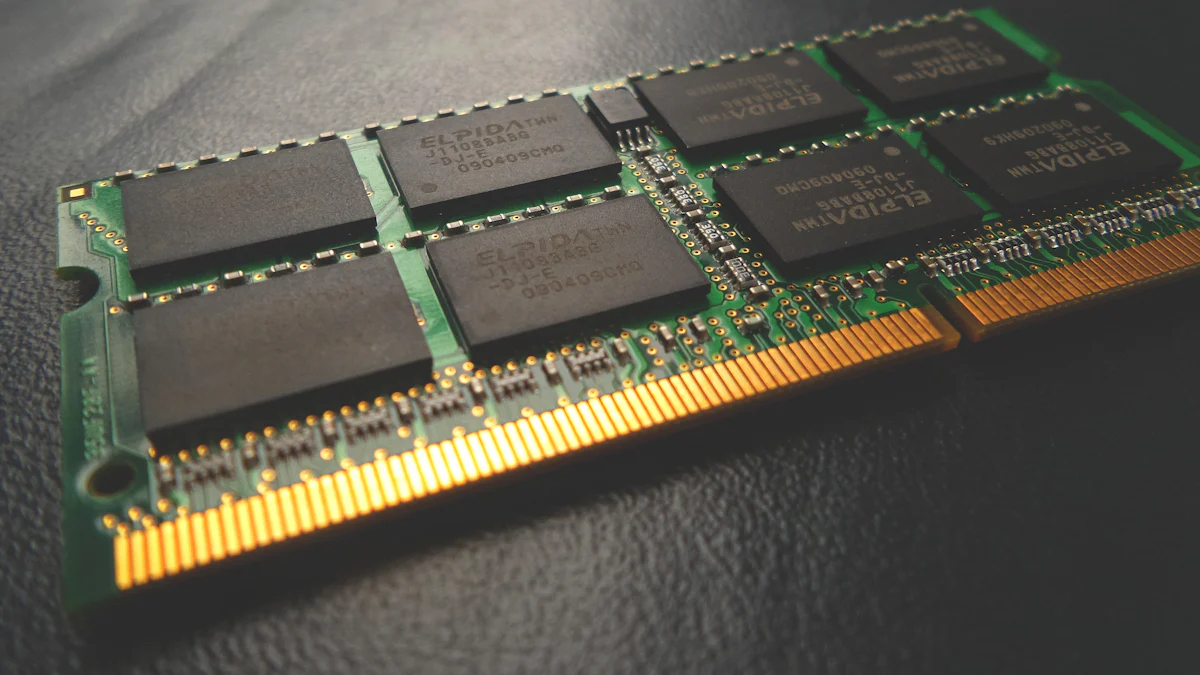
Silicon carbide wafers stand out from traditional silicon due to their superior performance and diverse applications. They offer higher thermal conductivity and can operate at elevated voltages, making them ideal for high-power and high-frequency applications. Industries such as electric vehicles, aerospace, and power grids increasingly rely on silicon carbide wafers for their efficiency and durability. The market for these wafers is experiencing rapid growth, with projections indicating a compound annual growth rate of 22.3% by 2029. This surge underscores the growing importance of silicon carbide in advancing electronic efficiencies across various sectors.
Key Takeaways
- Silicon carbide wafers offer superior thermal conductivity, allowing for efficient heat dissipation in high-power applications, making them ideal for industries like electric vehicles and aerospace.
- With a wider bandgap than traditional silicon, silicon carbide wafers can operate at higher voltages and temperatures, enhancing the efficiency and reliability of electronic devices.
- The durability and chemical stability of silicon carbide wafers ensure a longer lifespan for devices, reducing maintenance costs and downtime in demanding environments.
- Silicon carbide excels in power efficiency, significantly reducing energy loss in electronic devices, which is crucial for sustainable technology development.
- These wafers are particularly suited for high-voltage applications, capable of handling voltages up to ten times higher than traditional silicon, making them essential for power grids and electric vehicles.
- Despite higher manufacturing costs, advancements in technology are gradually making silicon carbide wafers more accessible, with a projected market growth rate of 22.3% by 2029.
- Industries should consider the long-term benefits of silicon carbide wafers, such as improved performance and energy efficiency, against the initial investment for optimal material selection.
Material Properties of Silicon Carbide Wafers
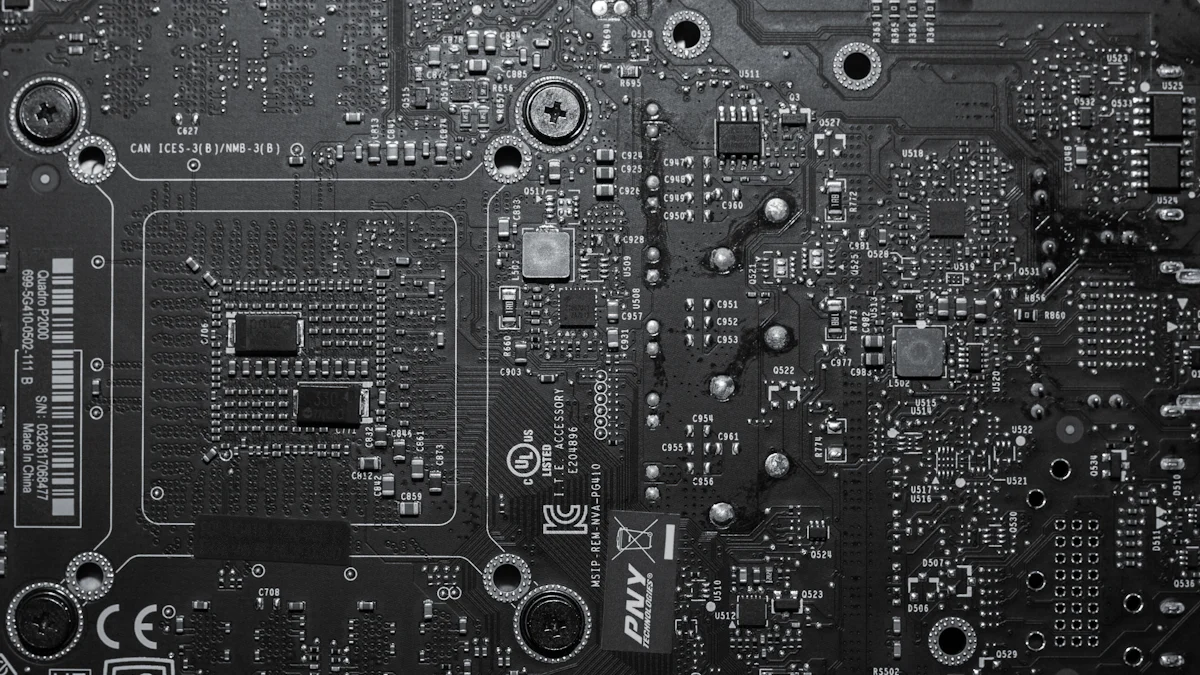
Physical Properties
Thermal Conductivity
Silicon carbide wafers exhibit exceptional thermal conductivity, which significantly surpasses that of traditional silicon. This property allows them to efficiently dissipate heat, making them ideal for high-power applications. Devices utilizing silicon carbide can operate at higher temperatures without compromising performance. This capability is crucial in industries where thermal management is a priority, such as electric vehicles and aerospace.
Bandgap
The bandgap of silicon carbide is wider than that of silicon, providing several advantages. A wider bandgap enables devices to function at higher voltages and temperatures. This characteristic enhances the efficiency and reliability of electronic components, especially in high-frequency applications. The wide bandgap also contributes to reduced energy loss, which is essential for modern electronic devices striving for energy efficiency.
Chemical Properties
Durability
Silicon carbide wafers are renowned for their durability. They possess a robust structure that withstands harsh environmental conditions, making them suitable for demanding applications. This durability ensures a longer lifespan for devices, reducing the need for frequent replacements and maintenance. Industries that require reliable and long-lasting components, such as power grids and industrial equipment, benefit greatly from this property.
Chemical Stability
The chemical stability of silicon carbide is another significant advantage. It resists chemical reactions that could degrade its performance over time. This stability is particularly beneficial in environments exposed to corrosive substances or extreme conditions. As a result, silicon carbide wafers maintain their integrity and functionality, ensuring consistent performance in various applications.
Performance Comparison of Silicon Carbide Wafers and Traditional Silicon
Efficiency
Power Efficiency
Silicon carbide wafers excel in power efficiency compared to traditional silicon. Their wide bandgap of 3.26 eV allows for faster switching speeds, which enhances the overall efficiency of electronic devices. This characteristic enables the creation of smaller, more efficient devices that consume less power. In high-power applications, silicon carbide wafers significantly reduce energy loss, making them a preferred choice for industries aiming to optimize energy consumption.
Energy Loss
Energy loss in electronic devices often results from inefficient heat management and electrical resistance. Silicon carbide wafers address these issues with their superior thermal conductivity and lower ON-resistance. These properties minimize energy dissipation as heat, ensuring that devices operate more efficiently. By reducing energy loss, silicon carbide wafers contribute to the development of sustainable technologies that prioritize energy conservation.
Power Handling
High-Voltage Applications
Silicon carbide wafers demonstrate remarkable performance in high-voltage applications. They can withstand voltages up to ten times higher than traditional silicon, making them ideal for power conversion and distribution systems. This capability is crucial for industries such as electric vehicles and power grids, where high-voltage handling is essential for efficient operation and safety.
Current Capacity
The current capacity of silicon carbide wafers surpasses that of traditional silicon due to their higher breakdown electric field strength. This attribute allows devices to handle larger currents without compromising performance. As a result, silicon carbide wafers are well-suited for applications requiring robust power handling, such as industrial equipment and high-power electronics.
Temperature Tolerance
High-Temperature Performance
Silicon carbide wafers exhibit exceptional high-temperature performance, a critical factor in many industrial applications. Their ability to operate at elevated temperatures without degradation ensures reliability and longevity in demanding environments. This makes them particularly valuable in sectors like aerospace and automotive, where components must endure extreme conditions.
Thermal Management
Effective thermal management is vital for maintaining device performance and preventing thermal runaway. Silicon carbide wafers offer superior thermal conductivity, which facilitates efficient heat dissipation. This property often eliminates the need for additional cooling systems, reducing both the complexity and cost of device design. Industries benefit from this advantage by achieving more compact and cost-effective solutions.
Applications of Silicon Carbide Wafers
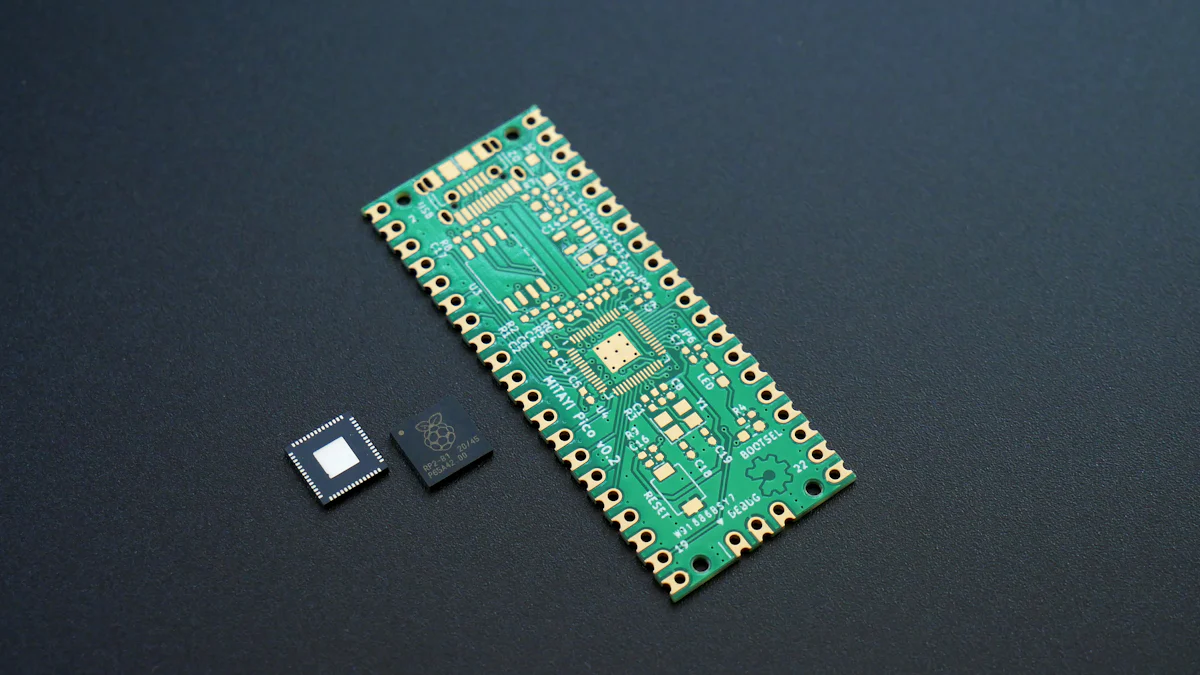
High-Power Environments
Electric Vehicles
Silicon carbide wafers have revolutionized the electric vehicle (EV) industry. Their ability to handle higher voltages and temperatures makes them ideal for EV power electronics. Silicon carbide enables efficient energy conversion in on-board DC/DC converters and off-board DC fast chargers. These wafers also enhance the performance of on-board battery chargers and EV powertrains. The automotive lighting systems, particularly LEDs, benefit from silicon carbide’s superior properties. By reducing energy loss and improving power density, silicon carbide wafers contribute to longer driving ranges and faster charging times for electric vehicles.
Power Grids
Power grids require components that can handle high voltages and currents efficiently. Silicon carbide wafers excel in these applications due to their high breakdown electric field strength. They improve the efficiency and reliability of power conversion and distribution systems. Silicon carbide’s thermal conductivity ensures effective heat dissipation, reducing the risk of overheating in power grid components. This capability supports the integration of renewable energy sources, such as solar and wind power, into the grid. By enhancing the performance of power grids, silicon carbide wafers play a crucial role in advancing sustainable energy solutions.
High-Temperature Environments
Aerospace
The aerospace industry demands materials that can withstand extreme conditions. Silicon carbide wafers meet this requirement with their exceptional high-temperature performance. They maintain stability and functionality in aerospace applications, where components face intense heat and pressure. Silicon carbide’s durability ensures the longevity of electronic systems in aircraft and spacecraft. Its ability to operate at elevated temperatures without degradation enhances the reliability of critical aerospace components. By providing efficient thermal management, silicon carbide wafers contribute to safer and more efficient aerospace technologies.
Industrial Equipment
Industrial equipment often operates in harsh environments, requiring materials that can endure high temperatures and mechanical stress. Silicon carbide wafers offer the necessary durability and thermal stability for these applications. They improve the efficiency of industrial motors and HVAC systems by reducing energy loss and enhancing power handling capabilities. Silicon carbide’s chemical stability ensures resistance to corrosive substances, making it suitable for use in challenging industrial settings. By extending the lifespan of industrial equipment, silicon carbide wafers reduce maintenance costs and downtime, contributing to increased productivity.
Cost and Availability of Silicon Carbide Wafers
Cost Implications
Manufacturing Costs
Silicon carbide wafers, while offering superior performance, come with higher manufacturing costs compared to traditional silicon. The production process for silicon carbide involves more complex and precise techniques, which contribute to the increased cost. Despite these higher initial expenses, advancements in technology and economies of scale are gradually reducing these costs. For instance, the 4H silicon carbide variant is cheaper to manufacture than its 6H counterpart, although both remain more expensive than traditional silicon.
Market Pricing
The market pricing of silicon carbide wafers reflects their advanced capabilities and the costs associated with their production. However, a downward trend in prices has been observed due to technological advancements and increased production volumes. This trend is expected to continue, making silicon carbide wafers more accessible to a broader range of industries. The global market for silicon carbide wafers is projected to grow significantly, reaching USD 4,385,550.41 Thousand by 2029, with a compound annual growth rate (CAGR) of 22.3% from 2022 to 2029. This growth indicates a promising future for silicon carbide in various applications.
Availability
Supply Chain Considerations
The availability of silicon carbide wafers depends heavily on the supply chain dynamics. Yield rates, often kept confidential within the industry, play a crucial role in determining the supply. Most forecasts estimate supply based on nameplate capacity, which can vary significantly across manufacturers. As demand for silicon carbide increases, companies are investing in expanding their production capabilities to ensure a steady supply. This expansion is essential to meet the growing needs of industries such as electric vehicles and power grids.
Market Trends
Market trends indicate a robust growth trajectory for silicon carbide wafers. The market size was valued at USD 742.7 Million in 2023 and is projected to reach USD 2,019.4 Million by 2030, growing at a CAGR of 20.3% during the forecast period from 2024 to 2030. This growth is driven by the increasing adoption of silicon carbide in high-voltage and high-temperature applications. As more industries recognize the benefits of silicon carbide, the demand is expected to rise, further influencing market trends and availability.
Silicon carbide wafers offer several advantages over traditional silicon, particularly in high-power applications. They excel in handling high voltages, high temperatures, and high currents due to their superior thermal conductivity and wide bandgap. These properties make them ideal for industries requiring efficient power management and durability. However, the higher capital cost remains a consideration for potential adopters. When selecting materials, industries should weigh these benefits against the initial investment. For applications demanding high performance and reliability, silicon carbide presents a compelling choice, ensuring long-term efficiency and reduced energy losses.
FAQ
What is a typical silicon carbide wafer?
A silicon carbide (SiC) wafer serves as a semiconductor material composed of silicon and carbon. Manufacturers create these wafers by etching crystalline silicon carbide, resulting in a thin material suitable for power semiconductor devices. SiC wafers exhibit conductivity in both directions, making them versatile for various applications. Their ability to operate across a wide temperature range proves crucial for managing electrical and magnetic fields in power semiconductors.
How does silicon carbide compare to traditional silicon in terms of thermal conductivity?
Silicon carbide significantly outperforms traditional silicon in thermal conductivity. This superior property allows SiC wafers to efficiently dissipate heat, which is essential for high-power applications. Devices using silicon carbide can maintain performance at higher temperatures, reducing the risk of overheating and enhancing reliability.
Why is the bandgap of silicon carbide important?
The wider bandgap of silicon carbide, compared to traditional silicon, offers several advantages. It enables devices to function at higher voltages and temperatures, enhancing efficiency and reliability. This characteristic also reduces energy loss, which is vital for modern electronic devices striving for energy efficiency.
What industries benefit most from silicon carbide wafers?
Industries such as electric vehicles, aerospace, and power grids benefit significantly from silicon carbide wafers. These sectors require materials that can handle high voltages, temperatures, and currents efficiently. Silicon carbide’s superior properties make it ideal for applications demanding robust power management and durability.
Are silicon carbide wafers more expensive than traditional silicon?
Yes, silicon carbide wafers generally incur higher manufacturing costs than traditional silicon due to the complex production processes involved. However, technological advancements and economies of scale are gradually reducing these costs, making SiC wafers more accessible to a broader range of industries.
How do silicon carbide wafers contribute to energy efficiency?
Silicon carbide wafers enhance energy efficiency through their wide bandgap and superior thermal conductivity. These properties allow for faster switching speeds and reduced energy loss, enabling the creation of smaller, more efficient devices that consume less power. This efficiency is particularly beneficial in high-power applications.
What are the supply chain considerations for silicon carbide wafers?
The availability of silicon carbide wafers heavily depends on supply chain dynamics, including yield rates and production capacities. As demand increases, manufacturers are investing in expanding their production capabilities to ensure a steady supply, especially for industries like electric vehicles and power grids.
How do silicon carbide wafers perform in high-temperature environments?
Silicon carbide wafers excel in high-temperature environments due to their exceptional thermal stability. They maintain performance without degradation, ensuring reliability and longevity in demanding conditions. This makes them valuable in sectors like aerospace and automotive, where components must endure extreme temperatures.
What role do silicon carbide wafers play in power grids?
In power grids, silicon carbide wafers improve efficiency and reliability by handling high voltages and currents effectively. Their high breakdown electric field strength and thermal conductivity support efficient power conversion and distribution, facilitating the integration of renewable energy sources into the grid.
How does the market for silicon carbide wafers look in the future?
The market for silicon carbide wafers is projected to grow significantly, driven by increasing adoption in high-voltage and high-temperature applications. As more industries recognize the benefits of SiC, demand is expected to rise, influencing market trends and availability positively.