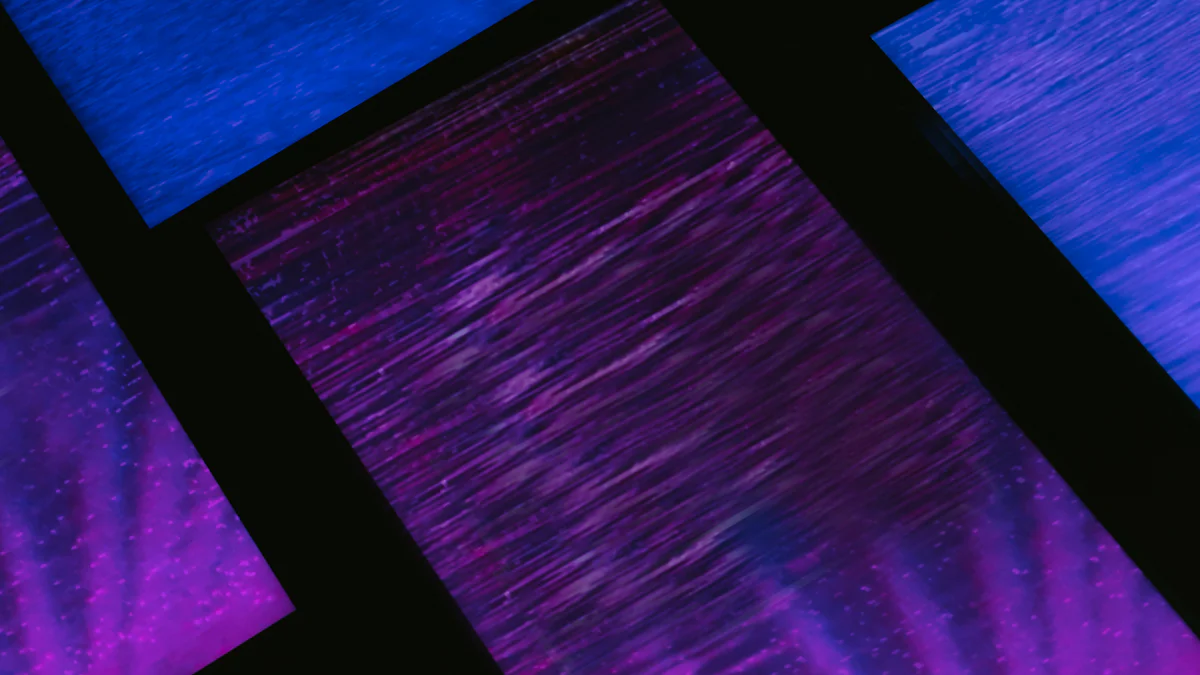
UV LED SiC trays represent a groundbreaking advancement in light-emitting diode applications and semiconductor manufacturing. UV LED technology emits ultraviolet light with precision and efficiency, making it essential for industries like disinfection and curing. Silicon carbide (SiC) trays are designed for durability and exceptional heat resistance, offering high thermal conductivity and abrasion resistance. The integration of UV LED SiC trays creates a powerful solution, addressing critical industrial needs with unparalleled reliability and performance.
Key Takeaways
- UV LED technology offers high efficiency, compact design, and long lifespan, making it a sustainable alternative to traditional UV light sources.
SiC trays provide exceptional durability and thermal stability, making them ideal for high-performance applications in semiconductor manufacturing and high-temperature processes.
- The combination of UV LEDs and SiC trays enhances industrial processes by delivering precise light emission and superior heat management, improving productivity and reliability.
- Industries can achieve significant cost savings with UV LEDs due to their lower energy consumption and reduced maintenance needs.
- Both UV LEDs and SiC trays support sustainability goals by minimizing waste and avoiding hazardous materials, contributing to eco-friendly industrial practices.
Applications of UV LED SiC trays span across disinfection, curing, and semiconductor manufacturing, showcasing their versatility and effectiveness in various sectors.
Understanding UV LED Technology
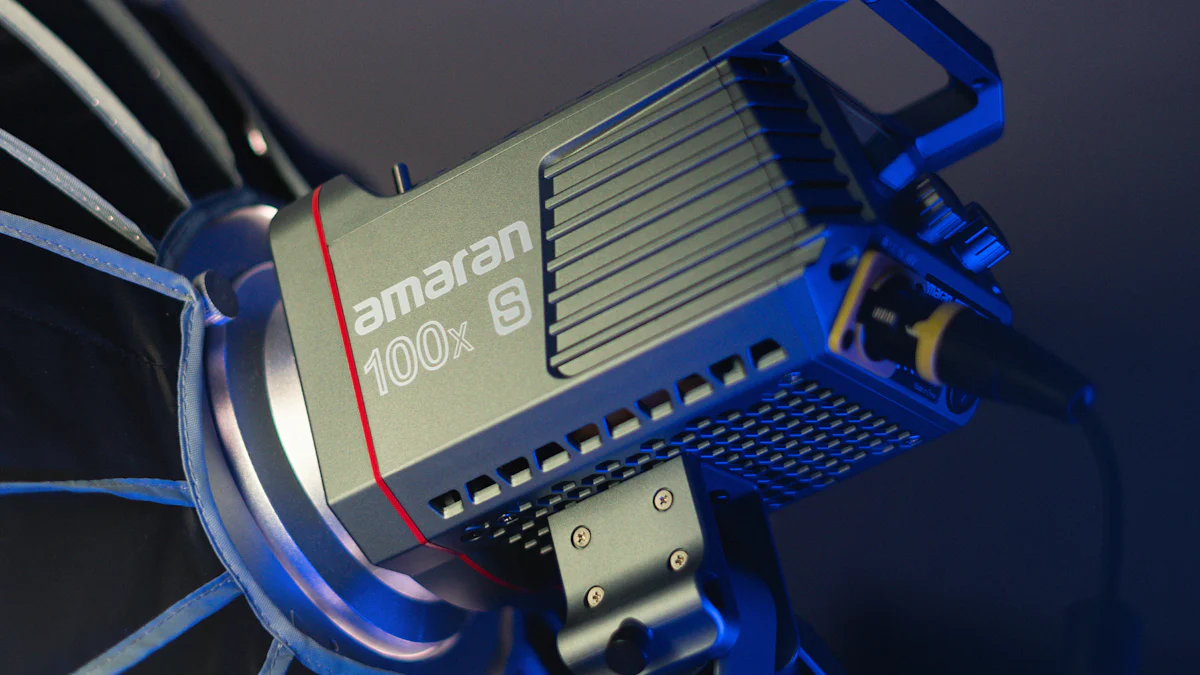
UV LED technology has revolutionized the way industries utilize ultraviolet light. By emitting UV light through light-emitting diodes, this technology offers precision, efficiency, and versatility across various applications. Its ability to replace traditional mercury lamps has positioned it as a sustainable and innovative solution in modern industries.
Key Features of UV LED
UV LEDs stand out due to their unique features, which make them indispensable in numerous fields:
- High Efficiency: UV LEDs deliver exceptional energy efficiency compared to conventional UV light sources. They consume less power while maintaining high output levels.
- Compact Design: These LEDs are small and lightweight, allowing seamless integration into devices and systems. Their compact nature enhances portability and design flexibility.
- Long Lifespan: UV LEDs boast a significantly longer operational life than traditional UV lamps. This reduces maintenance costs and ensures consistent performance over time.
- Wavelength Precision: UV LEDs can emit light at specific wavelengths, such as 265 nm for UV-C LEDs. This precision makes them ideal for targeted applications like disinfection and curing.
- Environmental Benefits: Unlike mercury lamps, UV LEDs do not contain hazardous materials. This makes them safer for the environment and easier to dispose of responsibly.
Benefits of UV LED
The advantages of UV LED technology extend beyond its features, offering tangible benefits to industries and consumers alike:
- Cost Savings: UV LEDs reduce operating costs by consuming less energy and requiring minimal maintenance. Their long lifespan further contributes to cost efficiency.
- Enhanced Performance: Industries benefit from the high output and reliability of UV LEDs. Applications like UV curing achieve faster and more consistent results, improving productivity.
- Versatility: UV LEDs cater to a wide range of applications, including disinfection, printing, and semiconductor manufacturing. Their adaptability makes them a preferred choice across sectors.
- Safety and Sustainability: The absence of mercury and reduced energy consumption align with global efforts to promote sustainability. UV LEDs provide a safer alternative for both users and the environment.
- Heat Management: UV LEDs generate less heat compared to traditional UV sources. This feature enables their use in heat-sensitive materials and processes, expanding their application scope.
For example, UV-C LEDs have gained prominence for their ability to inactivate pathogens, including viruses. Their compact size and high efficiency make them suitable for integration into medical devices and public health solutions. Similarly, UV LED curing has transformed printing and electronic assembly processes by reducing energy consumption and enhancing system capabilities.
The integration of UV LED technology with SiC trays further amplifies its benefits. Together, they create robust solutions for industries requiring precision, durability, and heat resistance. This combination exemplifies the potential of UV LED SiC trays in advancing industrial efficiency and sustainability.
Exploring SiC Trays
Silicon carbide (SiC) trays have emerged as a cornerstone in industries requiring high-performance materials. These trays, crafted from silicon carbide, exhibit exceptional durability and thermal stability, making them indispensable in demanding environments such as semiconductor manufacturing and high-temperature processes.
Properties of SiC Trays
SiC trays possess a unique set of properties that distinguish them from other materials. These characteristics enable their widespread use in advanced industrial applications:
- High Thermal Conductivity: SiC trays efficiently dissipate heat, ensuring stable performance even in extreme temperatures. This property makes them ideal for applications like wafer processing and MOCVD (Metal-Organic Chemical Vapor Deposition) processes.
- Exceptional Hardness: Silicon carbide ranks among the hardest ceramic materials. This hardness provides superior resistance to wear and mechanical stress, extending the lifespan of the trays.
- Chemical Resistance: SiC trays resist corrosion and oxidation, even when exposed to harsh chemicals or high-temperature environments. This ensures consistent performance in semiconductor fabrication and other critical processes.
- High Purity: The material’s purity minimizes contamination risks, which is crucial in industries like electronics and photovoltaics.
- Lightweight Structure: Despite their robustness, SiC trays remain lightweight, facilitating easier handling and integration into equipment.
For instance, SiC Coated Graphite Substrates combine a silicon carbide coating with a graphite base to deliver enhanced thermal stability and oxidation resistance. These substrates excel in high-temperature environments, such as those encountered in semiconductor processing.
Advantages of SiC Trays
The advantages of SiC trays extend beyond their inherent properties, offering tangible benefits that enhance operational efficiency and reliability:
- Durability: SiC trays withstand prolonged exposure to high temperatures and mechanical stress without degradation. This durability reduces replacement frequency and maintenance costs.
- Enhanced Performance: Their ability to operate at higher voltages and frequencies, coupled with superior thermal management, ensures optimal performance in high-power and high-frequency applications.
- Versatility: SiC trays support a wide range of applications, from LED substrate transportation to wafer processing. Their adaptability makes them a preferred choice across multiple sectors.
- Cost-Effectiveness: The long service life and reduced maintenance needs of SiC trays contribute to lower operational costs over time.
- Environmental Benefits: The high purity and chemical resistance of SiC trays minimize waste and contamination, aligning with sustainability goals in modern industries.
For example, High Purity 99.9% SiC Trays are specifically designed for semiconductor manufacturing. Their exceptional hardness and chemical resistance make them suitable for conveying LED substrates and other delicate components.
The integration of SiC trays with UV LED technology further amplifies their utility. Together, they form a robust solution for industries requiring precision, heat resistance, and durability. This synergy highlights the transformative potential of UV LED SiC trays in advancing industrial processes.
Applications of UV LED SiC Trays
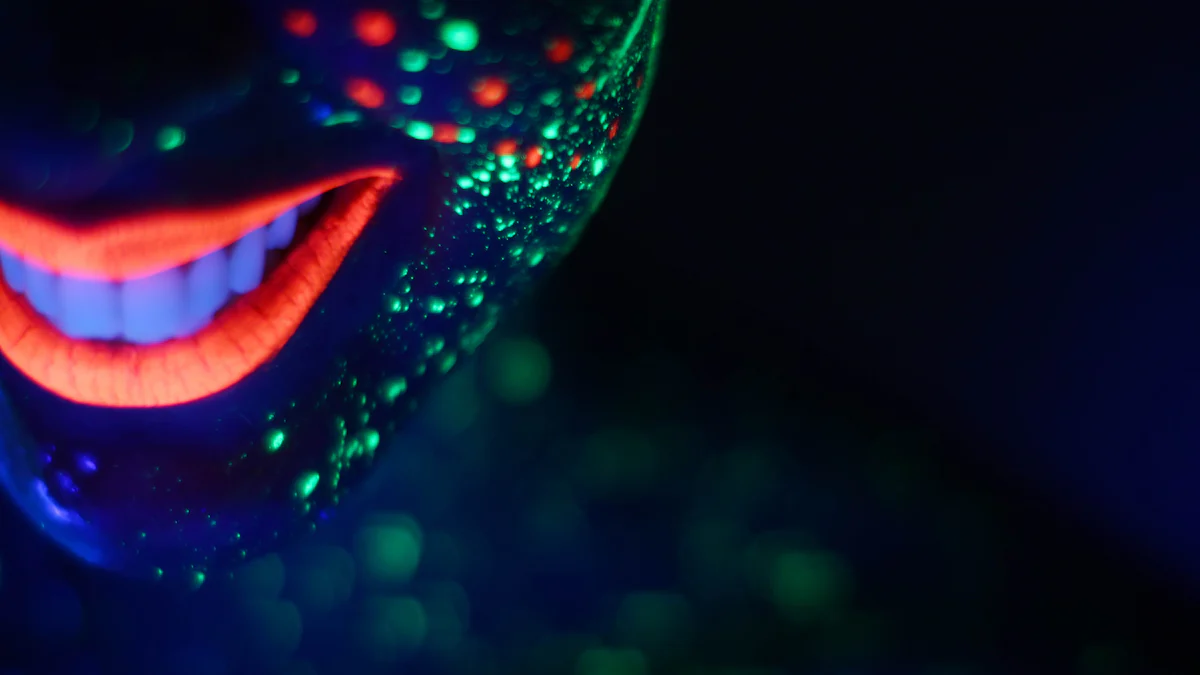
Applications of UV LED
UV LED technology has transformed numerous industries by offering efficient and precise ultraviolet light solutions. Its applications span across diverse fields:
- Disinfection and Sterilization: UV LEDs effectively inactivate bacteria, viruses, and other pathogens. Their compact size and wavelength precision make them ideal for medical devices, air purifiers, and water treatment systems.
- UV Curing: Industries like printing, electronics, and polymer manufacturing rely on UV LEDs for curing processes. These LEDs reduce energy consumption, lower surface temperatures, and eliminate the need for air exhaust systems, enhancing operational efficiency.
- Optoelectronic Systems: UV LEDs serve as trigger sources in optoelectronic systems, enabling digital and analog outputs for capturing UV-range images. This application is particularly valuable in scientific research and imaging technologies.
- Semiconductor Manufacturing: UV LEDs play a critical role in photolithography and wafer processing. Their ability to emit light at specific wavelengths ensures precision in these high-tech processes.
For instance, UV-C LEDs have gained prominence for their ability to disinfect surfaces and air, contributing significantly to public health advancements.
Applications of SiC Trays
Silicon carbide trays are indispensable in industries requiring materials with exceptional durability and thermal stability. Their applications include:
- Semiconductor Fabrication: SiC trays are widely used in processes like ICP etching and wafer transportation. Their high hardness, abrasion resistance, and thermal conductivity ensure reliability in these demanding environments.
- LED Substrate Conveyance: SiC trays excel in conveyor equipment for transporting LED substrates. Their chemical resistance and lightweight structure enhance efficiency and reduce contamination risks.
- High-Temperature Processes: Industries such as metallurgy and photovoltaics utilize SiC trays for their ability to withstand extreme temperatures without degradation.
- Advanced Coatings: SiC-coated graphite substrates combine the benefits of silicon carbide and graphite. These substrates provide enhanced thermal stability and oxidation resistance, making them suitable for high-temperature applications.
For example, high-purity 99.9% SiC trays are specifically designed for semiconductor manufacturing, ensuring minimal contamination and optimal performance.
Combined Applications of UV LED and SiC Trays
The integration of UV LED technology with SiC trays creates a powerful synergy, addressing critical industrial needs with unmatched precision and durability. Combined applications include:
- Wafer Processing: UV LEDs and SiC trays work together in wafer processing systems. UV LEDs provide precise light emission, while SiC trays ensure stable thermal management and substrate support.
- LED Manufacturing: The combination enhances the efficiency of LED production lines. UV LEDs facilitate curing processes, and SiC trays offer reliable substrate conveyance, reducing downtime and improving output quality.
- Photovoltaic Industry: UV LED SiC trays contribute to the production of solar cells by supporting high-temperature processes and ensuring uniformity in material handling.
- Medical Device Sterilization: UV LEDs integrated with SiC trays enable efficient sterilization of medical instruments. The trays’ chemical resistance and thermal stability complement the disinfection capabilities of UV LEDs.
For instance, UV LED SiC trays have proven invaluable in semiconductor manufacturing, where precision, heat resistance, and durability are paramount. This combination exemplifies the potential of advanced materials in driving industrial innovation.
UV LED and SiC trays showcase unique features that redefine industrial efficiency and reliability. UV LED technology delivers precision, energy savings, and environmental benefits, while SiC trays provide unmatched durability, thermal stability, and chemical resistance. Together, they address critical challenges in industries like semiconductor manufacturing, disinfection, and high-temperature processes. Their combined applications enhance productivity, reduce costs, and support sustainability goals. As industries evolve, the growing importance of these advanced materials highlights their role in driving technological innovation and meeting modern industrial demands.
FAQ
What are the environmental benefits of UV LED curing?
UV LED curing offers significant environmental advantages. It reduces energy consumption by up to 85%, as reported by users of UV LED systems. Unlike traditional mercury lamps, UV LEDs do not contain hazardous materials, making them a safer and more sustainable choice. This technology aligns with global efforts to minimize environmental impact while enhancing industrial efficiency.
Why is there a focus on developing LEDs that emit below 365 nm?
The development of LEDs emitting below 365 nm addresses critical needs in industries like air and water purification, food disinfection, and biomedical applications. These LEDs provide a superior alternative to mercury lamps, offering precision and efficiency. Their ability to target specific wavelengths enhances their effectiveness in sterilization and other specialized processes.
How does UV-C LED technology contribute to public health?
UV-C LEDs play a pivotal role in public health by inactivating pathogens, including bacteria and viruses. Their compact size and high efficiency make them ideal for integration into medical devices, air purifiers, and water treatment systems. For example, Stanley Electric has developed UV-C LEDs with industry-leading output and efficiency, ensuring reliable performance in disinfection applications.
What makes SiC trays suitable for semiconductor manufacturing?
SiC trays excel in semiconductor manufacturing due to their high thermal conductivity, exceptional hardness, and chemical resistance. These properties ensure stable performance in high-temperature environments and reduce contamination risks. Their lightweight structure also facilitates easy handling, making them indispensable in processes like wafer transportation and ICP etching.
Can UV LED and SiC trays be used together in industrial applications?
Yes, the combination of UV LED technology and SiC trays creates a robust solution for industries requiring precision and durability. In wafer processing, UV LEDs provide precise light emission, while SiC trays ensure efficient thermal management. This synergy enhances productivity and reliability in demanding environments like semiconductor and LED manufacturing.
How do UV LEDs compare to traditional mercury lamps?
UV LEDs outperform mercury lamps in several ways. They consume less energy, have a longer lifespan, and do not contain hazardous materials. Additionally, UV LEDs offer wavelength precision, enabling targeted applications such as disinfection and curing. These advantages make UV LEDs a more sustainable and cost-effective choice for modern industries.
What industries benefit the most from SiC trays?
SiC trays are widely used in industries like semiconductor fabrication, photovoltaics, and metallurgy. Their ability to withstand extreme temperatures and resist chemical corrosion makes them ideal for high-temperature processes. They also play a crucial role in LED substrate conveyance, ensuring minimal contamination and optimal performance.
Are UV LED systems cost-effective?
UV LED systems provide excellent cost savings over time. Their energy efficiency reduces operational costs, while their long lifespan minimizes maintenance expenses. Industries using UV LED curing systems have reported significant reductions in energy consumption, making this technology a cost-effective solution for various applications.
What role do UV LED SiC trays play in the photovoltaic industry?
UV LED SiC trays contribute to the photovoltaic industry by supporting high-temperature processes involved in solar cell production. SiC trays ensure uniform material handling, while UV LEDs enhance precision in curing and disinfection processes. This combination improves efficiency and supports sustainability goals in renewable energy production.
How do UV LEDs and SiC trays support sustainability goals?
UV LEDs and SiC trays align with sustainability objectives by reducing energy consumption and minimizing waste. UV LEDs eliminate the need for hazardous mercury, while SiC trays offer long service life and high purity, reducing contamination risks. Together, they provide eco-friendly solutions that enhance industrial efficiency and environmental responsibility.