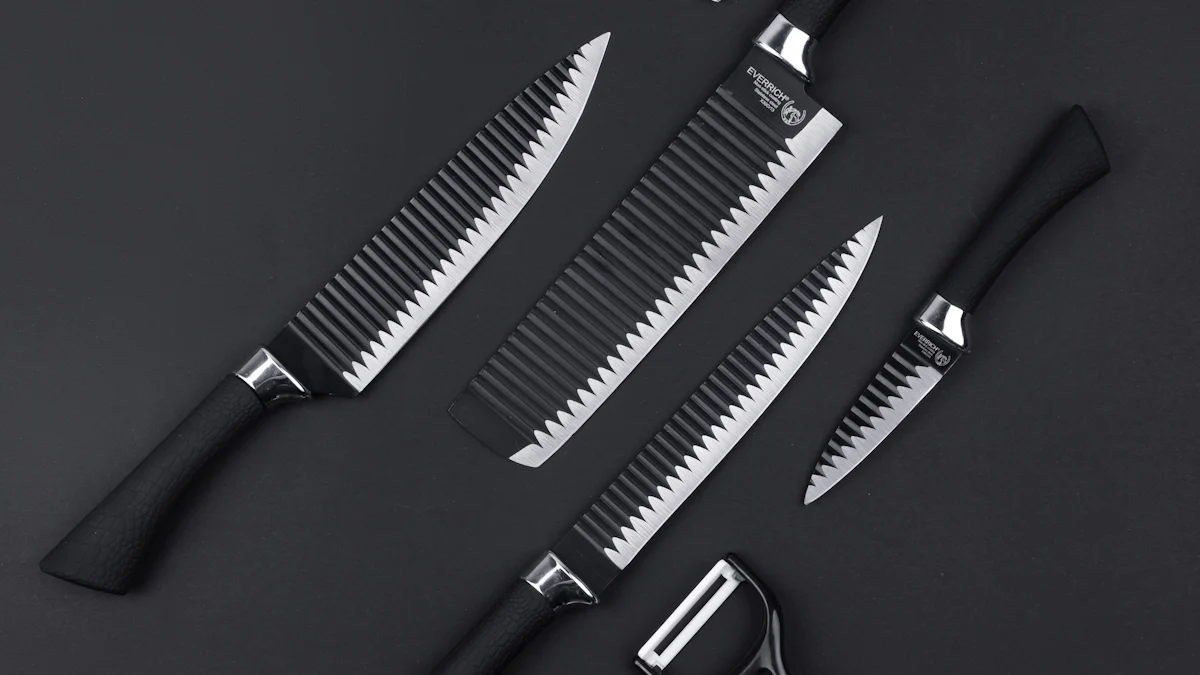
Chemical Vapor Deposition Silicon Carbide (CvD SiC) coatings represent a breakthrough in material science. These coatings deliver unmatched durability, making them ideal for demanding applications. Their exceptional heat resistance allows them to perform reliably under extreme temperatures. Additionally, their chemical stability ensures long-lasting protection against corrosive environments. Industries requiring high-performance materials, such as aerospace and electronics, benefit significantly from these advanced coatings. CvD SiC Coating technology continues to redefine standards, offering solutions that enhance efficiency and reliability across various sectors.
Key Takeaways
- CvD SiC coatings offer exceptional durability and hardness, making them ideal for high-stress applications in industries like aerospace and manufacturing.
- These coatings maintain structural integrity and protective properties even at temperatures exceeding 1,000 degrees Celsius, ensuring reliable performance in extreme heat.
- With excellent chemical stability, CvD SiC coatings protect against corrosion and chemical damage, extending the lifespan of critical components in harsh environments.
- The CvD process allows for precise control over coating properties, resulting in superior uniformity and adhesion compared to other coating technologies.
- Industries can achieve significant cost savings through reduced maintenance and replacement needs, thanks to the long-lasting performance of CvD SiC coatings.
- CvD SiC coatings enhance the efficiency of equipment by minimizing wear and energy loss, contributing to overall operational effectiveness.
- Adopting CvD SiC coatings supports innovation and progress across various sectors by providing advanced solutions that meet demanding material requirements.
What Are CvD SiC Coatings?
Defining CvD and SiC
What is Chemical Vapor Deposition (CvD)?
Chemical Vapor Deposition (CvD) is a process used to create thin films or coatings on a substrate. It involves the chemical reaction of gaseous precursors, which deposit a solid material onto the surface. This technique allows for precise control over the coating’s thickness, composition, and structure. CvD is widely recognized for producing high-quality coatings with excellent uniformity and adhesion. Industries such as aerospace, electronics, and manufacturing rely on CvD to enhance the performance of materials.
What is Silicon Carbide (SiC)?
Silicon Carbide (SiC) is a compound composed of silicon and carbon atoms. It is known for its exceptional hardness, thermal conductivity, and chemical stability. SiC exhibits remarkable resistance to wear, corrosion, and high temperatures, making it ideal for demanding applications. Its unique properties have made it a preferred material in industries requiring durability and reliability. From semiconductors to industrial tools, SiC plays a critical role in advancing technology and improving efficiency.
How CvD SiC Coatings Are Made
Overview of the CvD Process
The CvD process begins with the introduction of gaseous precursors into a reaction chamber. These gases react at high temperatures, forming a solid material that deposits onto the substrate. The process occurs in a controlled environment to ensure consistency and quality. By adjusting the reaction parameters, manufacturers can tailor the coating’s properties to meet specific requirements. This flexibility makes CvD an essential method for creating advanced coatings like CvD SiC Coating.
Key Steps in Creating CvD SiC Coatings
- Preparation of the Substrate: The substrate undergoes cleaning to remove impurities and ensure proper adhesion.
- Introduction of Precursors: Gaseous silicon and carbon compounds are introduced into the reaction chamber.
- Chemical Reaction: High temperatures facilitate the reaction, leading to the formation of silicon carbide.
- Deposition: The SiC material deposits onto the substrate, forming a dense and uniform coating.
- Cooling and Inspection: The coated substrate cools down, followed by a thorough inspection to verify quality and performance.
This meticulous process results in a coating that combines the benefits of CvD technology with the superior properties of SiC. CvD SiC Coating enhances the durability and functionality of materials, enabling them to perform reliably in extreme conditions.
Key Benefits of CvD SiC Coatings
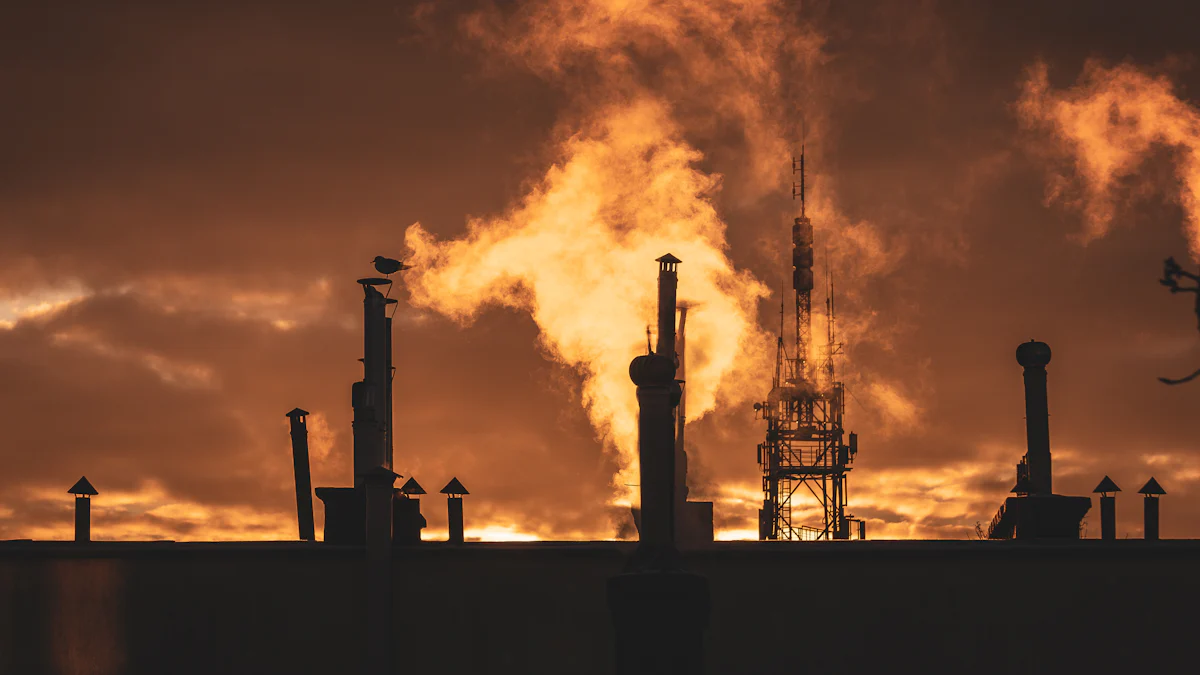
Exceptional Durability and Hardness
CvD SiC Coating offers remarkable durability, making it a preferred choice for industries that demand long-lasting materials. Its dense crystalline structure provides exceptional hardness, which resists wear and abrasion effectively. This property ensures that components coated with CvD SiC maintain their integrity even under heavy mechanical stress. Tools and equipment in manufacturing environments benefit significantly from this feature, as it reduces the frequency of replacements and maintenance. The superior hardness of CvD SiC Coating also enhances its ability to withstand impacts, ensuring reliable performance in challenging conditions.
High-Temperature Resistance
Materials coated with CvD SiC exhibit outstanding resistance to high temperatures. This capability allows them to perform reliably in environments where extreme heat would degrade other coatings. CvD SiC Coating maintains its structural stability and protective properties even when exposed to temperatures exceeding 1,000 degrees Celsius. This makes it an ideal solution for aerospace components, industrial furnaces, and semiconductor manufacturing equipment. By preventing thermal degradation, CvD SiC Coating extends the lifespan of materials and ensures consistent performance in heat-intensive applications.
Corrosion and Chemical Resistance
CvD SiC Coating provides excellent protection against corrosion and chemical damage. Its chemical stability prevents reactions with aggressive substances, including acids, alkalis, and oxidizing agents. This resistance makes it suitable for use in harsh environments, such as chemical processing plants and marine applications. The coating acts as a barrier, shielding the underlying material from corrosive elements and preserving its functionality. By reducing the risk of chemical wear, CvD SiC Coating enhances the reliability and longevity of critical components in demanding industries.
Enhanced Performance in Extreme Environments
CvD SiC Coating demonstrates exceptional performance in extreme environments where other materials often fail. Its unique properties enable it to withstand harsh conditions, ensuring reliability and efficiency in critical applications. High temperatures, corrosive chemicals, and abrasive forces challenge many materials, but CvD SiC Coating excels in these scenarios.
In high-pressure environments, the coating maintains its structural integrity. Its dense crystalline structure resists deformation and cracking, even under intense mechanical stress. This makes it a preferred choice for aerospace components and industrial machinery operating in demanding conditions.
The coating also performs exceptionally well in environments with rapid temperature fluctuations. Thermal shock often causes materials to expand and contract, leading to fractures or failures. CvD SiC Coating minimizes this risk by offering superior thermal stability. This capability ensures consistent performance in applications such as semiconductor manufacturing and high-temperature reactors.
In addition, the coating’s resistance to chemical corrosion enhances its functionality in industries like chemical processing and marine engineering. It acts as a protective barrier, preventing damage from aggressive substances and extending the lifespan of critical components. This durability reduces maintenance requirements and operational downtime, improving overall efficiency.
By delivering reliable performance in extreme conditions, CvD SiC Coating supports innovation and progress across various industries. Its ability to endure harsh environments makes it an invaluable solution for applications requiring durability and resilience.
Applications of CvD SiC Coatings
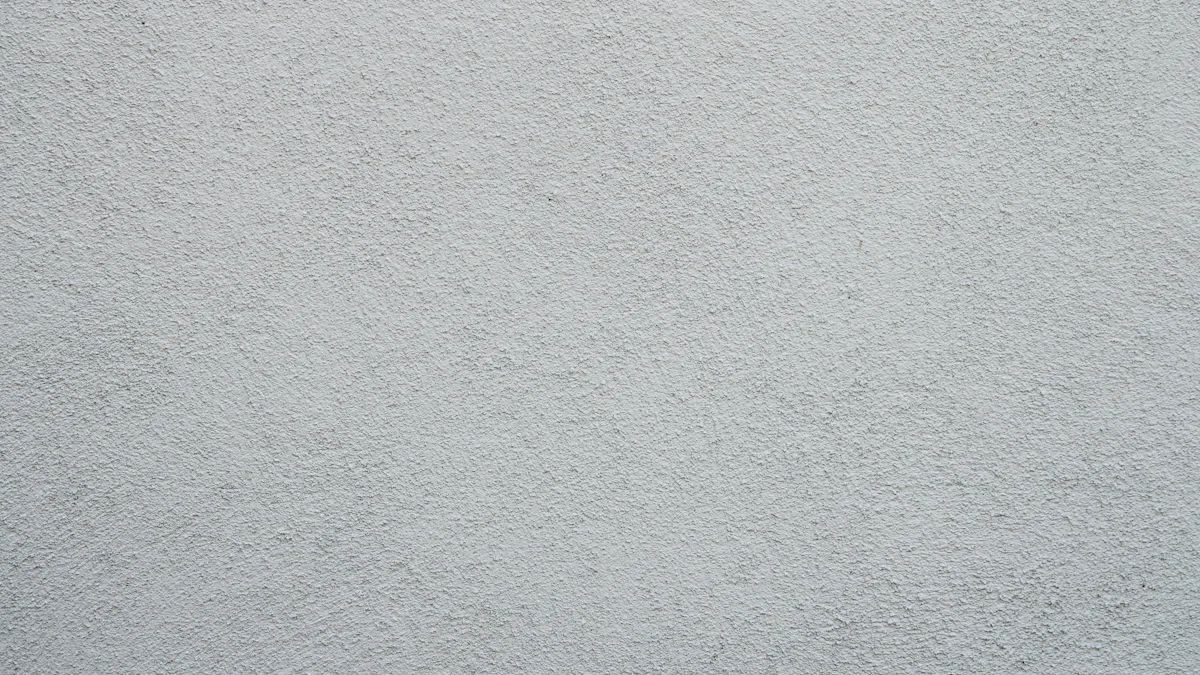
Aerospace and Defense
CvD SiC Coating plays a vital role in aerospace and defense industries. Aircraft components, such as turbine blades and engine parts, require materials that can endure extreme temperatures and mechanical stress. The coating enhances the durability of these components, ensuring reliable performance during high-speed operations. Its resistance to oxidation and corrosion protects critical parts from environmental damage, extending their lifespan.
In defense applications, the coating improves the performance of advanced weaponry and protective equipment. Radar systems and missile components benefit from its thermal stability and wear resistance. By reducing maintenance needs and increasing operational efficiency, CvD SiC Coating supports the development of cutting-edge technologies in these sectors.
Semiconductor and Electronics
The semiconductor and electronics industries rely on CvD SiC Coating for its exceptional properties. In semiconductor manufacturing, the coating ensures precision and reliability in high-temperature processes. It protects equipment like wafer carriers and etching chambers from chemical corrosion and thermal degradation. This protection enhances the quality of semiconductor devices and reduces production downtime.
Electronic components, such as power modules and circuit boards, also benefit from the coating’s thermal conductivity and electrical insulation. These properties improve heat dissipation and prevent overheating, ensuring stable performance in electronic devices. The coating’s ability to withstand harsh environments makes it indispensable in the production of advanced electronics.
Industrial and Manufacturing Equipment
Industrial and manufacturing sectors utilize CvD SiC Coating to enhance the performance of machinery and tools. The coating’s hardness and wear resistance make it ideal for cutting tools, molds, and dies. It reduces wear and tear, increasing the lifespan of equipment and minimizing replacement costs.
In manufacturing processes involving corrosive chemicals or abrasive materials, the coating acts as a protective barrier. It prevents damage to equipment surfaces, ensuring consistent operation and product quality. High-temperature applications, such as furnaces and reactors, also benefit from the coating’s thermal stability. By improving the durability and efficiency of industrial equipment, CvD SiC Coating contributes to cost savings and operational reliability.
Medical and Scientific Tools
CvD SiC Coatings have revolutionized the medical and scientific fields by enhancing the performance and durability of critical tools and equipment. Their unique properties make them indispensable in environments that demand precision, reliability, and resistance to harsh conditions.
Medical instruments benefit significantly from CvD SiC Coatings. Surgical tools coated with this material exhibit exceptional hardness and wear resistance, ensuring they maintain sharpness and functionality over extended periods. This durability reduces the frequency of replacements, which helps lower costs and ensures consistent performance during delicate procedures. Additionally, the chemical stability of CvD SiC Coatings prevents reactions with sterilization agents, maintaining the integrity of medical tools even after repeated cleaning cycles.
In scientific research, CvD SiC Coatings improve the reliability of laboratory equipment. Microscopes, spectrometers, and other precision instruments require materials that can withstand wear and exposure to corrosive substances. The coating acts as a protective barrier, shielding these devices from damage and preserving their accuracy. Researchers rely on this enhanced durability to conduct experiments without interruptions caused by equipment failure.
High-temperature applications in scientific settings also benefit from CvD SiC Coatings. Furnaces and reactors used in material testing or chemical synthesis require coatings that can endure extreme heat. CvD SiC Coatings provide thermal stability, ensuring these tools operate efficiently and safely under demanding conditions.
The biocompatibility of CvD SiC Coatings further extends their use in medical implants and devices. Pacemakers, prosthetics, and other implantable devices require materials that do not react adversely with the human body. CvD SiC Coatings offer a stable and inert surface, reducing the risk of rejection or complications. This property makes them a valuable solution for advancing medical technology and improving patient outcomes.
By enhancing the performance of medical and scientific tools, CvD SiC Coatings support innovation and progress in these critical fields. Their ability to withstand wear, corrosion, and extreme conditions ensures that professionals can rely on their equipment to deliver accurate and consistent results.
Why CvD SiC Coatings Are Superior
Comparison to Other Coating Technologies
CvD SiC Coating vs. PVD (Physical Vapor Deposition)
Chemical Vapor Deposition (CvD) and Physical Vapor Deposition (PVD) represent two distinct coating technologies. CvD SiC Coating offers superior uniformity and adhesion compared to PVD coatings. The CvD process allows for precise control over the coating’s thickness and composition, ensuring consistent quality across the entire surface. PVD, on the other hand, often struggles with achieving the same level of uniformity, especially on complex geometries.
CvD SiC Coating also excels in durability and resistance to extreme conditions. Its dense crystalline structure provides exceptional hardness and wear resistance, making it ideal for applications involving high mechanical stress. PVD coatings, while effective in some scenarios, typically lack the same level of robustness. They may degrade faster under harsh environments, such as high temperatures or exposure to corrosive chemicals.
The ability of CvD SiC Coating to withstand extreme heat further sets it apart. While PVD coatings can endure moderate temperatures, they often fail when exposed to prolonged high heat. CvD SiC Coating maintains its structural integrity and protective properties even at temperatures exceeding 1,000 degrees Celsius. This makes it a preferred choice for industries like aerospace and semiconductor manufacturing.
CvD SiC Coating vs. Traditional Coatings
Traditional coatings, such as paint or electroplated layers, cannot match the advanced properties of CvD SiC Coating. These conventional methods often provide only surface-level protection, which wears off quickly under demanding conditions. CvD SiC Coating, by contrast, forms a chemically bonded layer that integrates seamlessly with the substrate. This bond ensures long-lasting performance and resistance to wear.
Traditional coatings also fall short in terms of chemical stability. Many of them react with aggressive substances, leading to corrosion and degradation over time. CvD SiC Coating, with its exceptional chemical resistance, acts as a barrier against acids, alkalis, and other corrosive agents. This property makes it indispensable in environments where traditional coatings fail to provide adequate protection.
Furthermore, CvD SiC Coating outperforms traditional coatings in high-temperature applications. Paints and electroplated layers often lose their effectiveness when exposed to heat. CvD SiC Coating retains its protective qualities, ensuring reliable performance in extreme environments. Its ability to endure thermal stress and resist oxidation makes it a superior solution for industries requiring high-performance materials.
Cost-Effectiveness and Long-Term Performance Benefits
CvD SiC Coating delivers significant cost-effectiveness through its durability and long-term performance. Its exceptional hardness and wear resistance reduce the frequency of replacements and repairs. Industries benefit from lower maintenance costs and minimized downtime, which translates to increased operational efficiency.
The coating’s ability to withstand extreme conditions further enhances its value. Materials coated with CvD SiC maintain their functionality in harsh environments, reducing the need for frequent replacements. This longevity offsets the initial investment, making it a cost-effective solution for high-performance applications.
CvD SiC Coating also improves energy efficiency in certain applications. Its low friction coefficient reduces wear and energy loss in mechanical systems. This property enhances the performance of equipment, leading to savings in operational costs over time.
By combining durability, reliability, and efficiency, CvD SiC Coating offers unmatched long-term benefits. Industries relying on advanced materials recognize its value as a superior coating technology that supports innovation and progress.
CvD SiC Coating stands out with its unmatched properties, including exceptional durability, heat resistance, and chemical stability. These qualities have revolutionized industries by enhancing the performance and reliability of materials in extreme conditions. Its superiority over alternative coating technologies ensures long-term benefits and cost-effectiveness for various applications. Industries seeking advanced solutions can rely on this coating to meet demanding requirements. By adopting CvD SiC Coating, businesses can achieve greater efficiency, durability, and innovation in their operations.