Thermco system wafer boats serve as essential tools in semiconductor manufacturing. These specialized systems securely hold and transport semiconductor wafers during high-temperature processes. Their design ensures uniform heating, which is critical for achieving precise results in thermal treatments. By minimizing contamination risks, they maintain the cleanliness required in sensitive manufacturing environments. These systems play a pivotal role in supporting the production of advanced semiconductor devices, ensuring both efficiency and reliability in every step of the process.
Key Takeaways
- Thermco wafer boat systems are essential for securely holding and transporting semiconductor wafers during high-temperature processes, ensuring uniform heating and precise thermal treatment. The use of durable materials like quartz and silicon carbide allows these systems to withstand extreme temperatures, enhancing their longevity and reliability in semiconductor manufacturing.
- Minimizing contamination risks is a key feature of Thermco wafer boats, as their non-reactive surfaces and design help maintain cleanliness in sensitive manufacturing environments.
- Thermco’s expertise in wafer boat technology ensures compatibility with various furnace designs, making these systems versatile for different production needs.
- Safety and efficiency enhancements, such as robust construction and lightweight materials, contribute to faster production cycles and lower operational costs.
- Thermco wafer boats support advanced semiconductor technologies by providing the precision and reliability needed for complex manufacturing processes. Future innovations from Thermco may focus on sustainability and the development of wafer boats for emerging technologies, ensuring they remain at the forefront of the semiconductor industry.
What Are Thermco Wafer Boat Systems?
Definition and Purpose
Thermco wafer boat systems serve as critical tools in the semiconductor industry. These systems hold and transport semiconductor wafers during high-temperature processes like diffusion and oxidation. Their primary purpose lies in ensuring uniform heating and precise thermal treatment of wafers. By maintaining stability and alignment, they prevent damage to the wafers during processing. The design of these systems minimizes contamination risks, which is essential in cleanroom environments. This ensures that the wafers remain free from particles or impurities that could compromise their quality.
The structure of a Thermco system wafer boat often includes durable materials capable of withstanding extreme temperatures. These materials ensure longevity and reliability during repeated use in manufacturing cycles. The systems also support compatibility with various furnace designs, making them versatile for different production needs. Their role extends beyond simple wafer handling, as they contribute directly to the efficiency and accuracy of semiconductor fabrication.
Thermco’s Expertise in Wafer Boat Technology
Thermco Systems has established itself as a leader in wafer boat technology. With decades of experience in the semiconductor industry, the company has developed innovative solutions tailored to meet the demands of modern manufacturing. Their expertise lies in creating systems that balance precision, durability, and cleanliness. This focus ensures that their products meet the stringent requirements of semiconductor production.
Thermco’s designs prioritize minimal particle generation, which is vital for maintaining cleanroom standards. The company employs advanced engineering techniques to enhance the performance and reliability of its wafer boats. By integrating cutting-edge materials and designs, Thermco ensures that its systems can handle the challenges of high-temperature processes. Their commitment to innovation has positioned them as a trusted partner for manufacturers seeking efficient and reliable wafer handling solutions.
Thermco Systems continues to push the boundaries of wafer boat technology, supporting the advancement of semiconductor manufacturing through precision and innovation.
Key Features and Components of Thermco System Wafer Boat
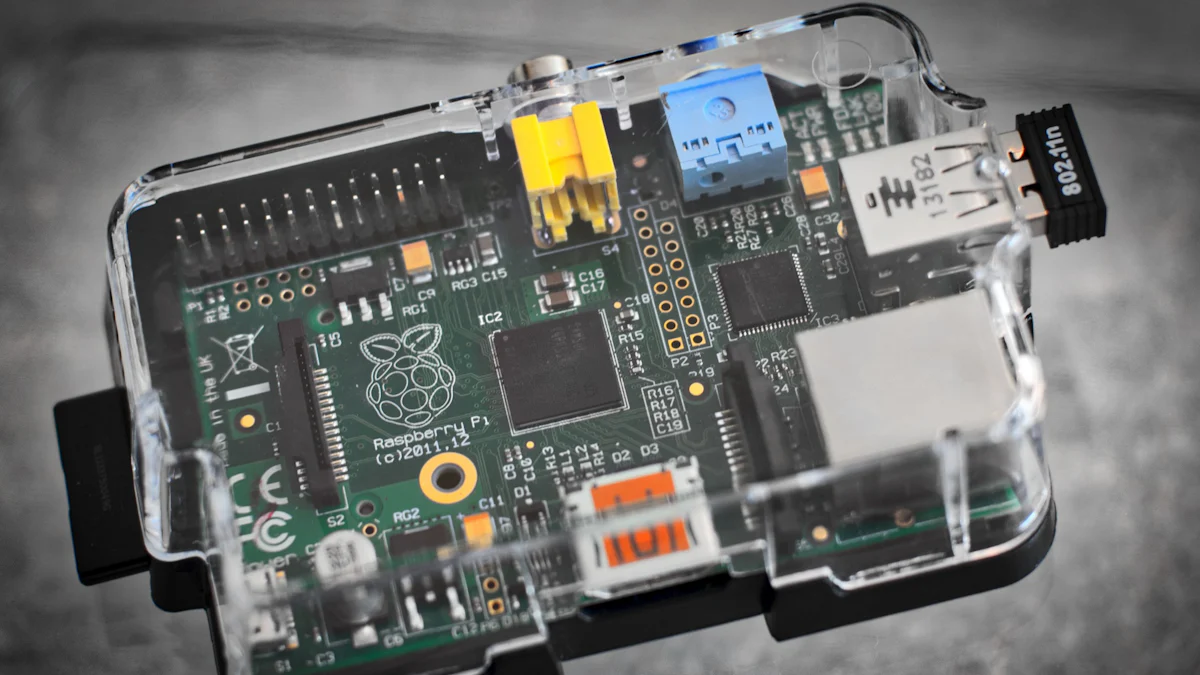
Material Composition and Durability
Thermco system wafer boats rely on high-quality materials to withstand the extreme conditions of semiconductor manufacturing. Manufacturers often use materials like quartz or silicon carbide due to their ability to endure high temperatures without deforming. These materials resist thermal shock, ensuring that the wafer boats maintain structural integrity during rapid heating and cooling cycles. Their durability allows for repeated use, reducing the need for frequent replacements and lowering operational costs.
The material composition also plays a vital role in maintaining cleanliness. Non-reactive surfaces prevent chemical interactions with wafers, preserving their purity. This feature is essential in cleanroom environments where even minor contamination can compromise production quality. By combining strength and cleanliness, Thermco system wafer boats meet the rigorous demands of modern semiconductor fabrication.
Design for Precision and Compatibility
The design of Thermco system wafer boats prioritizes precision to ensure accurate wafer alignment during processing. Proper alignment minimizes the risk of damage and guarantees uniform heating across all wafers. This precision contributes to consistent results in thermal treatments, which are critical for producing high-performance semiconductor devices.
Compatibility with various furnace systems enhances the versatility of these wafer boats. Thermco engineers design them to fit seamlessly into different manufacturing setups, allowing manufacturers to integrate them without extensive modifications. This adaptability supports a wide range of production requirements, making them suitable for diverse applications in the semiconductor industry.
Safety and Efficiency Enhancements
Safety features in Thermco system wafer boats protect both the wafers and the equipment. The robust construction reduces the likelihood of breakage, safeguarding the wafers during handling and processing. Additionally, the design minimizes particle generation, which helps maintain a clean manufacturing environment and reduces contamination risks.
Efficiency improvements further enhance their value. Lightweight materials make handling easier, while optimized designs reduce energy consumption during thermal processes. These enhancements contribute to faster production cycles and lower operational costs. By focusing on safety and efficiency, Thermco ensures that its wafer boats support reliable and cost-effective semiconductor manufacturing.
Applications of Thermco Wafer Boat Systems in Semiconductor Manufacturing
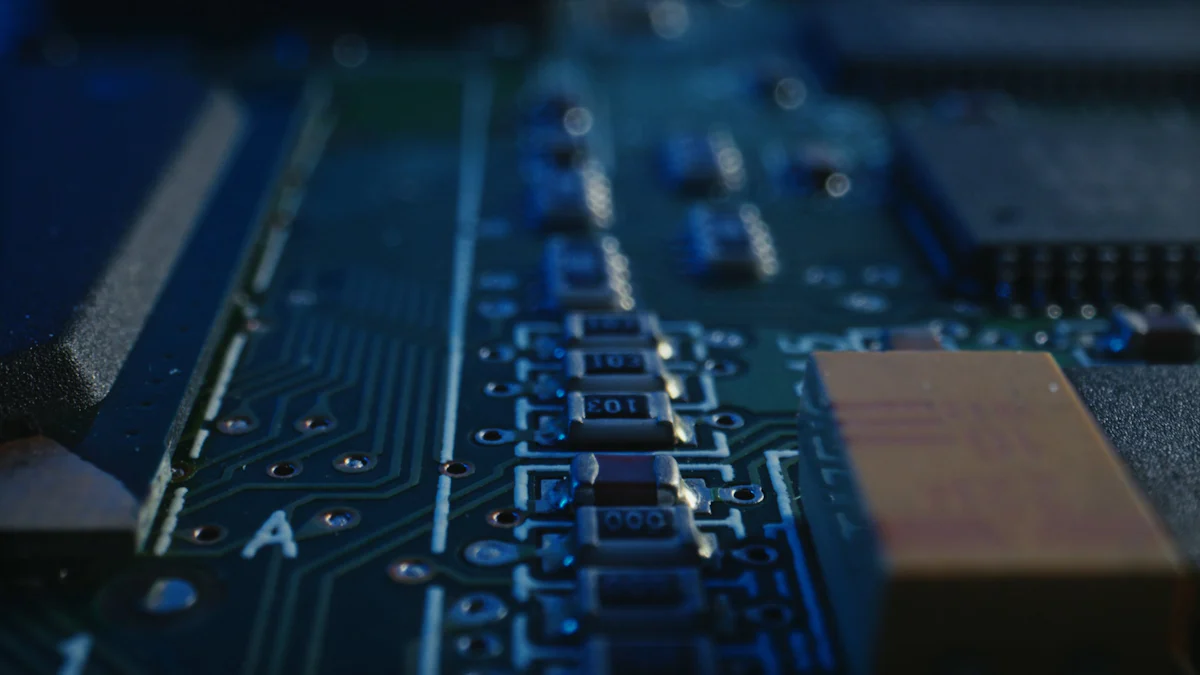
Thermal Processes (Diffusion, Oxidation, Annealing)
Thermco wafer boat systems play a vital role in thermal processes essential to semiconductor manufacturing. These processes include diffusion, oxidation, and annealing, which require precise temperature control and uniform heating. During diffusion, the system ensures that dopants spread evenly across the wafer surface, creating the desired electrical properties. In oxidation, it supports the formation of a thin oxide layer, which acts as an insulator or protective barrier. Annealing, another critical process, relies on these systems to repair crystal defects and enhance material properties.
The design of the thermco system wafer boat ensures stability during these high-temperature treatments. Its durable materials withstand extreme heat without deforming, maintaining the integrity of the wafers. By providing consistent thermal conditions, the system contributes to the production of reliable and high-performance semiconductor devices.
Wafer Handling and Contamination Control
Efficient wafer handling is crucial in semiconductor manufacturing, and Thermco wafer boat systems excel in this area. These systems securely hold wafers during transportation and processing, reducing the risk of physical damage. Proper alignment within the boat ensures that wafers remain stable throughout the manufacturing cycle. This precision minimizes errors and enhances overall production quality.
Contamination control is another significant advantage of these systems. The non-reactive surfaces of the wafer boats prevent chemical interactions that could compromise wafer purity. Additionally, the design minimizes particle generation, which is critical in cleanroom environments. By maintaining cleanliness, the system ensures that wafers meet the stringent standards required for advanced semiconductor technologies.
Support for Advanced Semiconductor Technologies
Thermco wafer boat systems provide essential support for the development of advanced semiconductor technologies. As the industry moves toward smaller and more complex devices, the demand for precision and reliability increases. These systems meet these challenges by offering compatibility with cutting-edge manufacturing processes. Their ability to handle high temperatures and maintain cleanliness makes them indispensable for producing next-generation semiconductors.
The adaptability of the thermco system wafer boat allows manufacturers to integrate it into various production setups. This flexibility supports innovations such as 3D stacking and advanced lithography techniques. By enabling these technologies, the system contributes to the growth and evolution of the semiconductor industry.
Importance and Future of Thermco Wafer Boat Systems
Contribution to Industry Growth and Efficiency
Thermco wafer boat systems have significantly impacted the semiconductor industry by enhancing production efficiency and ensuring high-quality output. Their precise design and durable materials allow manufacturers to achieve consistent results during thermal processes. This reliability reduces errors and minimizes waste, which directly contributes to cost savings and improved productivity.
The systems also support the industry’s growth by enabling the production of advanced semiconductor devices. As technology evolves, manufacturers require tools that can handle complex processes with precision. Thermco system wafer boats meet these demands by maintaining stability and cleanliness during high-temperature treatments. Their role in ensuring uniform heating and contamination control makes them indispensable for producing cutting-edge technologies.
By streamlining manufacturing processes, these systems help companies meet increasing market demands. Faster production cycles and reduced operational costs allow manufacturers to scale their operations efficiently. Thermco’s commitment to innovation ensures that its wafer boats remain a cornerstone of the semiconductor industry’s progress.
Innovations and Future Developments
Thermco continues to innovate its wafer boat systems to address the challenges of modern semiconductor manufacturing. The company invests in research and development to improve the performance and versatility of its products. Advanced materials and engineering techniques enhance the durability and precision of these systems, ensuring they meet the evolving needs of the industry.
Future developments may include wafer boats designed for emerging technologies such as 3D semiconductors and quantum computing. These advancements require tools capable of handling intricate processes with unparalleled accuracy. Thermco’s expertise positions it to lead the way in creating solutions for these next-generation applications.
Sustainability is another focus area for future innovations. Thermco aims to develop wafer boats that reduce energy consumption and minimize environmental impact. Lightweight materials and optimized designs will likely play a role in achieving these goals. By prioritizing sustainability, Thermco aligns its products with the industry’s shift toward greener manufacturing practices.
Thermco’s dedication to innovation ensures that its wafer boat systems will continue to support the semiconductor industry’s growth and adaptation to new technologies.
Thermco system wafer boats play a vital role in semiconductor manufacturing. Their precise design ensures uniform heating and contamination control, which are essential for producing high-quality devices. These systems enhance efficiency and reliability, supporting the industry’s demand for advanced technologies. By enabling precision in thermal processes, they contribute to the development of cutting-edge semiconductor innovations. Thermco’s commitment to improving its wafer boat systems positions the company as a key player in shaping the future of semiconductor manufacturing.
FAQ
What are Thermco wafer boat systems used for?
Thermco wafer boat systems hold and transport semiconductor wafers during high-temperature processes. They ensure uniform heating, precise thermal treatment, and contamination control, which are essential for semiconductor manufacturing.
Why is uniform heating important in semiconductor manufacturing?
Uniform heating ensures that all wafers receive consistent thermal treatment. This consistency prevents defects, enhances the quality of the semiconductor devices, and supports the production of reliable and high-performance technologies.
What materials are used to make Thermco wafer boats?
Manufacturers use materials like quartz and silicon carbide to construct Thermco wafer boats.
How do Thermco wafer boat systems minimize contamination?
Thermco wafer boats feature non-reactive surfaces that prevent chemical interactions with wafers. Their design reduces particle generation, maintaining the cleanliness required in cleanroom environments and ensuring wafer purity.
Are Thermco wafer boat systems compatible with all furnace designs?
Thermco wafer boat systems are designed for compatibility with various furnace systems. Their adaptable design allows manufacturers to integrate them into different production setups without extensive modifications.
What thermal processes rely on Thermco wafer boat systems?
Thermal processes such as diffusion, oxidation, and annealing depend on Thermco wafer boat systems. These processes require precise temperature control and uniform heating, which the systems provide to ensure optimal results.
How do Thermco wafer boat systems enhance safety?
Thermco wafer boats feature robust construction that reduces the risk of breakage during handling and processing. Their design minimizes particle generation, which helps maintain a clean manufacturing environment and reduces contamination risks.
What role do Thermco wafer boat systems play in advanced semiconductor technologies?
Thermco wafer boat systems support the development of advanced technologies like 3D semiconductors and quantum computing. Their precision, durability, and cleanliness make them indispensable for producing next-generation semiconductor devices.
How do Thermco wafer boat systems contribute to cost efficiency?
Thermco wafer boats reduce operational costs by offering durability and reusability. Their lightweight materials and optimized designs improve handling and energy efficiency, leading to faster production cycles and lower expenses.
What innovations can be expected in Thermco wafer boat systems?
Future innovations may include wafer boats designed for emerging technologies and sustainable manufacturing practices. Thermco focuses on advanced materials, optimized designs, and energy-efficient solutions to meet the evolving needs of the semiconductor industry.