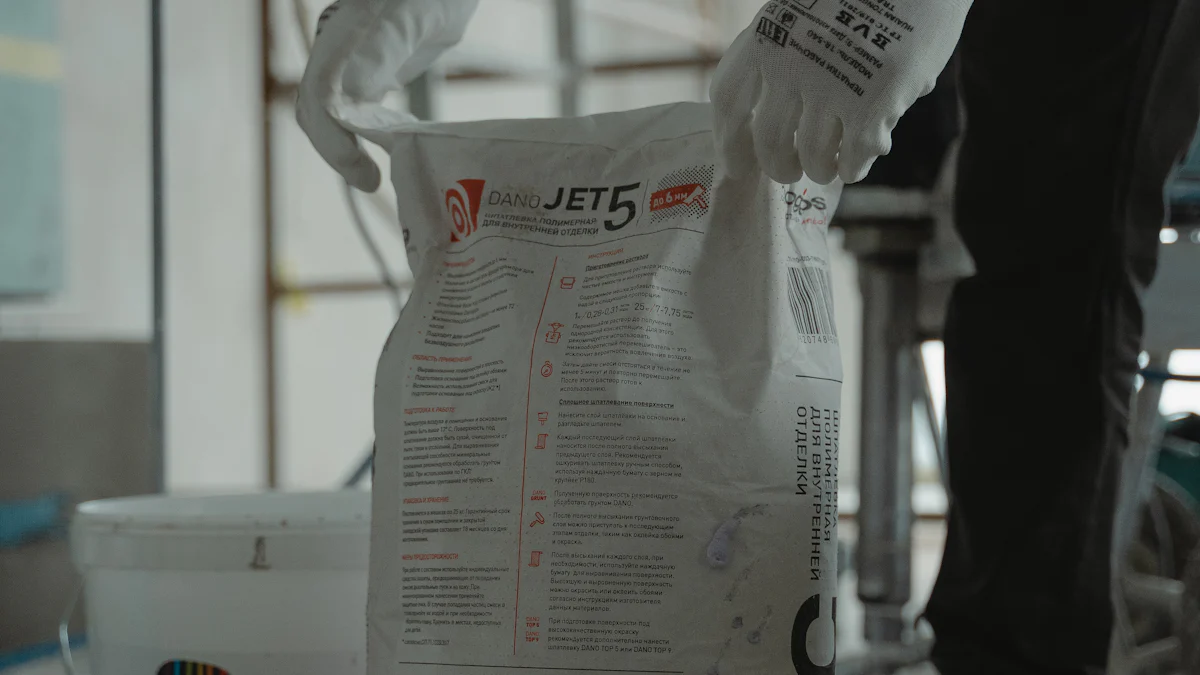
Tungsten carbide coating (TAC coating) plays a pivotal role in enhancing the durability and performance of materials. Its exceptional hardness and wear resistance make it indispensable for industries facing extreme conditions. By protecting components from abrasion, erosion, and corrosion, TAC coating significantly extends the lifespan of critical machinery. Industries such as aerospace, automotive, and manufacturing rely on this advanced coating to optimize performance and reduce maintenance costs. The ability to withstand harsh environments ensures that TAC coating remains a trusted solution for improving operational efficiency and reliability.
Key Takeaways
- Tungsten carbide coating (TAC coating) significantly enhances the durability and performance of materials, making it essential for industries facing extreme conditions.
- The coating’s exceptional hardness and wear resistance extend the lifespan of critical machinery, reducing maintenance costs and downtime.
- TAC coating can be customized to meet specific industrial needs, ensuring optimal performance in various applications, from aerospace to automotive.
- Advanced application methods like High Velocity Oxygen Fuel (HVOF) ensure a robust and uniform coating, enhancing adhesion and durability.
- By protecting against abrasion, erosion, and corrosion, TAC coating promotes operational efficiency and reliability in demanding environments.
- Investing in tungsten carbide coating not only saves costs but also supports environmental sustainability by reducing material waste and the carbon footprint.
What is tungsten carbide coating (TAC coating)?
Tungsten carbide coating, often referred to as TAC coating, is a specialized surface treatment designed to enhance the durability and performance of materials. This coating is widely recognized for its exceptional hardness and resistance to wear, making it an essential solution for industries that operate under extreme conditions. By forming a protective layer on components, TAC coating minimizes the effects of abrasion, erosion, and corrosion, ensuring prolonged operational efficiency.
Composition and properties of TAC coating
Tungsten carbide coating primarily consists of tungsten carbide particles, which are known for their remarkable hardness—nearly twice as hard as steel. These particles are often combined with a binder material, such as cobalt or nickel, to improve adhesion and toughness. The resulting composite delivers a unique combination of strength and resilience, making it suitable for demanding applications.
The properties of TAC coating can be tailored to meet specific requirements. For instance, the high velocity oxygen fuel (HVOF) process allows manufacturers to adjust the volume fraction and grain size of the coating. This customization ensures optimal performance, whether the goal is to increase hardness, enhance corrosion resistance, or improve overall durability. Additionally, the coating exhibits excellent thermal stability, maintaining its integrity even under high temperatures.
Key characteristics of TAC coating
TAC coating offers several key characteristics that make it indispensable in industrial applications:
- Exceptional Hardness: The coating provides a hard surface that resists wear and abrasion, extending the lifespan of critical components.
- Superior Wear Resistance: It protects against fretting, galling, and particle erosion, ensuring reliable performance in harsh environments.
- Corrosion Resistance: The coating shields substrates from chemical damage, making it ideal for corrosive settings.
- Thermal Stability: With a maximum temperature rating of approximately 730°F (400°C), TAC coating performs well in high-temperature applications.
- Customizability: Manufacturers can tailor the coating’s properties to suit specific industrial needs, enhancing its versatility.
These characteristics make TAC coating a preferred choice for industries such as aerospace, automotive, and manufacturing. Its ability to withstand extreme conditions while maintaining structural integrity ensures consistent performance and reduced maintenance costs.
How is tungsten carbide coating applied?
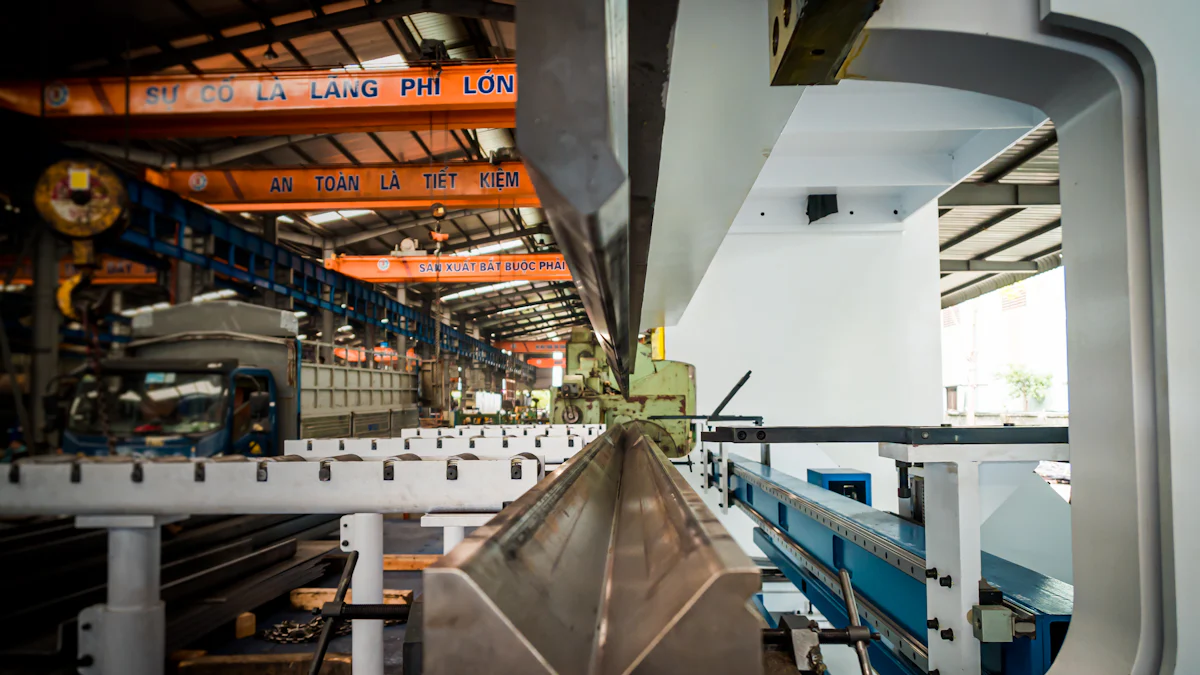
Tungsten carbide coating application involves advanced techniques to ensure optimal performance and durability. The process requires precision and expertise to achieve a uniform and robust layer on the substrate. Industries rely on specific methods to meet the demands of various applications.
Common application methods
Several methods are used to apply tungsten carbide coating, each offering unique advantages. The most widely adopted techniques include:
- Thermal Spraying: This method involves heating tungsten carbide particles and propelling them onto the surface at high velocity. It ensures strong adhesion and a dense coating layer.
- High Velocity Oxygen Fuel (HVOF): HVOF is a popular thermal spray technique. It uses a combustion process to accelerate tungsten carbide particles, creating a coating with superior hardness and wear resistance.
- Plasma Spraying: Plasma spraying utilizes a high-temperature plasma jet to melt and deposit the coating material. It is suitable for applications requiring thick coatings.
- Cold Spraying: This method applies tungsten carbide particles at supersonic speeds without melting them. It produces a coating with minimal thermal stress, preserving the substrate’s properties.
Each method is chosen based on the specific requirements of the application, such as desired coating thickness, surface finish, and operating conditions.
Steps in the coating process
The application of tungsten carbide coating follows a systematic process to ensure consistency and quality. The key steps include:
- Surface Preparation: The substrate undergoes cleaning and roughening to enhance adhesion. Techniques like grit blasting remove contaminants and create a textured surface.
- Coating Material Selection: The appropriate tungsten carbide composition is selected based on the application’s needs. Factors like hardness, corrosion resistance, and thermal stability influence this choice.
- Application: The chosen method, such as HVOF or plasma spraying, is used to apply the coating. Operators control parameters like temperature, velocity, and spray distance to achieve the desired properties.
- Post-Coating Treatment: After application, the coated surface may undergo finishing processes like grinding or polishing. These steps improve surface smoothness and ensure dimensional accuracy.
- Quality Inspection: The final step involves inspecting the coating for defects, thickness uniformity, and adhesion strength. Non-destructive testing methods verify the coating’s integrity.
This structured approach guarantees that the tungsten carbide coating meets industry standards and performs effectively in demanding environments.
Applications of tungsten carbide coating across industries
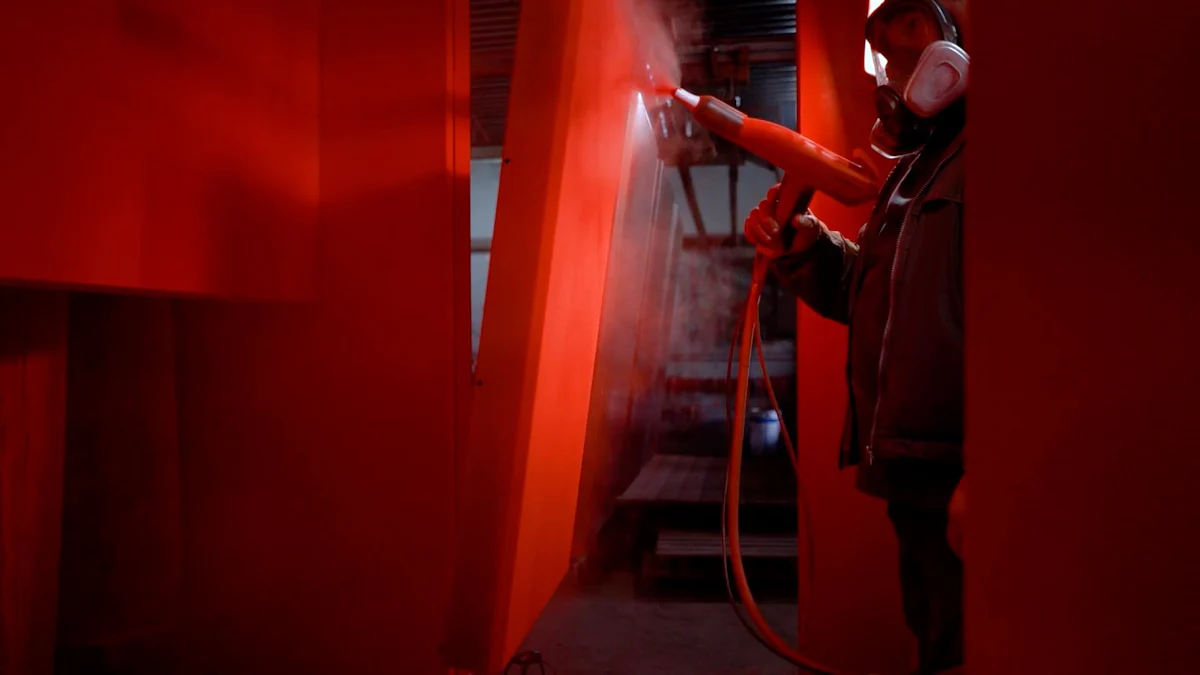
Tungsten carbide coating has become a cornerstone in various industries due to its exceptional durability, wear resistance, and ability to withstand extreme conditions. Its versatility allows it to address specific challenges in sectors such as aerospace, automotive, and manufacturing, ensuring enhanced performance and prolonged equipment lifespan.
Aerospace applications
The aerospace industry demands materials that can endure high temperatures, friction, and wear. Tungsten carbide coating meets these requirements by providing thermal protection and reducing friction in critical components like turbine engines and landing gear. Its corrosion resistance also ensures the longevity of parts exposed to harsh environmental conditions, such as saltwater or extreme altitudes.
For instance, tungsten carbide coatings offer 14 times more corrosion resistance than stainless steel, significantly extending the service life of turbine engine components.
In addition, the coating enhances the durability of aviation tools and equipment, minimizing wear and tear during operation. This reliability makes it an essential solution for maintaining the safety and efficiency of aircraft systems.
Automotive applications
In the automotive sector, tungsten carbide coating plays a vital role in improving the performance and durability of vehicle components. It is commonly applied to engine parts, fuel injection systems, and braking mechanisms to reduce wear and enhance operational efficiency. The coating’s hardness and abrasion resistance ensure that these components can withstand the constant friction and stress experienced during vehicle operation.
By extending the lifespan of critical parts, tungsten carbide coating reduces maintenance costs and downtime for automotive manufacturers and users. Its ability to perform under high temperatures and corrosive environments further solidifies its importance in modern automotive engineering.
Manufacturing and heavy machinery applications
Manufacturing and heavy machinery industries rely on tungsten carbide coating to protect tools and equipment from wear and damage. The coating is frequently applied to cutting tools, molds, and dies to improve their precision and durability. Its hardness allows these tools to maintain sharp edges and resist deformation, even under intense pressure.
In heavy machinery, tungsten carbide coating enhances the performance of components such as rollers, gears, and bearings. These parts often operate in abrasive environments, where uncoated surfaces would quickly degrade. The coating ensures consistent performance and reduces the need for frequent replacements, leading to increased productivity and cost savings.
As a result, industries such as metallurgy, mining, and oil drilling have adopted tungsten carbide coating to optimize their operations and extend the lifespan of critical equipment.
Benefits of tungsten carbide coating
Durability and wear resistance
Tungsten carbide coating provides unmatched durability, making it a preferred choice for industries requiring long-lasting solutions. Its exceptional hardness, nearly twice that of steel, ensures superior resistance to wear and abrasion. This coating protects components from fretting, galling, and particle erosion, even in extreme environments. By forming a robust barrier, it prevents damage caused by dynamic contact with hard surfaces or abrasive grains.
The coating’s ability to endure harsh conditions significantly extends the lifespan of critical machinery. For example, components like exhaust fans, conveyor screws, and steel rolls benefit from years of added durability when coated with tungsten carbide. This resilience reduces the frequency of replacements, ensuring consistent performance and minimizing operational disruptions.
Cost-effectiveness and operational efficiency
Tungsten carbide coating offers substantial cost savings by reducing maintenance and replacement expenses. Its wear-resistant properties lower the likelihood of component failure, which translates to fewer repairs and less downtime. Industries relying on heavy machinery or high-performance tools experience enhanced productivity due to the coating’s ability to maintain equipment functionality over extended periods.
The High Velocity Oxygen Fuel (HVOF) application process further enhances the coating’s cost-effectiveness. This method produces a dense layer with low porosity and high bond strength, ensuring long-term adhesion to substrates. The result is a reliable coating that withstands demanding conditions without frequent reapplication. By investing in tungsten carbide coating, businesses achieve operational efficiency while optimizing their resources.
Environmental advantages
Tungsten carbide coating contributes to environmental sustainability by promoting resource conservation. Its durability reduces the need for frequent replacements, which minimizes material waste. Industries benefit from longer-lasting components, leading to a decrease in the consumption of raw materials and energy required for manufacturing new parts.
The coating’s ability to protect against corrosion also reduces the environmental impact of chemical degradation. Components exposed to corrosive environments, such as saltwater or industrial chemicals, maintain their integrity for longer periods. This protection prevents the release of harmful substances into the environment, supporting eco-friendly practices.
Additionally, the extended lifespan of coated components reduces the carbon footprint associated with production and transportation. By choosing tungsten carbide coating, industries align with sustainable goals while maintaining high-performance standards.
Tungsten carbide coating stands as a vital innovation for enhancing material performance and extending component longevity. Its exceptional durability, wear resistance, and adaptability make it indispensable across industries such as aerospace, automotive, and manufacturing. By addressing challenges like abrasion, corrosion, and extreme conditions, this coating optimizes operational efficiency and reduces maintenance costs.
“Tungsten carbide coatings provide essential durability and protection for equipment exposed to harsh conditions,” according to Industry Experts.
Industries seeking tailored solutions can explore tungsten carbide coating applications or consult specialists to unlock its full potential. This advanced coating ensures reliability and sustainability, meeting the demands of modern industrial environments.