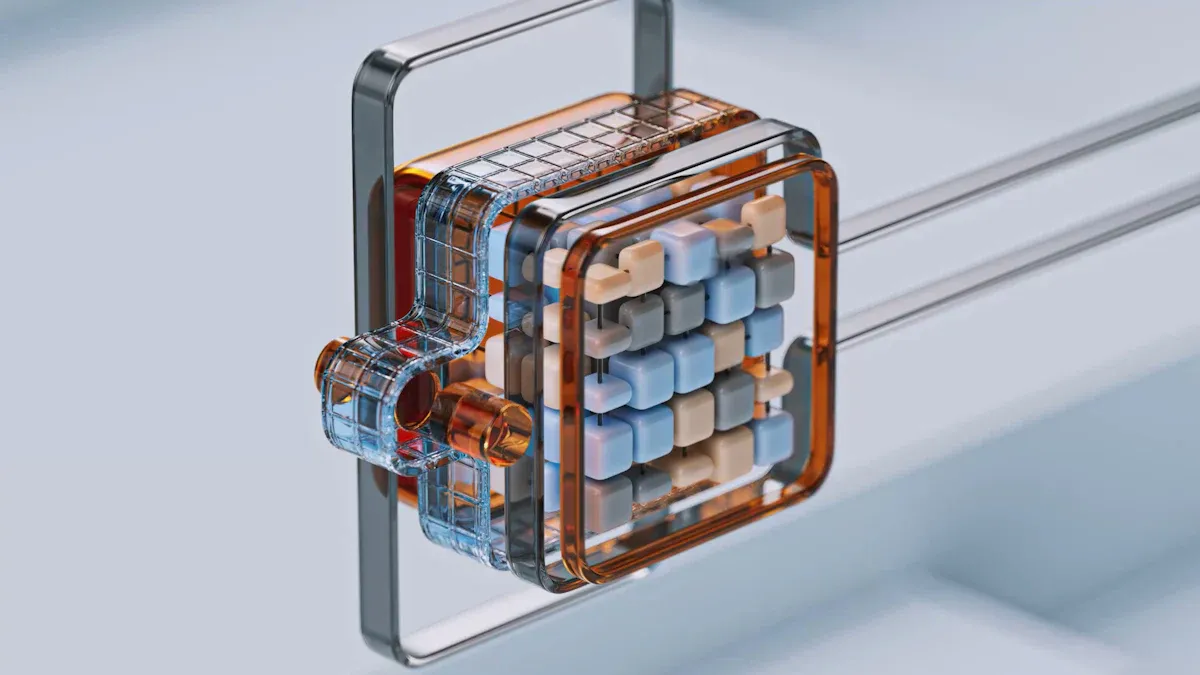
Fuel cell technology depends on durable components to ensure long-term performance. CVD SiC coating plays a vital role in protecting fuel cell stacks from damage. Its exceptional properties, such as corrosion resistance and thermal stability, make it indispensable in harsh operating conditions. This advanced CVD SiC coating technology forms a strong barrier against chemical degradation, extending the lifespan of critical components. Industries, including semiconductor equipment manufacturing, rely on SiC coating to maintain efficiency and reliability. The incorporation of corrosion resistance CVD SiC coating into fuel cells significantly enhances the durability of hydrogen energy systems.
Key Takeaways
- CVD SiC coatings keep fuel cell parts safe from damage and heat, making them last longer.
- These coatings handle very high heat, over 1600°C, and work well in tough conditions.
- Using CVD SiC coatings lowers repair costs and helps fuel cells work for a longer time, saving money.
- CVD SiC coatings help the environment by cutting waste and using fewer materials to make fuel cells.
- Adding CVD SiC coatings helps hydrogen energy systems grow, making them better and more dependable.
CVD SiC Coating Technology Overview
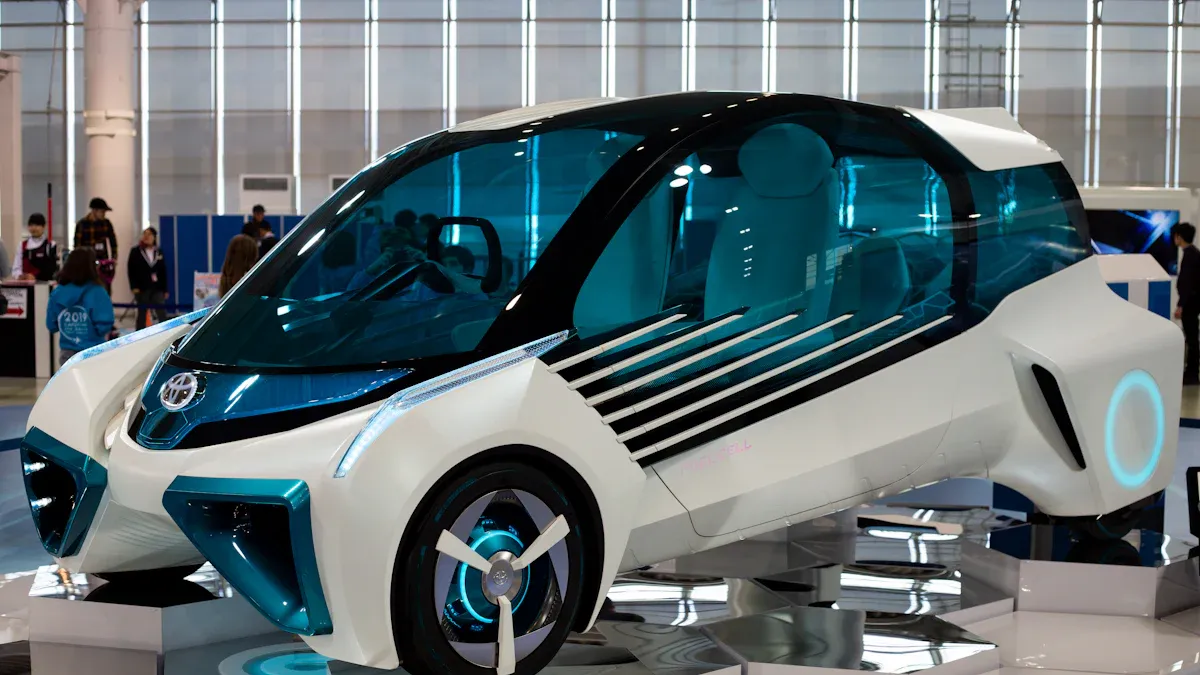
Defining CVD SiC Coating
CVD SiC coating refers to a thin layer of silicon carbide deposited on a substrate using chemical vapor deposition (CVD). This advanced coating technology creates a uniform and durable barrier that protects materials from harsh environments. Industries value CVD SiC coating for its ability to enhance the performance and longevity of components exposed to extreme conditions.
Key Properties of CVD SiC Coatings
CVD SiC coatings exhibit exceptional physical and chemical properties, making them ideal for demanding applications. These properties include high hardness, excellent modulus, and superior resistance to corrosion. The table below highlights some key characteristics:
Property | Value |
---|---|
Hardness | 46.8 GPa |
Modulus | 416.3 GPa |
Friction Coefficient | 1.47 |
Anti-Acid Corrosion Weight Loss | 0.26% (vs. 0.39%) after 8h |
These attributes ensure that CVD SiC coatings provide robust protection against mechanical wear, chemical degradation, and environmental stress.
Application Process of CVD SiC Coatings
The application of CVD SiC coatings involves a precise and controlled process. Chemical vapor deposition relies on high temperatures to decompose precursor gases, which then react and form a silicon carbide layer on the substrate. The following table outlines the critical parameters involved in this process:
Parameter | Description |
---|---|
Deposition Temperature | High temperatures are required for the decomposition of precursor gases. |
Gas Flow Rate | Controls the amount of precursor gases introduced into the reaction chamber. |
Deposition Pressure | Influences the reaction kinetics and coating uniformity. |
Deposition Time | Affects the thickness and quality of the coating produced. |
Coating Properties | Includes thickness, stoichiometry, grain size, crystal structure, and orientation. |
This meticulous process ensures that the CVD SiC coating adheres uniformly to the substrate, delivering consistent performance and durability.
Durability Challenges in Fuel Cell Stacks
Fuel cell stacks face several durability challenges that can limit their efficiency and lifespan. These challenges arise from the harsh operating conditions within fuel cells, including exposure to high temperatures, corrosive environments, and mechanical stress. Addressing these issues is essential for improving the reliability of hydrogen energy systems.
Corrosion and Material Degradation
Corrosion is a significant issue in fuel cell stacks, particularly in the gas diffusion layer (GDL) and other critical components. Over time, exposure to reactive gases and moisture leads to material degradation. Studies have quantified this degradation, showing that 6.32% of the pristine GDL sample and 10.12% of the aged GDL sample are prone to breakthroughs. The volume of these breakthrough regions increases from 774,200 µm³ in pristine samples to 1,239,700 µm³ in aged samples. This data highlights the need for protective measures, such as CVD SiC coating, to prevent corrosion and extend component life.
Thermal Stress and Mechanical Wear
Fuel cells operate under fluctuating temperatures, which cause thermal stress and mechanical wear. Rapid heating and cooling cycles can lead to material fatigue, cracking, and eventual failure. Research efforts have simulated these conditions to better understand their impact. For example, Bloom et al. in 2011 used square wave cycles to replicate vehicle idling and full-power conditions. Similarly, the Giantleap project in 2017 conducted accelerated tests by managing loading and unloading times. These studies emphasize the importance of materials that can withstand thermal stress without compromising performance.
Chemical Instability in Harsh Environments
Fuel cells often operate in chemically reactive environments, where exposure to acidic or alkaline substances can degrade materials. This chemical instability reduces the efficiency and durability of the stack. In 2018, researchers from Wuhan University developed a comprehensive test cycle to evaluate the effects of various operational conditions, including open-circuit voltage and overload. Their findings underscore the need for coatings that provide chemical resistance. By forming a robust barrier, CVD SiC coating protects components from chemical attack, ensuring long-term stability.
Role of CVD SiC Coatings in Addressing Durability Issues
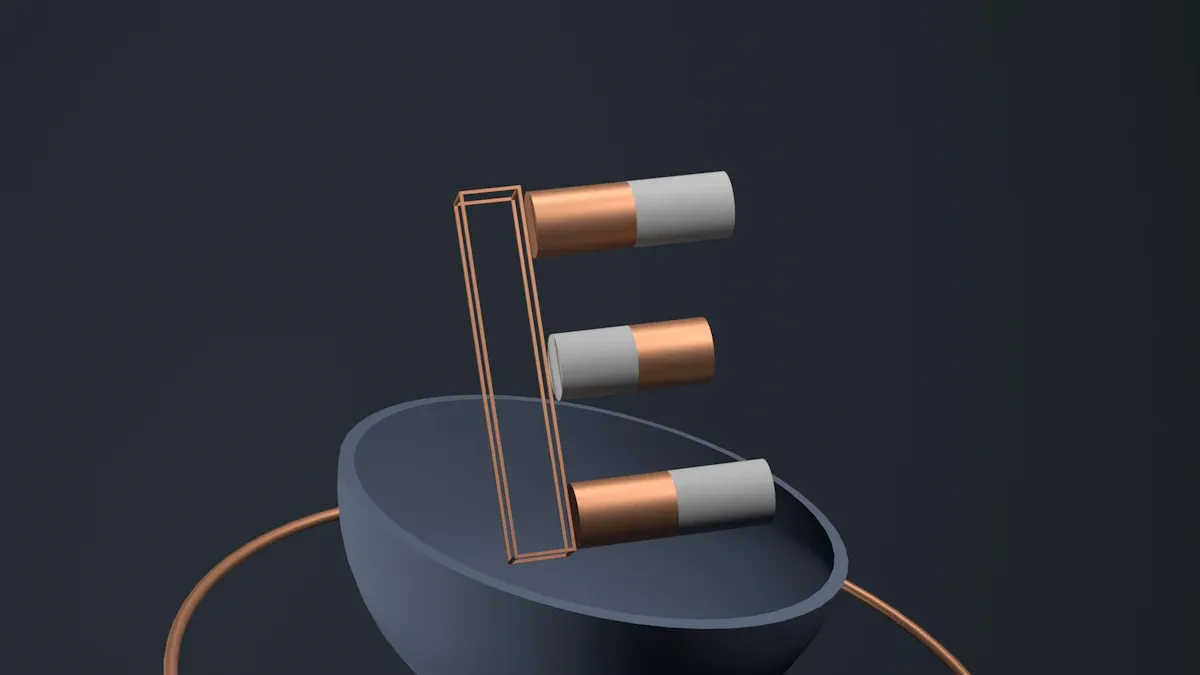
Corrosion Resistance and Oxidation Protection
Corrosion poses a significant threat to the longevity of fuel cell components. Reactive gases and moisture often accelerate material degradation, leading to reduced efficiency. CVD SiC coating provides a robust solution by forming a protective barrier against corrosive elements. Its dense and uniform structure prevents the penetration of moisture and reactive gases, safeguarding critical components. This protection ensures that materials maintain their structural integrity over extended periods.
Oxidation is another challenge in fuel cell environments. High temperatures and reactive oxygen species can cause severe damage to unprotected materials. CVD SiC coating resists oxidation effectively, even under extreme conditions. By minimizing oxidation, the coating extends the operational life of fuel cell components, reducing the need for frequent replacements.
Thermal Stability at High Temperatures
Fuel cells operate at elevated temperatures, which can cause thermal stress and material deformation. CVD SiC coating demonstrates exceptional thermal stability, making it ideal for such demanding conditions. Its ability to withstand oxidation at temperatures exceeding 1600°C ensures reliable performance in high-temperature environments.
The table below highlights the thermal stability and related properties of CVD SiC coatings:
Aspect | Detail |
---|---|
High Temperature Resistance | Coating withstands oxidation at temperatures exceeding 1600°C. |
Chemical Corrosion Resistance | Coating prevents reactions with process gases, reducing contamination risks. |
Structural Stability | Compatibility of thermal expansion coefficients minimizes deformation and cracking. |
Service Life | Extends the lifespan of carriers to over three times that of standard graphite carriers. |
The compatibility of thermal expansion coefficients between the coating and substrate further enhances its durability. This compatibility reduces the risk of cracking or delamination during temperature fluctuations. As a result, CVD SiC coating ensures consistent performance and reliability in fuel cell applications.
Chemical Resistance in Reactive Environments
Fuel cells often operate in chemically reactive environments, exposing components to acidic or alkaline substances. These harsh conditions can degrade unprotected materials, compromising the efficiency and durability of the system. CVD SiC coating offers superior chemical resistance, acting as a shield against corrosive agents. Its inert nature prevents reactions with process gases, reducing contamination risks and maintaining the purity of the fuel cell environment.
The coating’s chemical resistance also minimizes material wear caused by prolonged exposure to reactive substances. This protection ensures that components retain their functionality and structural integrity, even in the most challenging conditions. By enhancing chemical stability, CVD SiC coating contributes to the long-term reliability of fuel cell systems.
Case Studies: Applications of CVD SiC Coatings in Fuel Cells
Real-world applications of CVD SiC coatings in fuel cells demonstrate their effectiveness in enhancing durability and performance. These case studies highlight how industries have successfully utilized this advanced coating technology to address critical challenges.
- Protecting Bipolar Plates in PEM Fuel Cells
Bipolar plates are essential components in proton exchange membrane (PEM) fuel cells. They facilitate the flow of gases and electrons while maintaining structural integrity. However, exposure to acidic environments and high temperatures often leads to corrosion and material degradation. Manufacturers have applied CVD SiC coatings to bipolar plates to create a robust protective layer. This coating prevents chemical reactions with the environment, ensuring long-term stability. Studies have shown that coated plates exhibit significantly reduced weight loss and improved electrical conductivity compared to uncoated ones. - Enhancing Durability of Gas Diffusion Layers (GDLs)
Gas diffusion layers play a critical role in distributing reactant gases evenly across the fuel cell. Over time, these layers face wear and tear due to mechanical stress and exposure to reactive substances. By applying CVD SiC coatings, researchers have enhanced the mechanical strength and chemical resistance of GDLs. For instance, a study conducted in a high-humidity environment revealed that coated GDLs maintained their structural integrity and performance for over 1,000 operational cycles. This improvement translates to longer service life and reduced maintenance costs. - Improving Performance in Solid Oxide Fuel Cells (SOFCs)
Solid oxide fuel cells operate at extremely high temperatures, often exceeding 800°C. These conditions can cause thermal stress and oxidation in critical components. CVD SiC coatings have been used to protect interconnects and other parts in SOFCs. The coating’s exceptional thermal stability and oxidation resistance ensure reliable performance under such demanding conditions. Field tests have demonstrated that coated components experience minimal degradation, even after prolonged exposure to high temperatures. - Applications in Automotive Fuel Cells
Automotive fuel cells require materials that can withstand rapid temperature changes and mechanical vibrations. CVD SiC coatings have been applied to various components in automotive fuel cells to enhance their durability. For example, a leading automotive manufacturer reported a 30% increase in the lifespan of coated components compared to uncoated ones. This advancement has contributed to the development of more reliable and efficient hydrogen-powered vehicles.
Note: These case studies underscore the versatility and effectiveness of CVD SiC coatings in addressing diverse challenges across different fuel cell types. By providing superior protection against corrosion, thermal stress, and chemical degradation, this technology plays a pivotal role in advancing fuel cell applications.
Broader Impacts of Enhanced Fuel Cell Longevity
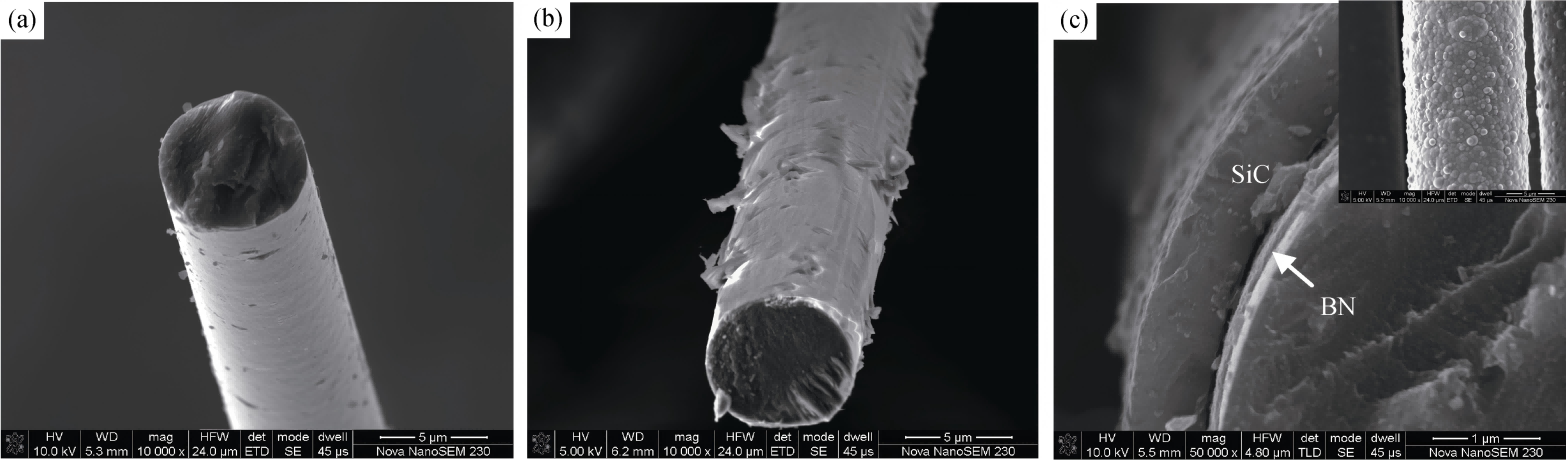
Cost Savings and Reduced Maintenance
Enhanced fuel cell longevity directly translates to significant cost savings and reduced maintenance requirements. Prolonging the lifespan of fuel cells minimizes the frequency of replacements, which lowers operational expenses. Additionally, durable components reduce the need for frequent repairs, saving both time and resources.
Economic analyses have highlighted these benefits. For instance, Schmuch et al. (2018) discussed the cost-performance balance of materials in energy systems, emphasizing potential savings in fuel cell applications. Similarly, Cullen et al. (2021) explored the advantages of fuel cells in heavy-duty transportation, noting reduced maintenance costs as a key benefit. The table below summarizes findings from various studies:
Study | Findings |
---|---|
Schmuch et al. (2018) | Performance and cost of materials indicate potential savings in fuel cell applications. |
Cullen et al. (2021) | Maintenance benefits highlighted for heavy-duty transportation fuel cells. |
Teichert et al. (2023) | Techno-economic assessments show cost-performance trade-offs in energy systems. |
Günter & Wassiliadis (2022) | Analysis of lithium-ion cells provides insights into fuel cell longevity and maintenance. |
Ank et al. (2023) | Characterization of Tesla 4680 cells contributes to understanding economic implications. |
These findings underscore the economic advantages of durable fuel cells, making them a cost-effective solution for various industries.
Environmental Benefits of Prolonged Fuel Cell Life
Extending the lifespan of fuel cells also benefits the environment. Longer-lasting fuel cells reduce the demand for raw materials, which decreases the environmental impact of mining and manufacturing processes. Additionally, fewer replacements mean less waste, contributing to a more sustainable energy ecosystem.
Durable fuel cells also enhance the efficiency of hydrogen energy systems. By maintaining optimal performance over time, they reduce energy losses and emissions associated with inefficiencies. This aligns with global efforts to transition to cleaner energy sources and combat climate change. Prolonged fuel cell life supports these goals by minimizing the carbon footprint of hydrogen energy systems.
Advancing Hydrogen Energy Adoption
Improving the durability of fuel cells plays a crucial role in advancing the adoption of hydrogen energy. Reliable and long-lasting fuel cells address key concerns about economic viability and dependability, making hydrogen energy more attractive to industries and consumers.
Research highlights the importance of durability in overcoming technological barriers. Catalyst and membrane degradation significantly impact fuel cell performance and lifespan. Addressing these issues through innovations like CVD SiC coating ensures that fuel cells remain efficient and reliable. Market analyses reveal that advancements in fuel cell technology are expanding their application range, making hydrogen energy competitive with traditional power sources.
For example, new hydrogen fuel cells now exceed the efficiency of diesel engines, demonstrating their potential to replace conventional energy systems. These innovations not only improve performance but also build confidence in hydrogen energy as a sustainable and practical solution. By enhancing fuel cell longevity, industries can accelerate the transition to a hydrogen-powered future.
CVD SiC coatings play a transformative role in enhancing the durability of fuel cell stacks. By addressing challenges like corrosion, thermal stress, and chemical degradation, these coatings ensure long-lasting and efficient performance.
Broader Benefits:
- Reduced maintenance costs and extended component life.
- Lower environmental impact through minimized waste.
- Accelerated adoption of hydrogen energy systems.
Continued innovation in coating technologies remains essential. Advancing these solutions will support the global transition to sustainable energy, paving the way for a cleaner and more efficient future.
FAQ
What is the primary purpose of CVD SiC coatings in fuel cells?
CVD SiC coatings protect fuel cell components from corrosion, thermal stress, and chemical degradation. These coatings enhance durability and ensure long-term performance in harsh operating conditions.
How does CVD SiC coating improve thermal stability?
CVD SiC coatings withstand high temperatures, exceeding 1600°C, without degrading. Their compatibility with substrate materials minimizes cracking and deformation during temperature fluctuations.
Are CVD SiC coatings environmentally friendly?
Yes, CVD SiC coatings extend the lifespan of fuel cells, reducing waste and the need for frequent replacements. This contributes to a more sustainable energy ecosystem by lowering material consumption and environmental impact.
Can CVD SiC coatings be applied to all fuel cell types?
CVD SiC coatings are versatile and suitable for various fuel cell types, including PEM and solid oxide fuel cells. Their properties make them effective in diverse applications, from automotive to industrial systems.
What industries benefit most from CVD SiC coatings?
Industries like hydrogen energy, automotive, and semiconductor manufacturing benefit significantly. These coatings enhance component reliability, reduce maintenance costs, and support advanced technological applications.
Tip: For more information on CVD SiC coatings, contact Semicera at sales01@semi-cera.com or sales05@semi-cera.com.