor technology support sustainable manufacturing?
Modern susceptor technology aligns with sustainable manufacturing goals by reducing energy consumption and material waste. Features like SiC coatings and inductive heating optimize energy efficiency, while durable materials minimize maintenance needs. These advancements lower operational costs and contribute to environmentally friendly production practices.
What role does AI play in enhancing susceptor performance?
Artificial intelligence (AI) enhances susceptor performance by enabling real-time monitoring and control of manufacturing processes. AI systems analyze data from sensors embedded in susceptors, optimizing parameters like temperature and gas flow. This ensures consistent production quality, reduces human error, and supports predictive maintenance for uninterrupted operations.
Can susceptors be customized for specific applications?
Yes, susceptors can be tailored to meet specific application requirements. Custom-built solutions address unique challenges in areas like LED production and power electronics. Manufacturers can optimize susceptor geometry, coatings, and materials to achieve desired performance, ensuring compatibility with specialized processes.
What future trends are expected in susceptor technology?
Future trends in susceptor technology include further integration with AI and IoT for smarter manufacturing. Advanced materials like atomic-layer-deposited coatings will enhance precision and durability. Custom-built susceptors will gain prominence, addressing the evolving needs of industries like quantum computing and advanced AI systems. These innovations will continue to drive progress in semiconductor manufacturing.