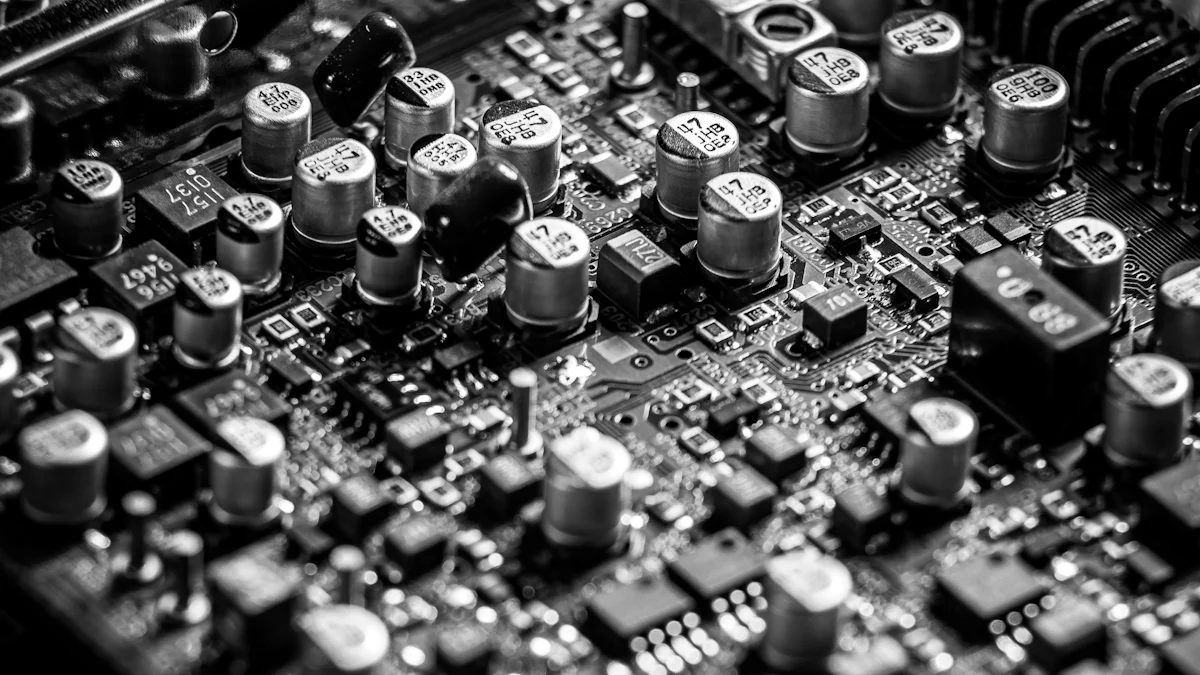
Silicon carbide is reshaping the semiconductor industry with its unmatched efficiency and durability. Its wide bandgap and superior thermal conductivity make it ideal for high-performance applications. Industries like automotive, aerospace, and energy are reaping the benefits. For instance, electric vehicles rely on silicon carbide products for better heat management and voltage resistance. The silicon carbide semiconductor market is booming, projected to grow at a CAGR of 32.6%, reaching $17.2 billion by 2029. With its diverse applications, silicon carbide uses are driving advancements in power electronics, renewable energy, and beyond.
Key Takeaways
- Silicon carbide (SiC) works better than regular silicon. It handles more heat and power.
- SiC helps electric cars use less energy and go farther.
- It keeps devices cool by moving heat away quickly. This stops overheating.
- SiC is important for green energy, making power use 99% efficient.
- It is strong and works well in tough places like space and defense.
- More money is being spent to make SiC easier to get.
- SiC parts are smaller and lighter, improving how systems work.
- As people need it more, SiC will shape future tech and help the planet.
The Unique Properties of Silicon Carbide
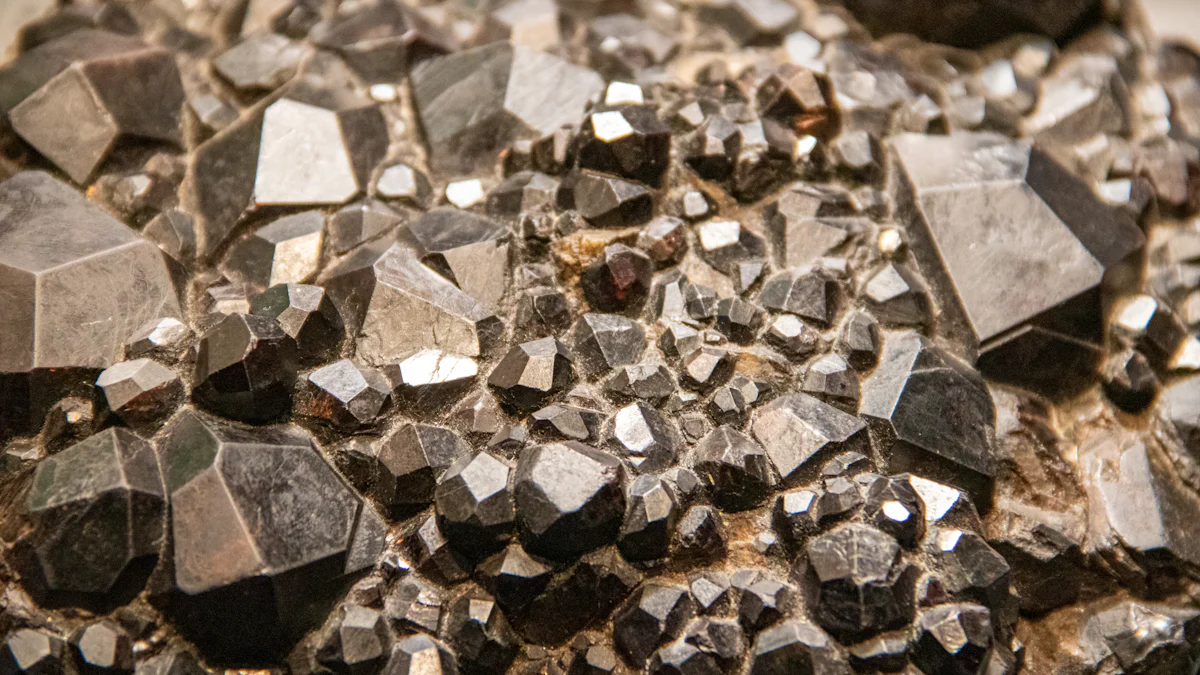
Wide Bandgap and Enhanced Thermal Conductivity
Silicon carbide stands out because of its wide bandgap, measuring about 3.26 eV. This is nearly three times larger than traditional silicon’s 1.12 eV. Why does this matter? A wider bandgap allows silicon carbide to handle higher voltages, frequencies, and temperatures without breaking a sweat. This makes it perfect for high-performance applications like power electronics and electric vehicles.
Its wide bandgap also contributes to its exceptional thermal conductivity. Silicon carbide can efficiently dissipate heat, which is critical for devices operating in high-temperature environments. For example, it can function at temperatures up to 800 degrees Celsius, far beyond what silicon can manage. This property ensures consistent performance and reduces the risk of overheating, even in demanding conditions.
These characteristics make silicon carbide a game-changer in industries where energy efficiency and thermal stability are essential. Whether it’s electric vehicle charging systems or renewable energy converters, silicon carbide uses are paving the way for more reliable and efficient technologies.
High Voltage and Power Handling Capabilities
Silicon carbide excels in high-voltage applications. It can withstand voltages up to 2400 kV/cm, which is significantly higher than silicon’s capacity. This means devices made with silicon carbide can handle more power without the risk of failure. For instance, in electric vehicles, this capability reduces conduction losses and improves energy efficiency, leading to better battery performance and longer driving ranges.
Another advantage is its ability to support higher switching frequencies. This allows for smaller and lighter components in power converters, making designs more compact and cost-effective. Imagine a smaller, more efficient inverter in an electric car or a lightweight power module in a renewable energy system. These are just a few examples of how silicon carbide uses are transforming modern technology.
Durability in Extreme Operating Conditions
Silicon carbide is built to last, even in the harshest environments. Its high strength and resistance to deformation ensure it can handle mechanical stress without losing its structural integrity. This makes it ideal for applications like satellites, where reliability is non-negotiable.
Its low coefficient of thermal expansion minimizes dimensional changes under temperature fluctuations, preserving its performance. Additionally, silicon carbide’s superior chemical inertness protects it from corrosion, making it suitable for use in harsh chemical environments. Whether it’s in aerospace systems or industrial machinery, silicon carbide delivers unmatched durability.
In extreme conditions, such as high radiation or vacuum environments, silicon carbide continues to perform reliably. This durability extends the lifespan of devices, reducing maintenance costs and ensuring consistent operation in critical applications.
Silicon Carbide Uses in Modern Technology
Power Electronics and High-Voltage Applications
Silicon carbide has become a cornerstone in power electronics and high-voltage systems. Its ability to operate at temperatures as high as 400°C—and potentially up to 800°C—makes it a reliable choice for demanding environments. Unlike traditional silicon, silicon carbide tolerates extreme conditions without losing performance. This resilience allows engineers to design systems with smaller heatsinks, reducing overall size and weight.
Devices made with silicon carbide also benefit from its dielectric strength, which is ten times greater than silicon. This enables them to handle higher voltages, making them ideal for applications like charging infrastructure and smart grids. Additionally, silicon carbide enhances power conversion efficiency by maintaining low switching losses, even at high voltages. This feature is particularly valuable in electric vehicles and renewable energy systems, where energy efficiency is critical.
By improving energy utilization and reducing heat generation, silicon carbide uses are transforming power electronics. Whether it’s in photovoltaic systems or wind power converters, this material ensures better performance and reliability.
Electric Vehicles and Charging Systems
Electric vehicles (EVs) are experiencing a revolution, thanks to silicon carbide. This material reduces energy losses in voltage and current, improving thermal efficiency. As a result, EV power components become smaller and lighter, which is a game-changer for vehicle design.
Silicon carbide devices exhibit lower switching and conduction losses, leading to higher efficiency and less wasted energy. Their superior thermal performance helps dissipate heat effectively, ensuring components last longer and perform reliably. For EV manufacturers, this means designing compact systems with increased power density.
Integrating silicon carbide into EV power systems enhances overall vehicle performance. It boosts driving range, allowing EVs to travel farther on a single charge. This addresses one of the biggest concerns for EV buyers—range anxiety.
Charging systems also benefit from silicon carbide’s properties. High power density and reduced heat sink requirements make chargers smaller and more efficient. With faster switching speeds and improved energy conversion, silicon carbide uses are paving the way for a more sustainable and efficient EV ecosystem.
Renewable Energy and Grid Management
Renewable energy systems rely on silicon carbide to maximize efficiency and reliability. For instance, silicon carbide inverters achieve about 99% efficiency, compared to 98% for silicon inverters. This seemingly small difference translates to a 50% reduction in energy loss, which is significant for large-scale solar or wind farms.
Silicon carbide’s ability to withstand temperatures up to 300°C and tolerate nearly ten times the voltage of silicon devices makes it a robust choice for renewable energy applications. Its high thermal conductivity and breakdown voltage improve power conversion systems, reducing energy wastage and enhancing energy utilization.
In grid management, silicon carbide devices offer up to 50% higher power density than traditional silicon. This allows for smaller, more cost-effective components, which is crucial for modernizing energy grids. By enabling more efficient energy storage and distribution, silicon carbide supports the transition to a greener, more sustainable energy future.
Aerospace and Defense Systems
Silicon carbide is making waves in aerospace and defense systems. Its unique properties allow it to thrive in some of the most challenging environments. Engineers and scientists are turning to this material to improve the performance and reliability of critical equipment.
One of the standout features of silicon carbide is its ability to handle extreme temperatures. It can operate at up to 200 degrees Celsius without losing efficiency. This makes it an excellent choice for military ground vehicles and aerospace systems, where heat resistance is essential. For example, silicon carbide-based electronics help aircraft perform better by reducing weight and functioning reliably in harsh conditions. Lighter components mean better fuel efficiency and enhanced maneuverability, which are crucial in both commercial and defense aviation.
Silicon carbide also shines in space applications. Its high melting point and resistance to radiation make it ideal for satellites and missiles. In space, equipment faces strong radiation and vacuum environments that can damage traditional materials. Silicon carbide devices, however, remain reliable under these conditions. They extend the service life of satellites and other critical systems, ensuring consistent performance over time. This durability is a game-changer for missions that require long-term reliability.
Another advantage of silicon carbide is its ability to handle mechanical stress. Aerospace and defense systems often operate in environments with intense vibrations and pressure changes. Silicon carbide’s strength and stability make it a dependable material for these demanding applications. Whether it’s in jet engines or missile guidance systems, this material delivers unmatched performance.
The use of silicon carbide in aerospace and defense doesn’t just improve performance—it also enhances safety. By reducing the risk of overheating and failure, it ensures that critical systems remain operational when they’re needed most. This reliability is vital for both military operations and space exploration.
Silicon carbide uses are transforming the aerospace and defense industries. From improving aircraft efficiency to extending the lifespan of satellites, this material is paving the way for more advanced and reliable technologies. Its ability to perform in extreme conditions makes it an invaluable asset in these high-stakes fields.
Comparing Silicon Carbide and Traditional Silicon
Efficiency and Power Density Advantages
Silicon carbide (SiC) outshines traditional silicon in efficiency and power density. Its unique properties allow it to handle higher voltages, temperatures, and frequencies, making it a superior choice for modern technology.
Here’s how SiC compares to silicon:
- SiC operates at temperatures up to 800°C, far exceeding silicon’s limit of 150°C.
- SiC has a breakdown voltage eight times greater than silicon, enabling it to handle more power without failure.
- SiC’s smaller form factor allows for lighter and more compact designs in electronic devices.
To break it down further:
- SiC’s bandgap energy is 3.26 eV, three times higher than silicon’s 1.12 eV.
- SiC exhibits a ten times higher electrical breakdown field compared to silicon.
- SiC’s thermal conductivity is three times that of silicon, ensuring better heat dissipation.
Property | Silicon Carbide (SiC) | Traditional Silicon |
---|---|---|
Bandgap | 3.26 eV | 1.12 eV |
Thermal Conductivity | Higher | Lower |
Breakdown Voltage | ~300 kV/cm | ~2400 kV/cm |
Operating Temperature | Up to 800 °C | Up to 150 °C |
Switching Frequency | Higher | Lower |
These advantages make SiC the go-to material for applications requiring high efficiency and compact designs, such as electric vehicles and renewable energy systems.
Superior Thermal Management and Heat Dissipation
Thermal management is another area where silicon carbide excels. It can operate at much higher temperatures than silicon, often up to 400°C or more. This capability allows SiC to handle extreme conditions without losing performance.
SiC’s high thermal conductivity also plays a key role. It dissipates heat more effectively, reducing the need for bulky cooling systems. For example:
- SiC can operate at temperatures up to 300°C, compared to silicon’s limit of 175°C.
- Its superior heat tolerance minimizes the need for active cooling systems, which can add weight and complexity to designs.
- Smaller heatsinks can be used with SiC, enhancing overall efficiency in high-performance applications.
This makes SiC ideal for industries like aerospace and power electronics, where managing heat is critical. Its ability to tolerate extreme heat ensures consistent performance, even in demanding environments.
Reliability in Harsh Environments
Silicon carbide’s durability sets it apart from traditional silicon. It thrives in harsh environments where silicon would fail. SiC’s high melting point and resistance to thermal stress make it a reliable choice for extreme conditions.
For instance, SiC performs well in high-radiation and vacuum environments, making it perfect for aerospace and defense applications. Its low leakage current at high voltages also reduces the impact of thermal effects, ensuring stable performance.
Additionally, SiC’s mechanical strength allows it to withstand intense vibrations and pressure changes. This makes it a dependable material for critical systems like satellites and industrial machinery.
By combining durability with efficiency, silicon carbide ensures long-lasting performance in even the toughest conditions. It’s no wonder industries are rapidly adopting this revolutionary material.
Cost and Scalability Considerations
Silicon carbide (SiC) offers incredible advantages, but its cost and scalability present unique challenges. While industries are eager to adopt SiC, its production process remains more expensive and complex compared to traditional silicon. Let’s break this down.
The production of SiC involves intricate processes that drive up costs. Growing high-quality SiC crystals takes time and requires advanced technology. This slow growth rate limits the availability of SiC wafers, making them pricier than silicon. In contrast, traditional silicon benefits from decades of refinement, resulting in faster and more efficient manufacturing.
Here’s a quick comparison of the challenges:
Challenge Type | Silicon Carbide (SiC) | Traditional Silicon |
---|---|---|
Production Cost | Higher due to complex processes | Lower and more efficient |
Manufacturing Process | Complex and slow growth rate | Simpler and faster |
Device Reliability | Issues due to defects in production | Generally more reliable |
The higher production cost of SiC can make it less appealing for budget-conscious industries. For example, manufacturers of consumer electronics may hesitate to adopt SiC due to its price tag. However, industries like electric vehicles and renewable energy are willing to invest in SiC because of its long-term benefits, such as improved efficiency and durability.
Scalability is another hurdle. Producing SiC at a large scale requires significant investment in specialized equipment and facilities. Traditional silicon, on the other hand, already has a well-established supply chain. This makes silicon easier to scale for mass production. SiC manufacturers are working hard to overcome these barriers by improving production techniques and expanding capacity.
Tip: As demand for SiC grows, economies of scale could help reduce costs. Innovations in manufacturing technology may also speed up production and improve reliability.
Despite these challenges, the potential of SiC is undeniable. Its superior performance in high-power and high-temperature applications makes it a worthwhile investment for industries aiming to innovate. While the initial costs are higher, the long-term savings in energy efficiency and system reliability often outweigh the upfront expenses.
In 2025, the semiconductor industry is expected to see significant advancements in SiC production. Companies are already exploring ways to streamline manufacturing and make SiC more accessible. As these efforts continue, SiC could become as scalable and cost-effective as traditional silicon, unlocking its full potential across various industries.
Addressing Energy and Sustainability Challenges with Silicon Carbide
Reducing Power Loss and Improving Energy Efficiency
Silicon carbide (SiC) plays a vital role in reducing power loss and boosting energy efficiency in modern systems. Its unique properties make it a preferred choice for industries aiming to optimize energy use. Here’s how SiC achieves this:
- SiC inverters operate at about 99% efficiency, compared to 98% for traditional silicon inverters. This 1% improvement might seem small, but it results in a 50% reduction in energy loss, especially in large-scale applications like renewable energy systems.
- SiC’s thermal conductivity is three to four times higher than silicon, allowing for better heat dissipation. This reduces the need for bulky cooling systems, making devices more compact and efficient.
In addition, SiC power devices enhance energy efficiency in electric vehicles and renewable energy systems. They reduce conduction losses and improve voltage blocking capabilities, ensuring less energy is wasted during operation. By integrating SiC, industries can achieve significant energy savings while maintaining high performance.
Supporting Sustainable and Green Technologies
Silicon carbide is a game-changer for sustainable and green technologies. Its ability to handle high voltages and temperatures makes it ideal for applications that demand energy efficiency and reliability. Here are some ways SiC supports green initiatives:
- SiC enhances energy efficiency in power electronics and high-temperature devices, reducing energy consumption.
- It minimizes energy loss at high voltages, making it a perfect fit for electric vehicles and renewable energy systems.
- SiC materials enable efficient energy conversion in high-voltage devices, which supports intelligent power transmission and grid management.
For example, SiC-based devices in renewable energy systems, such as solar inverters, achieve nearly 99% efficiency. This translates to more energy being converted into usable electricity and less being wasted. By improving energy utilization, SiC helps reduce the carbon footprint of these technologies, paving the way for a greener future.
Enabling Next-Generation Innovations
Silicon carbide is driving the development of next-generation innovations across multiple industries. Its high efficiency and rapid switching speeds significantly reduce energy losses during power conversion. This not only lowers operating costs but also maximizes power consumption in advanced systems.
Take a look at how SiC compares to traditional silicon in key properties:
Property | Silicon (Si) | Silicon Carbide (SiC) |
---|---|---|
Thermal Conductivity | 1.5 W/cm·K | 4.9 W/cm·K |
Breakdown Field | 0.3 MV/cm | 2.2 MV/cm |
Bandgap | 1.1 eV | 3.3 eV |
These advantages allow SiC to power innovations in consumer electronics, industrial machines, and electric vehicles. Its high breakdown voltages and superior heat dissipation improve the overall efficiency of electronic systems. As a result, SiC is enabling smarter, more sustainable technologies that meet the demands of the future.
By reducing energy waste, supporting green technologies, and driving innovation, silicon carbide is addressing some of the most pressing energy and sustainability challenges of our time. Its impact will only grow as industries continue to adopt this revolutionary material.
The Role of Silicon Carbide in the Semiconductor Industry in 2025
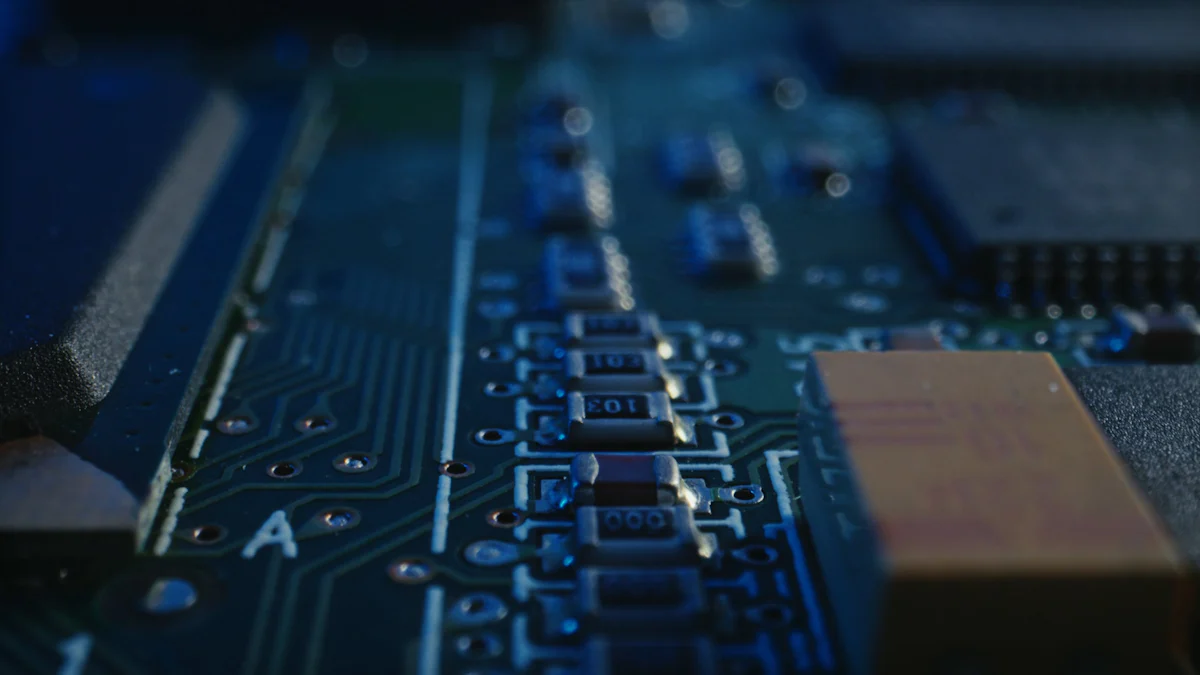
Advancing Power Electronics and High-Performance Systems
Silicon carbide (SiC) is driving major advancements in power electronics and high-performance systems. Its unique properties, like high thermal conductivity and wide bandgap, make it a standout material for modern applications. SiC dissipates heat three to four times better than traditional silicon, which is critical for high-power devices. This improved heat management ensures systems run efficiently, even under heavy loads.
SiC-based devices also excel in power conversion systems. They significantly reduce energy wastage, making them ideal for renewable energy applications. For example, SiC inverters convert energy more efficiently, ensuring better utilization of power. These improvements enhance the reliability of systems, especially in industries where performance cannot be compromised.
Hybrid technologies are another exciting development. By combining silicon with silicon carbide, engineers achieve higher efficiency without drastically increasing costs. This approach allows existing systems to benefit from SiC’s advantages without requiring a complete redesign. In fact, using SiC is often the only way to boost efficiency without changing the system’s overall structure.
The ability of SiC to handle higher voltages and temperatures makes it indispensable for high-performance systems. Its breakdown voltage is ten times greater than silicon, and its thermal conductivity ensures devices stay cool. These features are transforming industries like electric vehicles and renewable energy, where efficiency and reliability are non-negotiable.
Accelerating the Transition to Renewable Energy
Silicon carbide is playing a key role in the global shift toward renewable energy. Its efficiency in power electronics is unmatched, making it a preferred choice for solar and wind energy systems. SiC inverters, for instance, operate at 99% efficiency, compared to 98% for traditional silicon inverters. While the difference seems small, it results in a 50% reduction in energy loss. With 60 gigawatts of solar power installed in the U.S., this efficiency gain could generate an additional 600 megawatts of electricity annually.
SiC’s high thermal conductivity and wide bandgap allow it to perform reliably in demanding conditions. It dissipates heat effectively, ensuring components last longer and require less maintenance. This is especially important for large-scale renewable energy projects, where reliability directly impacts energy output.
By improving energy conversion and reducing waste, SiC supports the development of smarter, more efficient grids. Its ability to handle high voltages makes it ideal for managing power distribution in renewable energy systems. As the world moves toward greener energy solutions, SiC is helping to make this transition smoother and more sustainable.
Shaping the Future of Electric Mobility
Electric vehicles (EVs) are benefiting immensely from silicon carbide technology. SiC enhances the efficiency of EV power electronics, allowing vehicles to travel farther on a single charge. Its superior thermal performance ensures components stay cool, even during high-speed operation. This not only improves energy utilization but also extends the lifespan of critical systems.
SiC’s high power density enables the design of smaller, lighter components. This reduces the overall weight of EVs, improving their performance and energy efficiency. By lowering energy losses during power conversion, SiC helps EVs achieve longer driving ranges. This addresses one of the biggest concerns for EV buyers—range anxiety.
The environmental impact of SiC is equally significant. By improving energy efficiency, it reduces greenhouse gas emissions, making EVs a more sustainable transportation option. As the demand for electric mobility grows, SiC is shaping the future of the automotive industry with its unmatched performance and reliability.
🚗 Fun Fact: SiC-based power systems are helping EVs charge faster, making them even more convenient for everyday use.
Silicon carbide is not just a material; it’s a catalyst for innovation in electric mobility. Its role in enhancing efficiency, reducing emissions, and improving performance makes it a cornerstone of the EV revolution.
Challenges and Future Prospects for Silicon Carbide
Overcoming Manufacturing and Cost Barriers
Silicon carbide offers incredible benefits, but producing it comes with challenges. The high cost of preparation and processing makes it more expensive than traditional silicon. This price difference can be a hurdle, especially for industries that prioritize affordability.
The process of creating high-quality silicon carbide crystals is another obstacle. It’s slow and complex, often leading to defects and lower yields. The material’s hardness, while beneficial for durability, complicates processing further. These factors increase production costs and limit the availability of silicon carbide devices.
Long-term reliability is also a concern. While silicon carbide performs well in extreme conditions, its stability over time needs improvement. Engineers are working to enhance its durability to ensure it lasts longer in demanding applications.
Addressing these barriers requires innovation. Researchers are exploring ways to streamline production and reduce costs. By improving crystal growth techniques and refining processing methods, manufacturers aim to make silicon carbide more accessible and reliable.
Expanding Adoption Across Industries
Silicon carbide is gaining traction across various industries, thanks to strategic efforts by major players. Companies like STMicroelectronics and Infineon Technologies are forming partnerships to build dedicated silicon carbide production plants. These collaborations aim to meet the growing demand for this advanced material.
Onsemi is also making significant strides. They’re scaling up production by acquiring and optimizing manufacturing facilities. This expansion ensures a steady supply of high-quality silicon carbide wafers, which are essential for power electronics and other applications.
Increased investment in research and development is another key factor. As industries recognize the potential of silicon carbide, they’re pouring resources into improving its production and performance. These efforts are helping to expand its use in sectors like electric vehicles, renewable energy, and aerospace.
By focusing on partnerships, facility upgrades, and innovation, manufacturers are paving the way for silicon carbide to become a standard material in modern technology.
Innovations in Silicon Carbide Technology
Recent advancements in silicon carbide technology are addressing many of its current challenges. One of its standout features is its exceptional thermal conductivity, which is three to four times higher than silicon. This property improves heat dissipation, making silicon carbide ideal for high-power applications.
Silicon carbide devices also enhance energy efficiency. They significantly reduce energy losses during power conversion, which is crucial for industries like renewable energy and electric vehicles. This efficiency not only saves energy but also lowers operating costs.
Another exciting development is silicon carbide’s ability to operate at higher frequencies. This makes it perfect for cutting-edge technologies like 5G and high-performance electronics. By enabling faster and more efficient systems, silicon carbide is driving innovation in telecommunications and beyond.
These innovations are transforming silicon carbide into a versatile and indispensable material. As research continues, its potential applications will only grow, shaping the future of technology in remarkable ways.
Silicon carbide is reshaping the semiconductor industry with its unmatched properties. Its thermal conductivity, three to four times greater than silicon, enhances heat dissipation in high-power applications. SiC devices improve energy efficiency by reducing power losses and maximizing energy use, making them essential for electric vehicles and renewable energy systems.
As demand grows, investments in SiC production and innovation are accelerating. Projections show the market reaching $24.9 billion by 2031, driven by its role in energy-efficient and sustainable technologies. Silicon carbide’s ability to power next-generation advancements ensures it will continue transforming industries well beyond 2025.
FAQ
What makes silicon carbide better than traditional silicon?
Silicon carbide handles higher voltages, temperatures, and frequencies. It dissipates heat more efficiently and reduces energy loss. These properties make it ideal for high-performance applications like electric vehicles, renewable energy systems, and aerospace technologies.
Why is silicon carbide important for electric vehicles?
Silicon carbide improves EV efficiency by reducing energy losses and enhancing thermal management. It allows for smaller, lighter components, which increases driving range and reduces charging time. This makes EVs more reliable and sustainable.
How does silicon carbide support renewable energy?
Silicon carbide boosts the efficiency of solar and wind energy systems. Its high thermal conductivity and voltage tolerance reduce energy loss during power conversion. This ensures more electricity is generated and less is wasted, supporting a greener energy future.
Is silicon carbide expensive to produce?
Yes, silicon carbide production costs are higher due to complex manufacturing processes. However, its long-term benefits, like energy savings and durability, often outweigh the initial expense. Ongoing innovations aim to reduce costs and improve scalability.
Can silicon carbide operate in extreme conditions?
Absolutely! Silicon carbide thrives in high temperatures, radiation, and harsh environments. Its durability and thermal stability make it perfect for aerospace, defense, and industrial applications where reliability is critical.
What industries benefit the most from silicon carbide?
Electric vehicles, renewable energy, aerospace, and power electronics benefit significantly. Silicon carbide enhances efficiency, reduces energy loss, and improves durability, making it a game-changer across these sectors.
How does silicon carbide improve energy efficiency?
Silicon carbide reduces power loss during energy conversion. Its superior thermal conductivity and high voltage tolerance ensure less energy is wasted. This makes it a key material for energy-efficient technologies like EVs and smart grids.
Will silicon carbide replace traditional silicon?
Silicon carbide won’t completely replace silicon but will dominate high-performance applications. Its unique properties make it ideal for demanding environments, while silicon remains cost-effective for less intensive uses.
💡 Tip: Silicon carbide and silicon often work together in hybrid systems to balance performance and cost.