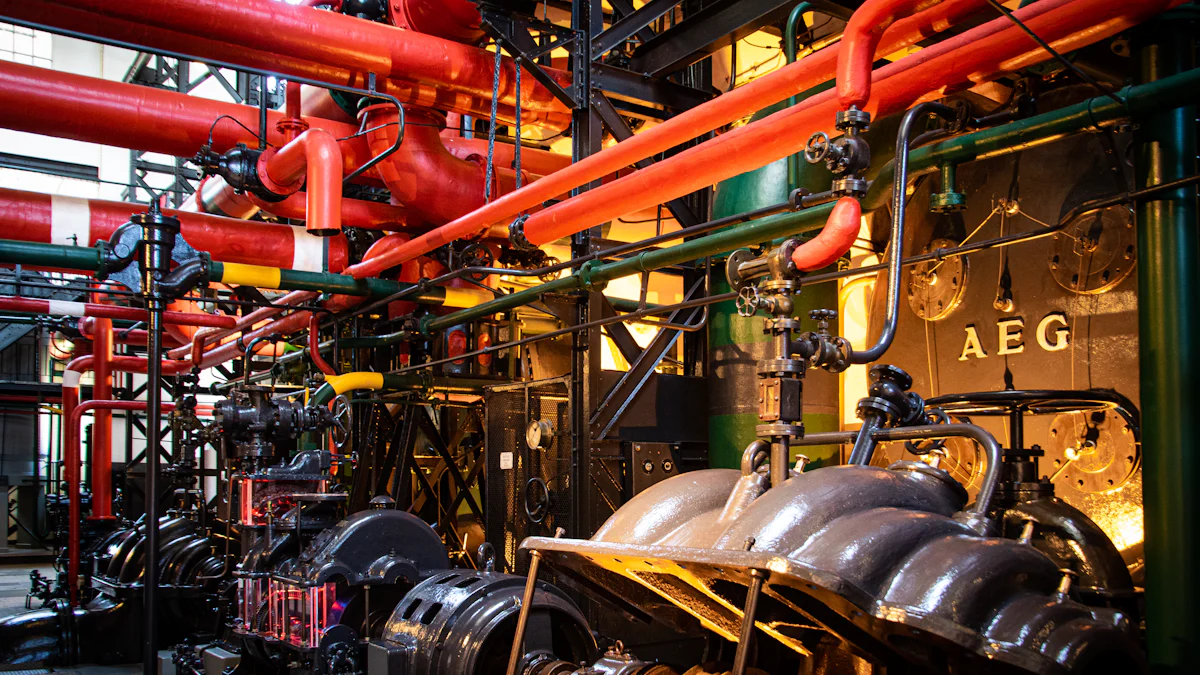
Solid SiC Focus Rings significantly enhance production efficiency across various industries. These rings, crafted from Sic Silicon Carbide Ceramic, offer unmatched durability and thermal stability. Their robust nature ensures longevity, reducing the need for frequent replacements and thus optimizing equipment performance. The precision of these Durable Focus Rings ensures consistent quality in manufacturing processes. By choosing a Sic Focus Ring, businesses can achieve longer replacement cycles and superior performance without incurring substantial costs. But what is a solid SiC focus ring? It is a critical component that boosts productivity by maintaining high standards of precision and reliability.
Key Takeaways
- Solid SiC Focus Rings enhance production efficiency by providing exceptional durability and thermal stability, reducing the need for frequent replacements.
- These rings are crucial in semiconductor manufacturing, particularly in processes like plasma etching and chemical vapor deposition, ensuring high precision and reliability.
- Investing in Solid SiC Focus Rings leads to significant cost savings over time due to their extended service life and reduced maintenance needs.
- The superior mechanical strength of silicon carbide allows these rings to withstand harsh environments, making them ideal for various industries, including automotive and aerospace.
- By maintaining consistent quality and reducing defects, Solid SiC Focus Rings contribute to higher manufacturing yields and improved customer satisfaction.
- Choosing Solid SiC over traditional materials like quartz and alumina offers unmatched performance, particularly in high-temperature and high-stress applications.
- Integrating Solid SiC Focus Rings into production processes not only boosts operational efficiency but also supports sustainable manufacturing practices by minimizing waste.
Understanding Solid SiC Focus Rings
Definition and Composition
What are Solid SiC Focus Rings?
Solid SiC Focus Rings serve as essential components in semiconductor wafer processing. They are crafted from silicon carbide, a material renowned for its exceptional properties. These rings play a pivotal role in processes such as plasma etching, CVD (Chemical Vapor Deposition), and ICP RIE (Inductively Coupled Plasma Reactive Ion Etching). Their design ensures they withstand high-stress environments, providing unparalleled resistance to erosion and wear. This makes them indispensable in maintaining the integrity and efficiency of semiconductor manufacturing equipment.
Material properties of Silicon Carbide
Silicon carbide, the core material of these focus rings, boasts several remarkable properties. It offers high thermal stability, ensuring performance consistency even under extreme temperatures. Its mechanical strength provides resistance to physical stress, while its chemical stability protects against corrosion in harsh environments. These attributes make silicon carbide an ideal choice for applications requiring durability and precision. The material’s high hardness and resistance to chemical erosion further enhance its suitability for use in semiconductor manufacturing.
Role in Production Processes
Application in various industries
Solid SiC Focus Rings find applications across a range of industries beyond semiconductors. In the automotive sector, they contribute to the efficiency of power electronics and renewable energy systems. Their ability to handle high-power and high-frequency devices makes them valuable in these fields. Additionally, their use extends to industries that require precision and reliability in manufacturing processes, such as aerospace and defense.
Importance in manufacturing efficiency
The integration of Solid SiC Focus Rings into production processes significantly boosts manufacturing efficiency. Their durability reduces the frequency of replacements, leading to cost savings and minimized downtime. The thermal and chemical stability of these rings ensures consistent quality in production, reducing defects and waste. By maintaining high standards of precision and reliability, they enhance overall productivity and contribute to higher manufacturing yields.
Key Benefits of Solid SiC Focus Rings
Durability and Longevity
Resistance to wear and tear
Solid SiC Focus Rings exhibit remarkable resistance to wear and tear. Their construction from silicon carbide, a material known for its high mechanical strength, ensures they withstand the rigors of demanding production environments. Unlike traditional materials such as quartz and alumina, these rings maintain their integrity even under continuous use. This durability translates into fewer replacements, minimizing disruptions in production processes.
Cost savings from reduced replacements
The longevity of Solid SiC Focus Rings leads to significant cost savings. Businesses benefit from extended service life, reducing the frequency of replacements. This not only lowers material costs but also decreases labor expenses associated with maintenance. Over time, the investment in these durable rings proves financially advantageous, enhancing overall operational efficiency.
Thermal Stability
Performance under high temperatures
Solid SiC Focus Rings excel in high-temperature environments. Silicon carbide’s superior thermal stability allows these rings to perform consistently even under extreme heat. This characteristic is crucial in industries where maintaining precise temperature control is essential for product quality. The rings’ ability to endure high temperatures without degradation ensures reliable performance across various applications.
Impact on production consistency
The thermal stability of Solid SiC Focus Rings contributes to consistent production outcomes. By maintaining their structural integrity under fluctuating temperatures, these rings help ensure uniformity in manufacturing processes. This consistency reduces the likelihood of defects, leading to higher-quality products and improved customer satisfaction.
Precision and Consistency
Ensuring consistent production quality
Precision is a hallmark of Solid SiC Focus Rings. Their design and material properties enable them to deliver consistent performance, ensuring high production quality. The rings’ ability to maintain precise dimensions and alignment plays a critical role in achieving accurate results in manufacturing processes. This precision supports the production of components that meet stringent industry standards.
Reducing defects and waste
Solid SiC Focus Rings contribute to reducing defects and waste in production. Their consistent performance minimizes variations in manufacturing, leading to fewer errors and less material waste. By enhancing process reliability, these rings support sustainable production practices and help businesses achieve their efficiency goals.
Comparison with Other Materials
SiC vs. Graphite
Efficiency comparison
Silicon carbide (SiC) and graphite serve distinct roles in industrial applications, each offering unique advantages. Solid SiC Focus Rings excel in environments requiring high thermal performance and durability. Their superior thermal conductivity allows them to maintain stability under rapid temperature changes, making them ideal for semiconductor manufacturing. In contrast, graphite shines in ultra-high-temperature applications within controlled atmospheres. Its ability to withstand extreme heat without degrading makes it a preferred choice for specific niche applications. However, when considering overall efficiency in diverse production settings, SiC often outperforms graphite due to its robustness and versatility.
Cost-effectiveness
Cost considerations play a crucial role in material selection. Graphite generally presents a more cost-effective option due to its lower production costs. However, the initial savings may not translate into long-term benefits. Solid SiC Focus Rings offer extended service life and reduced maintenance needs, leading to significant cost savings over time. The durability and reduced frequency of replacements associated with SiC can offset its higher upfront cost, providing a more economical solution in the long run.
SiC vs. Alumina
Performance differences
When comparing SiC with alumina, notable performance differences emerge. SiC exhibits approximately 25% greater hardness than aluminum oxide, making it more suitable for applications involving harder materials. Its sharper grain structure enhances its cutting and grinding capabilities, providing superior performance in demanding environments. Alumina, while offering commendable thermal conductivity, falls short of SiC’s thermal performance. This makes SiC a preferred choice for applications requiring high thermal stability and mechanical strength.
Long-term benefits
The long-term benefits of using SiC over alumina become apparent in high-stress applications. SiC’s complex production process results in a material that withstands harsh conditions, offering unparalleled durability. Although alumina is generally more cost-effective initially, SiC’s extended lifespan and reduced maintenance requirements provide substantial long-term advantages. Businesses investing in Solid SiC Focus Rings benefit from enhanced operational efficiency and reduced total cost of ownership, making SiC a strategic choice for industries prioritizing longevity and reliability.
Case Studies/Examples of Solid SiC Focus Rings
Real-world Applications
Example from the semiconductor industry
In the semiconductor industry, the Solid SiC Focus Ring has become a pivotal component. Semicera, a leading manufacturer, has developed a cutting-edge focus ring designed to meet the rigorous demands of advanced semiconductor manufacturing. This innovation enhances the overall efficiency of etching processes, ensuring precision and reliability. By integrating these focus rings, semiconductor companies have reported significant improvements in production rates and product quality. The durability and thermal stability of silicon carbide allow these rings to withstand harsh plasma environments, reducing downtime and maintenance costs.
Success story in automotive manufacturing
The automotive industry also benefits from the application of Solid SiC Focus Rings. A notable success story involves a major automotive manufacturer that incorporated these rings into their power electronics production line. The result was a marked increase in efficiency and a reduction in production defects. The rings’ ability to handle high-power and high-frequency devices proved invaluable, leading to enhanced performance and reliability in the final products. This success underscores the versatility and effectiveness of SiC focus rings across different industrial sectors.
Measurable Improvements
Increased production rates
The implementation of Solid SiC Focus Rings has led to measurable improvements in production rates. Companies utilizing these rings have experienced a noticeable boost in their manufacturing throughput. The rings’ resistance to wear and tear minimizes interruptions, allowing for continuous operation and increased output. This improvement not only enhances productivity but also contributes to meeting growing market demands efficiently.
Enhanced product quality
Product quality has also seen significant enhancement with the use of Solid SiC Focus Rings. The precision and consistency provided by these rings ensure that manufacturing processes yield high-quality products with minimal defects. This consistency is crucial in maintaining competitive advantage and customer satisfaction. By reducing variability and waste, businesses can achieve higher manufacturing yields and deliver superior products to the market.
Solid SiC Focus Rings in Semiconductor Manufacturing
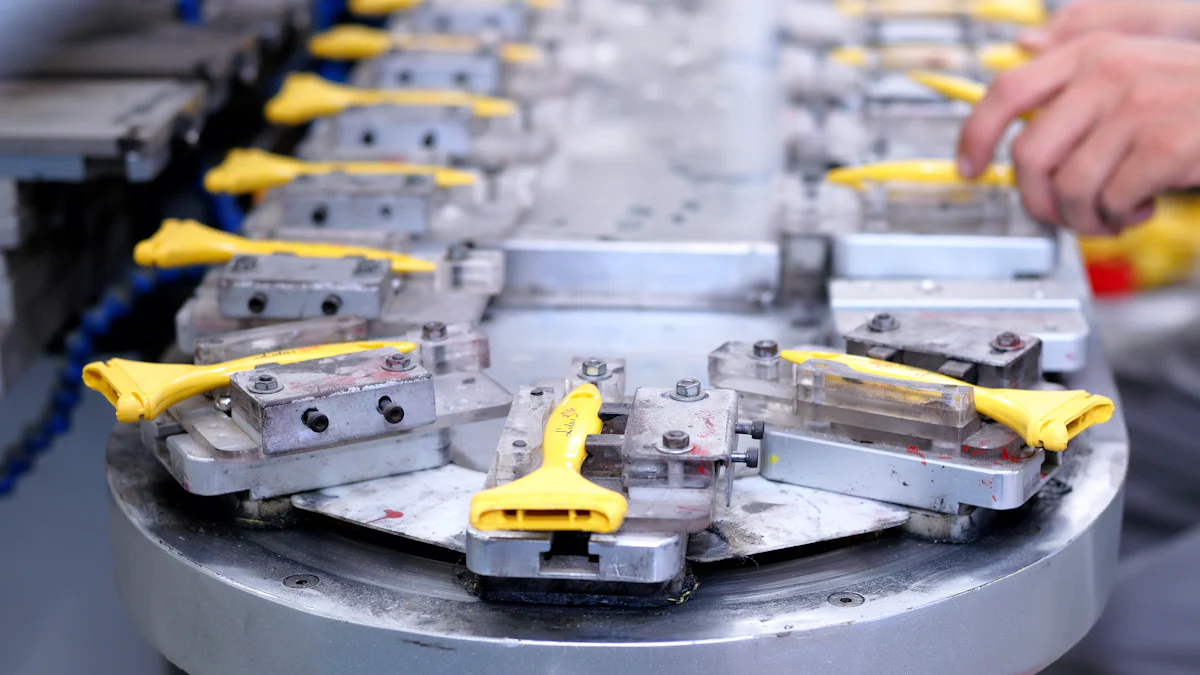
Erosion Resistance
Benefits in harsh plasma environments
Solid SiC Focus Rings play a pivotal role in semiconductor manufacturing, particularly in plasma etching processes. Their exceptional erosion resistance makes them indispensable in harsh plasma environments. Silicon carbide, the primary material of these rings, acts as a robust barrier, protecting the integrity of semiconductor chips during etching. This resistance to erosion ensures that the rings maintain their structural integrity, even under continuous exposure to aggressive plasma conditions. As a result, manufacturers experience fewer interruptions and longer equipment life, leading to enhanced production efficiency.
Scientific Research Findings: Studies highlight that manufacturers are investing in research and development to further enhance the properties of CVD SiC Focus Rings. These advancements aim to meet the evolving demands of the semiconductor industry, ensuring that the rings can withstand increasingly challenging conditions.
Electrical Properties
Ensuring plasma uniformity
The electrical properties of Solid SiC Focus Rings are crucial for maintaining plasma uniformity during semiconductor processing. Uniform plasma distribution is essential for achieving high precision in etching processes. Silicon carbide’s inherent electrical characteristics contribute to this uniformity, ensuring consistent etching results across the wafer. This precision is vital for producing semiconductor components that meet stringent industry standards.
Scientific Research Findings: Research indicates that silicon carbide focus rings play a critical role in plasma etching equipment. They ensure uniform plasma distribution, which is essential for maintaining high precision during the etching process. Continuous technological advancements aim to enhance the performance and durability of these rings, further solidifying their importance in semiconductor manufacturing.
Mechanical Strength of Solid SiC Focus Rings
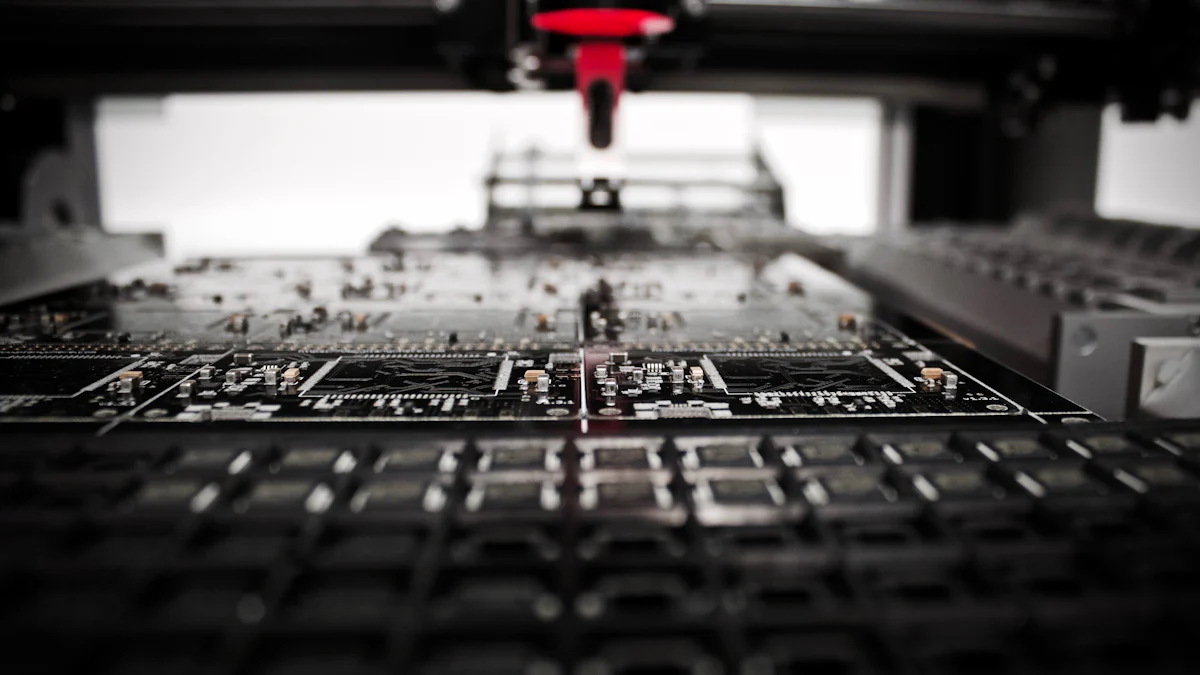
Withstanding High-Power Applications
Solid SiC Focus Rings demonstrate exceptional mechanical strength, making them ideal for high-power applications. Their robust construction allows them to endure the intense demands of semiconductor manufacturing processes. Silicon carbide, the primary material, provides superior hardness and resistance to mechanical stress. This strength ensures that the rings maintain their structural integrity even under continuous high-power operations. As a result, manufacturers experience reduced maintenance frequency, leading to fewer production interruptions and enhanced operational efficiency.
Stability Under Operational Conditions
Solid SiC Focus Rings offer remarkable stability under various operational conditions. Their high thermal conductivity and low thermal expansion coefficient make them highly resistant to thermal shock. These properties ensure that the rings perform consistently, even when exposed to rapid temperature fluctuations. The stability provided by silicon carbide minimizes the risk of thermal-induced failures, contributing to reliable and efficient manufacturing processes. This thermal resilience is crucial in maintaining the precision and quality of semiconductor components, ultimately boosting production efficiency.
Cost-Effectiveness of Solid SiC Focus Rings
Service Life Extension
Solid SiC Focus Rings offer a significant advantage in terms of service life extension. These rings can double the lifespan compared to conventional rings used in semiconductor manufacturing. The high-performance nature of silicon carbide, with its exceptional thermal stability and resistance to chemical corrosion, ensures that these rings maintain their integrity even in harsh plasma environments. This durability reduces the frequency of replacements, allowing businesses to operate more efficiently and with fewer interruptions.
Overall Cost Savings
The long-term financial benefits of using Solid SiC Focus Rings are substantial. Although the initial investment may be higher than other materials, the extended service life and reduced maintenance needs lead to significant cost savings over time. Businesses benefit from lower material costs and decreased labor expenses associated with frequent replacements. The robust nature of these rings ensures that they withstand the demands of advanced semiconductor manufacturing, enhancing overall operational efficiency and reducing the total cost of ownership.
Solid SiC Focus Rings have proven to be a game-changer in enhancing production efficiency across various industries. Their exceptional thermal and chemical stability, coupled with high mechanical strength, make them ideal for demanding environments like semiconductor manufacturing. These rings offer superior durability and resistance to plasma erosion, ensuring longer lifespans and reduced maintenance needs. By integrating Solid SiC Focus Rings, businesses can achieve significant cost savings and improved operational efficiency. The choice of SiC over traditional materials like quartz and alumina underscores its unmatched performance and reliability in harsh conditions.
FAQ
What are Solid SiC Focus Rings used for?
Solid SiC Focus Rings serve as critical components in semiconductor manufacturing. They play a vital role in processes like plasma etching and chemical vapor deposition. Their robust construction ensures they withstand harsh environments, maintaining the integrity of semiconductor equipment.
Why choose silicon carbide over other materials?
Silicon carbide offers superior thermal stability, mechanical strength, and resistance to chemical erosion. These properties make it ideal for demanding applications. Compared to materials like graphite and alumina, silicon carbide provides longer service life and enhanced performance.
How do Solid SiC Focus Rings improve production efficiency?
These rings reduce the frequency of replacements due to their durability. This minimizes downtime and maintenance costs. Their precision ensures consistent production quality, leading to fewer defects and higher manufacturing yields.
Are Solid SiC Focus Rings cost-effective?
Yes, they are. Although the initial investment may be higher, the extended lifespan and reduced maintenance needs result in significant cost savings over time. Businesses benefit from lower material and labor expenses.
Can Solid SiC Focus Rings withstand high temperatures?
Absolutely. Silicon carbide’s exceptional thermal stability allows these rings to perform consistently under extreme heat. This characteristic is crucial for industries where precise temperature control is essential for product quality.
What industries benefit from using Solid SiC Focus Rings?
Beyond semiconductors, industries like automotive, aerospace, and defense benefit from these rings. Their ability to handle high-power and high-frequency devices makes them valuable in power electronics and renewable energy systems.
How do Solid SiC Focus Rings contribute to product quality?
Their precision and consistency ensure high production quality. By maintaining precise dimensions and alignment, these rings support the production of components that meet stringent industry standards, reducing defects and waste.
What makes Solid SiC Focus Rings durable?
The construction from silicon carbide, known for its high mechanical strength, ensures these rings withstand demanding production environments. Unlike traditional materials, they maintain integrity even under continuous use.
How do Solid SiC Focus Rings enhance semiconductor manufacturing?
They offer exceptional erosion resistance in plasma environments, protecting semiconductor chips during etching. Their electrical properties ensure plasma uniformity, which is essential for achieving high precision in etching processes.
What are the long-term benefits of using Solid SiC Focus Rings?
Businesses experience enhanced operational efficiency and reduced total cost of ownership. The extended lifespan and reduced maintenance requirements provide substantial long-term advantages, making them a strategic choice for industries prioritizing longevity and reliability.