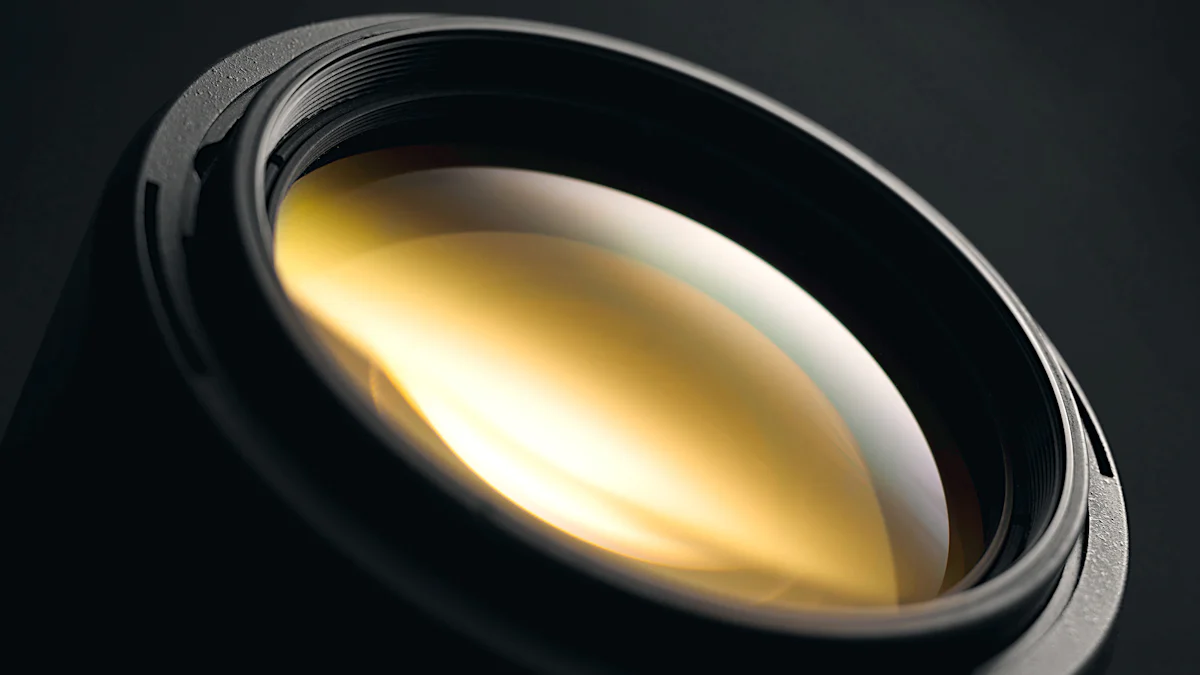
Chemical Vapor Deposition (CVD) represents a pivotal advancement in coating technology. This process involves depositing a solid material from a gaseous phase, creating high-quality coatings with exceptional adhesion and uniformity. CVD coatings find applications across various industries due to their ability to enhance product durability and performance. The global market for CVD coating technology was valued at approximately 7.5billionin2023,withprojectionsindicatinggrowthto7.5 billion in 2023, with projections indicating growth to 7.5billionin2023,withprojectionsindicatinggrowthto12.4 billion by 2032. This surge reflects the increasing demand for advanced coatings that offer superior wear resistance and thermal stability.
Key Takeaways
- CVD technology is essential for creating high-quality coatings that enhance durability and performance across various industries.
- The CVD process involves transforming gaseous precursors into solid coatings through chemical reactions, requiring precise temperature control for optimal results.
- CVD excels in coating complex shapes, making it invaluable in fields like electronics and aerospace where uniformity and precision are critical.
- Industries benefit from CVD coatings’ versatility, as they can be applied to a wide range of materials, including metals, ceramics, and glass.
- While CVD offers significant advantages, such as high-quality coatings, it also presents challenges like hazardous by-products and high operational costs that must be managed.
- Choosing between CVD and other coating technologies, like PVD or electroplating, depends on specific application needs, including temperature sensitivity and desired coating properties.
- Implementing CVD technology can lead to improved product reliability and longevity, making it a worthwhile investment for industries focused on performance.
How CVD Coating Technology Works
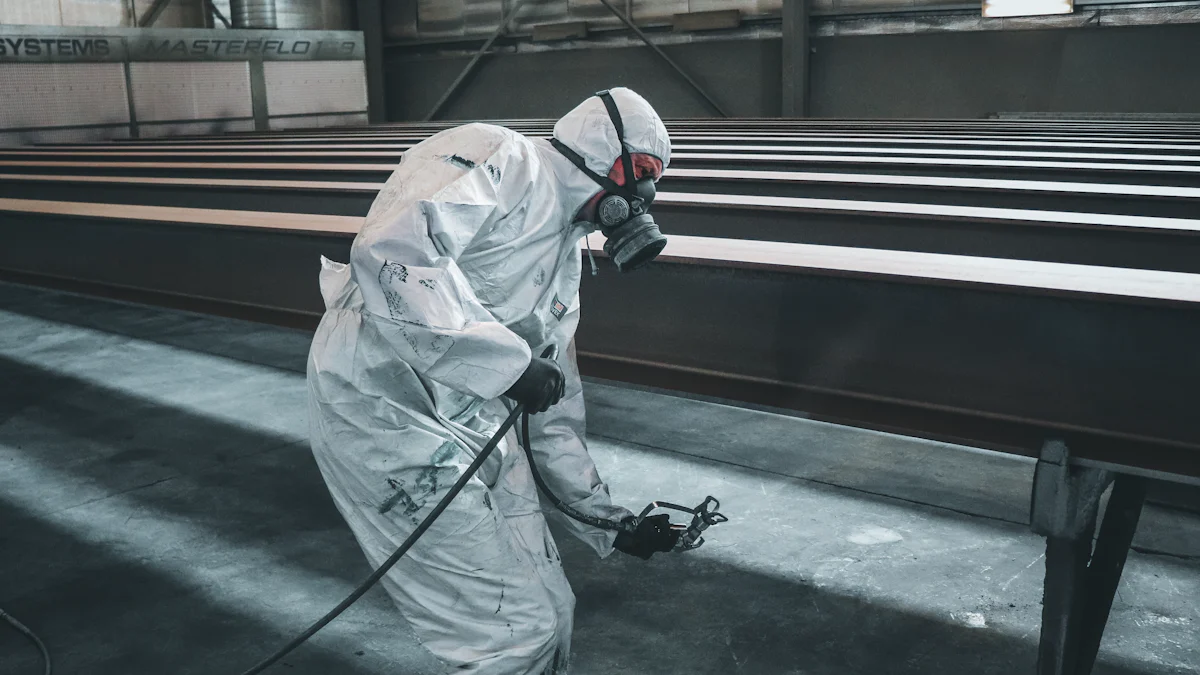
The CVD Process
Chemical Vapor Deposition (CVD) involves a series of intricate steps that transform gaseous precursors into a solid coating on a substrate. This process begins with the introduction of volatile precursor gases into a reaction chamber. These gases undergo chemical reactions, often involving decomposition or combination, to form a solid material that adheres to the substrate surface.
Chemical Reactions Involved
The chemical reactions in CVD are crucial for forming a strong bond between the coating and the substrate. These reactions typically occur at elevated temperatures, which facilitate the breakdown of precursor gases into reactive species. These species then interact with the substrate, depositing a thin film layer by layer. The ability to customize precursor gases allows for the creation of coatings with specific properties, enhancing the versatility of CVD technology.
Equipment Used in CVD
CVD requires specialized equipment to ensure precise control over the deposition process. Key components include a reaction chamber, gas delivery system, and temperature control mechanisms. The reaction chamber maintains the necessary environment for the chemical reactions, while the gas delivery system introduces the precursor gases at controlled rates. Temperature control is vital, as it influences the reaction kinetics and, consequently, the quality of the cvd coating.
Importance of Reaction Temperature
Temperature plays a pivotal role in the CVD process, affecting both the rate of chemical reactions and the properties of the resulting coating.
Effects on Coating Quality
The reaction temperature directly impacts the quality of the cvd coating. Higher temperatures generally enhance the reaction rate, leading to more uniform and dense coatings. However, excessively high temperatures can cause unwanted side reactions or damage to the substrate. Therefore, maintaining an optimal temperature range is essential for achieving high-quality coatings.
Temperature Control Mechanisms
To ensure precise temperature control, CVD systems employ advanced mechanisms such as thermocouples and heating elements. These devices monitor and adjust the temperature within the reaction chamber, maintaining the conditions necessary for consistent coating deposition. Effective temperature control not only improves coating quality but also enhances the overall efficiency of the CVD process.
Coating Complex Shapes
CVD technology excels in coating complex shapes, a capability that sets it apart from other deposition methods.
Techniques for Uniform Coating
Achieving uniform coatings on intricate geometries requires careful management of gas flow and reaction conditions. Techniques such as rotating the substrate or using multiple gas inlets help distribute the precursor gases evenly across the surface. This ensures that even the most complex shapes receive a consistent and high-quality cvd coating.
Challenges and Solutions
Coating complex shapes presents challenges, such as ensuring complete coverage and avoiding shadowing effects. Solutions include optimizing the gas flow dynamics and adjusting the reaction parameters to accommodate the specific geometry of the substrate. By addressing these challenges, CVD technology can produce coatings that enhance the performance and durability of components across various industries.
Applications of CVD in Various Industries
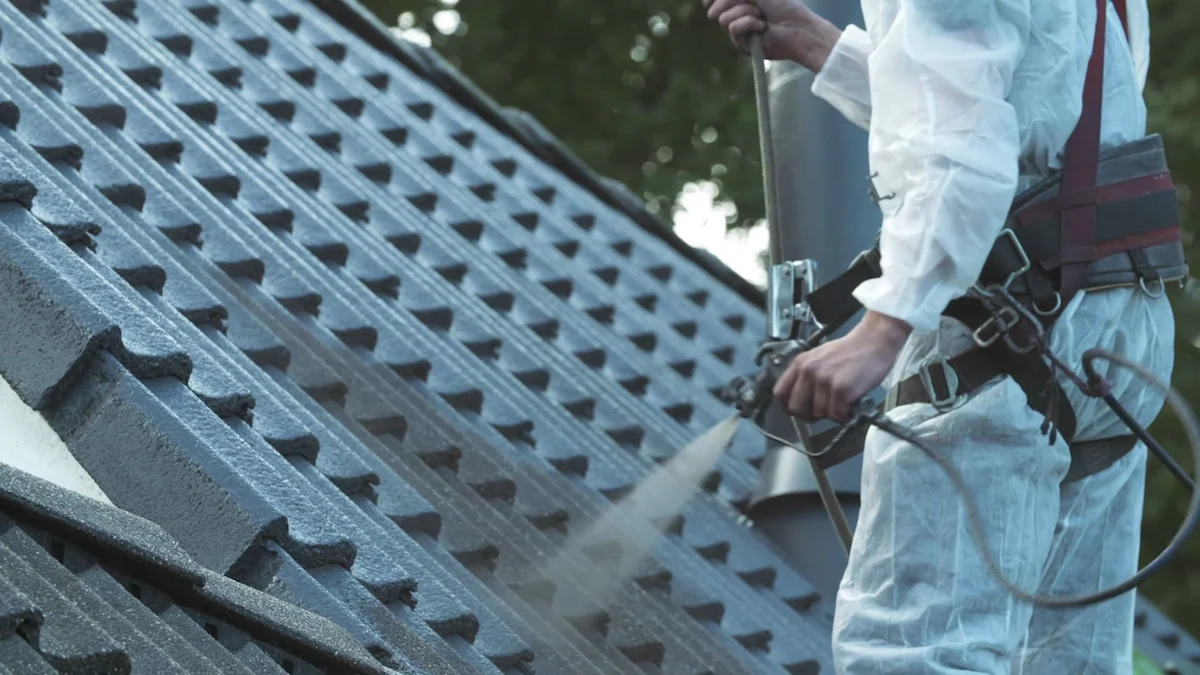
Electronics Industry
The electronics industry heavily relies on CVD coating technology to enhance the performance and reliability of its products.
Semiconductor Manufacturing
In semiconductor manufacturing, CVD coatings play a crucial role. They provide thin films essential for creating integrated circuits and other semiconductor devices. These coatings ensure precise control over electrical properties, which is vital for the functionality of electronic components. The ability of CVD to deposit uniform layers on complex geometries makes it indispensable in this field.
Protective Coatings for Components
CVD coatings also serve as protective barriers for electronic components. They shield sensitive parts from environmental factors such as moisture and corrosion. This protection extends the lifespan of devices and maintains their performance over time. By using CVD coatings, manufacturers can produce more durable and reliable electronic products.
Aerospace Industry
The aerospace industry benefits significantly from the advanced properties of CVD coatings.
Thermal Barrier Coatings
CVD coatings provide thermal barrier protection for aerospace components like turbine blades. These coatings withstand extreme temperatures, reducing heat transfer and protecting the underlying materials. This capability enhances the efficiency and longevity of aircraft engines, contributing to improved performance and reduced maintenance costs.
Wear-Resistant Coatings
Wear-resistant CVD coatings are essential for aerospace applications. They increase the durability of components exposed to harsh conditions, such as friction and abrasion. By applying these coatings, the aerospace industry can ensure that critical parts maintain their integrity and functionality throughout their service life.
Medical Industry
In the medical sector, CVD coatings offer unique advantages that improve the safety and effectiveness of medical devices.
Biocompatible Coatings
CVD technology provides biocompatible coatings for medical implants and tools. These coatings ensure that implants integrate well with human tissue, reducing the risk of rejection and complications. The precision of CVD allows for the creation of coatings that meet stringent medical standards, enhancing patient outcomes.
Sterilization-Resistant Surfaces
Medical devices require surfaces that can withstand repeated sterilization without degrading. CVD coatings offer excellent resistance to sterilization processes, ensuring that medical tools remain safe and effective over time. This durability is crucial for maintaining hygiene and preventing infections in healthcare settings.
Advantages of CVD Coating Technology
High-Quality Coatings
Chemical Vapor Deposition (CVD) technology stands out for producing high-quality coatings that enhance the durability and performance of various components. These coatings exhibit remarkable durability and longevity, making them ideal for applications in harsh environments. Industries such as automotive and aerospace benefit significantly from CVD coatings due to their ability to withstand wear and tear over extended periods. The high hardness and wear resistance of CVD coatings ensure that components maintain their integrity and functionality, even under challenging conditions.
Moreover, CVD coatings offer precision and consistency in their application. The process allows for the deposition of uniform layers, ensuring that every part of the substrate receives an even coating. This precision is crucial in industries like electronics, where even minor inconsistencies can affect the performance of semiconductor devices. By providing consistent coatings, CVD technology enhances the reliability and efficiency of electronic components.
Versatility in Materials
CVD technology’s versatility in materials makes it a preferred choice across various industries. It can coat a wide range of coatable substrates, including metals, ceramics, and glass. This adaptability allows manufacturers to apply CVD coatings to diverse materials, expanding the scope of their applications. For instance, in the biomedical field, CVD coatings are used to enhance the biocompatibility of medical implants, ensuring they integrate well with human tissue.
Additionally, CVD technology offers customizable coating properties, enabling the creation of coatings tailored to specific requirements. By adjusting the precursor gases and reaction conditions, manufacturers can produce coatings with desired characteristics, such as enhanced corrosion resistance or improved thermal stability. This customization capability makes CVD coatings suitable for specialized applications, such as protective barriers in the semiconductor industry or thermal barriers in aerospace components.
Disadvantages of CVD Coating Technology
Hazardous By-Products
Chemical Vapor Deposition (CVD) technology, while advantageous, presents certain challenges, particularly concerning hazardous by-products. The chemical reactions involved in the CVD process often produce by-products that can pose environmental and safety concerns.
Environmental and Safety Concerns
The production of hazardous by-products during the CVD process raises significant environmental and safety concerns. These by-products may include toxic gases and volatile organic compounds (VOCs) that can harm the environment if not properly managed. The release of such substances into the atmosphere contributes to air pollution and poses health risks to workers and nearby communities. Therefore, industries utilizing CVD technology must implement stringent safety protocols to mitigate these risks.
Mitigation Strategies
To address these environmental and safety concerns, industries have developed various mitigation strategies. One effective approach involves the use of advanced filtration and scrubbing systems to capture and neutralize harmful emissions before they are released into the environment. Additionally, manufacturers are increasingly adopting eco-friendly materials and processes to reduce the generation of hazardous by-products. These sustainability initiatives not only minimize environmental impact but also align with the growing demand for greener technologies.
Equipment and Operational Costs
Another notable disadvantage of CVD coating technology lies in its equipment and operational costs. The initial investment and ongoing expenses can be substantial, impacting the overall cost-effectiveness of the technology.
Initial Investment
The initial investment required for CVD coating technology can be significant. Setting up a CVD system involves purchasing specialized equipment, such as reaction chambers, gas delivery systems, and temperature control mechanisms. These components are essential for ensuring precise control over the deposition process but come with a high price tag. Consequently, the upfront costs may deter smaller companies from adopting CVD technology.
Maintenance and Operational Expenses
In addition to the initial investment, maintenance and operational expenses contribute to the overall cost of CVD technology. Regular maintenance is crucial to ensure the equipment functions optimally and to prevent costly breakdowns. Furthermore, the operational expenses associated with running a CVD system, including energy consumption and gas supply, can add up over time. Despite these costs, the durability and performance benefits of CVD coatings often justify the investment for industries seeking high-quality solutions.
Comparing CVD with Other Coating Technologies
CVD vs. PVD
Process Differences
Chemical Vapor Deposition (CVD) and Physical Vapor Deposition (PVD) represent two distinct approaches to coating technology. CVD involves the transformation of gaseous precursors into a solid film on a substrate through chemical reactions. This process typically requires high temperatures, which facilitate the breakdown of gases and the formation of a uniform coating. In contrast, PVD relies on physical processes such as evaporation or sputtering to deposit material onto a substrate. PVD operates at lower temperatures compared to CVD, making it suitable for heat-sensitive materials.
- CVD excels in providing uniform coatings and offers higher deposition rates. It can deposit a diverse range of materials, including metals, ceramics, and polymers.
- PVD is known for its environmentally friendly nature and results in high-purity coatings with excellent adhesion. However, it has slower deposition rates and limitations on coating complex geometries.
Application Suitability
The choice between CVD and PVD often depends on the specific application requirements. CVD is favored for applications that demand high purity and uniform coatings, such as semiconductor manufacturing and aerospace components. Its ability to coat complex shapes makes it indispensable in industries where intricate geometries are common.
- CVD provides high purity and uniform coatings, making it ideal for applications requiring precise control over coating properties.
- PVD is preferred for applications where lower temperature processing is crucial, such as coating temperature-sensitive substrates.
CVD vs. Electroplating
Advantages and Limitations
Chemical Vapor Deposition (CVD) and electroplating offer different advantages and limitations in coating technology. CVD provides high-quality coatings with exceptional adhesion and uniformity. It can coat a wide range of materials and complex shapes, making it versatile for various industries. However, CVD involves high-temperature processes and produces hazardous by-products, which require careful management.
- CVD offers high-quality coatings with excellent adhesion and uniformity. It can coat complex shapes and a wide range of materials.
- Electroplating involves the deposition of a metal layer onto a substrate using an electric current. It is cost-effective and suitable for large-scale production but may not provide the same level of uniformity and adhesion as CVD.
Use Cases
The use cases for CVD and electroplating vary based on their respective strengths. CVD is commonly used in industries such as electronics, aerospace, and medical devices, where high-quality coatings are essential for performance and durability. Its ability to deposit uniform layers on complex geometries makes it ideal for semiconductor manufacturing and protective coatings for aerospace components.
- CVD is used in semiconductor manufacturing, aerospace components, and medical devices, where high-quality coatings are crucial.
- Electroplating is widely used in automotive, jewelry, and decorative applications, where cost-effectiveness and large-scale production are priorities.
Chemical Vapor Deposition (CVD) technology offers significant advantages, including high-purity coatings, uniformity, and versatility across various industries. Its ability to coat complex shapes and a wide range of materials makes it a preferred choice for applications demanding precision and durability. However, the high equipment costs and hazardous by-products require careful consideration. Industries should weigh these factors when deciding to implement CVD coating. For applications needing high-quality, uniform coatings, CVD remains an optimal choice, especially in sectors like electronics and aerospace, where performance and reliability are paramount.
FAQ
What is CVD coating?
CVD coating refers to the process of depositing a solid material from a gaseous phase onto a substrate. This technique creates high-quality coatings with excellent adhesion and uniformity. CVD coatings are widely used in industries such as electronics, aerospace, and medical devices due to their ability to enhance product durability and performance.
Why should I use PVD or CVD?
Choosing between PVD (Physical Vapor Deposition) and CVD (Chemical Vapor Deposition) depends on specific application needs. CVD offers high-purity, uniform coatings and excels in coating complex shapes. PVD, on the other hand, operates at lower temperatures and is suitable for heat-sensitive materials. Both methods provide unique advantages, and selecting the right one involves considering factors like material compatibility and desired coating properties.
How does the CVD process work?
The CVD process involves introducing volatile precursor gases into a reaction chamber. These gases undergo chemical reactions, often at elevated temperatures, to form a solid material that adheres to the substrate surface. The process allows for precise control over coating thickness and composition, making it ideal for applications requiring high-quality coatings.
What industries benefit from CVD coatings?
CVD coatings benefit a wide range of industries, including electronics, aerospace, and medical sectors. In electronics, they are crucial for semiconductor manufacturing and protecting components. Aerospace applications include thermal barrier and wear-resistant coatings. In the medical field, CVD provides biocompatible and sterilization-resistant surfaces for implants and devices.
Are there any environmental concerns with CVD technology?
Yes, the CVD process can produce hazardous by-products, such as toxic gases and volatile organic compounds (VOCs). These substances pose environmental and safety concerns if not properly managed. Industries using CVD technology implement mitigation strategies, including advanced filtration systems and eco-friendly materials, to minimize environmental impact.
What are the cost considerations for CVD technology?
CVD technology involves significant initial investment and operational costs. Setting up a CVD system requires purchasing specialized equipment, which can be expensive. Additionally, maintenance and operational expenses, such as energy consumption and gas supply, contribute to the overall cost. Despite these expenses, the high-quality coatings produced by CVD often justify the investment for industries seeking durable solutions.
How does CVD compare to electroplating?
CVD and electroplating offer different advantages. CVD provides high-quality coatings with exceptional adhesion and uniformity, suitable for complex shapes and a wide range of materials. Electroplating, which involves depositing a metal layer using an electric current, is cost-effective and ideal for large-scale production. However, it may not achieve the same level of uniformity and adhesion as CVD.
Can CVD coat complex shapes effectively?
Yes, CVD technology excels in coating complex shapes. Techniques such as rotating the substrate and using multiple gas inlets ensure uniform coatings on intricate geometries. This capability makes CVD indispensable in industries where precise and consistent coatings on complex shapes are essential.
What are the advantages of CVD coatings?
CVD coatings offer several advantages, including high durability, precision, and versatility. They provide long-lasting protection against wear and corrosion, making them ideal for harsh environments. The process allows for customizable coating properties, enabling manufacturers to tailor coatings to specific requirements, such as enhanced thermal stability or improved biocompatibility.
How does temperature affect the CVD process?
Temperature plays a crucial role in the CVD process, influencing reaction rates and coating quality. Higher temperatures generally enhance reaction rates, resulting in more uniform and dense coatings. However, excessively high temperatures can cause unwanted side reactions or damage the substrate. Maintaining an optimal temperature range is essential for achieving high-quality coatings.