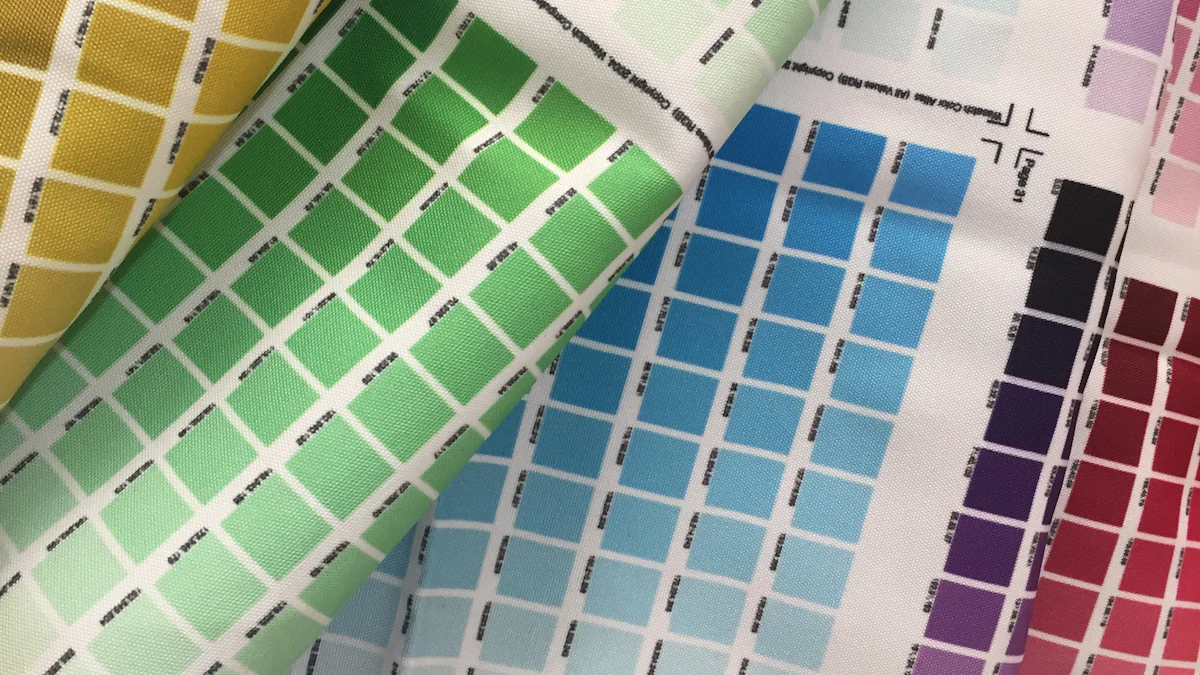
The material used in a MOCVD susceptor plays a pivotal role in determining the efficiency and quality of deposition processes. High thermal conductivity ensures uniform heat distribution, which directly impacts the precision of thin-film deposition. Chemical stability prevents unwanted reactions, maintaining the purity of the deposited layers. Mechanical strength enhances durability, reducing wear during high-temperature operations. Materials like graphite and silicon carbide excel in these areas, making them ideal choices for susceptors for MOCVD reactors. Selecting the right silicon susceptor for MOCVD applications optimizes performance and minimizes operational costs in MOCVD semiconductor manufacturing. Understanding what is MOCVD susceptor is essential for achieving the best results in these advanced processes.
Key Takeaways
- Choosing the right material for MOCVD susceptors is crucial for optimizing deposition efficiency and quality.
- Silicon carbide (SiC) is the top-performing material due to its exceptional thermal conductivity, chemical stability, and mechanical strength.
- Graphite offers cost-effectiveness and versatility but may require SiC coatings to enhance its durability and chemical resistance.
- Chemical stability of the susceptor material directly influences the purity of deposited films, preventing contamination during the process.
- Mechanical strength is essential for ensuring the susceptor can withstand extreme conditions without failure, maintaining consistent results.
- For specialized applications, quartz is valuable for its chemical purity and optical performance, despite its limitations in strength.
- Aligning material properties with specific process demands helps manufacturers balance cost, durability, and efficiency in MOCVD processes.
Overview of MOCVD Susceptors
Metal-Organic Chemical Vapor Deposition (MOCVD) susceptors serve as critical components in the deposition process. These specialized materials provide a stable platform for substrates during thin-film growth, ensuring precise temperature control and uniformity. The choice of susceptor material directly influences the efficiency and quality of the deposition process, making it a key consideration in MOCVD reactor design.
Role of MOCVD Susceptors
MOCVD susceptors play a pivotal role in facilitating the deposition of high-quality epitaxial layers. They act as the interface between the heat source and the substrate, ensuring consistent thermal distribution across the surface. This uniformity is essential for achieving precise film thickness and composition. Additionally, susceptors must withstand extreme temperatures and maintain chemical stability to prevent contamination during the deposition process.
“The performance of a susceptor determines the success of the MOCVD process by ensuring uniform heat transfer and maintaining the purity of deposited films.”
Materials like graphite, silicon carbide (SiC), and molybdenum are commonly used for MOCVD susceptors. Each material offers unique advantages. For instance, SiC-coated susceptors excel in thermal conductivity and durability, ensuring precise temperature control and high-quality film deposition. Graphite provides efficient heat transfer but often requires additional coatings to enhance its chemical resistance. Molybdenum, while suitable for high-temperature applications, has lower thermal conductivity compared to SiC and graphite.
Importance of Material Selection for MOCVD Susceptors
Selecting the right material for a MOCVD susceptor is crucial for optimizing performance and achieving desired results. The material must exhibit high thermal conductivity to ensure uniform heat distribution. It should also possess excellent chemical stability to resist reactions with precursors and byproducts. Mechanical strength is another critical factor, as susceptors must endure repeated thermal cycling without degradation.
Silicon carbide (SiC) stands out as a preferred material due to its superior thermal stability, chemical resistance, and mechanical strength. Its ability to maintain performance under extreme conditions makes it ideal for demanding applications. Graphite, while cost-effective, benefits from SiC coatings to improve its durability and chemical properties. Molybdenum, though less common, remains a viable option for specific high-temperature processes.
Key Material Properties for MOCVD Susceptors
Thermal Conductivity
Thermal conductivity plays a vital role in the performance of a MOCVD susceptor. Materials with high thermal conductivity ensure efficient heat transfer across the substrate surface. This property allows the susceptor to distribute heat evenly, maintaining consistent temperatures during thin-film deposition. Uniform heat distribution is critical for achieving precise film thickness and composition, which directly impacts the quality of the epitaxial layers.
Silicon carbide (SiC) stands out as a top-performing material due to its exceptional thermal conductivity. It ensures precise temperature control, even under extreme conditions, making it a preferred choice for advanced semiconductor manufacturing. Graphite, another commonly used material, also offers good thermal conductivity. However, its performance can be further enhanced with SiC coatings, which improve both heat transfer and durability. Molybdenum, while less common, provides excellent thermal and electrical conductivity, making it suitable for specific high-temperature applications.
“Efficient heat transfer is essential for maintaining the integrity of the deposition process and ensuring high-quality results.”
Chemical Stability
Chemical stability is another critical property for MOCVD susceptors. High-quality materials resist chemical reactions with process gases, preventing contamination and maintaining the purity of the deposited films. This resistance enhances the durability of the susceptor and reduces the risk of wear, even under prolonged exposure to extreme conditions.
SiC-coated susceptors excel in chemical stability, offering unmatched resistance to corrosive environments. This makes them ideal for demanding applications in the semiconductor and solar industries. Graphite, while cost-effective, benefits significantly from SiC coatings, which enhance its chemical resistance and extend its lifespan. Molybdenum also demonstrates good chemical stability, making it a viable option for specific processes requiring high resistance to reactive gases.
“The chemical stability of a susceptor material directly influences the purity and quality of the epitaxial layers.”
Mechanical Strength
Mechanical strength ensures that a MOCVD susceptor can withstand extreme conditions without deforming or breaking. A durable susceptor material guarantees reliable performance throughout the deposition process, even under repeated thermal cycling and intense heat. This property is crucial for maintaining the structural integrity of the susceptor and ensuring consistent results.
SiC once again emerges as a superior material due to its exceptional mechanical strength. It maintains its performance under high stress, making it suitable for demanding applications. Graphite, while less robust, can achieve improved mechanical properties with SiC coatings. Molybdenum, known for its strength, also performs well in high-temperature environments, providing a reliable option for specific needs.
“Mechanical strength is a cornerstone of susceptor performance, ensuring durability and consistency in advanced deposition processes.”
Comparison of Common Materials Used in MOCVD Susceptors
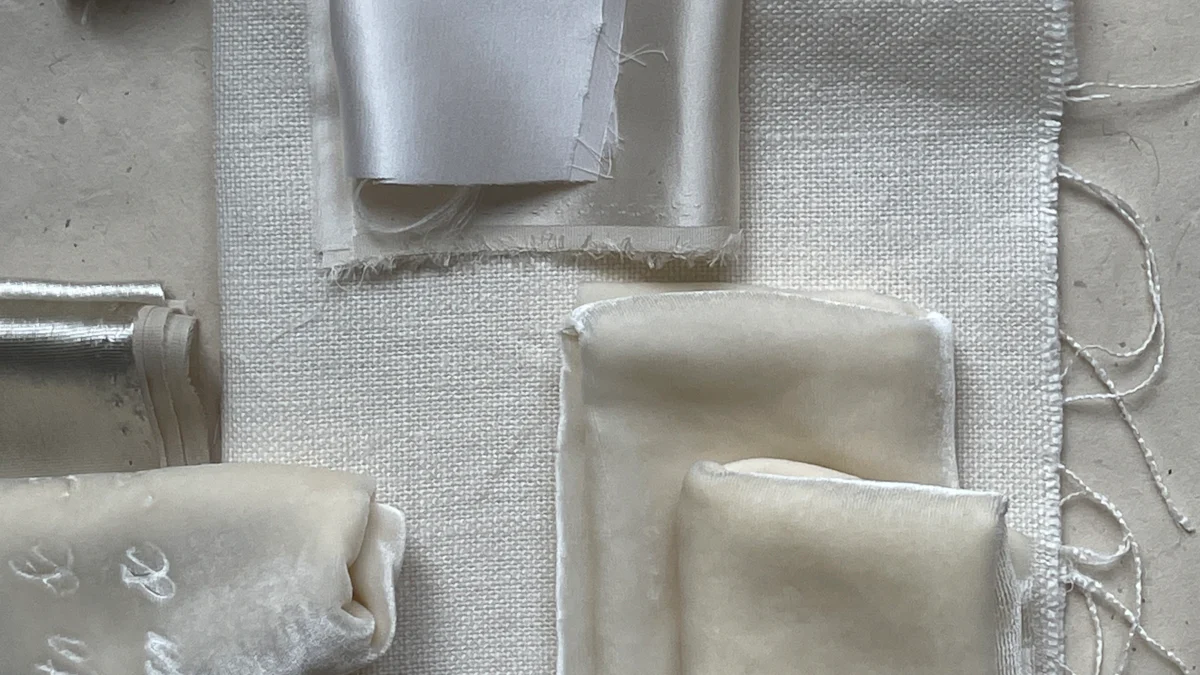
Graphite
Graphite remains a widely used material for MOCVD susceptors due to its excellent thermal conductivity and cost-effectiveness. Its ability to transfer heat efficiently ensures uniform temperature distribution, which is critical for achieving high-quality thin-film deposition. However, graphite’s chemical stability diminishes under high-temperature conditions, especially in reactive environments. This limitation often necessitates the application of coatings, such as silicon carbide (SiC), to enhance its durability and resistance to chemical reactions.
Graphite also offers mechanical flexibility, making it suitable for various applications. When combined with SiC coatings, it achieves improved hardness and wear resistance, extending its lifespan in demanding processes. This combination, known as siliconized graphite, merges the self-lubricating properties of graphite with the strength and chemical resistance of SiC, making it a versatile choice for MOCVD reactors.
“Graphite, when enhanced with SiC coatings, balances cost-efficiency with improved performance, making it a practical option for many MOCVD applications.”
Silicon Carbide (SiC)
Silicon carbide (SiC) stands out as a superior material for MOCVD susceptors due to its exceptional thermal conductivity, chemical stability, and mechanical strength. It excels in high-temperature environments, maintaining performance even under extreme conditions. SiC’s ability to resist corrosion and thermal shock makes it ideal for demanding applications in semiconductor and photovoltaic industries.
SiC-coated susceptors offer unmatched durability, ensuring consistent performance over extended periods. This material also provides high resistance to reactive gases, preventing contamination and preserving the purity of deposited films. While SiC’s cost is higher compared to traditional materials like graphite, its long-term reliability and efficiency often justify the investment.
“SiC-coated susceptors redefine performance standards in MOCVD processes, delivering precision and durability for advanced manufacturing needs.”
Quartz
Quartz serves as a specialized material for MOCVD susceptors, particularly in applications prioritizing chemical purity and optical performance. Its low thermal conductivity limits its use in high-temperature environments, but its chemical inertness makes it indispensable for processes requiring minimal contamination. Quartz’s transparency to certain wavelengths also supports optical monitoring during deposition, adding value in specific scenarios.
Despite its advantages, quartz lacks the mechanical strength of materials like SiC or graphite. This limitation restricts its use to less demanding applications where chemical purity outweighs the need for durability. Manufacturers often consider quartz for niche applications where its unique properties align with specific process requirements.
“Quartz remains essential for applications demanding chemical purity and optical precision, despite its limitations in mechanical strength.”
Application Suitability of MOCVD Susceptor Materials
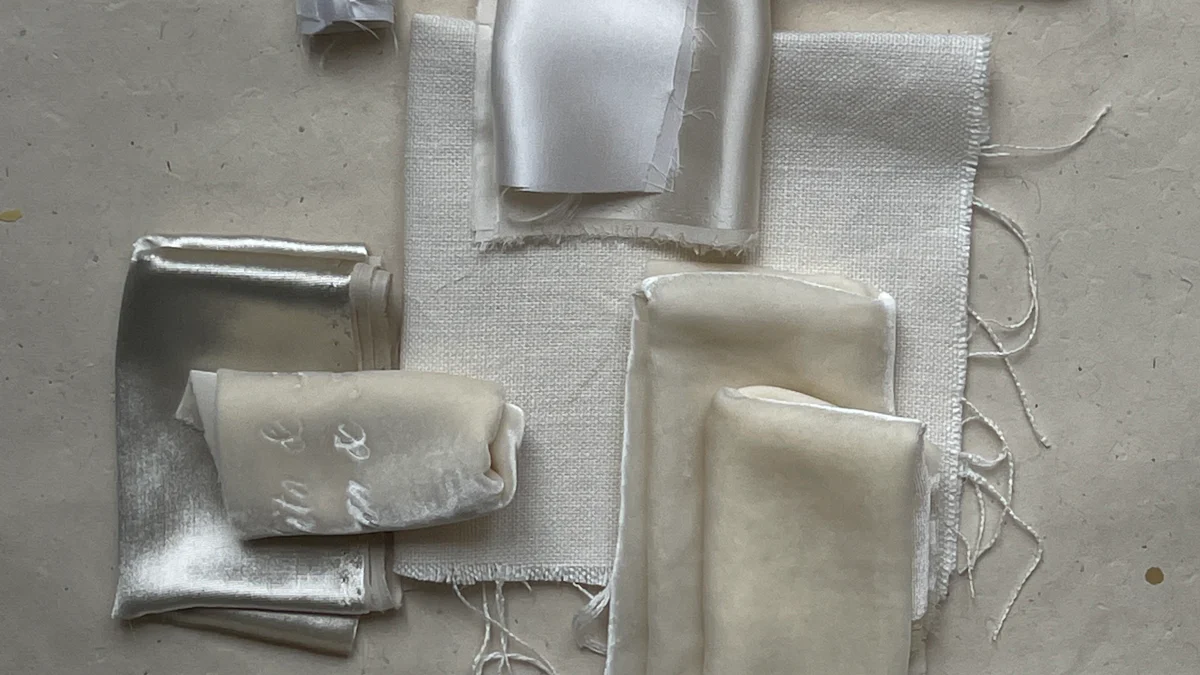
High-Temperature Applications
High-temperature applications demand materials that can endure extreme thermal conditions without compromising performance. Silicon carbide (SiC) excels in such environments due to its exceptional thermal stability and conductivity. Its ability to maintain structural integrity under intense heat ensures consistent performance, making it a preferred choice for advanced semiconductor manufacturing. SiC minimizes temperature gradients, reducing the risk of defects like uneven film thickness or crystal imperfections.
Molybdenum also proves effective in high-temperature scenarios. Its low thermal expansion and excellent thermal conductivity make it suitable for processes requiring precise temperature control. This material maintains its structural integrity even at elevated temperatures, ensuring reliable operation during prolonged use. Industries often rely on molybdenum for producing high-quality semiconductor wafers, especially in demanding applications.
“Silicon carbide (SiC) emerges as the top-performing material for MOCVD susceptors due to its superior thermal conductivity, durability, and chemical stability.”
Cost-Sensitive Applications
Cost-sensitive applications prioritize affordability without sacrificing essential performance characteristics. Graphite stands out as a practical option in these scenarios. Its cost-effectiveness, combined with good thermal conductivity, makes it a popular choice for many MOCVD processes. However, graphite’s chemical stability may diminish under high-temperature or reactive conditions. To address this, manufacturers often enhance graphite with SiC coatings, improving its durability and resistance to chemical reactions.
Siliconized graphite, which combines the self-lubricating properties of graphite with the strength of SiC, offers a balanced solution for cost-sensitive projects. This combination extends the material’s lifespan while maintaining affordability. Industries seeking to optimize costs while achieving reliable results frequently turn to graphite-based solutions.
“Graphite, when enhanced with SiC coatings, balances cost-efficiency with improved performance, making it a practical option for many MOCVD applications.”
Specialized Applications
Specialized applications require materials tailored to unique process demands. Quartz serves as an ideal choice for scenarios prioritizing chemical purity and optical precision. Its chemical inertness prevents contamination, ensuring the purity of deposited films. Additionally, quartz’s transparency to specific wavelengths supports optical monitoring during deposition, making it indispensable for niche applications.
Despite its advantages, quartz lacks the mechanical strength of SiC or graphite, limiting its use to less demanding environments. For processes requiring minimal contamination and high optical performance, quartz remains a critical material. Industries often select quartz for applications where its unique properties align with specific requirements.
Silicon carbide also plays a role in specialized applications. Its unmatched durability and chemical resistance make it suitable for processes involving corrosive environments or extreme conditions. SiC’s versatility allows it to meet the demands of both high-performance and niche applications, solidifying its position as a top-performing material.
“Quartz remains essential for applications demanding chemical purity and optical precision, despite its limitations in mechanical strength.”
Selecting the right material for a MOCVD susceptor is essential for achieving optimal performance. Graphite offers cost-effectiveness and versatility, making it suitable for budget-conscious applications. Silicon carbide (SiC) stands out as the top-performing material due to its superior thermal conductivity, chemical stability, and mechanical strength, ensuring reliability in high-temperature and demanding environments. Quartz, with its chemical purity and optical precision, caters to specialized needs. Aligning material properties with specific process demands allows manufacturers to balance cost, durability, and efficiency, ultimately enhancing the reliability and quality of MOCVD processes.
FAQ
What is the importance of material selection for an MOCVD susceptor?
Material selection plays a critical role in the success of thin-film deposition processes. High-quality materials ensure uniform heating, which enhances film consistency and minimizes defects. Chemically stable materials prevent contamination, safeguarding the integrity of the substrate. Durable options reduce wear, lower maintenance costs, and extend the lifespan of equipment. Professionals in the semiconductor industry must prioritize material selection to optimize performance and maintain a competitive edge. By choosing the right susceptor material, manufacturers can achieve superior efficiency, improve product quality, and reduce operational expenses.
Key takeaway: The right material choice directly impacts the efficiency, quality, and cost-effectiveness of MOCVD processes.
What is the role of a susceptor in the MOCVD process?
The susceptor serves as a vital component in the MOCVD process. It provides a stable platform for substrates during thin-film deposition and ensures uniform heat distribution. This uniformity is essential for achieving precise film thickness and composition. The susceptor also acts as a barrier, maintaining chemical stability and preventing contamination. By selecting the appropriate material and design, manufacturers can enhance process efficiency, improve device performance, and reduce production costs.
As the demand for high-performance electronic devices grows, the importance of high-quality susceptors continues to rise.
Why is thermal conductivity important in MOCVD susceptors?
Thermal conductivity ensures efficient heat transfer across the substrate surface. Materials with high thermal conductivity distribute heat evenly, maintaining consistent temperatures during deposition. This uniform heat distribution is crucial for achieving precise film thickness and composition, which directly impacts the quality of epitaxial layers. Silicon carbide (SiC) excels in this property, making it a preferred choice for advanced semiconductor manufacturing.
Pro tip: Consistent heat distribution reduces defects and enhances the reliability of thin-film deposition.
How does chemical stability affect MOCVD processes?
Chemical stability prevents unwanted reactions between the susceptor material and process gases. This resistance ensures the purity of deposited films and reduces the risk of contamination. Materials like SiC-coated susceptors offer unmatched chemical stability, making them ideal for demanding applications in the semiconductor and solar industries. Graphite, when enhanced with SiC coatings, also demonstrates improved chemical resistance.
Insight: Chemical stability directly influences the quality and purity of epitaxial layers, ensuring superior results.
What makes silicon carbide (SiC) a preferred material for MOCVD susceptors?
Silicon carbide (SiC) stands out due to its exceptional thermal conductivity, chemical stability, and mechanical strength. It performs reliably under extreme conditions, maintaining structural integrity and resisting corrosion. SiC-coated susceptors deliver unmatched durability, ensuring consistent performance over extended periods. While SiC may have a higher initial cost, its long-term reliability and efficiency often justify the investment.
Fact: SiC-coated susceptors redefine performance standards in MOCVD processes, offering precision and durability.
Can graphite be used effectively in MOCVD susceptors?
Graphite is widely used due to its excellent thermal conductivity and cost-effectiveness. It transfers heat efficiently, ensuring uniform temperature distribution. However, its chemical stability diminishes under high-temperature or reactive conditions. To address this, manufacturers often enhance graphite with SiC coatings, improving its durability and resistance to chemical reactions. Siliconized graphite combines the self-lubricating properties of graphite with the strength of SiC, making it a versatile choice.
Tip: Graphite, when enhanced with SiC coatings, balances cost-efficiency with improved performance.
What are the advantages of quartz in MOCVD susceptors?
Quartz offers unique advantages in applications prioritizing chemical purity and optical precision. Its chemical inertness prevents contamination, ensuring the purity of deposited films. Quartz’s transparency to specific wavelengths supports optical monitoring during deposition. However, its low thermal conductivity and limited mechanical strength restrict its use to less demanding environments.
Quartz remains essential for niche applications where chemical purity and optical performance are critical.
How do MOCVD susceptors impact production costs?
The choice of susceptor material directly affects production costs. Durable materials like SiC reduce wear and maintenance expenses, extending equipment lifespan. Cost-effective options like graphite, when enhanced with coatings, provide a balance between affordability and performance. Selecting the right material minimizes operational costs while maintaining high-quality results.
Takeaway: Investing in the right susceptor material reduces long-term costs and enhances process efficiency.
What factors should manufacturers consider when selecting a susceptor material?
Manufacturers should evaluate thermal conductivity, chemical stability, and mechanical strength. The material must ensure uniform heat distribution, resist chemical reactions, and withstand extreme conditions. Application-specific requirements, such as cost constraints or the need for chemical purity, also influence material selection. Aligning material properties with process demands ensures optimal performance.
Advice: A thorough evaluation of material properties helps manufacturers achieve the best results in MOCVD processes.
How does mechanical strength contribute to susceptor performance?
Mechanical strength ensures that the susceptor can endure extreme conditions without deforming or breaking. Durable materials maintain structural integrity during repeated thermal cycling and intense heat. This reliability guarantees consistent results and reduces the risk of equipment failure. SiC excels in mechanical strength, making it suitable for demanding applications.
Reminder: Stronger materials enhance durability and ensure consistent performance in advanced deposition processes.