Silicon carbide coating offers you a durable, heat-resistant, and corrosion-resistant solution for protecting materials. This advanced layer enhances the performance and lifespan of components in demanding environments. Its unique properties, such as high hardness and thermal stability, make it ideal for industries requiring reliable protection. You’ll find that SIC coating resists chemical reactions, ensuring materials remain intact even in harsh conditions. Applications like SIC Tac Coating and silicon carbide coated susceptors demonstrate its versatility. For example, sic coated susceptors improve efficiency in semiconductor manufacturing by withstanding extreme temperatures without degrading.
Key Takeaways
- Silicon carbide coating is very strong and stops scratches or damage.
- It can handle very high heat, over 1,000°C, for hot uses.
- The coating does not get damaged by chemicals, even in tough places.
- Using this coating means less fixing is needed, saving time and money.
- It works well under pressure, helping planes and cars work better.
- This coating is cheap in the long run and makes parts last longer.
- It can be made special to fit different jobs or needs.
- Using silicon carbide coating helps the planet by cutting waste and saving energy.
What Is Silicon Carbide Coating?
Composition and Structure
Silicon carbide coating consists of silicon and carbon atoms arranged in a crystalline structure. This unique arrangement gives it exceptional hardness and strength. You’ll notice that its structure resembles a diamond, which explains its durability. The coating forms a thin, protective layer on surfaces, acting as a shield against wear and damage. It also has a high melting point, making it suitable for extreme environments.
The material’s chemical composition ensures stability under harsh conditions. It resists oxidation and chemical reactions, even when exposed to acids or alkalis. This makes it ideal for industries where materials face constant stress. The crystalline structure also contributes to its thermal conductivity, allowing heat to dissipate efficiently.
Manufacturing Process
The process of creating silicon carbide coating involves several precise steps. Manufacturers typically use chemical vapor deposition (CVD) or physical vapor deposition (PVD) techniques. In CVD, you introduce silicon and carbon gases into a chamber. These gases react at high temperatures, forming a thin layer of silicon carbide on the surface. PVD, on the other hand, involves vaporizing solid silicon carbide and depositing it onto the material.
Both methods ensure uniform coating and strong adhesion to the substrate. You’ll find that the choice of method depends on the application and desired properties. For example, CVD is often used for semiconductor components due to its precision. The manufacturing process also allows customization, enabling you to tailor the coating thickness and properties to specific needs.
Key Properties and Characteristics
Silicon carbide coating stands out for its remarkable properties. Its hardness ranks just below diamond, making it highly resistant to scratches and abrasion. This ensures long-lasting protection for materials in demanding environments. The coating also exhibits excellent thermal stability. It can withstand temperatures exceeding 1,000°C without degrading, making it perfect for high-heat applications.
Another key characteristic is its chemical inertness. You’ll appreciate how it resists corrosion from acids, alkalis, and other chemicals. This makes it a reliable choice for industries like aerospace and electronics. Additionally, the coating’s low thermal expansion minimizes the risk of cracking under temperature changes. Its lightweight nature further enhances its appeal, especially in applications where weight reduction is crucial.
By understanding these aspects, you can see why silicon carbide coating is a preferred solution across various industries. Its unique combination of strength, heat resistance, and chemical stability ensures superior performance and durability.
Benefits of Silicon Carbide Coating
Durability and Wear Resistance
You’ll find that silicon carbide coating offers unmatched durability. Its exceptional hardness protects surfaces from scratches, dents, and other forms of wear. This makes it ideal for environments where materials face constant friction or impact. For example, in industrial machinery, the coating reduces wear on moving parts, ensuring they last longer and perform efficiently.
The wear resistance of silicon carbide coating also minimizes maintenance needs. You won’t have to replace or repair components as often, saving time and resources. This durability proves especially valuable in industries like aerospace and automotive, where reliability is critical. By choosing silicon carbide coating, you ensure your equipment remains operational even under extreme stress.
Heat Resistance and Thermal Stability
Silicon carbide coating excels in high-temperature environments. It can withstand temperatures exceeding 1,000°C without breaking down or losing its protective properties. This makes it a reliable choice for applications like furnaces, turbines, and semiconductor manufacturing. You’ll notice that even under intense heat, the coating maintains its structural integrity.
Its thermal stability also prevents thermal shock. When materials experience rapid temperature changes, they often crack or deform. Silicon carbide coating minimizes this risk by expanding and contracting at a controlled rate. This ensures your components remain intact, even in fluctuating conditions. If you work in industries that deal with extreme heat, this coating provides the protection you need.
Corrosion Resistance in Harsh Environments
In environments exposed to chemicals, moisture, or salt, corrosion can quickly degrade materials. Silicon carbide coating acts as a barrier, shielding surfaces from these harmful elements. You’ll appreciate how it resists acids, alkalis, and other corrosive substances, ensuring your equipment stays functional.
This corrosion resistance proves especially useful in industries like marine, chemical processing, and electronics. For instance, in offshore drilling, silicon carbide coating protects equipment from saltwater corrosion. In electronics, it prevents damage from chemical exposure during manufacturing. By using this coating, you extend the lifespan of your materials and reduce the risk of failure in harsh conditions.
Cost-Effectiveness Over Time
Silicon carbide coating provides long-term savings by reducing maintenance and replacement costs. Its durability ensures that components last longer, even in challenging environments. You won’t need to replace parts as frequently, which lowers operational expenses. This makes it a cost-effective solution for industries that rely on high-performance equipment.
The coating’s resistance to wear and corrosion also minimizes downtime. When machinery operates without interruptions, productivity increases. You can allocate resources more efficiently instead of spending time and money on repairs. Over time, this reliability translates into significant financial benefits.
Another advantage is its ability to maintain performance under extreme conditions. Materials coated with silicon carbide retain their functionality, even after prolonged exposure to heat or chemicals. This reduces the risk of unexpected failures, which can be costly. By investing in this coating, you ensure consistent performance and avoid unplanned expenses.
In addition, the manufacturing process allows customization. You can tailor the coating to meet specific requirements, optimizing its cost-effectiveness. For example, adjusting the thickness can balance initial costs with long-term benefits. This flexibility makes silicon carbide coating a practical choice for various applications.
Enhanced Performance in High-Stress Applications
Silicon carbide coating excels in high-stress environments where materials face intense pressure, heat, or friction. Its exceptional hardness protects surfaces from damage, ensuring reliable performance. You’ll notice that components coated with this material perform better and last longer, even under extreme conditions.
In aerospace and defense, the coating enhances the durability of critical components. It withstands the high temperatures and pressures experienced during flight. This ensures the safety and efficiency of aircraft systems. Similarly, in the automotive industry, it improves the performance of engine parts and braking systems. These components endure constant stress, and the coating helps them function effectively.
The coating’s thermal stability also plays a crucial role. It prevents materials from deforming or cracking when exposed to rapid temperature changes. This makes it ideal for applications like turbines and furnaces. You can rely on silicon carbide coating to maintain structural integrity in these demanding settings.
Its chemical resistance further boosts performance in industries like electronics and chemical processing. The coating protects sensitive equipment from corrosive substances, ensuring uninterrupted operation. By choosing silicon carbide coating, you enhance the reliability and efficiency of your systems in high-stress applications.
Applications of Silicon Carbide Coating
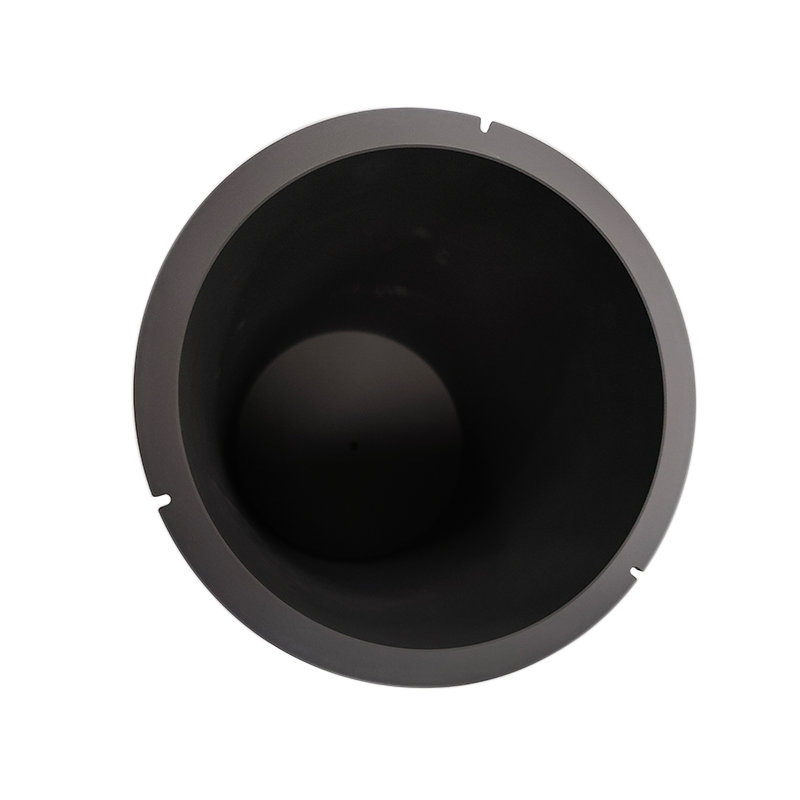
Aerospace and Defense
You’ll find silicon carbide coating indispensable in aerospace and defense applications. Aircraft and spacecraft components face extreme conditions, including high temperatures, friction, and exposure to corrosive elements. This coating protects critical parts like turbine blades, heat shields, and engine components. Its ability to withstand temperatures above 1,000°C ensures these parts maintain their integrity during operation.
In defense, the coating enhances the durability of equipment used in harsh environments. For example, it protects missile components and radar systems from wear and corrosion. Its lightweight nature also makes it ideal for applications where reducing weight is crucial. By using silicon carbide coating, you improve the reliability and performance of aerospace and defense systems.
Automotive Components
In the automotive industry, silicon carbide coating plays a vital role in improving the efficiency and lifespan of components. Engine parts, such as pistons and cylinders, benefit from its wear resistance. The coating reduces friction between moving parts, which enhances fuel efficiency and minimizes energy loss. You’ll notice smoother engine performance and fewer maintenance requirements.
Brake systems also rely on this coating for durability. It protects brake rotors and pads from wear caused by constant friction. This ensures consistent braking performance and extends the lifespan of these critical components. Additionally, the coating’s heat resistance prevents overheating, which is essential for safety in high-performance vehicles. By incorporating silicon carbide coating, you enhance the reliability and longevity of automotive systems.
Electronics and Semiconductor Industry
Silicon carbide coating is a game-changer in the electronics and semiconductor industry. It protects delicate components from damage caused by heat, chemicals, and wear. For instance, silicon carbide-coated susceptors improve the efficiency of semiconductor manufacturing. These susceptors withstand extreme temperatures during the production process without degrading.
In electronics, the coating shields sensitive parts from corrosion and thermal stress. It ensures the longevity of devices like circuit boards and sensors. You’ll also find it useful in protecting optical components, such as lenses and mirrors, from scratches and chemical exposure. By using silicon carbide coating, you enhance the performance and durability of electronic and semiconductor devices.
Energy and Power Systems
Silicon carbide coating plays a critical role in energy and power systems. You’ll notice its effectiveness in protecting components exposed to extreme heat, pressure, and corrosive environments. Power plants, for example, rely on this coating to enhance the durability of turbines, heat exchangers, and boiler tubes. These components often operate under intense thermal and mechanical stress. The coating ensures they maintain their structural integrity and efficiency over time.
In renewable energy systems, silicon carbide coating improves the performance of solar panels and wind turbines. Solar panels benefit from its ability to resist wear and corrosion caused by environmental factors like dust, moisture, and UV radiation. This protection ensures consistent energy output and reduces maintenance needs. Wind turbine blades, coated with silicon carbide, withstand the abrasive effects of high-speed winds and airborne particles. This durability extends their operational lifespan and minimizes downtime.
You’ll also find this coating valuable in battery technology. It enhances the thermal management of battery systems by dissipating heat efficiently. This prevents overheating and improves the safety and performance of energy storage solutions. In fuel cells, silicon carbide coating protects components from chemical degradation, ensuring reliable operation in harsh conditions.
The coating’s lightweight nature further benefits energy systems by reducing the overall weight of components. This is especially important in applications like aerospace power systems, where weight reduction translates to improved efficiency. By incorporating silicon carbide coating, you optimize the performance and longevity of energy and power systems.
Medical and Optical Equipment
In the medical field, silicon carbide coating ensures the reliability and safety of critical equipment. Surgical tools, for instance, benefit from its wear resistance and chemical inertness. The coating prevents corrosion caused by sterilization processes, ensuring tools remain sharp and functional. You’ll also find it used in medical implants, where its biocompatibility ensures compatibility with the human body.
Optical equipment, such as lenses and mirrors, also relies on silicon carbide coating for protection. The coating resists scratches and chemical damage, preserving the clarity and precision of optical surfaces. This is particularly important in medical imaging devices, where accuracy is crucial. You’ll notice that coated lenses maintain their performance even after prolonged use in demanding environments.
In addition, the coating enhances the durability of diagnostic equipment. Devices like endoscopes and microscopes face constant handling and exposure to cleaning agents. Silicon carbide coating shields these instruments from wear and corrosion, ensuring consistent performance. By using this coating, you improve the reliability and lifespan of medical and optical equipment.
Comparison with Other Coatings
Silicon Carbide Coating vs. Ceramic Coatings
When comparing silicon carbide coating to ceramic coatings, you’ll notice key differences in performance and application. Both options provide excellent heat resistance, but silicon carbide coating offers superior durability. Its hardness ranks just below diamond, making it more resistant to scratches and wear. Ceramic coatings, while effective, tend to be more brittle. This brittleness increases the risk of cracking under mechanical stress.
Thermal conductivity is another area where silicon carbide coating excels. It dissipates heat more efficiently, which is crucial in high-temperature applications like turbines or semiconductor manufacturing. Ceramic coatings, on the other hand, often act as thermal insulators. This makes them suitable for applications requiring heat retention, such as engine exhaust systems.
Chemical resistance also sets silicon carbide coating apart. It withstands exposure to acids, alkalis, and other corrosive substances better than most ceramic coatings. If you work in industries like electronics or chemical processing, this advantage ensures longer-lasting protection for your equipment.
Silicon Carbide Coating vs. Metal Coatings
Metal coatings, such as chrome or nickel, offer good wear resistance and corrosion protection. However, silicon carbide coating outperforms them in extreme environments. Its ability to withstand temperatures above 1,000°C makes it ideal for high-heat applications. Metal coatings often degrade or oxidize at such temperatures, reducing their effectiveness.
You’ll also find that silicon carbide coating provides better chemical inertness. Metal coatings can corrode when exposed to harsh chemicals, while silicon carbide remains unaffected. This makes it a more reliable choice for industries like aerospace or marine, where materials face constant chemical exposure.
In terms of weight, silicon carbide coating has the advantage. It adds minimal weight to components, which is critical in applications like aviation or automotive. Metal coatings, while durable, often increase the overall weight of the material. This can impact performance and fuel efficiency in weight-sensitive industries.
Cost-Performance Analysis
When evaluating cost-performance, silicon carbide coating proves to be a long-term investment. Its durability reduces the need for frequent maintenance or replacement, saving you money over time. While the initial cost may be higher than some alternatives, the extended lifespan of coated components offsets this expense.
Metal coatings may seem more affordable upfront, but their shorter lifespan and susceptibility to wear can lead to higher maintenance costs. Ceramic coatings, though durable, often require specialized application techniques, which can increase costs. Silicon carbide coating strikes a balance by offering exceptional performance and durability with customizable application methods.
If you prioritize reliability and long-term savings, silicon carbide coating provides the best value. Its ability to perform under extreme conditions ensures consistent results, making it a cost-effective solution for demanding industries.
Environmental Impact of Silicon Carbide Coating
Sustainability in Production
You’ll find that the production of silicon carbide coating aligns with modern sustainability goals. Manufacturers often use energy-efficient methods like chemical vapor deposition (CVD) to create the coating. These processes minimize waste by ensuring precise application and reducing material loss. Additionally, the raw materials used, silicon and carbon, are abundant and widely available. This reduces the environmental strain caused by resource extraction.
Some manufacturers also focus on reducing emissions during production. By optimizing energy use and adopting cleaner technologies, they lower the carbon footprint of the coating process. You can see how these efforts contribute to a more sustainable manufacturing cycle. Choosing silicon carbide coating supports industries that prioritize eco-friendly practices.
Longevity and Waste Reduction
The durability of silicon carbide coating plays a significant role in reducing waste. Its exceptional wear resistance ensures that coated components last longer, even in harsh conditions. You won’t need to replace parts as frequently, which reduces the amount of discarded materials. This longevity helps industries cut down on waste and conserve resources.
For example, in automotive and aerospace applications, the coating extends the lifespan of critical components. This reduces the need for frequent replacements, saving both materials and energy. By using silicon carbide coating, you contribute to a circular economy where products are designed to last and generate less waste over time.
Eco-Friendly Applications
Silicon carbide coating supports eco-friendly applications across various industries. In renewable energy systems, it enhances the efficiency of solar panels and wind turbines. The coating protects these systems from environmental damage, ensuring consistent energy output. You’ll notice that this improves the sustainability of renewable energy solutions.
In electronics, the coating prevents corrosion and extends the life of devices. This reduces electronic waste, which is a growing environmental concern. Medical equipment also benefits from the coating’s durability, ensuring tools and devices remain functional for longer periods. By choosing silicon carbide coating, you support applications that align with environmental conservation goals.
Future Trends and Innovations
Emerging Technologies in Silicon Carbide Coating
You’ll notice that emerging technologies are transforming the way silicon carbide coating is applied and utilized. One exciting development is the integration of nanotechnology. Researchers are exploring how nanoparticles can enhance the coating’s properties, such as improving its hardness and thermal conductivity. This innovation could lead to even more durable and efficient coatings for high-performance applications.
Another trend involves the use of artificial intelligence (AI) in the coating process. AI algorithms analyze data to optimize application techniques, ensuring uniform coverage and reducing material waste. This technology also predicts potential issues during manufacturing, allowing you to address them before they occur. These advancements make the coating process more precise and cost-effective.
Plasma-enhanced chemical vapor deposition (PECVD) is another emerging technology. This method uses plasma to deposit the coating at lower temperatures, making it suitable for heat-sensitive materials. You’ll find this particularly useful in industries like electronics, where delicate components require careful handling.
Advancements in Manufacturing Techniques
Manufacturing techniques for silicon carbide coating are evolving rapidly. One significant advancement is the development of 3D printing methods. By combining 3D printing with coating technologies, manufacturers can create complex shapes with precise silicon carbide layers. This innovation opens up new possibilities for custom-designed components in aerospace, automotive, and medical industries.
Another breakthrough is the use of environmentally friendly processes. Manufacturers are adopting green technologies to reduce emissions and energy consumption during production. For example, some companies now use renewable energy sources to power their coating facilities. These efforts align with global sustainability goals and help you make eco-conscious choices.
Automation is also revolutionizing the manufacturing process. Robotic systems apply the coating with unmatched accuracy, ensuring consistent quality across large-scale production. This reduces human error and increases efficiency, making the coating more accessible for various applications.
Expanding Applications Across Industries
The versatility of silicon carbide coating continues to drive its adoption across new industries. In the food processing sector, the coating is being used to protect equipment from wear and corrosion caused by constant exposure to moisture and chemicals. This ensures food safety and reduces maintenance costs.
In the textile industry, silicon carbide coating is gaining popularity for its ability to enhance the durability of machinery. Coated components last longer, even under the stress of continuous operation. This improves productivity and reduces downtime.
You’ll also see its applications expanding in space exploration. The coating’s lightweight and heat-resistant properties make it ideal for spacecraft components. It protects against extreme temperatures and abrasive particles encountered in outer space. These advancements highlight the growing importance of silicon carbide coating in diverse fields.
Silicon carbide coating offers you unmatched durability, heat resistance, and corrosion protection. These qualities make it essential for improving the performance and lifespan of materials in demanding industries. By using this coating, you reduce maintenance needs and enhance sustainability through waste reduction and energy efficiency.
Its potential for innovation continues to grow. Advancements in manufacturing and emerging technologies promise even broader applications. Whether in aerospace, automotive, or renewable energy, this coating remains a reliable solution for high-performance needs. You can expect it to play a critical role in shaping the future of industrial and environmental advancements.
FAQ
What industries benefit the most from silicon carbide coating?
Industries like aerospace, automotive, electronics, and renewable energy benefit significantly. You’ll find it enhances durability, heat resistance, and corrosion protection in these fields. Medical and optical equipment also rely on this coating for improved performance and longevity.
How does silicon carbide coating improve energy efficiency?
The coating reduces friction and wear in machinery, which minimizes energy loss. Its thermal conductivity helps dissipate heat efficiently, preventing overheating. You’ll notice improved performance and reduced energy consumption in applications like engines, turbines, and renewable energy systems.
Is silicon carbide coating environmentally friendly?
Yes, it supports sustainability. Its durability reduces waste by extending the lifespan of components. Manufacturers often use energy-efficient processes, and the coating enhances eco-friendly applications like solar panels and wind turbines. By choosing it, you contribute to waste reduction and energy conservation.
Tip: Look for manufacturers that prioritize green production methods for an even greater environmental impact.
Can silicon carbide coating be customized for specific needs?
Absolutely! You can tailor the coating’s thickness, hardness, and thermal properties to suit your application. For example, thinner coatings work well for electronics, while thicker layers provide extra durability for industrial machinery.
How does silicon carbide coating compare to traditional coatings?
Silicon carbide coating outperforms traditional coatings in durability, heat resistance, and chemical inertness. Unlike metal coatings, it withstands extreme temperatures without degrading. It also resists corrosion better than ceramic coatings, making it ideal for harsh environments.
What maintenance does silicon carbide coating require?
Minimal maintenance is needed. Its wear resistance and corrosion protection reduce the need for frequent repairs or replacements. Regular cleaning suffices to maintain its performance. You’ll save time and resources with this low-maintenance solution.
Is silicon carbide coating suitable for high-temperature applications?
Yes, it excels in high-temperature environments. It withstands temperatures above 1,000°C without losing its protective properties. You’ll find it ideal for furnaces, turbines, and semiconductor manufacturing, where extreme heat is common.
How long does silicon carbide coating last?
The lifespan depends on the application and operating conditions. In most cases, it lasts significantly longer than traditional coatings. Its durability ensures extended protection, reducing the need for replacements and lowering long-term costs.
Note: Proper application and regular maintenance can further extend its lifespan.
Contact: Kelly Feng Mob/Whatsapp: 86-17386007648 Email: sales003@china-vet.com