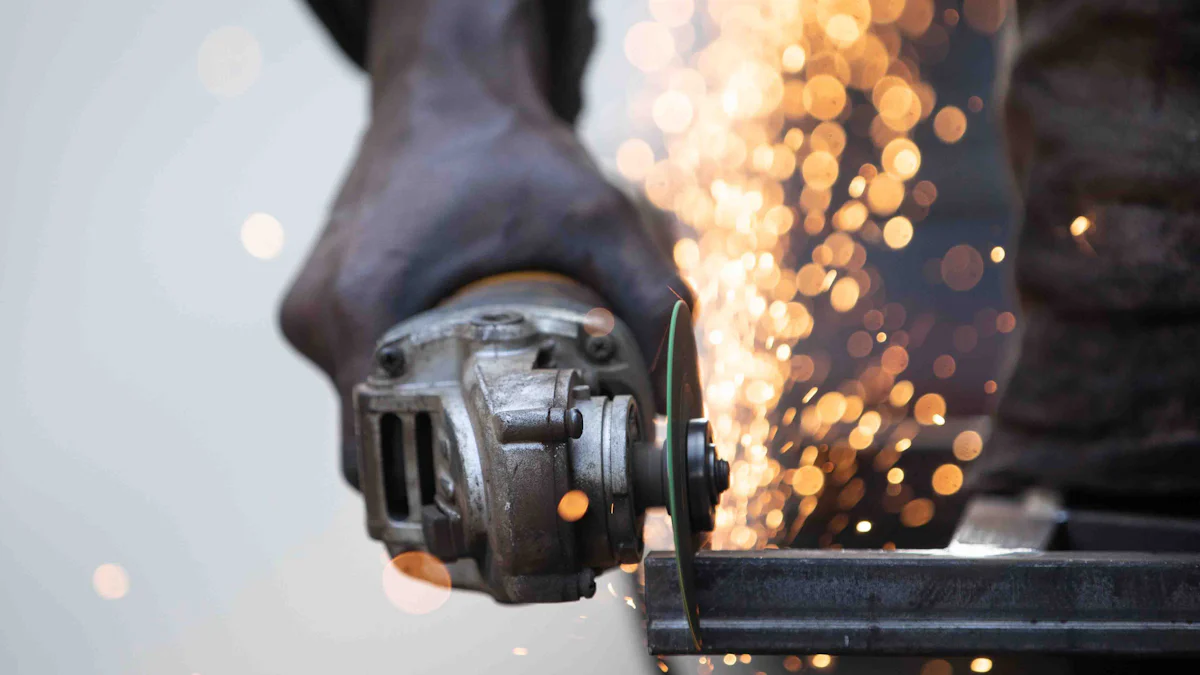
Porous graphite plays a pivotal role in modern industries, offering unmatched versatility and performance. Its unique properties, such as high porosity, thermal stability, and chemical inertness, make it indispensable for applications in sectors like photovoltaics, semiconductors, and energy storage. Selecting the right porous graphite material ensures optimal efficiency and durability. For instance, a porous graphite electrode enhances conductivity in energy systems, while a porous graphite plate or porous graphite sheet provides structural integrity in high-temperature environments. Understanding porous graphite meaning and its specific characteristics is essential to meet industrial demands effectively.
Key Takeaways
- Porous graphite is essential for various industries due to its unique properties, including high porosity, thermal stability, and chemical inertness.
- Understanding the specific porosity levels (low, medium, high) helps in selecting the right type of porous graphite for applications like filtration, thermal management, and electrical components.
- Evaluating material properties such as thermal and electrical conductivity, chemical resistance, and mechanical strength is crucial for ensuring optimal performance in demanding environments.
- Consulting with material experts can provide valuable insights and help tailor porous graphite solutions to meet specific industrial requirements.
- Conducting small-scale testing and prototyping allows manufacturers to validate the suitability of porous graphite before large-scale production, minimizing risks and ensuring performance.
- Choosing a reliable supplier with industry certifications ensures consistent quality and timely availability of porous graphite, supporting efficient production processes.
Understanding Porous Graphite
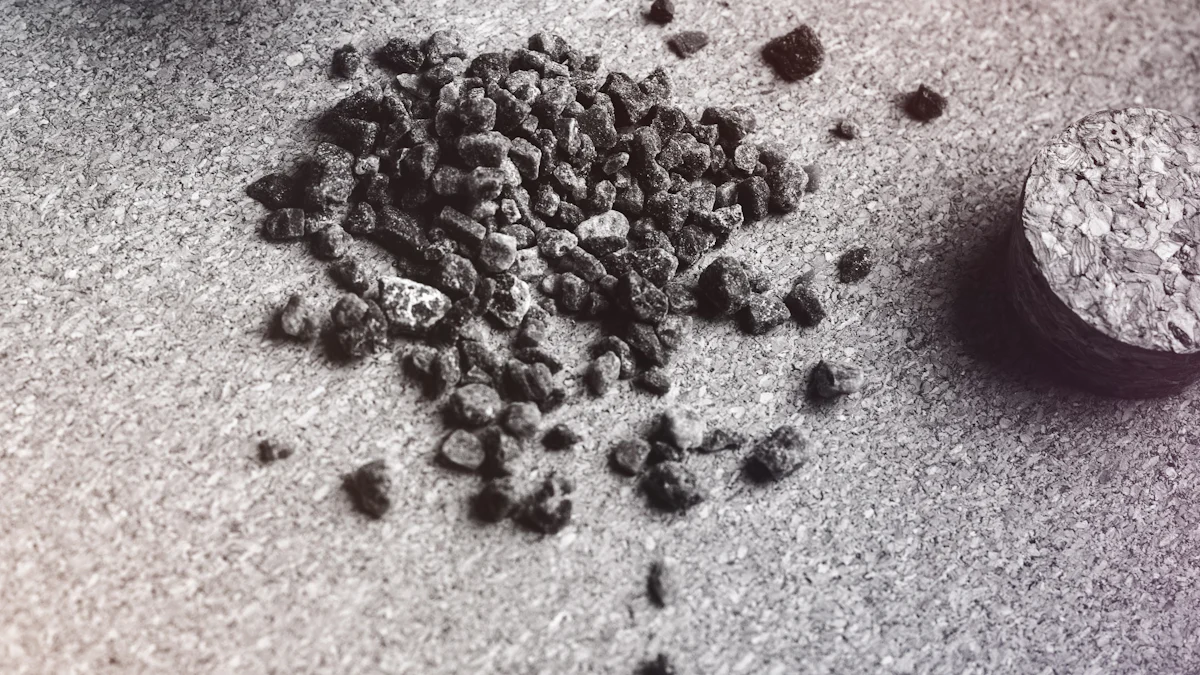
What is Porous Graphite?
Definition and Key Characteristics of Porous Graphite
Porous graphite refers to a specialized form of graphite that features an interconnected network of pores or voids within its structure. This material combines the inherent properties of graphite, such as thermal conductivity and chemical stability, with the added benefits of high porosity. The density of porous graphite typically ranges around 1.15 g/cm³, while its porosity can reach up to 47%. These characteristics make it an excellent choice for applications requiring permeability and durability.
The average pore size of porous graphite, often around 40 microns, enhances its suitability for filtration, gas diffusion, and catalysis. Additionally, its compressive strength, measured at approximately 16 MPa, ensures reliability in demanding industrial environments. These features, coupled with its low density and electrical conductivity, position porous graphite as a versatile material for various industries.
Unique Properties of Porous Graphite for Industrial Use
Porous graphite exhibits several unique properties that make it indispensable for industrial applications. Its high thermal conductivity allows efficient heat transfer, while its chemical inertness ensures stability in harsh environments. The material’s low density reduces overall weight, which is crucial for applications requiring lightweight components. Furthermore, the interconnected pore structure increases surface area, enhancing its performance in processes like filtration and catalysis.
Industries such as semiconductors and photovoltaics benefit significantly from these properties. For instance, porous graphite plays a critical role in crystal growth furnaces, improving production efficiency. Its ability to withstand extreme temperatures and maintain structural integrity further underscores its value in high-performance applications.
Importance of Porous Graphite in Industrial Applications
Versatility and Benefits Across Industries
Porous graphite demonstrates remarkable versatility, making it suitable for a wide range of industries. Its mechanical strength, combined with its unique porosity, enables it to perform effectively in diverse environments. The material finds applications in chemical processing, petrochemical operations, and energy storage systems. Its ability to handle high temperatures and resist chemical reactions ensures consistent performance across these sectors.
In addition to its functional benefits, porous graphite offers increased surface area compared to non-porous alternatives. This feature enhances its efficiency in processes like gas diffusion and catalysis. The material’s adaptability allows engineers and manufacturers to tailor it to specific industrial needs, ensuring optimal results.
Common Use Cases in Photovoltaics, Semiconductors, and More
Porous graphite has become a cornerstone in industries like photovoltaics and semiconductors. In photovoltaic systems, it serves as a reliable material for components exposed to high temperatures and corrosive environments. Its thermal stability and chemical resistance ensure long-lasting performance in these demanding conditions.
In the semiconductor industry, porous graphite is widely used in crystal growth furnaces. Its high porosity and thermal conductivity improve heat distribution, leading to enhanced production efficiency. Beyond these sectors, porous graphite also supports applications in filtration systems, where its pore structure facilitates the removal of impurities, and in energy storage devices, where it contributes to improved conductivity and durability.
Types of Porous Graphite and Their Applications
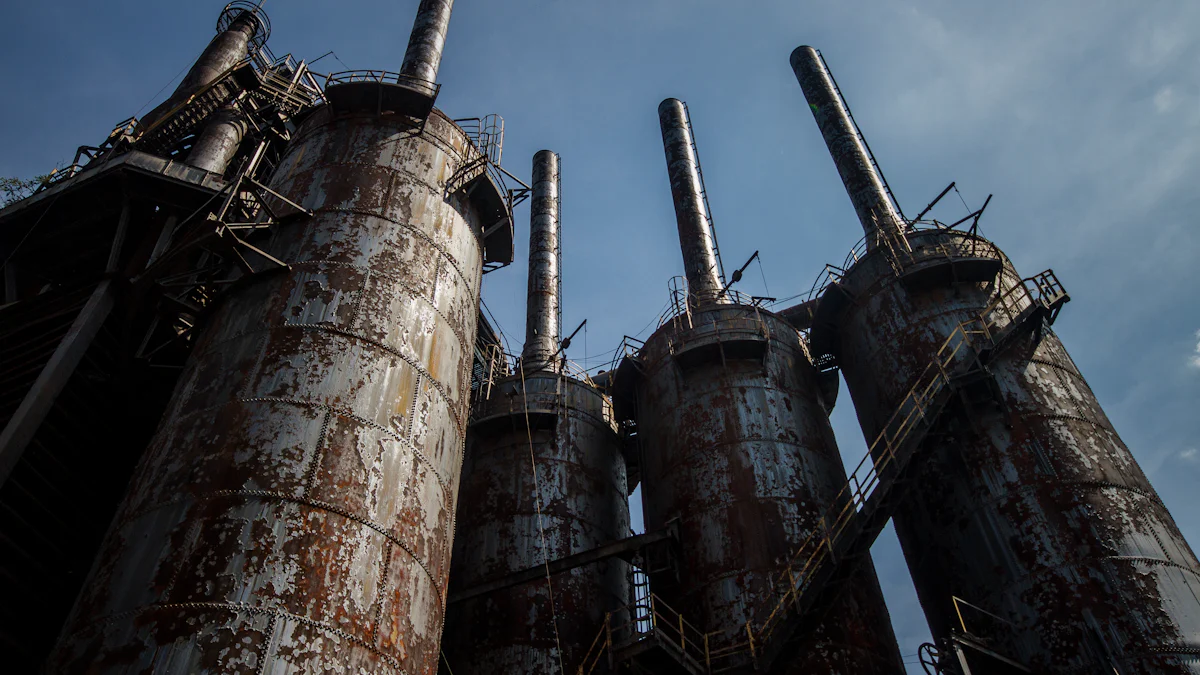
Classification of Porous Graphite
Porosity Levels: Low, Medium, and High
Porosity levels in porous graphite significantly influence its performance and suitability for various applications. Low-porosity graphite features a dense structure with minimal voids, offering high strength and excellent electrical conductivity. This type is ideal for applications requiring durability and precision, such as electrical contacts and electrodes.
Medium-porosity graphite balances strength and permeability. Its moderate porosity allows efficient thermal management, making it suitable for heat exchangers and thermal insulation systems. This type provides a reliable solution for industries that demand both structural integrity and effective heat dissipation.
High-porosity graphite exhibits an extensive network of interconnected pores. This structure enhances its surface area and permeability, making it perfect for filtration, gas diffusion, and chemical processing. The high porosity also supports catalytic reactions by facilitating the movement of gases and liquids through the material.
Manufacturing Methods: Isostatic Pressing, Extrusion, and Others
The manufacturing process of porous graphite determines its structural properties and performance. Isostatic pressing involves applying uniform pressure from all directions, resulting in a highly dense and isotropic material. This method produces graphite with consistent properties, making it suitable for demanding applications like semiconductors and photovoltaics.
Extrusion creates porous graphite with directional properties. This process involves forcing the material through a die, forming components with specific shapes and orientations. Extruded graphite is commonly used in applications requiring customized geometries, such as rods and tubes.
Other methods, such as chemical vapor deposition (CVD) and sintering, allow further customization of porous graphite. These techniques enable precise control over porosity, density, and surface characteristics, ensuring the material meets specific industrial requirements.
Applications of Different Types of Porous Graphite
High-Porosity Graphite for Filtration and Chemical Processing
High-porosity graphite excels in filtration and chemical processing due to its extensive pore network. The material’s permeability allows efficient separation of impurities in filtration systems. In chemical processing, its chemical inertness ensures stability when exposed to corrosive substances. Industries such as petrochemicals and water treatment rely on high-porosity graphite for its ability to withstand harsh environments while maintaining performance.
Medium-Porosity Graphite for Thermal Management
Medium-porosity graphite plays a critical role in thermal management applications. Its balanced porosity enables effective heat transfer while maintaining structural integrity. Heat exchangers, thermal insulation panels, and cooling systems benefit from this type of graphite. Its thermal stability ensures consistent performance in high-temperature environments, making it indispensable for industries like energy storage and electronics.
Low-Porosity Graphite for Electrical Applications
Low-porosity graphite is the preferred choice for electrical applications requiring high conductivity and mechanical strength. Its dense structure minimizes resistance, enhancing electrical performance in components like electrodes, brushes, and connectors. The material’s durability ensures long-lasting performance, even under heavy electrical loads. Industries such as power generation and electronics manufacturing utilize low-porosity graphite for its reliability and efficiency.
Key Factors to Consider When Selecting Porous Graphite
Evaluating Material Properties
Porosity and Its Impact on Performance
Porosity plays a critical role in determining the performance of porous graphite. The interconnected pore structure directly influences properties such as permeability, density, and strength. A higher porosity level increases the material’s surface area, making it ideal for applications like filtration and catalysis. However, excessive porosity can compromise structural integrity, especially under high-pressure conditions. Manufacturers carefully control porosity during production to ensure the material meets specific industrial requirements. For instance, oxygen concentration during manufacturing significantly affects porosity levels, highlighting the importance of precision in the production process.
Thermal and Electrical Conductivity
Thermal and electrical conductivity are essential properties of porous graphite, particularly for industries like semiconductors and energy storage. The material’s ability to conduct heat efficiently ensures optimal thermal management in high-temperature environments. Similarly, its electrical conductivity supports applications such as electrodes and connectors. The balance between porosity and conductivity must be carefully evaluated. While higher porosity enhances surface area, it may reduce conductivity. Engineers must select the appropriate grade of porous graphite to achieve the desired performance in their specific application.
Chemical Resistance and Durability
Chemical resistance ensures that porous graphite remains stable in harsh environments, including exposure to corrosive substances. This property is vital for industries like chemical processing and petrochemicals. The material’s durability further enhances its reliability, allowing it to withstand mechanical stress and prolonged use. Selecting porous graphite with high chemical resistance and mechanical strength ensures long-lasting performance, even in demanding conditions.
Application-Specific Considerations
Operating Environment: Temperature, Pressure, and Chemical Exposure
The operating environment significantly impacts the selection of porous graphite. High-temperature applications, such as crystal growth furnaces, require materials with excellent thermal stability. Similarly, environments with high pressure demand graphite with sufficient mechanical strength to maintain structural integrity. Chemical exposure also plays a crucial role. For instance, in chemical processing, the material must resist degradation caused by corrosive agents. Understanding these environmental factors helps manufacturers choose the most suitable porous graphite for their needs.
Mechanical Strength and Load-Bearing Requirements
Mechanical strength determines the material’s ability to withstand physical stress and load-bearing requirements. Applications involving heavy loads or dynamic forces, such as industrial machinery, demand porous graphite with high compressive strength. The material’s structural integrity ensures consistent performance and prevents failure under challenging conditions. Engineers must assess the specific load-bearing requirements of their application to select the appropriate grade of porous graphite.
Balancing Cost and Availability
Performance vs. Budget Considerations
Balancing performance and budget is a key factor when selecting porous graphite. High-performance grades often come at a premium cost due to their superior properties and precision manufacturing processes. However, investing in high-quality materials can lead to long-term savings by reducing maintenance and replacement costs. Manufacturers must evaluate their budget constraints while ensuring the selected material meets the performance requirements of their application.
Supplier Lead Times and Reliability
Supplier reliability plays a crucial role in ensuring the timely availability of porous graphite. Delays in material delivery can disrupt production schedules and increase operational costs. Choosing a supplier with a proven track record and industry certifications ensures consistent quality and dependable lead times. Collaborating with a reliable supplier helps manufacturers maintain efficiency and meet project deadlines without compromising on material quality.
Evaluating Suppliers and Ensuring Quality Assurance
Selecting a Reliable Supplier for Porous Graphite
Importance of Industry Certifications and Standards
Industry certifications and standards serve as critical benchmarks when evaluating suppliers of porous graphite. These certifications, such as ISO 9001 for quality management systems, demonstrate a supplier’s commitment to maintaining consistent production quality. Adherence to recognized standards ensures that the material meets stringent industrial requirements, including thermal stability, chemical resistance, and mechanical strength.
Suppliers with certifications often follow rigorous quality control processes. This reduces the risk of defects and ensures that the porous graphite performs reliably in demanding applications. Manufacturers should prioritize suppliers who can provide documentation of compliance with these standards. This guarantees that the material aligns with the specific needs of industries like photovoltaics, semiconductors, and energy storage.
Assessing Supplier Reputation and Track Record
A supplier’s reputation reflects their reliability and expertise in producing high-quality porous graphite. Companies with a proven track record often have long-standing relationships with clients across various industries. Positive reviews and testimonials from other manufacturers can provide valuable insights into a supplier’s performance.
Evaluating a supplier’s history of delivering consistent quality and meeting deadlines is essential. For instance, companies like Semicorex emphasize their ability to provide customized porous graphite solutions tailored to specific industrial requirements. Their focus on high-purity materials and competitive pricing highlights their dedication to customer satisfaction. Collaborating with such reputable suppliers ensures access to reliable materials and long-term partnerships.
Quality Assurance Practices for Porous Graphite
Performance Testing and Material Analysis
Comprehensive performance testing and material analysis are vital to ensuring the quality of porous graphite. These practices involve evaluating the material’s physical and chemical properties, such as porosity, density, and thermal conductivity. Advanced testing methods, including scanning electron microscopy (SEM) and X-ray diffraction (XRD), help identify potential defects or inconsistencies in the material.
Suppliers committed to quality often conduct these tests at multiple stages of production. This ensures that the final product meets the required specifications for industrial applications. For example, porous graphite used in filtration systems must undergo permeability testing to confirm its efficiency in separating impurities. Manufacturers should collaborate with suppliers who prioritize thorough testing to guarantee optimal performance.
Ensuring Consistency in Production Quality
Consistency in production quality is crucial for maintaining the reliability of porous graphite across different batches. Suppliers achieve this by implementing standardized manufacturing processes and strict quality control measures. Techniques like isostatic pressing and extrusion require precise control to produce materials with uniform properties.
Regular audits and inspections further enhance production consistency. Suppliers with robust quality assurance systems can deliver materials that meet the exacting demands of industries like semiconductors and chemical processing. Partnering with such suppliers minimizes the risk of variability, ensuring that the porous graphite performs consistently in all applications.
Practical Tips for Matching Porous Graphite to Your Needs
Conducting a Needs Assessment
Identifying Critical Performance Criteria
Selecting the right porous graphite begins with identifying the specific performance criteria required for the application. Each industrial process demands unique material properties. For instance, thermal stability is essential for high-temperature environments like crystal growth furnaces in the semiconductor industry. Similarly, chemical inertness becomes critical in chemical processing applications where exposure to corrosive substances is common. Engineers must evaluate factors such as porosity, density, and conductivity to ensure the material aligns with operational demands.
A systematic approach to defining these criteria helps narrow down the options. Start by listing the key functional requirements, such as mechanical strength, permeability, or electrical conductivity. Then, prioritize these based on the application’s primary objectives. This method ensures that the selected porous graphite meets both performance and durability expectations.
Consulting with Material Experts
Collaborating with material experts provides valuable insights into the selection process. These professionals possess in-depth knowledge of porous graphite properties and their implications for various industries. For example, experts can recommend specific grades of porous graphite tailored to applications in photovoltaics or energy storage systems. Their guidance ensures that the material’s characteristics, such as porosity levels and thermal conductivity, match the intended use.
Material experts also assist in interpreting technical specifications and performance data. They help manufacturers understand how factors like pore size distribution or compressive strength impact the material’s behavior under real-world conditions. Engaging with these specialists early in the decision-making process minimizes the risk of selecting an unsuitable material.
Testing and Prototyping Porous Graphite
Importance of Small-Scale Testing
Small-scale testing plays a crucial role in validating the suitability of porous graphite for specific applications. Before committing to large-scale production, manufacturers should test the material under controlled conditions. This approach allows them to assess its performance in scenarios that mimic actual operating environments. For instance, testing porous graphite in filtration systems can reveal its efficiency in removing impurities and maintaining flow rates.
Testing also identifies potential issues, such as structural weaknesses or inconsistencies in porosity. Addressing these problems during the prototyping phase prevents costly errors later. By conducting thorough evaluations, manufacturers gain confidence in the material’s ability to meet their requirements.
Iterative Adjustments for Optimal Performance
Prototyping involves an iterative process of refining the material to achieve optimal performance. After initial testing, engineers analyze the results and make necessary adjustments to the porous graphite’s properties. For example, increasing porosity may enhance permeability for filtration applications, while reducing it could improve mechanical strength for load-bearing components.
This iterative approach ensures that the final product aligns with the application’s demands. Manufacturers can experiment with different grades of porous graphite or modify production methods, such as isostatic pressing or extrusion, to achieve the desired outcomes. Continuous refinement during prototyping leads to a material that delivers consistent and reliable performance in industrial settings.
Understanding porous graphite and its properties is essential for achieving optimal performance in industrial applications. Selecting the right material requires careful consideration of factors such as porosity, thermal conductivity, and chemical resistance. Consulting with experts or suppliers ensures tailored solutions that align with specific operational needs. This approach minimizes risks and enhances efficiency.
“Take your time, do your research, and don’t be afraid to ask questions.” Making informed decisions about porous graphite is an investment in long-term success. Contact us today to discover the perfect solution for your industrial requirements.
FAQ
What are the key features of porous graphite?
Porous graphite offers a unique combination of properties that make it highly versatile. With a density of 1.15 g/cm³ and a porosity of 47%, it provides excellent permeability for applications like filtration, gas diffusion, and catalysis. The average pore size of 40 microns enhances its efficiency in these processes. Additionally, its compressive strength of 16 MPa ensures durability and reliability in demanding environments. High thermal conductivity and chemical stability further solidify its role in industries such as semiconductors, petrochemicals, and chemical processing.
Why is porosity important in graphite materials?
Porosity plays a critical role in determining the performance of graphite materials. Excessive porosity can lead to issues, such as components taking on the shape of carriers during heat treatment or phenolic-treated materials failing to achieve imperviousness due to larger pores. Properly controlled porosity ensures structural integrity and optimal performance. High-quality porous graphite, produced under strict supervision, minimizes these risks and guarantees reliable results in industrial applications.
What are the main applications of porous graphite?
Porous graphite serves a wide range of industries due to its unique properties. In the semiconductor sector, it is essential for crystal growth furnaces, where it enhances production efficiency. Its high permeability and chemical inertness make it ideal for filtration systems and catalytic processes. Additionally, its thermal stability supports applications in photovoltaics, energy storage, and chemical processing.
How does porous graphite benefit the semiconductor industry?
Porous graphite plays a pivotal role in the semiconductor industry, particularly in crystal growth furnaces. Its high thermal conductivity ensures efficient heat distribution, while its chemical stability withstands harsh processing conditions. These properties improve production efficiency and contribute to the creation of high-quality semiconductor components.
What factors should be considered when selecting porous graphite?
Several factors influence the selection of porous graphite. Key considerations include porosity, thermal conductivity, and chemical resistance. The operating environment, such as temperature, pressure, and exposure to corrosive substances, also impacts the choice. Manufacturers must evaluate these factors to ensure the material meets specific application requirements.
Can porous graphite be customized for specific applications?
Yes, porous graphite can be tailored to meet unique industrial needs. Manufacturing methods like isostatic pressing and extrusion allow precise control over properties such as porosity, density, and surface characteristics. This customization ensures that the material aligns with the performance demands of various applications, from filtration systems to thermal management solutions.
How does porous graphite ensure durability in harsh environments?
Porous graphite exhibits exceptional durability due to its chemical inertness and mechanical strength. It resists degradation when exposed to corrosive substances, making it suitable for chemical processing and petrochemical applications. Its compressive strength ensures reliability under high-pressure conditions, while its thermal stability supports consistent performance in extreme temperatures.
What makes porous graphite suitable for filtration applications?
The interconnected pore structure of porous graphite enhances its surface area and permeability, making it ideal for filtration. It efficiently separates impurities while maintaining flow rates, ensuring optimal performance in water treatment and chemical processing systems. Its chemical resistance further ensures stability in challenging environments.
How does thermal conductivity impact the performance of porous graphite?
Thermal conductivity is a crucial property of porous graphite, especially in high-temperature applications. It enables efficient heat transfer, which is vital for processes like crystal growth and thermal management. The balance between porosity and thermal conductivity ensures that the material performs effectively without compromising structural integrity.
Why is it important to work with reliable suppliers for porous graphite?
Partnering with reliable suppliers ensures access to high-quality porous graphite that meets industry standards. Suppliers with certifications and a proven track record provide consistent materials, reducing the risk of defects. Reliable suppliers also offer tailored solutions and dependable lead times, supporting efficient production and long-term success.