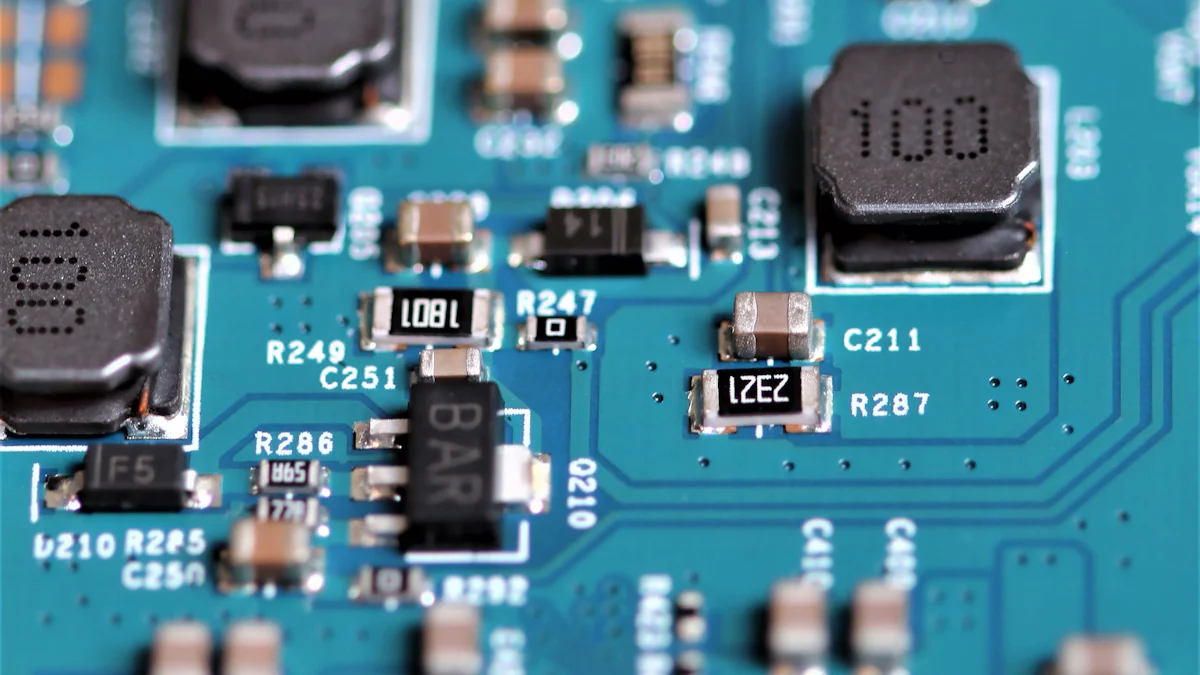
Wafer size plays a pivotal role in semiconductor manufacturing, directly influencing production efficiency. Larger wafers enable manufacturers to produce more semiconductor devices per unit, reducing costs and improving throughput. For instance, transitioning from 200 mm to 300 mm wafers has been shown to lower the price per die by approximately 30–40%. This efficiency stems from the ability to ship more parts in less time and maximize die per wafer area.
SiC wafer boats, known for their stability and high thermal conductivity, are indispensable in handling wafers during production. Their design evolves to accommodate varying wafer sizes, ensuring seamless operations and optimized manufacturing processes.
Key Takeaways
- Larger wafers, such as 300 mm, significantly enhance production efficiency by allowing manufacturers to produce more chips per wafer, reducing costs by 30-40%.
SiC wafer boats are essential for handling wafers during production, providing stability and high thermal conductivity to ensure precise wafer alignment.
Transitioning to larger wafers like 450 mm presents challenges, including increased costs and the need for advanced equipment, but offers potential for greater efficiency.
- Smaller wafers, such as 200 mm, remain valuable for specialized applications due to their lower investment requirements and suitability for niche markets.
- Manufacturers must balance the benefits of larger wafers with the complexities of implementation to optimize production processes effectively.
- The design of SiC wafer boats evolves with wafer sizes, ensuring they can support the increased weight and surface area of larger wafers while maintaining operational stability.
- Investing in automated handling systems alongside SiC wafer boats is crucial for managing the complexities of larger wafer production and enhancing overall efficiency.
Overview of Wafer Sizes
Common Wafer Sizes in Semiconductor Manufacturing
Semiconductor manufacturing relies on wafers of varying sizes, each tailored to specific production needs. The most prevalent wafer sizes include 200 mm (8-inch) and 300 mm (12-inch) wafers. These sizes dominate the industry due to their balance of cost-effectiveness and production efficiency. While 200 mm wafers remain widely used for legacy systems and certain specialized applications, 300 mm wafers have become the standard for high-volume production.
The industry has also explored larger wafers, such as 450 mm (18-inch) wafers, to meet future demands. However, transitioning to these larger sizes presents significant challenges. Manufacturers must address increased costs, complex lithography requirements, and the need for advanced automated handling systems. Despite these hurdles, research continues to focus on developing technologies that can support larger wafer sizes, ensuring readiness for future market shifts.
Advantages and Challenges of Different Wafer Sizes
Each wafer size offers distinct advantages and poses unique challenges. Smaller wafers, such as 200 mm, are cost-effective for producing smaller batches or specialized chips. They require less investment in equipment and infrastructure, making them ideal for niche markets. However, their limited surface area restricts the number of chips produced per wafer, which can impact scalability.
Larger wafers, like 300 mm, significantly enhance production efficiency. They allow manufacturers to produce more chips per wafer, reducing the cost per die by approximately 30–40%. This efficiency stems from the ability to maximize the usable area of the wafer. However, the transition to 300 mm wafers required substantial investment in new facilities and equipment, which posed initial financial barriers for many manufacturers.
The potential shift to 450 mm wafers promises even greater efficiency gains. These wafers could further reduce production costs and increase throughput. Yet, the challenges associated with this transition are considerable. Manufacturers face higher costs for research and development, as well as the need to redesign existing processes and equipment. Additionally, concerns about achieving a sufficient return on investment have slowed widespread adoption.
"The semiconductor industry must carefully weigh the benefits of larger wafers against the costs and complexities of implementation," as highlighted by ongoing research efforts.
Impact of Wafer Size on Production Efficiency
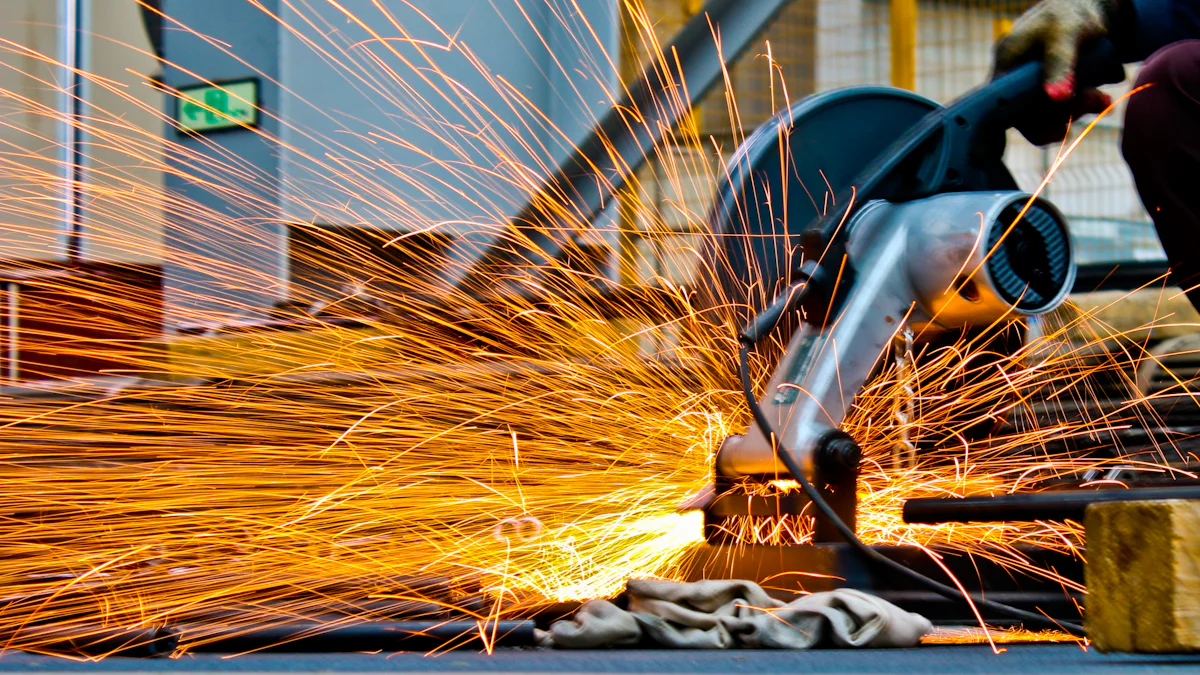
Throughput and Yield Considerations
Wafer size directly affects throughput in semiconductor manufacturing. Larger wafers, such as 300 mm, allow manufacturers to produce more chips per wafer compared to smaller wafers like 200 mm. This increased capacity enhances throughput, enabling faster production cycles and higher output volumes. For instance, a 300 mm wafer can accommodate significantly more chips than a 200 mm wafer, making it the preferred choice for high-volume production.
However, yield considerations complicate the benefits of larger wafers. Historically, yield tends to decrease as wafer size increases. This decline occurs because larger wafers require more precise manufacturing processes, which take time to perfect. Over time, manufacturers achieve comparable yields across different wafer sizes, but the initial challenges can impact production efficiency. The delicate balance between maximizing throughput and maintaining high yield remains a critical focus for semiconductor producers.
"The semiconductor process becomes more complex with larger wafers, but the potential for higher throughput drives innovation in manufacturing techniques," as noted by industry experts.
Cost Implications of Wafer Size
Wafer size plays a pivotal role in determining production costs. Smaller wafers, such as 200 mm, are more cost-effective for producing specialized chips or smaller batches. They require less investment in equipment and infrastructure, making them suitable for niche markets. The cost of producing and assembling semiconductor chips is generally lower with 200 mm wafers compared to 300 mm wafers, which appeals to manufacturers focused on cost-sensitive applications.
Larger wafers, like 300 mm, offer significant cost advantages in high-volume production. By fitting more chips onto a single wafer, manufacturers reduce the cost per die by approximately 30–40%. This reduction stems from the ability to maximize the usable area of the wafer, which lowers material waste and improves overall efficiency. Despite these benefits, transitioning to 300 mm wafers required substantial upfront investment in new facilities and advanced equipment.
The potential shift to 450 mm wafers introduces even greater cost implications. These wafers promise enhanced productivity but come with steep financial challenges. 450 mm wafers are expected to cost four times as much as 300 mm wafers, and equipment costs could rise by 20–50%. This significant expense has slowed the adoption of 450 mm wafers, despite their potential to revolutionize semiconductor manufacturing.
"The cost of transitioning to larger wafers must be carefully weighed against the long-term benefits of increased efficiency and reduced cost per chip," according to ongoing industry analysis.
SiC Wafer Boats and Their Role in Manufacturing
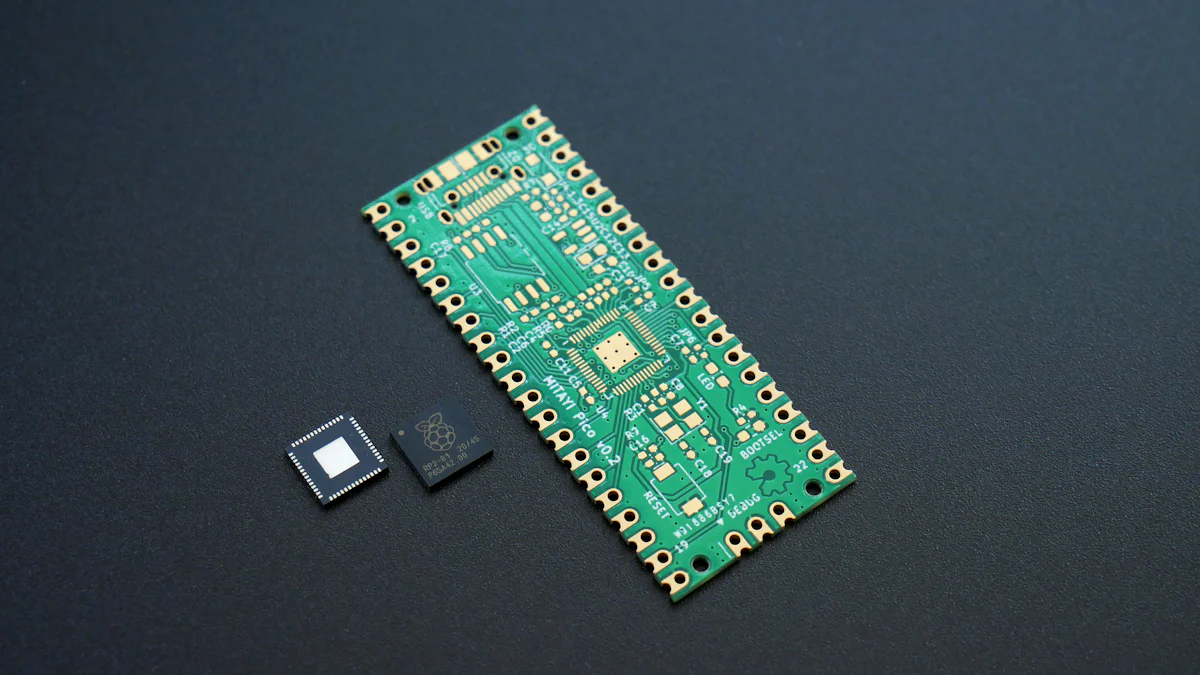
Overview of SiC Wafer Boats
Silicon carbide (SiC) wafer boats serve as critical components in the semiconductor manufacturing process. These boats, also referred to as wafer carriers, are designed to securely hold silicon carbide wafers during various production stages. Their primary function is to ensure the safe transportation and precise positioning of wafers within high-temperature environments, such as furnaces and reactors.
Manufacturers construct SiC wafer boats using high-purity silicon carbide, a material renowned for its exceptional thermal and mechanical properties. This advanced material offers superior heat resistance, enabling the boats to withstand extreme temperatures without compromising structural integrity. Additionally, SiC boats exhibit remarkable chemical stability, making them resistant to corrosive substances encountered during semiconductor fabrication.
The design of these wafer boats often includes slots or grooves that firmly hold wafers in place. This feature prevents movement or sliding during critical processes, ensuring uniformity and accuracy in wafer treatment. Some SiC wafer boats also feature specialized coatings to enhance their durability and extend their operational lifespan. For instance, SiC-coated boats provide even greater heat resistance and chemical stability, making them ideal for demanding manufacturing conditions.
"SiC wafer boats play an indispensable role in maintaining wafer integrity and optimizing production efficiency," as noted by industry experts.
Importance of SiC Wafer Boats for Different Wafer Sizes
The size of the wafer directly influences the design and functionality of SiC wafer boats. As wafer sizes increase, the boats must adapt to accommodate the larger dimensions while maintaining stability and precision. For example, boats designed for 200 mm wafers differ significantly from those used for 300 mm or 450 mm wafers. Larger wafers require boats with enhanced structural strength and capacity to handle the increased weight and surface area.
SiC wafer boats designed for smaller wafers, such as 200 mm, are often more compact and cost-effective. These boats cater to niche markets and specialized applications where smaller wafers remain prevalent. On the other hand, boats for 300 mm wafers prioritize high-volume production efficiency. Their design focuses on maximizing throughput while ensuring consistent wafer alignment and protection.
The potential shift to 450 mm wafers presents new challenges and opportunities for SiC wafer boat manufacturers. Boats for these larger wafers must incorporate advanced engineering to support the increased size and weight. They must also address the need for automated handling systems, which are essential for managing the complexities of larger wafer production.
Interplay Between Wafer Size and SiC Wafer Boats
Design and Capacity Adjustments for SiC Wafer Boats
The design of SiC wafer boats evolves to meet the demands of varying wafer sizes. As wafer dimensions increase, manufacturers must enhance the structural integrity and capacity of these boats. Larger wafers, such as 300 mm or the emerging 450 mm, require boats with reinforced frameworks to support their weight and surface area. This adjustment ensures that the wafers remain stable during high-temperature processes, reducing the risk of damage or misalignment.
SiC wafer boats for smaller wafers, like 200 mm, prioritize compactness and cost-efficiency. These boats cater to specialized applications where smaller wafers dominate. In contrast, boats designed for larger wafers focus on maximizing throughput and maintaining precision. For instance, the grooves or slots in these boats must align perfectly with the wafer’s dimensions to ensure uniform processing. This precision becomes even more critical as wafer sizes grow, demanding advanced engineering solutions.
The increasing adoption of SiC-based semiconductors has further driven innovation in wafer boat design. SiC wafer boats now incorporate features like enhanced thermal stability and chemical resistance, which are essential for handling larger wafers in complex manufacturing environments. These advancements not only improve the boats’ performance but also extend their operational lifespan, offering manufacturers a cost-effective solution for high-volume production.
"The evolution of SiC wafer boats reflects the industry’s commitment to optimizing semiconductor manufacturing processes," as highlighted in market analyses.
Efficiency and Optimization in Manufacturing
The interplay between wafer size and SiC wafer boats significantly impacts manufacturing efficiency. Larger wafers, when paired with well-designed SiC wafer boats, enable manufacturers to process more chips per production cycle. This synergy reduces downtime and increases throughput, making high-volume production more feasible. For example, a 300 mm wafer, supported by a robust SiC wafer boat, can accommodate more chips than a 200 mm wafer, streamlining the entire manufacturing process.
SiC wafer boats contribute to optimization by ensuring precise wafer alignment and stability. Their superior thermal conductivity and mechanical strength minimize the risk of defects during high-temperature treatments. This reliability enhances yield rates, which is crucial for maintaining cost-effectiveness in semiconductor production. Additionally, the chemical resistance of SiC material protects the wafers from contamination, further improving product quality.
The transition to larger wafers, such as 450 mm, presents new opportunities for efficiency gains. However, it also introduces challenges that require innovative solutions. SiC wafer boat manufacturers must develop designs that can handle the increased size and weight of these wafers without compromising performance. Automated handling systems, integrated with advanced SiC wafer boats, are emerging as a key solution to address these challenges. These systems ensure seamless operations, reducing manual intervention and the associated risks of errors.
"SiC wafer boats play a pivotal role in achieving efficiency and optimization in semiconductor manufacturing," as noted in industry reports.
Industry Trends and Recommendations
Trends in Wafer Size and SiC Wafer Boat Usage
The semiconductor industry continues to witness a steady evolution in wafer sizes, driven by the demand for higher production efficiency and advanced semiconductor devices. Historically, 200 mm wafers dominated the market, serving as the standard for many fabrication facilities. However, the transition to 300 mm wafers has become widespread due to their ability to significantly reduce the cost per die and increase throughput. This shift aligns with the industry’s focus on optimizing manufacturing processes to meet growing consumer and industrial demands.
The push for larger wafers, such as 450 mm, represents the next frontier in semiconductor manufacturing. These wafers promise unparalleled efficiency gains, enabling manufacturers to produce more chips per wafer while reducing material waste. However, the adoption of 450 mm wafers introduces several challenges. Facilities must invest in advanced equipment, including vertical furnaces and automated wafer transport systems, to handle the increased size and weight. Additionally, the structural integrity of these larger wafers requires innovative solutions to prevent warping and deformation during production.
The role of the sic wafer boat has also evolved alongside these trends. As wafer sizes increase, manufacturers have developed wafer boats with enhanced structural strength and thermal stability. These advancements ensure that larger wafers remain secure and aligned during high-temperature processes. The integration of automated handling systems with SiC wafer boats further supports the industry’s move toward larger wafer sizes, streamlining operations and minimizing human error.
"The increasing size of silicon wafers is one of the most obvious trends in silicon material technology," as noted in technical analyses. This trend underscores the industry’s commitment to innovation and efficiency.
Wafer size profoundly influences production efficiency by shaping throughput, yield, and cost dynamics. Larger wafers enable higher chip output per cycle, while smaller wafers cater to specialized applications. SiC wafer boats remain indispensable in this process, ensuring the safe handling and precise alignment of wafers during manufacturing. Their evolving designs accommodate varying wafer sizes, enhancing operational stability and efficiency. Manufacturers must prioritize the synergy between wafer size and SiC wafer boats to optimize production processes. This focus will drive innovation, improve cost-effectiveness, and maintain competitiveness in the rapidly advancing semiconductor industry.
FAQ
What are the factors to consider when determining wafer sizes for semiconductor devices?
Manufacturers evaluate several factors when selecting wafer sizes. These include production costs, yield rates, and overall efficiency. Larger wafers often reduce the cost per chip, but they require significant investment in advanced equipment. The impact on the semiconductor industry also plays a role, as larger wafers can drive innovation and meet growing market demands.
How are wafer sizes described in the current market?
Wafer sizes are typically measured in millimeters, reflecting their diameter. Common sizes include 200 mm, 300 mm, and the emerging 450 mm wafers. Companies may also request custom sizes to meet specific production requirements.
What are the challenges presented by the increasing size of silicon wafers?
Larger silicon wafers introduce several challenges. These include the need for new equipment capable of handling increased weight and size. Manufacturers must also develop advanced patterning techniques and thicker wafers to maintain structural integrity. Automated transport systems become essential to manage the heavier wafers efficiently.
What is the primary use of 12-inch silicon wafers?
The 12-inch (300 mm) silicon wafers dominate high-volume production. They are primarily used for memory chips and products like personal computers and mobile phones. Their larger surface area supports precision processes, making them ideal for these applications.
What are the common sizes of wafers used in electronics?
Electronics manufacturing commonly uses wafers ranging from 100 mm to 450 mm in diameter. The 200 mm and 300 mm wafers remain the most widely adopted sizes. Although 450 mm wafers promise greater efficiency, they are not yet in general use due to technical and financial barriers.
How has the wafer diameter changed over time?
The semiconductor industry has seen a steady increase in wafer diameters. The 300 mm wafer has become the standard for high-volume production. Research continues to focus on making 450 mm wafers more practical, aiming to further enhance efficiency and reduce costs.
What is the significance of silicon carbide (SiC) wafer boats in the semiconductor industry?
SiC wafer boats play a critical role in semiconductor manufacturing. They securely hold and transport wafers during high-temperature processes, ensuring stability and precision. Their exceptional thermal and chemical properties contribute to consistent quality and reliability in production.
Why are automated systems important for larger wafers?
Larger wafers, such as 450 mm, require automated systems for efficient handling. These systems reduce the risk of human error and ensure precise alignment during production. Automation also addresses the challenges posed by the increased weight and size of larger wafers.
What advantages do larger wafers offer in semiconductor manufacturing?
Larger wafers, like 300 mm and 450 mm, allow manufacturers to produce more chips per wafer. This reduces the cost per die and increases throughput. They also minimize material waste, making them a cost-effective choice for high-volume production.
Are 450 mm wafers expected to become the industry standard?
While 450 mm wafers promise significant efficiency gains, their adoption faces challenges. High equipment costs and the need for process redesigns have slowed their widespread use. However, ongoing research and development aim to overcome these obstacles, paving the way for future implementation.