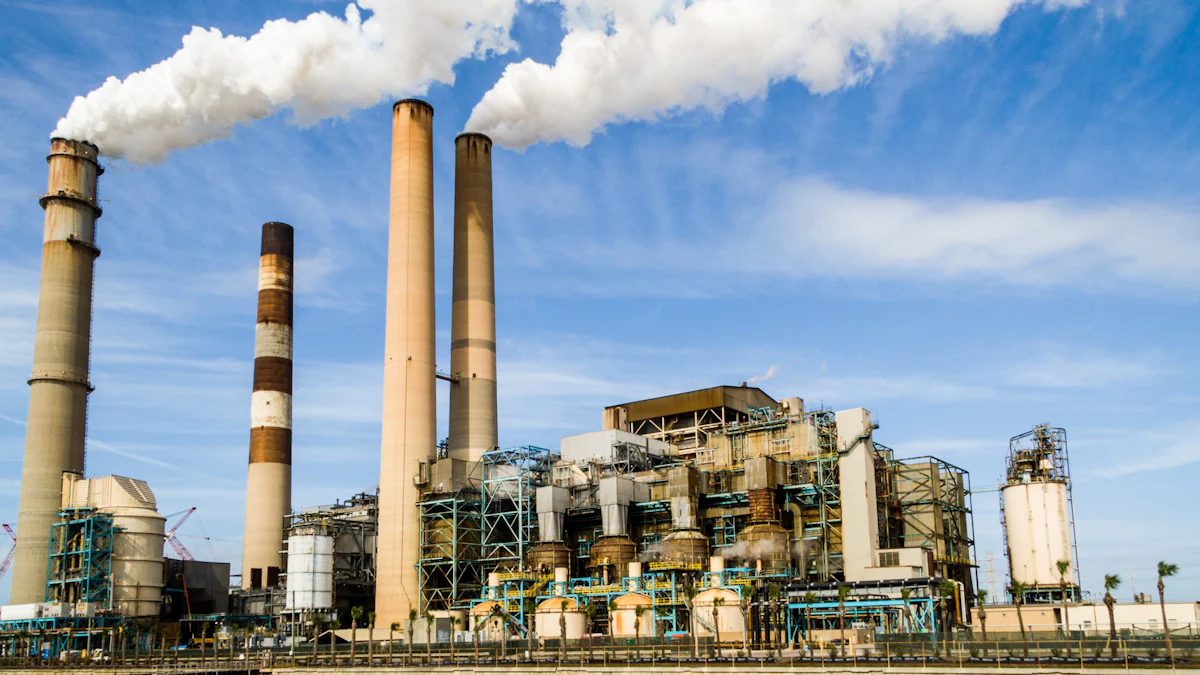
In the realm of industrial applications, understanding the differences between CVD SiC and sintered SiC is crucial. These two forms of silicon carbide offer distinct properties and advantages. The CVD SiC Coating results from a chemical vapor deposition process, providing exceptional purity, hardness, and thermal conductivity. This makes it ideal for high-performance applications, such as the cvd coated sic paddle used in semiconductor manufacturing. Additionally, sic cvd coated materials exhibit superior mechanical properties, enhancing their performance in demanding environments. In contrast, sintered SiC, while less expensive, features a rougher surface finish and porous properties, making it suitable for high-temperature work. The choice between these materials depends on specific industrial needs and performance requirements.
Key Takeaways
- CVD SiC offers exceptional purity and thermal conductivity, making it ideal for high-performance applications like semiconductor manufacturing.
- Sintered SiC is a cost-effective alternative, suitable for high-temperature environments and applications where budget constraints are a priority.
- When selecting between CVD and sintered SiC, consider specific industrial needs such as purity, cost, and application environment to ensure optimal performance.
- CVD SiC’s high mechanical strength and polishability enhance its use in optics and electronic packaging, providing reliable heat management.
- Sintered SiC’s inherent porosity can be advantageous in filtration systems, effectively removing particulates from liquids and gases.
- Both forms of SiC exhibit excellent chemical stability, making them valuable in harsh industrial environments, reducing maintenance costs and downtime.
- Understanding the distinct properties of CVD and sintered SiC can help industries make informed decisions that enhance operational efficiency.
Overview of Silicon Carbide (SiC) and Its Importance
What is Silicon Carbide?
Silicon Carbide (SiC) stands as a compound of silicon and carbon, renowned for its exceptional hardness and thermal properties. This material, often referred to as carborundum, exhibits a crystalline structure that contributes to its durability and resilience. SiC’s unique characteristics make it a preferred choice in various industrial applications.
Key Properties of SiC:
- High Hardness: SiC ranks just below diamond in terms of hardness, making it ideal for abrasive applications.
- Thermal Conductivity: It efficiently conducts heat, which is crucial for high-temperature environments.
- Chemical Stability: SiC resists chemical corrosion, enhancing its longevity in harsh conditions.
Importance of SiC in Industrial Applications
Silicon Carbide plays a pivotal role in numerous industries due to its versatile properties. Its application spans from automotive to semiconductor sectors, each benefiting from SiC’s unique attributes.
-
Automotive Industry: SiC enhances the efficiency of electric vehicles by improving system performance within inverter systems. This improvement can lead to increased driving distances, making SiC a valuable component in the push towards sustainable transportation.
-
Semiconductor Processing: The high purity of SiC, especially when produced through chemical vapor deposition, makes it suitable for semiconductor processing equipment. Its ability to withstand high temperatures and maintain stability ensures optimal performance in wafer processing chambers.
-
Industrial Machinery: SiC’s wear resistance and thermal properties make it an excellent choice for components exposed to extreme conditions. Its use in furnace furniture and other high-temperature applications underscores its importance in maintaining operational efficiency.
-
Chemical Processing: The chemical corrosion resistance of SiC makes it ideal for environments where exposure to harsh chemicals is common. This property extends the lifespan of equipment, reducing maintenance costs and downtime.
Understanding CVD SiC
Manufacturing Process of CVD SiC
Chemical Vapor Deposition (CVD) serves as the primary method for producing CVD SiC. This process involves a vacuum deposition technique where gaseous reactants form a solid material on a substrate. The result is a face-centered cubic, polycrystalline form of silicon carbide. This method ensures high purity and uniform composition, making CVD SiC an ideal choice for applications demanding superior material properties. The process, although more expensive than sintering or reaction bonding, yields a product with excellent thermal conductivity and density.
Properties of CVD SiC
CVD SiC boasts several remarkable properties that make it stand out in industrial applications:
- Purity: With a purity level exceeding 99.9%, CVD SiC offers unmatched chemical and oxidation resistance.
- Thermal Conductivity: Approaching 300 W/mK, its thermal conductivity ensures efficient heat management.
- Mechanical Strength: The material’s high density and cubic structure contribute to its exceptional mechanical strength and durability.
- Polishability: It can be polished to a very smooth finish, enhancing its suitability for optical applications.
- Dimensional Stability: The material maintains stability under thermal and cryogenic conditions, making it reliable in extreme environments.
Typical Applications of CVD SiC
The unique properties of CVD SiC make it suitable for a wide range of industrial applications:
- Semiconductor Manufacturing: The cvd coated sic paddle plays a crucial role in semiconductor processing equipment. Its ability to withstand high temperatures and resist chemical corrosion ensures optimal performance in wafer processing chambers.
- Optics: CVD SiC serves as an excellent material for reflective optics, including mirrors for surveillance and high-energy laser systems. Its superior polishability and low scatter make it ideal for precision optical components.
- Aerospace and Defense: The material’s thermal and dimensional stability make it suitable for use in large astronomical telescopes and weather satellites.
- Electronic Packaging: As a heat sink, CVD SiC effectively manages heat in electronic devices, enhancing their performance and longevity.
CVD Coated SiC Paddle in Semiconductor Manufacturing
In the semiconductor industry, the cvd coated sic paddle plays a pivotal role in wafer processing. This component, crafted from CVD SiC, showcases exceptional properties that make it indispensable in high-performance environments. The chemical vapor deposition process used to create these paddles ensures a high-purity, polycrystalline material with a face-centered cubic structure. This results in superior thermal conductivity, approaching 300 W/mK, which is crucial for managing the intense heat generated during semiconductor manufacturing.
Key Advantages of CVD Coated SiC Paddle:
-
Thermal Management: The cvd coated sic paddle efficiently dissipates heat, maintaining optimal temperatures within the processing chamber. This capability reduces the risk of thermal damage to sensitive wafers, ensuring consistent quality and performance.
-
Chemical Resistance: The high purity of CVD SiC provides excellent resistance to chemical corrosion. This property is vital in semiconductor environments where exposure to harsh chemicals is common. The paddle’s durability minimizes maintenance needs and extends its operational lifespan.
-
Mechanical Strength: The dense, cubic structure of CVD SiC imparts remarkable mechanical strength to the paddle. This strength allows it to withstand the physical stresses of wafer handling and processing without compromising its integrity.
-
Dimensional Stability: The cvd coated sic paddle maintains its shape and size under varying thermal conditions. This stability is essential for precise wafer positioning and alignment, which are critical for successful semiconductor fabrication.
The cvd coated sic paddle exemplifies the advantages of using CVD SiC in semiconductor manufacturing. Its combination of thermal management, chemical resistance, and mechanical strength makes it a reliable choice for enhancing the efficiency and reliability of semiconductor processing equipment.
Understanding Sintered SiC
Manufacturing Process of Sintered SiC
Sintered Silicon Carbide (SiC) emerges from a meticulous manufacturing process that involves the densification of silicon carbide powder. This process utilizes non-oxide sintering aids at elevated temperatures. The sintering process transforms the powder into a solid mass, resulting in a material with a distinct set of properties. Unlike CVD SiC, which forms through a vapor phase reaction, sintered SiC relies on solid-state processes. This method produces a material that, while generally less pure than CVD SiC, offers unique advantages in specific applications.
Properties of Sintered SiC
Sintered SiC exhibits several noteworthy properties that make it suitable for various industrial uses:
- Chemical Corrosion Resistance: Sintered SiC stands out for its ability to resist chemical corrosion, making it ideal for environments where exposure to harsh chemicals is common.
- Thermal Stability: The material maintains stability under high-temperature conditions, which is crucial for applications involving extreme heat.
- Mechanical Strength: Although not as hard as CVD SiC, sintered SiC still offers significant mechanical strength, allowing it to withstand physical stresses.
- Porosity: The inherent porosity of sintered SiC can be advantageous in applications requiring filtration or diffusion.
Typical Applications of Sintered SiC
The unique properties of sintered SiC make it suitable for a variety of industrial applications:
-
High-Temperature Furnaces: Sintered SiC’s thermal stability and resistance to chemical corrosion make it an excellent choice for components in high-temperature furnaces. It ensures durability and longevity in these demanding environments.
-
Chemical Processing Equipment: The material’s resistance to chemical attack makes it ideal for use in chemical processing equipment, where it can withstand corrosive substances and extend the lifespan of the equipment.
-
Abrasive Applications: Due to its hardness, sintered SiC finds use in abrasive applications, such as grinding and cutting tools, where it provides effective material removal and wear resistance.
-
Filtration Systems: The porosity of sintered SiC makes it suitable for filtration systems, where it can effectively filter particulates and impurities from liquids and gases.
Sintered SiC, with its distinct properties and advantages, plays a vital role in various industrial sectors. Its ability to withstand harsh conditions and maintain performance makes it a reliable choice for applications requiring durability and resistance to extreme environments.
Comparative Analysis of CVD SiC and Sintered SiC
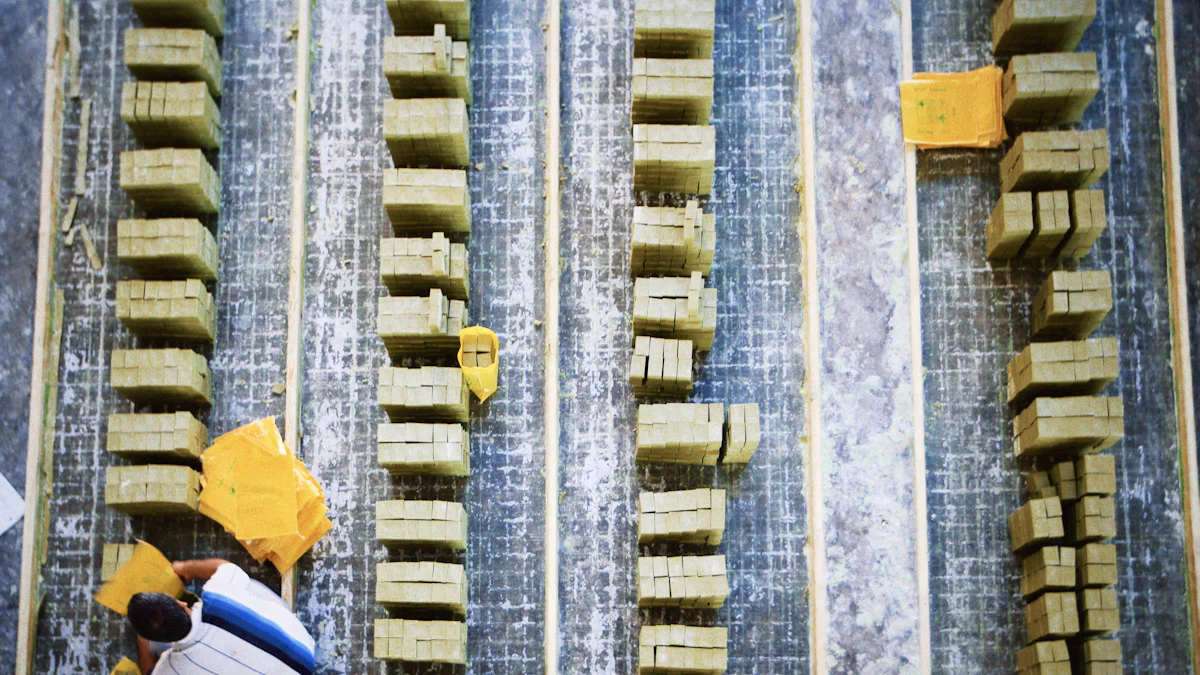
Material Properties Comparison
CVD SiC and Sintered SiC exhibit distinct material properties that cater to different industrial needs. CVD SiC, produced through chemical vapor deposition, boasts a high purity level exceeding 99.9%. This purity translates into exceptional chemical and oxidation resistance. Its thermal conductivity approaches 300 W/mK, ensuring efficient heat management. The material’s high density and cubic structure contribute to its remarkable mechanical strength and durability. Additionally, CVD SiC can be polished to a very smooth finish, enhancing its suitability for optical applications.
In contrast, Sintered SiC is manufactured by densifying silicon carbide powder with non-oxide sintering aids at high temperatures. This process results in a material with notable chemical corrosion resistance and thermal stability. Although Sintered SiC does not match the hardness of CVD SiC, it still offers significant mechanical strength. Its inherent porosity can be advantageous in applications requiring filtration or diffusion.
Cost Analysis
The cost of producing CVD SiC tends to be higher than that of Sintered SiC due to the complexity of the chemical vapor deposition process. This method involves a vacuum deposition technique where gaseous reactants form a solid material on a substrate, ensuring high purity and uniform composition. The expense of this process reflects in the final product’s price, making CVD SiC more suitable for high-performance applications where superior material properties justify the cost.
On the other hand, Sintered SiC emerges as a more cost-effective option. The manufacturing process involves conventional ceramic forming techniques and sintering in an inert atmosphere at temperatures above 2000°C. This method, while less expensive, results in a material with a rougher surface finish and porous properties. Sintered SiC serves as an economical choice for applications where cost considerations outweigh the need for extreme purity and polishability.
Suitability for Different Industrial Uses
The choice between CVD SiC and Sintered SiC depends on specific industrial requirements. CVD SiC excels in environments demanding high thermal conductivity, chemical resistance, and mechanical strength. Its applications include semiconductor manufacturing, optics, aerospace, and electronic packaging. The material’s ability to maintain stability under thermal and cryogenic conditions makes it reliable in extreme environments.
Sintered SiC, with its chemical corrosion resistance and thermal stability, finds use in high-temperature furnaces, chemical processing equipment, and abrasive applications. Its porosity makes it suitable for filtration systems, effectively filtering particulates and impurities from liquids and gases. Sintered SiC offers a practical solution for industries prioritizing cost-effectiveness and durability in harsh conditions.
In summary, CVD SiC and Sintered SiC serve distinct industrial purposes. CVD SiC offers high purity, exceptional durability, and resistance to corrosion, making it ideal for high-performance applications like semiconductor manufacturing. Its non-porous nature ensures stability and reliability. Conversely, Sintered SiC provides a cost-effective solution with its chemical reactivity and surface roughness, suitable for environments where budget constraints are paramount.
When selecting the appropriate type of SiC, industries should consider specific needs such as purity, cost, and application environment to ensure optimal performance and efficiency.
FAQ
What makes Silicon Carbide (SiC) a valuable material?
Silicon Carbide (SiC) stands out due to its exceptional properties. It is a versatile non-oxide ceramic known for its unique physical and chemical characteristics. SiC exhibits high hardness, excellent thermal conductivity, and remarkable chemical stability, making it ideal for various industrial applications.
How does CVD SiC differ from Sintered SiC in terms of manufacturing?
CVD SiC is produced through a chemical vapor deposition process, resulting in a highly pure, polycrystalline material. This method ensures superior thermal conductivity and mechanical properties. In contrast, Sintered SiC is created by densifying silicon carbide powder with non-oxide sintering aids at high temperatures, leading to a material that is generally less pure but offers unique advantages in specific applications.
Why is SiC considered superior for semiconductor components?
SiC’s excellent electrical conductivity and thermal performance make it a superior choice for semiconductor components. Its ability to withstand high temperatures and maintain stability ensures optimal performance in demanding environments, such as semiconductor processing equipment.
What are the typical applications of CVD SiC?
CVD SiC finds use in semiconductor manufacturing, optics, aerospace, and electronic packaging. Its high purity and exceptional durability make it suitable for high-performance applications, including reflective optics and heat sinks in electronic devices.
How does Sintered SiC perform in high-temperature settings?
Sintered SiC excels in high-temperature environments due to its thermal stability and resistance to chemical corrosion. It is often used in high-temperature furnaces, chemical processing equipment, and abrasive applications, where it provides durability and longevity.
What role does SiC play in the automotive industry?
In the automotive sector, SiC enhances the efficiency of electric vehicles by improving system performance within inverter systems. This improvement can lead to increased driving distances, making SiC a valuable component in the push towards sustainable transportation.
How does the cost of CVD SiC compare to Sintered SiC?
The production of CVD SiC tends to be more expensive due to the complexity of the chemical vapor deposition process. This method ensures high purity and uniform composition, making CVD SiC suitable for high-performance applications. Sintered SiC, on the other hand, offers a more cost-effective solution for applications where budget constraints are paramount.
What are the advantages of using SiC in chemical processing?
SiC’s chemical corrosion resistance makes it ideal for environments where exposure to harsh chemicals is common. This property extends the lifespan of equipment, reducing maintenance costs and downtime, making SiC a reliable choice for chemical processing applications.
How does SiC contribute to industrial machinery?
SiC’s wear resistance and thermal properties make it an excellent choice for components exposed to extreme conditions. Its use in furnace furniture and other high-temperature applications underscores its importance in maintaining operational efficiency.
What factors should industries consider when selecting between CVD SiC and Sintered SiC?
Industries should consider specific needs such as purity, cost, and application environment. CVD SiC offers high purity and exceptional durability, making it ideal for high-performance applications. Sintered SiC provides a cost-effective solution with its chemical reactivity and surface roughness, suitable for environments where budget constraints are paramount.