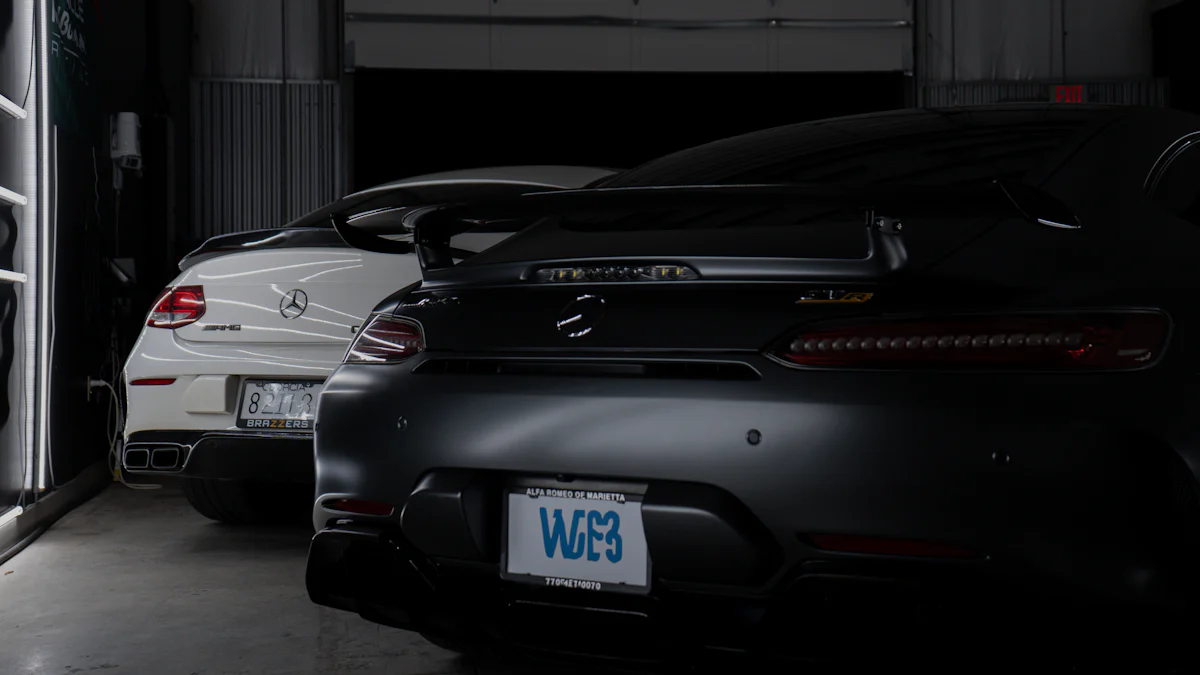
SiC ceramic coating has emerged as the leading choice for 2025, driven by its exceptional durability and ability to withstand harsh environments. Its chemical resistance and thermal stability make it a preferred option for industries like automotive and aerospace. isprojectedtogrowto17.9 billion by 2033, reflecting a compound annual growth rate of 5.6%. SiC coating stands out due to its long-lasting protection, reducing the need for frequent reapplications. Understanding what is SiC coating reveals its unique ability to deliver unmatched performance in demanding conditions.
Key Takeaways
- SiC coating is the best for 2025. It lasts 7 years.
- SiO2 coatings are cheap and easy to use. They are great for saving money while protecting surfaces.
- Graphene coatings are strong and handle heat well. But, they are hard to apply evenly and may not always work the same.
- SiC coatings resist scratches very well. They are rated 9H on the Mohs scale and work in tough conditions.
- SiO2 coatings need regular care and last 1 to 3 years. SiC coatings need less reapplication.
- SiC coatings work best when installed by experts, especially in hot places.
- Graphene coatings might improve in the future. They could help in electronics and cars because of their special features.
- Picking the right coating depends on your needs, like cost, strength, and how you’ll use it.
Understanding the Coatings
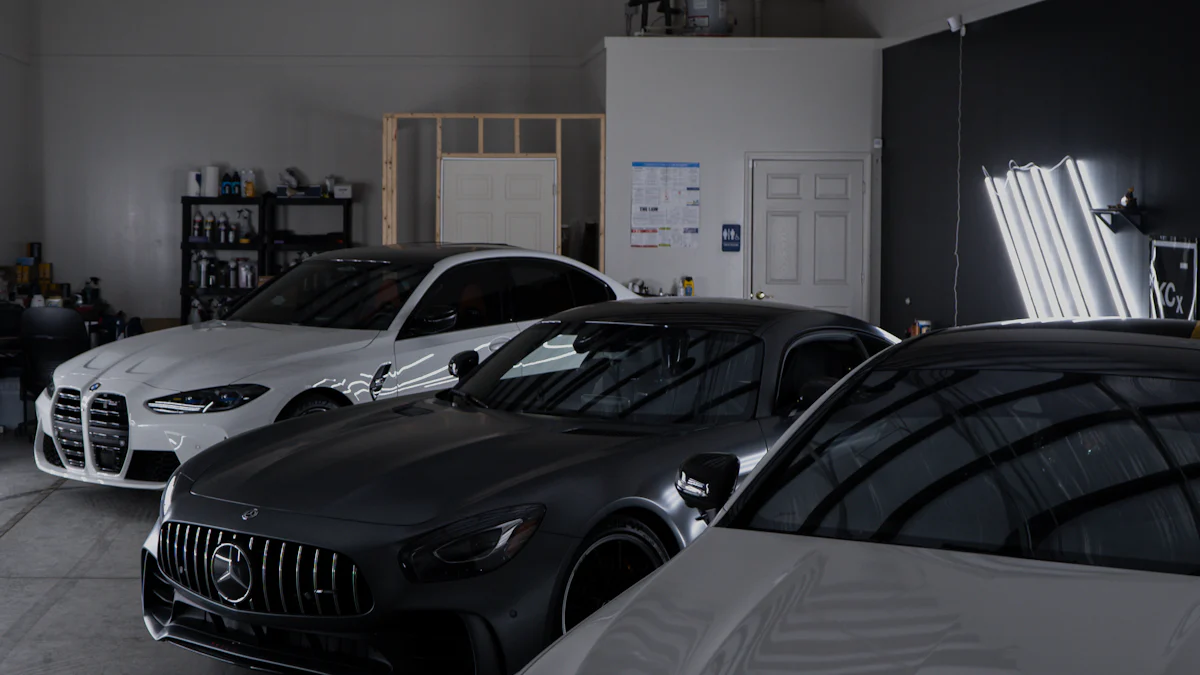
SiO2 Ceramic Coating
What is SiO2?
SiO2, or silicon dioxide, forms the foundation of traditional ceramic coatings. This compound, derived from quartz, creates a thin yet durable layer on surfaces. It is widely used in automotive and industrial applications for its protective qualities.
Key Features and Benefits
SiO2 ceramic coatings offer several advantages:
- Durability: They provide a long-lasting protective layer that resists wear and tear.
- Chemical Resistance: These coatings shield surfaces from chemical attacks, ensuring longevity.
- UV Resistance: They protect against harmful UV rays, preventing fading and degradation.
- Hydrophobic Properties: Water beads up and rolls off, making cleaning easier.
- Enhanced Appearance: SiO2 coatings add depth to colors and create a mirror-like gloss.
Drawbacks and Limitations
Despite their benefits, SiO2 coatings face challenges:
Challenge/Limitations | Description |
---|---|
High Cost of Raw Materials | Increases production expenses and affects pricing strategies. |
Complexity of Application Processes | Requires specialized equipment and skilled labor, limiting accessibility for smaller enterprises. |
Environmental Regulations | Stringent guidelines increase operational costs and affect profitability. |
Competition from Alternative Technologies | Other coating technologies may offer similar benefits at lower costs, attracting potential customers. |
Lack of Awareness in Emerging Markets | Hinders adoption rates and slows market penetration. |
SiC Ceramic Coating
What is SiC?
SiC, or silicon carbide, is a high-performance ceramic coating known for its exceptional hardness and thermal stability. It is often used in demanding environments such as aerospace, automotive, and electronics industries.
Unique Properties and Advantages
SiC ceramic coating stands out due to its unique properties:
- High Thermal Conductivity: Ensures efficient heat dissipation, making it ideal for high-temperature applications.
- Exceptional Hardness: Provides a robust surface that resists scratches and wear, extending the lifespan of equipment.
- Corrosion Resistance: Protects against corrosive elements, maintaining surface integrity.
- Oxidation Resistance: Prevents degradation in oxidative environments.
This coating also excels in durability and chemical resistance. Its inert nature creates a strong barrier against corrosive agents, making it suitable for harsh industrial conditions.
Challenges and Niche Appeal
SiC ceramic coating faces certain challenges:
Challenges | Niche Applications |
---|---|
High production costs | Aerospace (turbine blades) |
Need for specialized equipment | Automotive (engine parts, brake discs) |
Competition from alternative coatings | Semiconductor (wafer processing) |
Complexity of application processes | Electronics (harsh environments) |
Environmental regulations |
Despite these challenges, its niche applications in aerospace and automotive industries highlight its value in extreme conditions.
Graphene Ceramic Coating
What is Graphene Coating?
Graphene ceramic coatings represent the latest innovation in surface protection. Combining graphene’s strength with ceramic durability, these coatings offer a thinner yet stronger protective layer.
Cutting-Edge Features
Graphene coatings bring several advancements:
- Graphene-Ceramic Fusion: Combines graphene’s strength with ceramic’s durability.
- Hydrophobic Barrier: Repels contaminants, UV rays, and water spots.
- High Gloss Finish: Enhances surface appearance with a deep, glossy shine.
- Ease of Application: Features a simple spray-on and wipe-off process.
- Versatility: Suitable for paint, glass, and plastics.
- Long-Lasting Effects: Provides months of protection.
Current Limitations and Research Gaps
Graphene coatings remain in the early stages of development. Challenges include:
- Achieving uniform dispersion and bonding within the coating matrix.
- Developing water-borne formulations without harmful VOCs.
- Creating transparent layers without solvent-borne binders.
These limitations indicate ongoing research to unlock graphene’s full potential in practical applications.
Head-to-Head Comparison
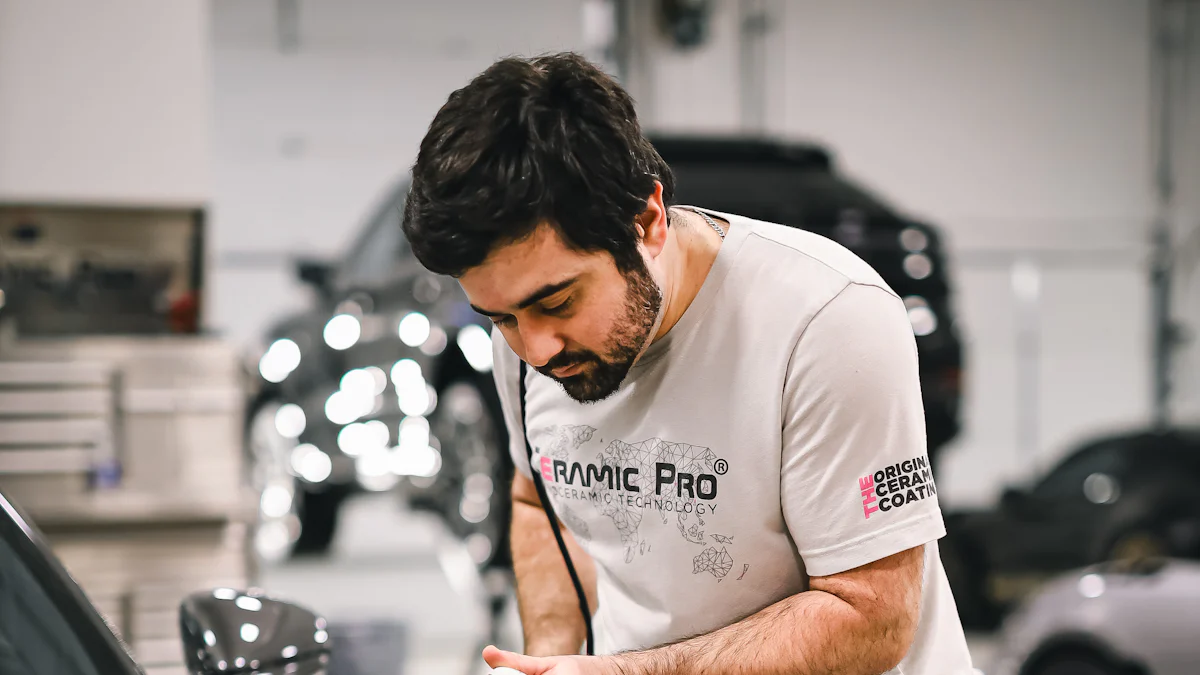
Durability
Longevity of SiO2
SiO2 ceramic coatings typically last between 1 to 3 years with proper care. Their durability depends on factors such as environmental exposure and maintenance routines. While they provide reliable protection against UV rays and minor abrasions, they require periodic reapplication to maintain their effectiveness.
Longevity of SiC
SiC ceramic coatings outperform SiO2 in terms of longevity, lasting up to 7 years or more with proper maintenance. This extended lifespan results from their exceptional hardness, corrosion resistance, and thermal stability. These properties reduce wear and tear, ensuring long-term protection.
Silicon carbide ceramic coating excels in high-temperature environments due to its outstanding thermal conductivity and stability, preventing localized overheating and ensuring consistent performance.
Property | Description |
---|---|
Increased Hardness | Fortifies surfaces, making them resistant to wear and tear. |
Corrosion Resistance | Shields equipment from corrosive elements, ensuring durability. |
Thermal Stability | Maintains integrity under high temperatures, crucial for demanding environments. |
Longevity of Graphene
Graphene coatings are marketed as highly durable, with claims of lasting 5 to 10 years. However, practical challenges such as achieving uniform dispersion and adhesion often hinder their real-world performance. These issues can lead to a shorter lifespan compared to SiC coatings.
Ease of Application and Maintenance
Application Process for SiO2
SiO2 coatings are relatively straightforward to apply. They can be polished and reapplied without affecting the clear coat thickness, making them ideal for users who may inadvertently damage the surface. Regular maintenance involves cleaning and occasional reapplication to preserve their hydrophobic and glossy properties.
Application Process for SiC
Applying SiC ceramic coating requires precision and expertise. Unlike SiO2, it does not add thickness to the clear coat. Polishing SiC coatings may result in a loss of the clear coat, which makes careful application crucial. Despite these challenges, their durability reduces the need for frequent maintenance, offering long-term benefits.
Application Process for Graphene
Graphene coatings promise a simple spray-on and wipe-off process. However, their performance often falls short due to low active ingredient content. This limitation affects both their lifespan and reliability, making them less practical compared to SiO2 and SiC coatings.
Cost-Effectiveness
Cost of SiO2 and Value for Money
SiO2 coatings are available in a wide price range, starting at 50forDIYoptionsandexceeding50 for DIY options and exceeding 50forDIYoptionsandexceeding100 for professional-grade products. Their ability to add a thicker protective layer and withstand polishing enhances their value for users seeking durability and ease of maintenance.
Cost of SiC and Value for Money
SiC ceramic coatings are less common and have varying costs. They provide a mirror-like finish and achieve a hardness of 9H, enhancing the resilience of the existing clear coat. These features make them a worthwhile investment for users prioritizing durability and aesthetics.
Cost of Graphene and Value for Money
Graphene coatings are priced between 70and70 and 70and100 for a 30ml bottle, making them more expensive than many SiO2 options. Despite their self-healing properties, their low active ingredient content limits their effectiveness, reducing their overall value for money.
Performance Metrics
Scratch Resistance Comparison
Scratch resistance is a critical factor when evaluating ceramic coatings. SiO2 coatings provide moderate protection against minor abrasions, making them suitable for everyday use. However, their softer composition limits their ability to withstand deeper scratches.
SiC ceramic coating excels in scratch resistance due to its exceptional hardness, rated at 9H on the Mohs scale. This hardness creates a robust barrier that protects surfaces from significant wear and tear. It is particularly effective in environments where surfaces are exposed to frequent physical contact or abrasive materials.
Graphene coatings also offer impressive scratch resistance. Their unique structure, derived from graphene’s atomic lattice, provides a durable shield. However, their performance can vary depending on the formulation and application process. While they rival SiC coatings in theory, practical limitations often reduce their effectiveness.
Heat Dissipation Capabilities
Heat dissipation plays a vital role in maintaining the integrity of coated surfaces, especially in high-temperature environments. SiC coatings demonstrate moderate heat management capabilities. While their primary focus lies in protection against environmental factors, their thermal stability ensures consistent performance under heat stress.
Graphene coatings stand out in this category. Their superior thermal conductivity allows for efficient heat dissipation, making them ideal for applications where temperature regulation is crucial. This property enhances their appeal in industries like automotive and electronics, where overheating can compromise performance.
SiO2 coatings, on the other hand, prioritize UV resistance and chemical protection over heat dissipation. While they provide reliable surface protection, their thermal conductivity remains limited compared to SiC and graphene coatings.
- SiC coatings provide a mirror finish and achieve a hardness of 9H, enhancing the resilience of the existing clear coat.
- Graphene coatings excel in thermal conductivity, offering enhanced heat dissipation.
- Ceramic coatings, including SiC, focus more on environmental protection than heat management.
Aesthetic Enhancements
Ceramic coatings significantly enhance the visual appeal of surfaces. SiO2 coatings create a glossy finish that adds depth to colors, making vehicles appear more vibrant. Once cured, they maintain a rich luster over time, eliminating the need for frequent waxing.
SiC ceramic coating takes aesthetics to the next level. Its mirror-like finish transforms the surface, providing a sleek and polished appearance. This enhancement not only improves the vehicle’s look but also elevates its overall value.
Graphene coatings also deliver remarkable aesthetic benefits. Their ability to create a deep, glossy shine rivals traditional ceramic coatings. However, their thinner application layer may result in a less pronounced effect compared to SiC coatings.
- Ceramic coatings enhance the overall appearance of vehicles, providing a depth of gloss and shine that exceeds traditional waxing methods.
- Once cured, they offer long-lasting protection and a vibrant finish, reducing the need for frequent maintenance.
- Applying a ceramic coating transforms the car’s surface, making it visually striking on the road.
Expert Recommendation
Best Choice for General Users
For general users, SiC ceramic coating emerges as the most practical option in 2025. Its ability to deliver a mirror-like finish significantly enhances the appearance of vehicles by creating a reflective surface. This aesthetic improvement appeals to users who value a polished and professional look for their vehicles. The coating’s 9H hardness ensures exceptional durability, making it resilient against environmental factors such as UV rays, dirt, and minor abrasions.
General users benefit from the coating’s long-lasting protection, which reduces the need for frequent reapplications. While polishing can restore its finish if damaged, users must exercise caution as this process may thin the clear coat. SiC ceramic coating suits individuals who maintain their vehicles meticulously, ensuring the coating retains its protective and aesthetic qualities over time.
Best Choice for Car Enthusiasts
Car enthusiasts often seek coatings that combine performance, aesthetics, and durability. SiC ceramic coating meets these demands with its advanced features. The table below highlights its specific benefits:
Benefit | Description |
---|---|
Durability | Lasts up to 7 years or more with proper maintenance, ensuring long-lasting protection. |
Gloss and Hydrophobicity | Provides a deep, rich gloss and superior hydrophobic properties, enhancing appearance and cleanliness. |
Temperature Resistance | Superior resistance to high temperatures, ideal for vehicles in extreme conditions. |
These features make SiC ceramic coating a top choice for enthusiasts who prioritize both functionality and style. Its hydrophobic properties simplify cleaning by repelling water and contaminants, keeping vehicles spotless with minimal effort. Additionally, its resistance to high temperatures ensures reliable performance in extreme environments, such as during high-speed driving or exposure to intense sunlight. Enthusiasts can rely on this coating to preserve their vehicle’s pristine condition while showcasing a stunning, glossy finish.
Best Choice for Budget-Conscious Buyers
Budget-conscious buyers often prioritize affordability without compromising quality. For this group, SiO2 ceramic coatings offer the best balance between cost and performance. These coatings are widely available at various price points, starting as low as $50 for DIY kits. They provide reliable protection against UV rays, minor scratches, and chemical exposure, making them a cost-effective solution for everyday use.
While SiC ceramic coating offers superior durability and aesthetics, its higher cost may deter budget-conscious buyers. Graphene coatings, though innovative, often fall short in terms of value due to their limited active ingredient content and inconsistent performance. SiO2 coatings, on the other hand, deliver dependable results at a fraction of the cost, making them an accessible option for those seeking basic surface protection.
Future Potential of Graphene Coatings
Graphene ceramic coatings hold immense potential for innovation and market adoption. Their unique properties position them as a transformative solution across various industries. As research progresses, these coatings are expected to redefine surface protection and functionality.
Graphene’s exceptional strength, approximately 200 times stronger than steel, makes it a standout material. Despite its strength, it remains lightweight, which is crucial for applications requiring minimal added weight. Its superb electrical conductivity enhances the performance of electronic components, while its excellent thermal conductivity ensures efficient heat dissipation. These features make graphene coatings particularly appealing for industries like electronics and automotive.
The table below highlights the key properties that contribute to graphene’s future potential:
Property | Description |
---|---|
Exceptional Strength | Graphene is approximately 200 times stronger than steel, yet lightweight. |
Superb Electrical Conductivity | Enhances electrical properties of substrates, crucial for electronics. |
Excellent Thermal Conductivity | Highly efficient at dissipating heat. |
Impermeability | Ideal for creating barriers against gases and liquids. |
Transparency | Remarkable feature when used as a coating. |
Durability | Highly resistant to scratches and wear. |
Flexibility | Easier to apply and bonds well with various surfaces. |
Lightweight | Adds minimal weight while providing significant strength. |
Mechanical Strength | Enhances toughness and resistance to physical damage. |
The global graphene coating market was valued at USD 183.86 million in 2023. Analysts project a compound annual growth rate (CAGR) of 29.3% over the next decade. This rapid growth reflects the increasing demand for graphene coatings in sectors like healthcare, automotive, and aerospace. In healthcare, graphene’s impermeability and biocompatibility drive its use in medical devices and drug delivery systems. Its ability to create barriers against gases and liquids also makes it ideal for protective coatings in harsh environments.
Graphene coatings’ flexibility and lightweight nature further enhance their appeal. These characteristics simplify application processes and improve adhesion to various surfaces. As a result, industries can adopt graphene coatings without significant changes to existing workflows. Additionally, their transparency allows for innovative uses, such as protective layers on optical devices or displays.
Despite these advantages, graphene coatings face challenges. Achieving uniform dispersion and bonding within the coating matrix remains a hurdle. Researchers are also working to develop water-borne formulations that eliminate harmful volatile organic compounds (VOCs). Overcoming these obstacles will unlock graphene’s full potential and expand its applications.
Graphene coatings are poised to revolutionize surface protection. Their unique combination of strength, conductivity, and flexibility ensures they will play a pivotal role in future innovations. As industries continue to explore their capabilities, graphene coatings may soon rival established solutions like sic ceramic coating in both performance and versatility.
SiC ceramic coating stands out as the premier choice for 2025 due to its unmatched durability, superior scratch resistance, and long-lasting performance. Compared to SiO2 coatings, which offer affordability and ease of application, SiC provides greater longevity and resilience in harsh conditions. While graphene coatings show promise with their advanced thermal conductivity and strength, they remain limited by developmental challenges.
Choosing the right ceramic coating requires careful consideration of cost, durability, and application needs. Professional installation ensures optimal performance and longevity. Evaluating factors like heat resistance, maintenance requirements, and surface preparation can help users make informed decisions. Consulting reputable installers guarantees a seamless experience and maximizes the coating’s benefits.
FAQ
What is the primary difference between SiC, SiO2, and Graphene ceramic coatings?
SiC coatings excel in durability and thermal stability. SiO2 coatings offer affordability and ease of application. Graphene coatings provide advanced thermal conductivity and strength but remain in early development stages. Each serves different needs based on performance and cost priorities.
How long does each type of ceramic coating last?
SiO2 coatings last 1–3 years with proper care. SiC coatings can last 7 years or more due to their superior hardness. Graphene coatings claim a lifespan of 5–10 years, but real-world performance often falls short due to formulation challenges.
Are ceramic coatings safe for all vehicle surfaces?
Yes, ceramic coatings are safe for most surfaces, including paint, glass, and plastics. However, professional application ensures proper bonding and avoids potential damage. Users should consult product guidelines to confirm compatibility with specific materials.
Which coating is best for high-temperature environments?
SiC coatings perform best in high-temperature environments due to their exceptional thermal stability and conductivity. Graphene coatings also excel in heat dissipation, making them suitable for applications requiring efficient temperature regulation. SiO2 coatings prioritize UV protection over heat resistance.
Can ceramic coatings be applied at home?
DIY kits are available for SiO2 and Graphene coatings, offering simple application processes. SiC coatings require professional expertise due to their precision demands. While DIY options save costs, professional installation ensures optimal performance and longevity.
How do ceramic coatings enhance a vehicle’s appearance?
Ceramic coatings create a glossy finish that enhances color depth and shine. SiO2 coatings provide a vibrant luster, while SiC coatings deliver a mirror-like finish. Graphene coatings offer a deep, glossy shine but may lack the pronounced effect of SiC coatings due to their thinner application layer.
Are ceramic coatings environmentally friendly?
SiO2 and SiC coatings are generally safe for the environment when applied correctly. Graphene coatings face challenges in developing water-borne formulations to eliminate harmful VOCs. Users should choose products with eco-friendly certifications to minimize environmental impact.
What is the cost range for ceramic coatings?
SiO2 coatings range from 50forDIYkitstoover50 for DIY kits to over 50forDIYkitstoover100 for professional-grade products. SiC coatings are more expensive due to their advanced properties. Graphene coatings cost 70–70–70–100 for a 30ml bottle, but their value depends on active ingredient content and performance.
Tip: Always compare product features and consult professionals to ensure the best value for your investment.