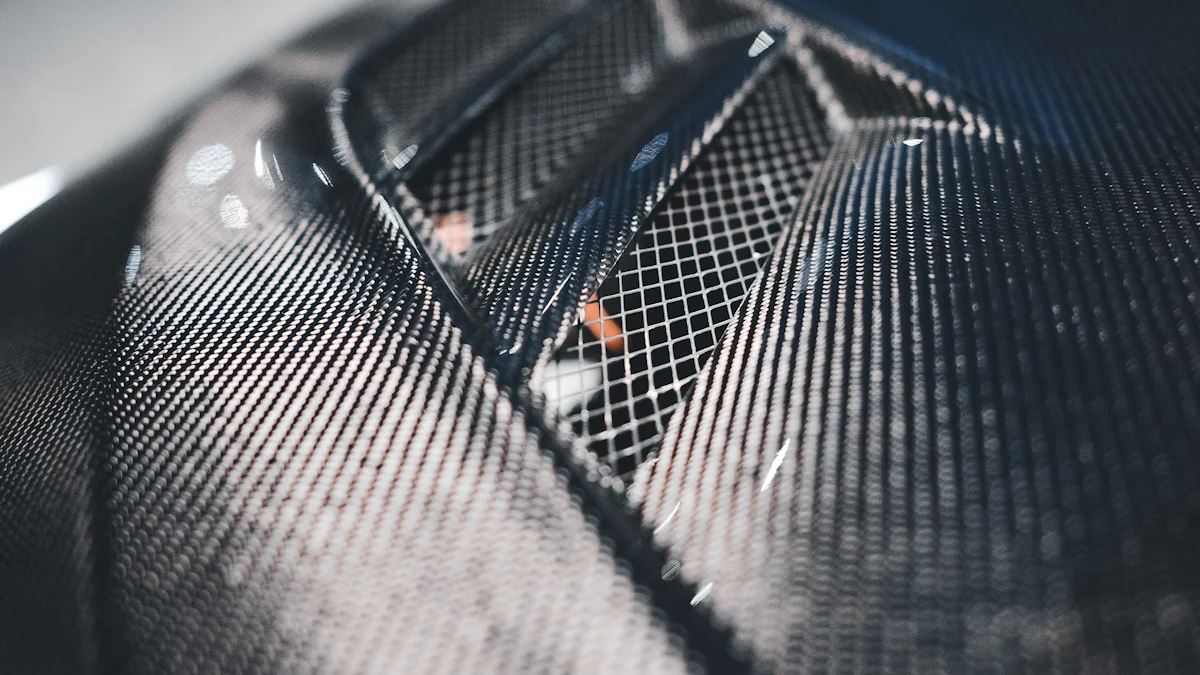
Carbon-carbon composites are transforming industries with their outstanding properties. These advanced materials, including carbon fiber carbon plate options, offer a combination of high strength, lightweight structure, and exceptional heat resistance, making them essential for high-performance uses. Industries such as aerospace and automotive heavily depend on them for critical components. For example, the market is expected to grow from 1.92billionin2023to1.92 billion in 2023 to 1.92billionin2023to3.4 billion by 2032, fueled by the increasing demand for advanced materials. The unique characteristics of carbon-carbon composites, such as low thermal expansion and high fatigue resistance, make them perfect for extreme environments. From aircraft to electric vehicles, carbon-carbon composites applications are continually evolving, highlighting their versatility and cutting-edge innovation.
Key Takeaways
- Carbon-carbon composites are revolutionizing industries with their lightweight, high-strength, and heat-resistant properties, making them essential for aerospace and automotive applications.
- Each type of carbon-carbon composite—2D, 2.5D, 3D, and 4D—has unique fiber orientations and structures that cater to specific performance needs, enhancing their versatility in extreme environments.
- Innovative production methods, including advanced 3D printing and integration of carbon nanotubes, allow for the creation of complex shapes and improved mechanical properties, driving advancements in engineering and technology.
2D Carbon Carbon Composites
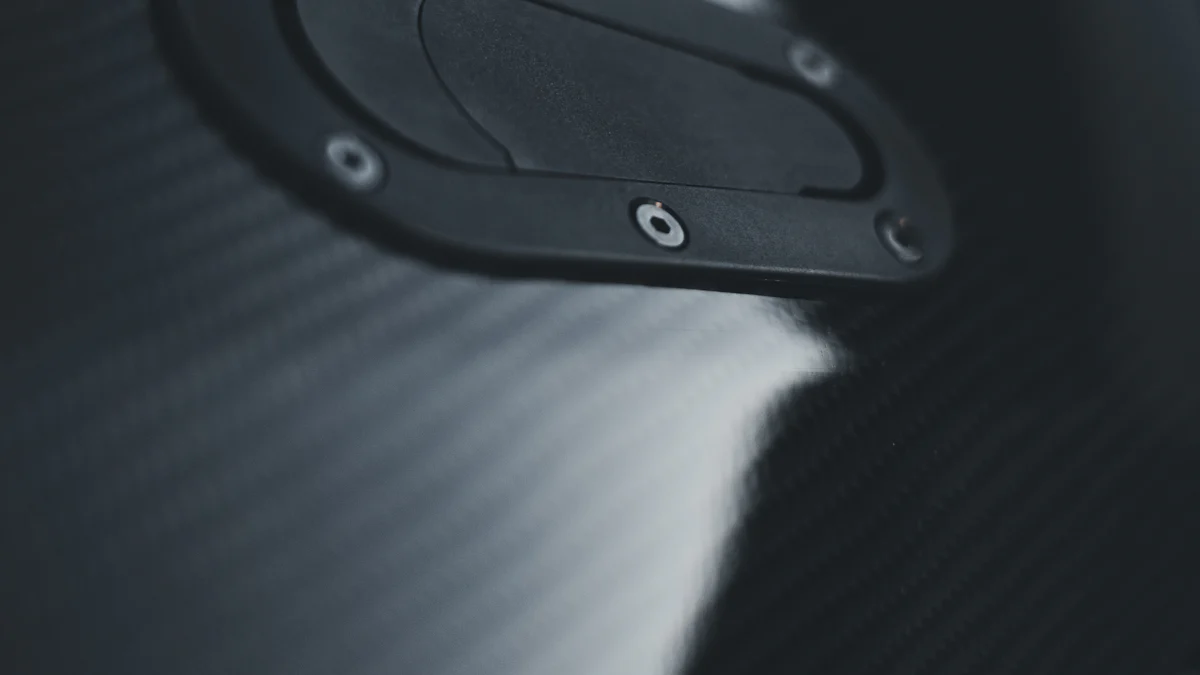
Structure and Fiber Orientation
The fibers in these composites are arranged in two primary directions: x and y, forming a flat plane. This orientation gives them excellent in-plane strength and stiffness. Manufacturers typically use carbon fiber cloths, layering them together to create the composite. Common products include carbon composite boards, sheets, and profiles, which are often used in heaters and other high-performance applications. This straightforward structure makes 2D composites a reliable choice for many industries.
Production Methods
The production of 2D carbon carbon composites involves several methods, each tailored to specific needs. Here’s a quick overview:
Production Method | Description |
---|---|
Open Molding | Hand layup or spray-up techniques apply resin and fiber into a mold. |
Hand Layup and Vacuum Bagging | Layers of carbon fiber fabric or prepreg sheets are placed by hand onto a mold with resin applied. |
Resin-Infused Carbon Fiber Fabrication | Processes like Resin-transfer molding (RTM) and Vacuum-assisted resin transfer molding (VARTM). |
High-Volume Molding Methods | Compression molding and injection molding for large-scale production. |
Other High-Volume Methods | Includes tube rolling, filament winding, pultrusion, automated fiber placement (AFP), and automated tape laying (ATL). |
These methods ensure the composites meet the demands of various industries, from small-scale custom projects to high-volume manufacturing.
Applications in Aerospace and Energy
Their lightweight and heat-resistant properties make them ideal for aircraft components, such as brake discs and thermal shields. In the energy industry, they are used in high-temperature environments like furnaces and reactors. These composites also help improve efficiency and durability in extreme conditions. Their versatility and reliability continue to drive innovation in these fields.
2.5D Carbon Carbon Composites
Structure and Fiber Orientation
Unlike 2D composites, which have fibers in two directions, and 3D composites, which distribute fibers evenly in all three dimensions, 2.5D composites take a different approach. Their fibers are arranged in three directions, but the z-direction contains fewer fibers. This design creates a balance between strength and weight, making them ideal for applications requiring moderate out-of-plane strength without the complexity of full 3D composites. The reduced fiber density in the z-direction also helps lower production costs while maintaining excellent performance.
Production Methods
The production of involves cutting-edge techniques. One advanced method integrates carbon nanotubes (CNTs) into additive manufacturing processes. This process begins by creating a high-density CNT nanocomposite filament using CO2-derived CNTs and thermoplastic PLA polymers as a binder. The filament is then used in 3D printing to form intricate carbon structures. After printing, thermal treatment removes the binder, leaving behind a robust carbon scaffold. To enhance mechanical properties, the scaffold is infiltrated with epoxy. This innovative approach allows for high CNT loading and eliminates the need for molds, enabling the fabrication of complex shapes with exceptional structural integrity.
Applications in Automotive and Engineering
It is find extensive use in automotive and engineering industries. Their lightweight and durable nature makes them perfect for components like brake pads, clutch plates, and structural reinforcements. In engineering, they are used in high-stress environments, such as turbine blades and heat exchangers. These composites improve performance and efficiency while reducing wear and tear. Their ability to withstand extreme conditions ensures reliability in critical applications, driving advancements in both fields.
3D Carbon Carbon Composites
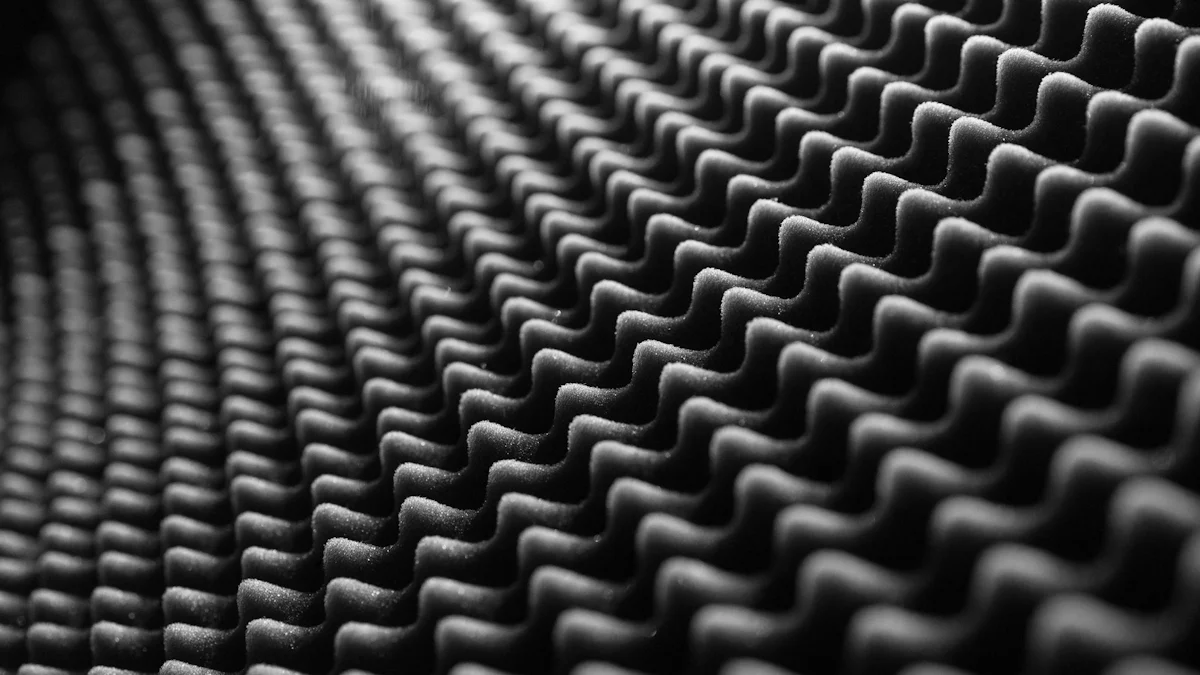
Structure and Fiber Orientation
Are designed with fibers arranged in three distinct directions, creating a robust and versatile structure. These directions—x, y, and z—form what’s known as a 3D xyz structure. Another common design is the 3D hoop structure, where fibers are oriented axially, radially, and in hoop directions. These configurations provide exceptional strength and durability, making them ideal for demanding applications. Beyond these, manufacturers have developed various other 3D structures to meet specific performance needs. This multi-directional fiber arrangement ensures superior mechanical properties, especially in environments requiring high thermal and structural stability.
Production Methods
The production involves innovative techniques that push the boundaries of material science. One cutting-edge method uses CO2-derived carbon nanotubes (CNTs) in additive manufacturing. This process begins with an integrated system that converts CO2 into CNTs using an anion exchange membrane CO2 electrolyzer stack and a thermochemical reactor. The resulting CNTs are then combined with thermoplastic polymers to create high-density nanocomposite filaments. These filaments are used in 3D printing, where the CNTs are aligned to enhance the material’s strength. This approach eliminates the need for molds, allowing for the creation of complex shapes with remarkable precision and durability.
Applications in High-Temperature Environments
3D carbon carbon composites excel in high-temperature environments, making them indispensable in aerospace and defense industries. They are used in missile warhead parts, where they withstand extreme heat and pressure during re-entry. Solid rocket engine nozzles also benefit from these composites, as they improve nozzle efficiency and reduce ignition loss rates. Additionally, space shuttles rely on these materials for thermal protection during re-entry, ensuring the safety and integrity of the spacecraft. Their ability to perform under such intense conditions highlights their critical role in advancing high-performance technologies.
4D Carbon Carbon Composites
Structure and Fiber Orientation
Stand out due to their advanced fiber arrangement. Their structure incorporates one or two additional fibers in the plane direction, setting them apart from the other types. This unique orientation enhances their strength and durability, making them suitable for demanding applications. Unlike 2D, 2.5D, or 3D composites, the weaving methods used for 4D composites allow for greater adaptability in density and properties. These features make them a top choice for extreme environments where reliability is critical.
Production Methods
The production involves innovative techniques that ensure precision and performance. The process begins with 3D printing using the Carbon DLS method and EPX 82 material. This step creates a semi-rigid, partially cured part. Next, the part is combined with pre-impregnated fiber reinforcement, which enhances its structural integrity. Finally, the assembly undergoes thermal curing in an oven. This step activates a chemical reaction that bonds the materials permanently, resulting in a void-free and highly durable composite. These advanced methods allow manufacturers to create complex shapes with exceptional strength.
Applications in Dynamic and Adaptive Systems
Excel in dynamic and adaptive systems due to their superior properties. Their unique fiber orientation and weaving methods make them ideal for components exposed to extreme heat, such as rocket nozzles and thermal protection systems for re-entry vehicles. They also play a crucial role in high-performance braking systems, clutches, and structural components. These composites adapt to various applications, showcasing their versatility in modern engineering. Their ability to withstand harsh conditions ensures reliability in critical systems, driving innovation across industries.
Carbon carbon composites—2D, 2.5D, 3D, and 4D—each bring unique strengths to the table. Their differences in fiber orientation and structure make them suitable for a wide range of applications.
Type | Structure Description | Applications |
---|---|---|
2D | Fibers in two directions (x, y), produced by layering carbon fiber cloths. | Carbon composite boards, sheets, U, L profiles. |
2.5D | Similar to 2D but with some fibers between layers, providing a third direction (z). | Enhanced structural applications. |
3D | Fibers in three directions (x, y, z), known as 3D xyz structure. | Complex structural components. |
4D | 3D structure with additional fibers in the plane direction, customizable. | Specialized products based on customer needs. |
These composites are revolutionizing industries by offering lightweight, durable, and heat-resistant solutions. Their adaptability allows engineers to meet specific design needs, from aerospace to automotive. As industries push for innovation, these materials will continue to play a critical role in building a sustainable and advanced future.
FAQ
What makes carbon-carbon composites unique?
Carbon-carbon composites combine lightweight properties with high strength and heat resistance. They perform exceptionally well in extreme environments, making them ideal for aerospace and automotive industries.
How do 2D and 3D carbon-carbon composites differ?
2D composites have fibers in two directions, while 3D composites include fibers in three directions. This difference gives 3D composites superior strength and durability.
Can carbon-carbon composites be customized?
Yes! Manufacturers can tailor fiber orientation and density to meet specific performance needs, ensuring the material fits unique applications like thermal shields or structural reinforcements.