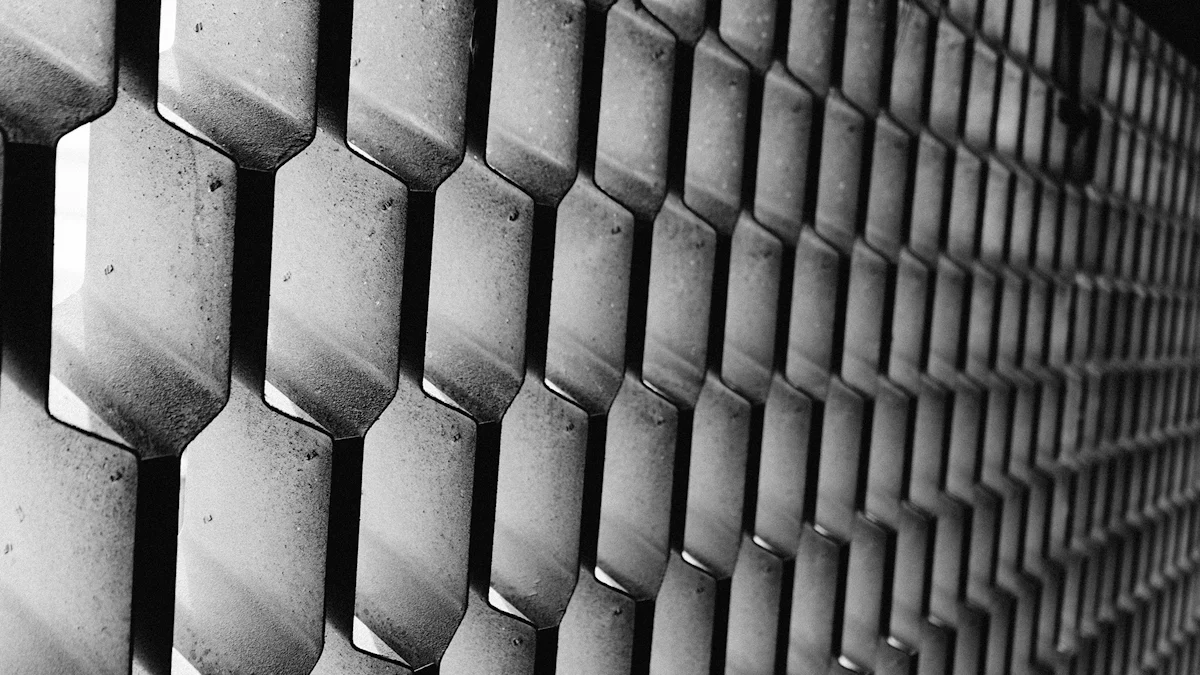
Carbon-carbon (CC) material stands out as a revolutionary composite known for its exceptional strength, thermal resistance, and lightweight nature. It combines carbon fibers with a carbon matrix, creating a material capable of withstanding extreme temperatures and mechanical stress. The C/C composite is particularly notable for its high-temperature stability and superior thermal conductivity. On the other hand, carbon fiber, a closely related material, is renowned for its high tensile strength and stiffness, making it indispensable in industries like aerospace and automotive. Understanding the differences between carbon composite vs carbon fiber is crucial for industries seeking optimal performance and durability in advanced applications. Additionally, the carbon-carbon composite manufacturing process involves carbonizing plastic into carbon through high-temperature firing and heat treatment, which enhances the c/sic material properties and overall performance of the composite.
Key Takeaways
- Carbon-carbon materials excel in extreme heat environments, withstanding temperatures over 1,000ºC, making them ideal for aerospace and defense applications.
- The unique structure of carbon-carbon composites, combining carbon fibers with a carbon matrix, provides exceptional strength, thermal resistance, and chemical stability.
- Carbon fiber is renowned for its lightweight and high tensile strength, making it a preferred choice in automotive and aerospace industries where weight reduction is critical.
- Understanding the differences between carbon-carbon materials and carbon fiber is essential for selecting the right material for specific applications, ensuring optimal performance and durability.
- The production processes for both materials are complex, with carbon-carbon requiring high-temperature treatments to enhance its properties, while carbon fiber involves spinning and carbonization of organic polymers.
- Both materials are revolutionizing their respective industries, with carbon-carbon being used in high-performance applications like rocket nozzles and carbon fiber enhancing sports equipment and automotive components.
What is Carbon-Carbon (CC) Material?
Composition and Structure of Carbon-Carbon Material
Carbon-carbon (CC) material consists of carbon fibers embedded within a carbon matrix. This unique structure gives it remarkable strength and thermal stability. The carbon fibers act as the reinforcement, while the carbon matrix binds the fibers together, creating a composite that performs exceptionally well under extreme conditions. Unlike traditional composites that use polymer matrices, CC materials rely entirely on carbon, which enhances their ability to withstand high temperatures and mechanical stress.
The material’s low density makes it lighter than metals, yet it offers tensile strength that is 7-9 times greater than steel. This combination of lightweight and strength makes CC materials ideal for demanding applications. Additionally, CC materials exhibit a low coefficient of thermal expansion, meaning they maintain their shape and size even when exposed to significant temperature changes. Their resistance to acids, alkalis, and salts further adds to their versatility in various environments.
Production Process of Carbon-Carbon Material
The production of carbon-carbon material involves several intricate steps. Manufacturers begin by arranging carbon fibers into the desired shape or structure. These fibers are then impregnated with a resin or pitch, which acts as a precursor for the carbon matrix. The next step involves carbonizing the material through high-temperature firing. This process removes non-carbon elements, leaving behind a carbon-rich structure.
To enhance the material’s properties, the composite undergoes additional heat treatments at temperatures exceeding 1,000ºC. This step increases the carbon content to over 99%, improving its mechanical strength and thermal resistance. In some cases, the material may also receive coatings or surface treatments to protect it from oxidation in high-temperature, oxygen-rich environments. This meticulous production process ensures that CC materials achieve their exceptional performance characteristics.
Key Properties of Carbon-Carbon Material
Carbon-carbon materials boast a range of impressive properties that make them stand out in advanced applications:
- High Strength and Stiffness: CC materials offer excellent mechanical strength and stiffness, making them suitable for structural applications under extreme stress.
- Thermal Resistance: They can withstand temperatures exceeding 1,000ºC without losing their integrity, making them ideal for high-temperature environments.
- Thermal Shock Resistance: CC materials handle rapid temperature changes without cracking or deforming, ensuring reliability in dynamic conditions.
- Low Density: Their lightweight nature reduces the overall weight of components, which is crucial in industries like aerospace and defense.
- Chemical Stability: These materials resist acids, bases, and salts, allowing them to perform well in chemically aggressive environments.
- Low Coefficient of Thermal Expansion: CC materials maintain dimensional stability, even under extreme heat, ensuring precision in critical applications.
These properties make carbon-carbon materials indispensable in industries requiring high-performance solutions. From aerospace components like turbine engine leading edges and rocket nozzles to industrial applications, CC materials continue to push the boundaries of what advanced materials can achieve.
What is Carbon Fiber?
Composition and Structure of Carbon Fiber
Carbon fiber is a material made up of thin, strong crystalline filaments of carbon atoms. These filaments are bundled together to form a thread-like structure, which can then be woven into fabrics or combined with other materials to create composites. The atomic structure of carbon fiber resembles a tightly packed chain of carbon atoms, giving it exceptional strength and stiffness.
The fibers themselves are incredibly lightweight, yet they possess a tensile strength that surpasses many metals, including steel. This unique combination of properties makes carbon fiber a go-to material for industries that demand high performance. Additionally, carbon fiber exhibits low thermal expansion, meaning it maintains its shape and size even when exposed to temperature fluctuations. This stability ensures precision in applications where accuracy is critical.
Production Process of Carbon Fiber
The production of carbon fiber involves a meticulous process that transforms organic polymers into high-strength filaments. Here’s a simplified breakdown of the steps:
- Spinning: Manufacturers begin by spinning a polymer, such as polyacrylonitrile (PAN), into long strands. These strands serve as the precursor material for carbon fiber.
- Stabilization: The strands are then heated in an oxygen-rich environment to stabilize their molecular structure. This step prevents the fibers from melting during the next stages.
- Carbonization: The stabilized fibers are exposed to extremely high temperatures, often exceeding 1,000ºC, in an oxygen-free environment. This process removes non-carbon elements, leaving behind pure carbon filaments.
- Surface Treatment: To improve bonding with resins or other materials, the fibers undergo surface treatment. This step enhances the compatibility of carbon fiber with composite matrices.
- Sizing: Finally, a protective coating is applied to the fibers to prevent damage during handling and to make them easier to weave or mold.
This process results in a material that is not only lightweight but also incredibly strong and durable. Advances in production techniques, such as those identified by the Carbon Fiber Technology Facility (CFTF), continue to lower costs and expand the accessibility of carbon fiber for various industries.
Key Properties of Carbon Fiber
Carbon fiber stands out due to its remarkable properties, which make it a preferred choice for high-performance applications:
- High Tensile Strength: Carbon fiber can withstand significant pulling forces without breaking, making it ideal for structural components.
- Lightweight: Despite its strength, carbon fiber is much lighter than traditional materials like steel or aluminum, reducing overall weight in applications like aerospace and automotive.
- Stiffness: Its rigidity ensures that components maintain their shape under stress, which is crucial for precision engineering.
- Low Thermal Expansion: Carbon fiber resists changes in size or shape when exposed to heat, ensuring stability in temperature-sensitive environments.
- Durability: The material resists wear and tear, making it reliable for long-term use in demanding conditions.
- Corrosion Resistance: Unlike metals, carbon fiber does not rust or corrode, even in harsh environments.
These properties explain why carbon fiber is widely used in industries such as aerospace, automotive, and sports equipment. For example, its application in racing car bodywork and aircraft components highlights its ability to deliver both strength and weight savings. Additionally, innovations like fire-retardant carbon fiber materials further expand its versatility, ensuring safety in applications where fire resistance is essential.
Carbon fiber continues to revolutionize modern engineering, offering a blend of strength, lightness, and reliability that few materials can match.
Carbon Composite vs Carbon Fiber: Key Differences
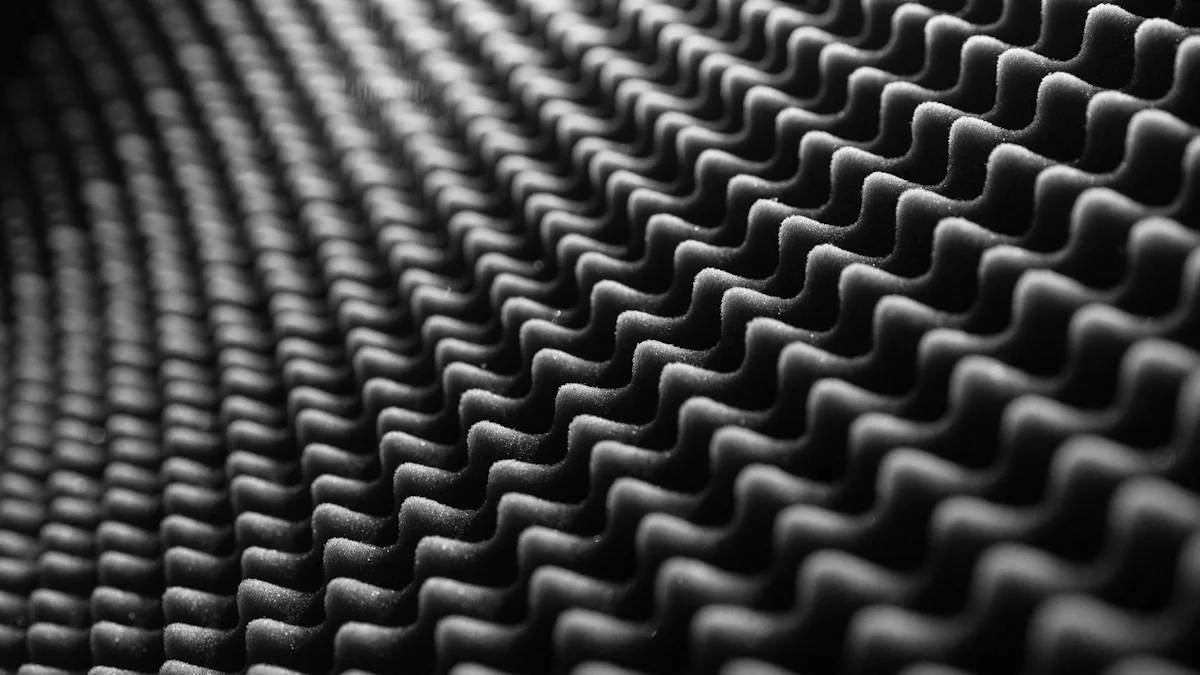
When comparing carbon composite vs carbon fiber, it’s essential to understand how their unique characteristics influence their performance in various applications. Let’s break down the key differences between these two advanced materials.
Strength and Durability
Both carbon composites and carbon fiber are celebrated for their strength, but they excel in different ways. Carbon fiber, as a standalone material, offers exceptional tensile strength. It is up to ten times stronger than steel and twice as stiff, making it a top choice for applications requiring high strength-to-weight ratios. This strength allows it to endure significant pulling forces without breaking, which is why it’s often used in aerospace and automotive industries.
Carbon composites, on the other hand, combine carbon fiber with a matrix material, such as resin or carbon. This combination enhances durability and provides additional structural integrity. For instance, carbon-carbon composites (a type of carbon composite) exhibit superior toughness and can withstand extreme mechanical stress. They also resist wear and tear over time, making them ideal for long-term use in demanding environments. While carbon fiber alone is strong, carbon composites take durability to the next level by integrating the fibers into a reinforced structure.
Thermal Resistance
Thermal resistance is another area where these materials differ significantly. Carbon fiber performs well under moderate heat conditions, maintaining its shape and strength even when exposed to temperature fluctuations. However, it has limitations when subjected to extremely high temperatures.
Carbon composites, particularly carbon-carbon materials, excel in high-temperature environments. They can withstand temperatures exceeding 1,000ºC without losing their structural integrity. This makes them indispensable in industries like aerospace, where components must endure intense heat during operation. For example, carbon-carbon composites are often used in rocket nozzles and turbine engine parts due to their ability to handle thermal stress. In contrast, carbon fiber composites with polymer matrices may degrade at much lower temperatures, limiting their use in ultra-high-temperature applications.
Cost and Production Complexity
The cost and complexity of production also set these materials apart. Carbon fiber production involves a meticulous process, including spinning, stabilization, and carbonization, which requires specialized equipment and expertise. This makes carbon fiber relatively expensive compared to traditional materials like steel or aluminum. Additionally, the labor-intensive nature of weaving or molding carbon fiber into desired shapes adds to its cost.
Carbon composites, especially carbon-carbon materials, involve even more intricate manufacturing processes. The production includes multiple stages of heat treatment and carbonization to achieve the desired properties. These additional steps increase both the time and cost of production. However, the enhanced performance of carbon composites often justifies the higher price in applications where strength, durability, and thermal resistance are critical.
Weight and Flexibility
Weight and flexibility play a significant role in determining the suitability of materials for various applications. Carbon fiber and carbon-carbon materials both excel in these areas, but they do so in distinct ways.
Carbon fiber is renowned for its lightweight nature. It weighs about two-thirds less than steel while offering superior strength. This makes it a top choice for industries like aerospace and automotive, where reducing weight can improve fuel efficiency and performance. For example, carbon fiber is often used in aircraft components and racing car bodywork to achieve high strength without adding unnecessary bulk. Its low density ensures that structures remain light, even when designed for heavy-duty use.
Carbon-carbon materials, while also lightweight, bring additional advantages in terms of flexibility. The unique combination of carbon fibers and a carbon matrix allows these materials to maintain structural integrity under stress while adapting to dynamic conditions. This flexibility makes carbon-carbon composites ideal for applications requiring both strength and adaptability, such as turbine engine parts or rocket nozzles. Unlike traditional materials, they can handle mechanical stress without cracking or deforming.
When comparing carbon composite vs carbon fiber, flexibility becomes a key differentiator. Carbon fiber, though strong, tends to be more rigid. Its stiffness ensures precision in applications like sports equipment or construction, where maintaining shape is critical. On the other hand, carbon-carbon composites offer a balance of strength and flexibility, making them better suited for environments with fluctuating forces or temperatures.
Applications of Carbon-Carbon Material
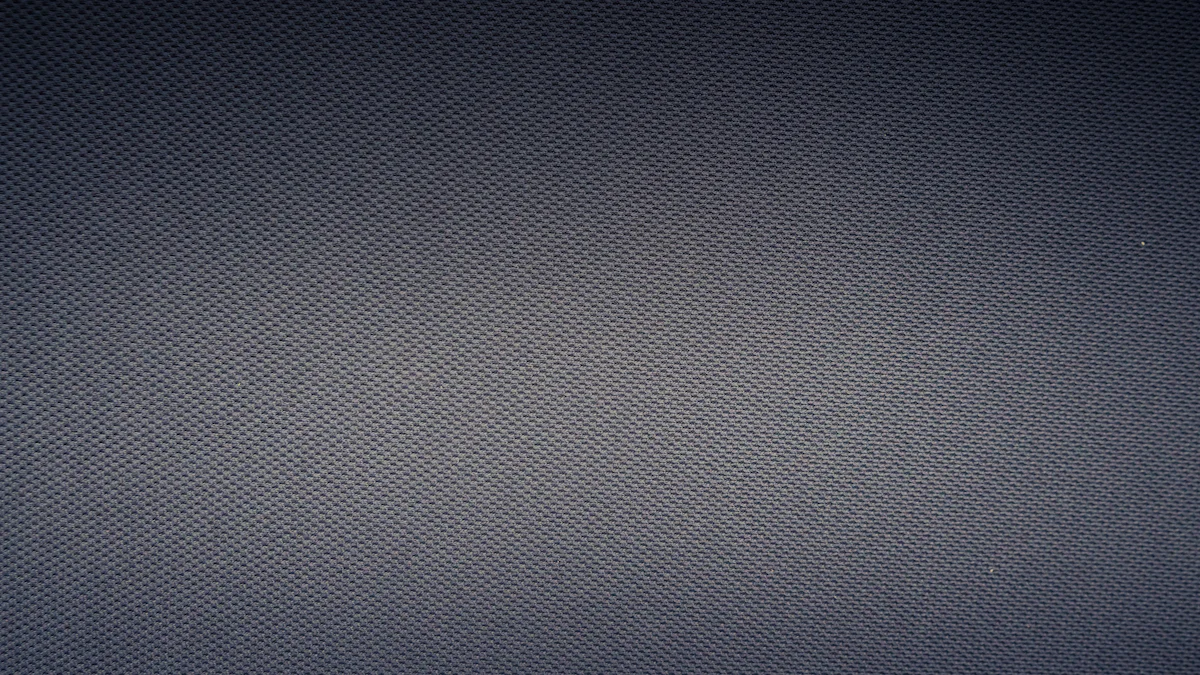
Aerospace and Defense
Carbon-carbon materials play a vital role in aerospace and defense industries. Their ability to withstand extreme temperatures and mechanical stress makes them indispensable for high-performance applications. For instance, airplane braking systems rely on carbon-carbon composites due to their exceptional thermal resistance and durability. These materials ensure reliable performance during rapid deceleration, even under intense heat.
In space exploration, rocket nozzles and re-entry vehicle heat shields utilize carbon-carbon composites. These components face extreme thermal and mechanical conditions during launch and atmospheric re-entry. The high-temperature stability of carbon-carbon materials ensures that these critical parts maintain their integrity and functionality. Additionally, their lightweight nature reduces the overall mass of spacecraft, improving fuel efficiency and payload capacity.
The defense sector also benefits from carbon-carbon materials. Advanced carbon composites provide the strength, endurance, and stability required for military applications. From missile components to protective armor, these materials enhance performance while maintaining a lightweight profile. Their superior thermal conductivity and chemical stability further solidify their importance in this field.
Industrial and Energy Sectors
Carbon-carbon materials have revolutionized industrial and energy applications. Their unique properties make them ideal for environments requiring high strength and thermal resistance. In the energy sector, turbine engine components often incorporate carbon-carbon composites. These materials handle the intense heat and mechanical stress generated during operation, ensuring efficiency and longevity.
In manufacturing, carbon-carbon materials are used in furnace linings and heat treatment fixtures. Their ability to withstand temperatures exceeding 1,000ºC without deformation makes them perfect for high-temperature processes. Additionally, their low thermal expansion ensures dimensional stability, which is crucial for precision manufacturing.
The chemical industry also benefits from carbon-carbon materials. Their resistance to acids, alkalis, and salts allows them to perform well in corrosive environments. For example, they are used in chemical reactors and heat exchangers, where durability and thermal conductivity are essential. These materials not only improve performance but also reduce maintenance costs, making them a cost-effective solution for industrial applications.
Medical and Specialized Uses
The medical field has embraced carbon-carbon materials for their unique combination of strength, lightness, and biocompatibility. In specialized surgical tools and implants, these materials offer durability and precision. For instance, carbon-carbon composites are used in prosthetics and orthopedic devices, providing patients with lightweight yet strong solutions that enhance mobility and comfort.
In addition to medical applications, carbon-carbon materials find use in niche industries requiring advanced performance. For example, they are employed in nuclear reactors due to their ability to withstand radiation and extreme heat. Their chemical stability and thermal resistance make them a reliable choice for such critical environments.
Furthermore, carbon-carbon materials support research and development in cutting-edge technologies. From semiconductor manufacturing to new energy solutions, these materials enable innovation by offering unmatched performance in demanding conditions. Their versatility and reliability continue to push the boundaries of what is possible in modern industries.
Applications of Carbon Fiber
Automotive and Aerospace Industries
Carbon fiber has transformed the automotive and aerospace industries with its lightweight and high-strength properties. In the automotive sector, manufacturers use carbon fiber to create lighter vehicles that improve fuel efficiency and performance. Components like car hoods, roofs, and body panels benefit from this material’s strength-to-weight ratio. High-performance sports cars often feature carbon fiber parts to enhance speed and agility without compromising durability.
In aerospace, carbon fiber plays a critical role in aircraft design. Engineers rely on it to reduce the weight of airplanes while maintaining structural integrity. Aircraft wings, fuselages, and tail sections often incorporate carbon fiber to ensure safety and efficiency during flight. Its stiffness and resistance to fatigue make it ideal for handling the stresses of high-altitude travel. Additionally, spacecraft components, such as satellite structures, use carbon fiber to withstand the harsh conditions of space while minimizing launch weight.
Sports and Recreation
The sports and recreation industry has embraced carbon fiber for its ability to enhance performance and durability. Athletes and enthusiasts benefit from equipment made with this advanced material. For example, bicycles with carbon fiber frames offer a perfect balance of strength and lightness, allowing riders to achieve greater speed and control. Golf clubs, tennis rackets, and fishing rods also utilize carbon fiber to improve precision and reduce weight, giving users a competitive edge.
Water sports equipment, such as paddleboards and kayaks, often features carbon fiber for its resistance to wear and tear. This material ensures that gear remains lightweight yet sturdy, even in challenging environments. Ski poles and snowboards made with carbon fiber provide better flexibility and shock absorption, enhancing the overall experience for winter sports enthusiasts. By combining strength, lightness, and resilience, carbon fiber continues to revolutionize recreational activities.
Construction and Infrastructure
In construction and infrastructure, carbon fiber offers innovative solutions for building stronger and more durable structures. Engineers use carbon fiber to reinforce concrete, bridges, and other load-bearing elements. Its high tensile strength helps prevent cracks and extends the lifespan of these structures. Retrofitting older buildings with carbon fiber sheets or wraps improves their stability and resistance to seismic activity.
Wind energy projects also benefit from carbon fiber’s unique properties. Wind turbine blades made with this material are lighter and more efficient, enabling them to generate more power. In addition, carbon fiber’s corrosion resistance makes it suitable for infrastructure exposed to harsh weather conditions, such as coastal bridges and offshore platforms. By integrating carbon fiber into construction projects, industries can achieve greater sustainability and performance.
Choosing Between Carbon-Carbon Material and Carbon Fiber
Selecting the right material for a project can feel overwhelming, especially when both options offer exceptional performance. Carbon-carbon material and carbon fiber each have unique strengths, making them suitable for different applications. Let’s explore when to choose one over the other.
When to Use Carbon-Carbon Material
Carbon-carbon material shines in environments where extreme heat and mechanical stress are unavoidable. Its ability to withstand temperatures exceeding 1,000ºC without losing structural integrity makes it a top choice for aerospace and defense industries. For example, rocket nozzles and re-entry vehicle heat shields rely on carbon-carbon composites to endure intense thermal and mechanical conditions. Their low density and excellent ablation properties further enhance their suitability for these demanding applications.
Industries requiring materials with high thermal shock resistance also benefit from carbon-carbon composites. Turbine engine components and furnace linings often incorporate this material due to its ability to handle rapid temperature changes without cracking or deforming. Additionally, its chemical stability makes it ideal for use in corrosive environments, such as chemical reactors and heat exchangers.
In short, carbon-carbon material is the go-to option for projects that demand high-temperature stability, thermal conductivity, and durability under extreme conditions. Its unique properties make it indispensable for aerospace, industrial, and energy sectors.
When to Use Carbon Fiber
Carbon fiber excels in applications where weight reduction is critical without compromising strength. Its lightweight nature, combined with high tensile strength, makes it a favorite in industries like automotive and aerospace. For instance, car manufacturers use carbon fiber to create lighter vehicles, improving fuel efficiency and performance. Similarly, aircraft wings and fuselages benefit from carbon fiber’s strength-to-weight ratio, ensuring safety and efficiency during flight.
Sports and recreation industries also take advantage of carbon fiber’s properties. Bicycles, golf clubs, and tennis rackets made with carbon fiber offer enhanced performance due to their lightness and stiffness. These qualities allow athletes to achieve greater speed, precision, and control.
Construction projects often use carbon fiber to reinforce structures like bridges and buildings. Its high tensile strength prevents cracks and extends the lifespan of these structures. Wind turbine blades also incorporate carbon fiber to improve efficiency and durability in harsh weather conditions.
Carbon-carbon materials and carbon fiber each bring unique strengths to the table. Carbon-carbon excels in high-temperature environments, offering unmatched thermal resistance and durability. Carbon fiber, with its lightweight and high tensile strength, shines in applications requiring precision and efficiency. Choosing the right material depends on the specific demands of the project. Together, these materials drive innovation across industries like aerospace, automotive, and energy. By leveraging their complementary properties, industries can achieve breakthroughs in performance, reliability, and sustainability.
FAQ
What is carbon fiber?
Carbon fiber is a material made from thin strands of carbon atoms. These strands are twisted together, much like yarn, and then woven into fabric or combined with other materials to create composites. Known for its lightweight nature and high tensile strength, carbon fiber is incredibly durable and stiff. Industries like aerospace, automotive, and construction rely on it for its ability to deliver strength without adding unnecessary weight.
Where is carbon fiber used?
Carbon fiber finds applications in many industries. In aerospace, it’s used for parts that need to be strong yet lightweight, such as aircraft wings and fuselages. The automotive industry incorporates it into performance parts and body panels to enhance speed and efficiency. Sports equipment, including bicycles, tennis rackets, and fishing rods, benefits from its strength-to-weight ratio. Additionally, modern construction projects use carbon fiber to reinforce buildings and bridges.
How does carbon-carbon material differ from carbon fiber?
Carbon-carbon material combines carbon fibers with a carbon matrix, while carbon fiber is often used with polymer matrices to form composites. Carbon-carbon materials excel in high-temperature environments, withstanding temperatures over 1,000ºC. Carbon fiber, on the other hand, is valued for its lightweight and high tensile strength, making it ideal for applications where weight reduction is critical.
Why is carbon-carbon material used in aerospace?
Carbon-carbon material is perfect for aerospace because of its ability to handle extreme heat and mechanical stress. Components like rocket nozzles and heat shields rely on its high-temperature stability and durability. Its lightweight nature also reduces the overall mass of spacecraft, improving fuel efficiency and payload capacity.
Can carbon fiber replace traditional materials like steel?
Carbon fiber can replace traditional materials like steel in many applications due to its superior strength-to-weight ratio. It is much lighter than steel but offers comparable or even greater strength. This makes it a popular choice in industries like automotive and aerospace, where reducing weight can significantly improve performance and efficiency.
What makes carbon-carbon material unique?
Carbon-carbon material stands out for its ability to withstand extreme temperatures without losing structural integrity. Its combination of carbon fibers and a carbon matrix provides exceptional thermal resistance, mechanical strength, and chemical stability. These properties make it indispensable in industries like aerospace, defense, and energy.
Is carbon fiber environmentally friendly?
Carbon fiber itself is not biodegradable, and its production process requires significant energy. However, its durability and lightweight nature contribute to energy savings in applications like fuel-efficient vehicles and wind turbines. Researchers are also exploring ways to recycle carbon fiber to make it more sustainable.
How does the production process of carbon-carbon material enhance its properties?
The production process of carbon-carbon material involves high-temperature firing and heat treatments. These steps remove non-carbon elements and increase the carbon content to over 99%. This meticulous process enhances the material’s mechanical strength, thermal resistance, and overall performance, making it suitable for demanding applications.
What industries benefit the most from carbon fiber?
Industries like aerospace, automotive, and sports benefit significantly from carbon fiber. Aerospace uses it for lightweight aircraft components. Automotive manufacturers rely on it for performance parts and body panels. Sports equipment, such as bicycles and golf clubs, takes advantage of its strength and lightness to improve user performance.
How do I choose between carbon-carbon material and carbon fiber?
The choice depends on the application. Carbon-carbon material is ideal for environments with extreme heat and mechanical stress, such as aerospace and industrial sectors. Carbon fiber works best in applications requiring lightweight and high tensile strength, like automotive, sports, and construction. Understanding the specific demands of your project will help determine the right material.